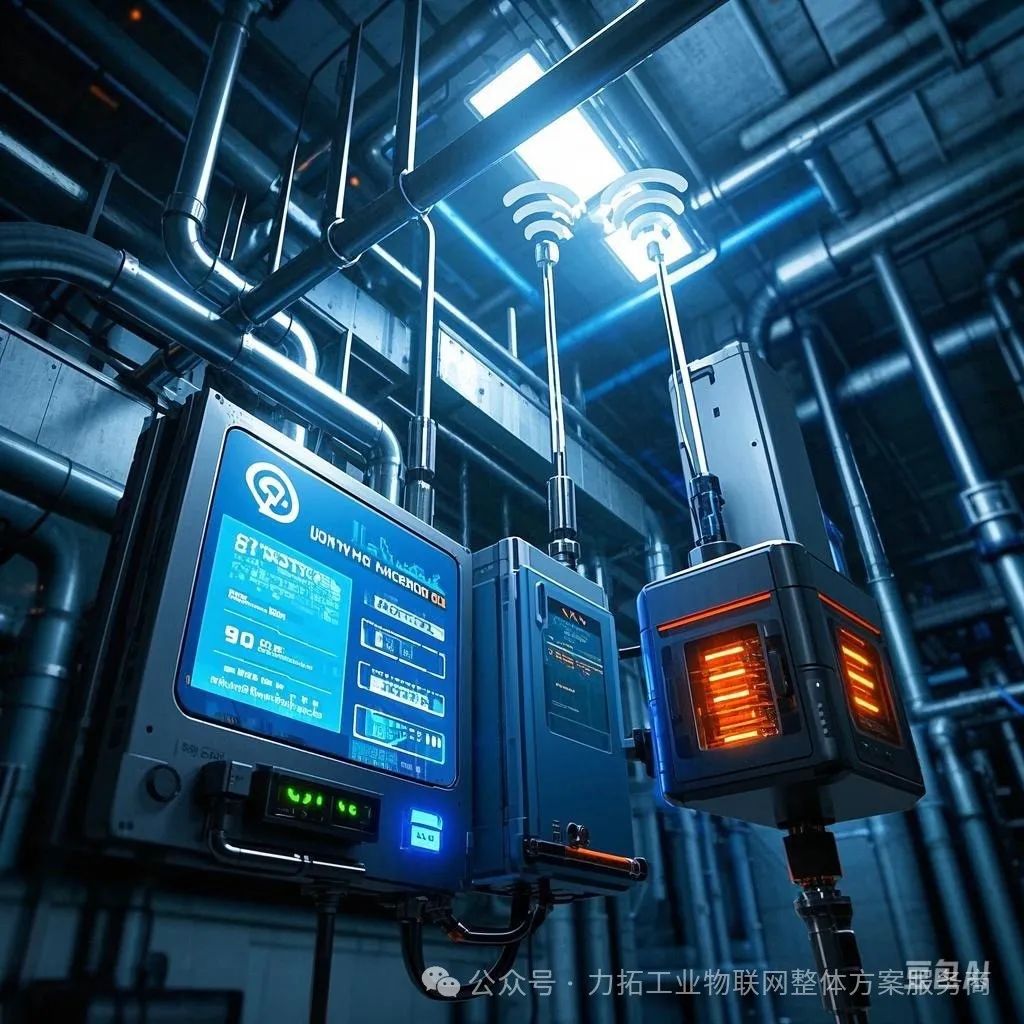
In the current context of profound adjustments in the global economic landscape and rapid technological development, traditional manufacturing is at a crossroads of transformation and upgrading. The Industrial Internet of Things (IIoT), as a product of the deep integration of new generation information technology and manufacturing, acts like a timely rain, injecting strong momentum into the transformation of traditional manufacturing, reshaping the industry’s ecology and future direction.
