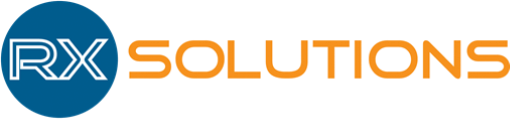
Using Industrial Computed Tomography (CT) Technology
To Expand Your 3D Measurement Capabilities
Translated by RAD
Translation | Rely Detection
Capturing the internal and external geometries of small or complex parts is not easy, but it can provide significant advantages for designers, engineers, and manufacturers across various industries. Fortunately, metrology-grade computed tomography (CT) offers a reliable, non-destructive method to capture high-resolution three-dimensional data of complex freeform parts without the need for line-of-sight access.
The results of CT scans include millions of data points that can be measured and analyzed to provide critical information. Through the measurement results, engineers and designers can remove outer layers, dynamically slice parts, and observe discrete distances between internal components. This three-dimensional scanning method is provided in the form of 3D scanning services, producing high-quality results with the help of trained technicians.
If you are looking for a service that can assist you with quality control, inspection, defect detection, and dimensional measurement, look no further. We outline the technical capabilities and benefits of using industrial computed tomography technology for 3D measurement applications. Here’s what this advanced form of scanning can do for your complex parts or components, and how CT scanning can unlock valuable information that would otherwise be difficult or impossible to measure.
The Top Ten Applications and Advantages of Industrial CT
01丨Non-Destructive Testing Method
In short, industrial CT scanning uses radiographic technology to produce multiple two-dimensional images of an object. As the scanned object rotates on a turntable, X-rays penetrate it to varying degrees based on density. The radiation that is not absorbed by the part bounces back to the detector panel, producing hundreds of cross-sectional two-dimensional X-ray images, which are then reconstructed to create three-dimensional measurement data.
Throughout the scanning process, there are no cutting, slicing, stressing, pressuring, or other forces that could damage or affect the integrity of the part. This non-destructive characteristic of industrial CT scanning makes it an excellent choice for advanced analysis, quality inspection, and reverse engineering of parts and components with complex geometries and difficult-to-measure features.
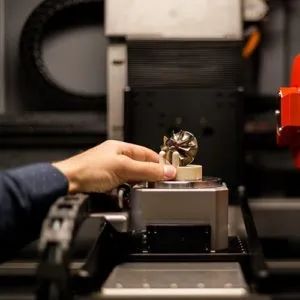
# 01 Non-Destructive Testing Method
02丨Internal and External Measurement
Contact coordinate measuring machines, non-contact laser, and structured light measurement technologies each have their advantages in recording shapes and dimensions, but even they cannot provide the internal and multi-material assembly details that CT scanners can. CT scanning services will generate complete 3D datasets of the external and internal geometries, all without the need for line-of-sight or visual access to internal components.
This may be the greatest benefit of industrial CT scanning, as it can provide detailed internal measurements without disassembling parts or products. In addition to building three-dimensional models for various measurement and inspection applications, the cross-sectional two-dimensional images generated during the CT scan can also be analyzed. This not only shortens product development cycles but also provides an efficient and straightforward quality control method that might otherwise take impractical time or even leave defects undetected.
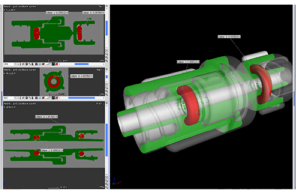
# 02 Internal and External Measurement
03丨Dimensional Analysis Comparison
Another advantage of industrial computed tomography is that this inspection method can quickly and accurately perform shape comparison analysis. CT scanning can be used to create form analysis reports that compare the accuracy of physical parts or components against standards such as CAD files or ideal dimensions. Comparisons with standards can detect any deviations from technical specifications. Whether you need part-to-part or part-to-CAD comparisons, industrial CT scanning can provide characteristic parameters that other methods, such as contact coordinate measuring systems, cannot measure.
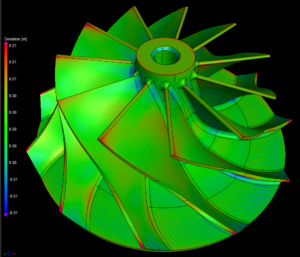
# 03 Dimensional Analysis Comparison
04丨Dimensional Measurement and Reporting
Measuring and verifying the internal geometries of complex parts can be a challenge. While laser-based scanning and coordinate measuring machine technologies can record the external shapes and dimensions of parts, they require visual access to generate representations of their internal dimensions. Obtaining internal dimension data with these systems without compromising the structure or integrity of a part is unlikely and carries the risk of distorting measurement results.