The core of the Industrial Internet of Things lies in the interconnection of various equipment, machines, production lines, and even entire factories in industrial production through technologies such as sensors, network communication, and big data analysis, achieving intelligent perception, control, and management.In traditional manufacturing, production processes are often relatively fragmented, making it difficult to accurately grasp the operational status of equipment in a timely manner, which not only leads to low production efficiency but can also cause significant downtime losses due to equipment failures. The intervention of the Industrial Internet of Things allows production equipment to “speak” in real-time, continuously transmitting its operational parameters, performance indicators, and other data to the management system. For example, in an automotive manufacturing workshop, by deploying sensors on key equipment such as stamping, welding, and painting, production managers can remotely monitor the working status of each device, predict potential equipment failures in advance, and arrange maintenance timely, thereby minimizing the risk of production interruptions and significantly enhancing production continuity and stability, which in turn greatly improves production efficiency.
Quality control is the lifeline of the manufacturing industry, and the Industrial Internet of Things plays a crucial role in this area as well.With the help of high-precision sensors and intelligent algorithms, various quality indicators of products during the production process can be monitored and analyzed in real-time. Once quality data deviates from preset standards, the system immediately issues an alarm and traces the root of the problem, achieving a shift from “post-inspection” to “in-process control” and even “prevention”. This not only reduces the defect rate, minimizes raw material waste and rework costs, but also enhances the market competitiveness of products, helping traditional manufacturing establish a foothold in high-end markets and escape the predicament of low added value.
Looking to the future, the development prospects of the Industrial Internet of Things in traditional manufacturing are vast and boundless.With the comprehensive coverage of 5G networks, its low latency, high bandwidth, and wide connectivity characteristics will further unleash the potential of the Industrial Internet of Things, making communication between devices smoother and more efficient, providing solid support for real-time remote control of complex industrial equipment and large-scale collaborative manufacturing. The deep integration of artificial intelligence technology with the Industrial Internet of Things will endow production systems with autonomous decision-making capabilities, enabling dynamic optimization of production plans and adjustment of process parameters based on real-time production data, achieving intelligent production scheduling and resource allocation, and promoting the manufacturing industry towards a higher level of flexible production to quickly respond to market’s personalized customization needs.
In the journey of transformation and upgrading of traditional manufacturing, the Industrial Internet of Things is undoubtedly one of the most critical driving forces. It is leading the manufacturing industry from traditional extensive production to a new manufacturing model characterized by intelligence, precision, and greenness, assisting traditional manufacturing in breaking out of its cocoon in the wave of global industrial competition, achieving high-quality and sustainable development, redefining the future blueprint of manufacturing, and creating a more efficient, intelligent, and prosperous industrial new era.
Rio Tinto – Professional EPC Solution Provider for Industrial IoT
Remote monitoring, industrial interconnection
Visual management, cost reduction, and efficiency increase
Business consulting + V: shjsztc3949
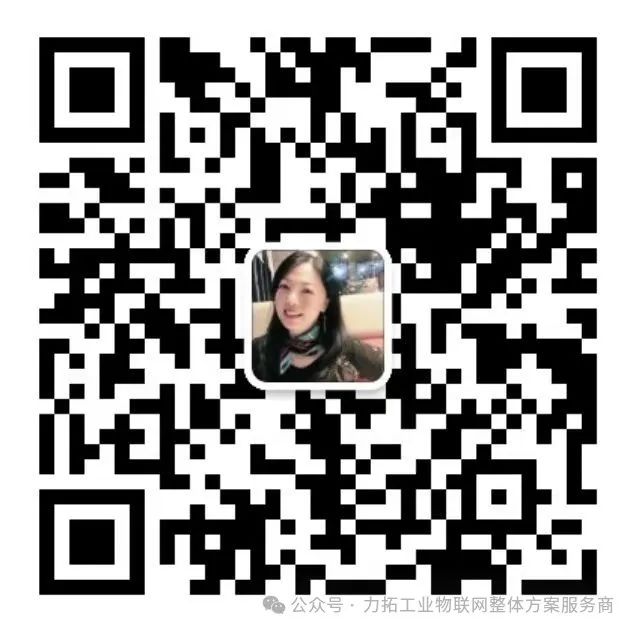