Fortunately, industrial CT can perform internal and external dimensional measurements and reporting. This makes computed tomography technology particularly suitable for precision injection molded parts or other parts and components with internal geometries that are difficult to analyze.
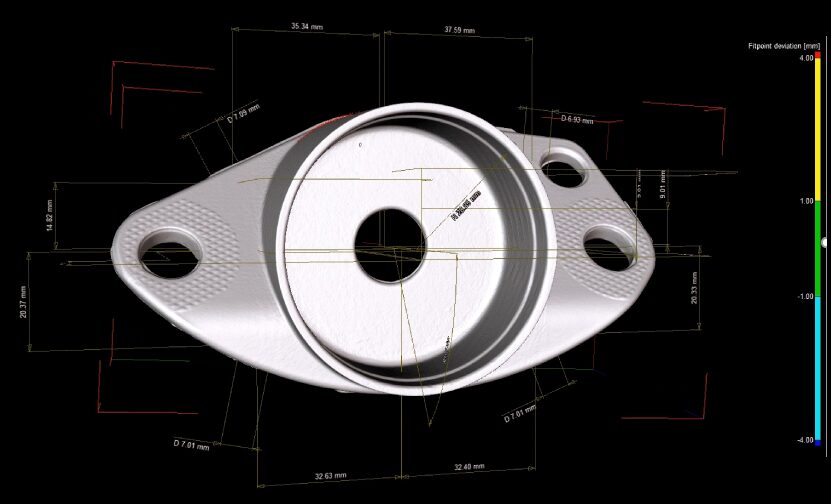
# 04 Dimensional Measurement and Reporting
05丨Wall Thickness Analysis
Wall thickness is another quality control factor that can be conveniently and quickly analyzed using industrial CT. Minor variations in wall thickness across an entire part can disrupt manufacturing or design processes and can quickly become costly, especially when manufacturers produce large quantities of identical parts. To detect any variations, a boundary is established around the external and internal features of the part. The distance between each surface is calculated to determine the minimum wall thickness. Then, three-dimensional data is rendered to display thickness values in color for quick visualization and easy interpretation. This wall thickness analysis method does not require standard CAD files for comparison and is very valuable for detecting and correcting variations that could lead to issues such as cracking and deformation of parts.
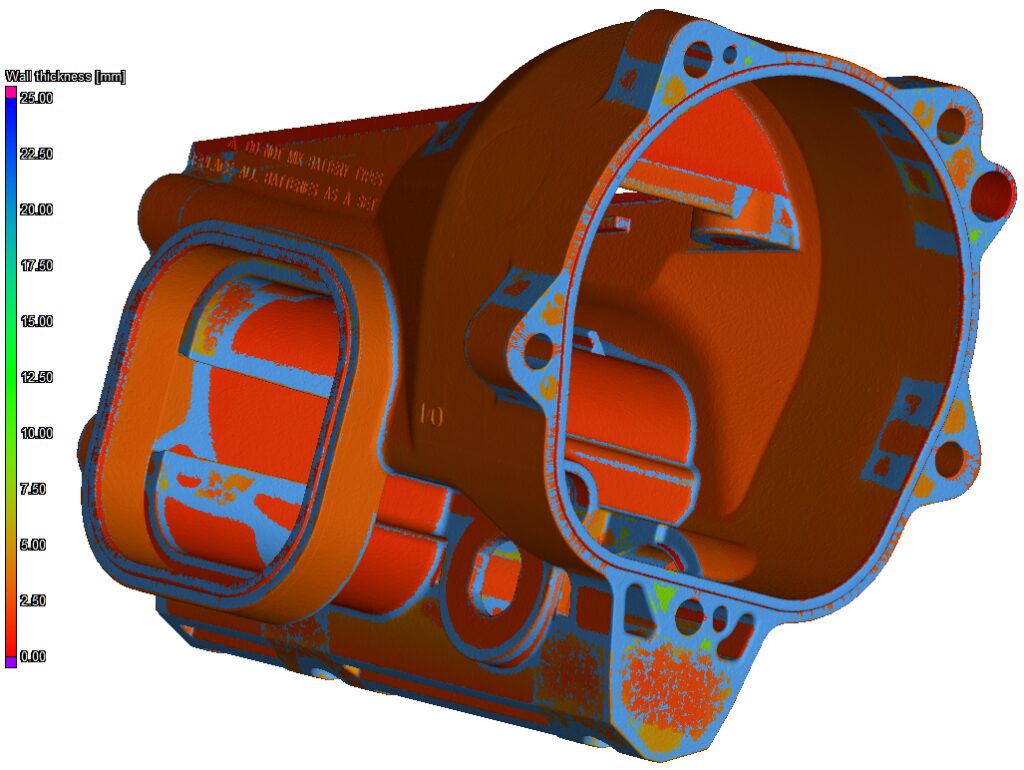
# 05 Wall Thickness Analysis
06丨Defect Detection and Analysis
In addition to detecting dimensional defects, industrial CT can also detect manufacturing defects. This plays a crucial role in quality control and product development. CT scanning can be used for porosity and inclusion verification, including identifying and precisely locating high-density and low-density regions throughout the part. After scanning, the resulting model can be used to show the location and volume of inclusions and internal porosity, as well as the percentage of porosity.
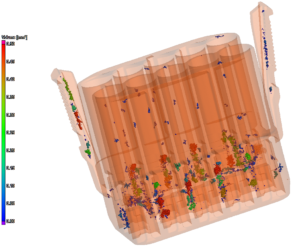
# 06 Defect Detection and Analysis
07丨Fiber Orientation Analysis
CT scanning also aids in analyzing the orientation of embedded fibers used to reinforce materials such as plastics. After scanning an object, fiber flow analysis can reveal the orientation of fibers at any point. This measurement can then be compared to the simulated nominal orientation of the fibers. This type of analysis is useful for quality control and for better understanding the interactions of internal components in composite materials.
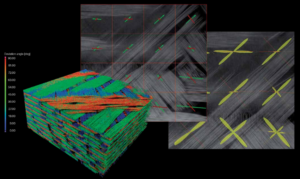
# 07 Fiber Orientation Analysis
08丨Failure Analysis
Failure analysis is a critical step in the product development cycle, and industrial computed tomography technology is very suitable for any inspections, testing tools, and techniques. Due to its non-destructive imaging method, CT scanning provides insights into failed devices or parts, while destructive testing methods can only destroy the product with no follow-up testing. The high level of detail and accuracy provided by CT scanning offers a significant advantage in finding the root cause of problems.
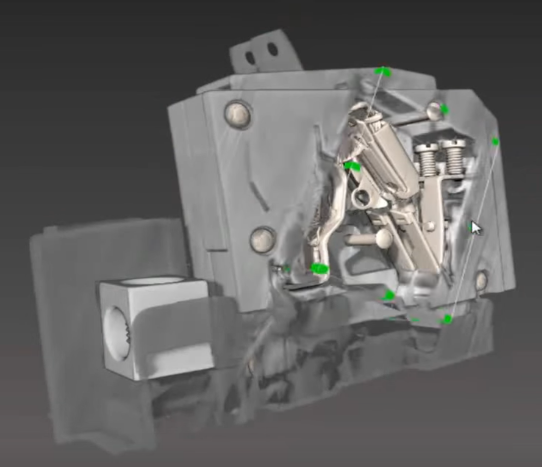
# 08 Failure Analysis
09丨Assembly Visualization Confirmation
Before the introduction of computed tomography technology, verifying and visualizing how different components fit together in an assembly was difficult, if not impossible, to do without compromising the original state. We can now assess and measure the internal and external geometries of parts and their fits through non-destructive CT scanning without cutting or disassembling the device. This method can provide valuable insights that further inform product development and quality control efforts.
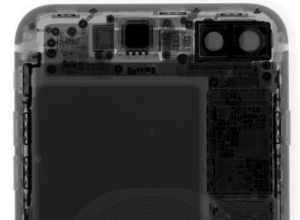
# 09 Assembly Visualization Confirmation
10丨Research and Development
CT scanning can also serve as an excellent tool for research and development. Given that a single CT scan can perform a variety of analyses, this technology is particularly suitable for universities, manufacturers, engineers, and product developers seeking further insights into material research, preliminary product design, or improving the efficiency of existing parts.
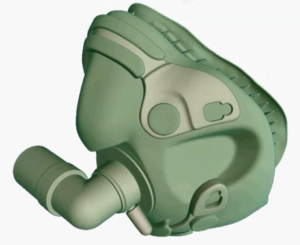
# 10 Research and Development
Original source:
Using Industrial Computed Tomography (CT) Technology to Expand Your 3D Measurement Capabilities
Click the end of the article 【Read Original】 to jump.
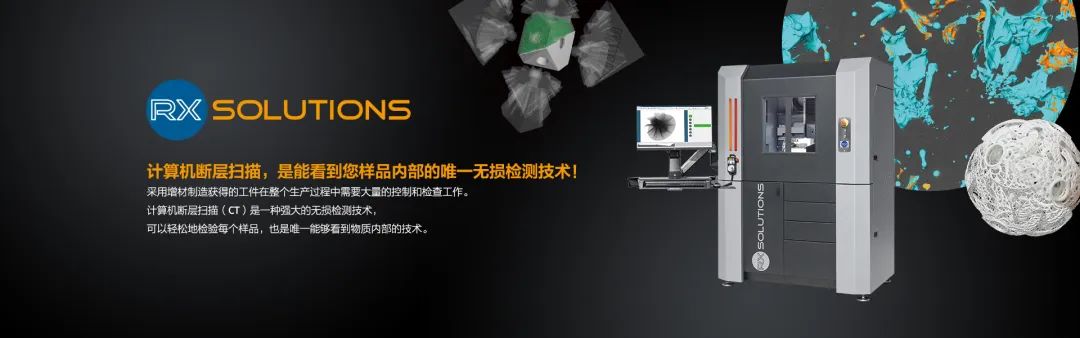
Thank you for reading.
Rely Optical Inspection, supporting a high-quality future!
For more product information, please long press the QR code below, scan, and follow the WeChat public account: Rely Detection (ID: rely-measure); or visit our official website: www.rely-measure.com.
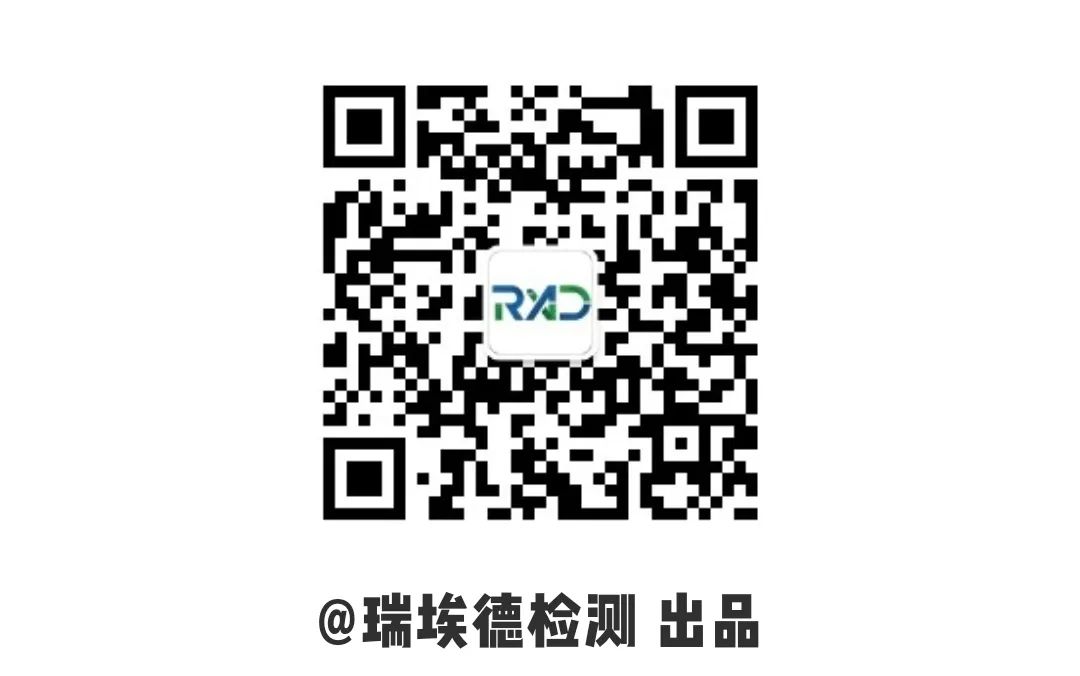