1. Understanding Automotive Chips
According to their functions, automotive-grade chips can be categorized into four types: computing and control chips, power chips, sensor chips, and others. Computing and control chips mainly consist of microcontrollers and logic ICs, primarily used for calculation, analysis, and decision-making; power chips mainly convert electrical energy and control circuits; sensor chips are responsible for sensing vehicle operating conditions, converting non-electrical information into electrical output.
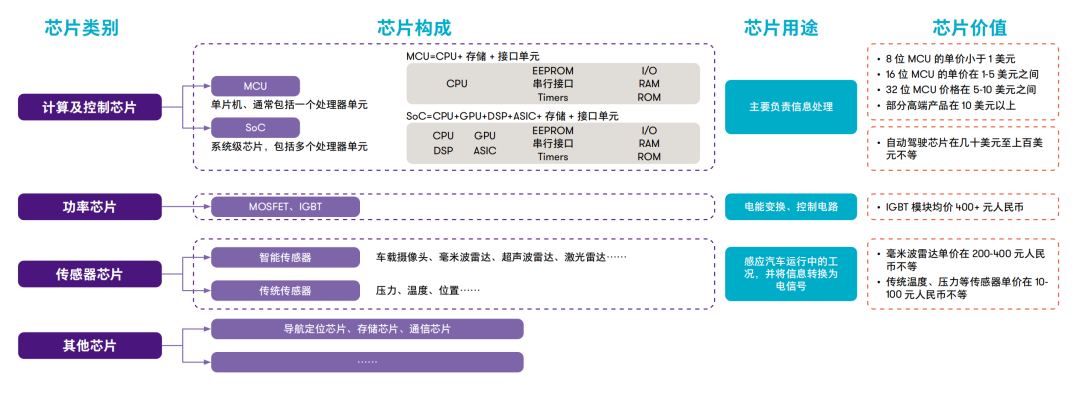
Chipone Electronics is developing AFE automotive-grade lithium battery protection chips, with plans to launch products in the second half of 2024;
Jiefa Technology’s first functional safety automotive-grade MCU chip AC7840x has been delivered to several benchmark clients and is being applied on a large scale. It can be widely used in automotive body, cockpit, lights, new energy, and motor control fields;
Xinchi Technology has obtained ISO 26262 functional safety process certification, AEC-Q100 reliability certification, ISO 26262 functional safety product certification, and national secret certification, becoming the first automotive chip company in China to hold all four certifications.
GigaDevice’s GD552G high-capacity product has passed AEC-Q100 automotive certification, and the SPI NOR Flash automotive-grade product capacity has been fully deployed, with the GD25 automotive-grade storage series achieving mass adoption in several automotive companies;
Beijing Junzheng ranked among the top in the global automotive SRAM and automotive DRAM markets in 2022, with significant growth in automotive Flash chip sales compared to 2021;
Jucheng Co., Ltd. started from consumer-grade EEPROM and has entered the automotive field, with automotive-grade EEPROM products now being supplied in large quantities.
Chenxin’s CX1860 chip is one of the first domestic SoC wireless communication chips supporting C-V2X for connected vehicles, and has been successfully applied in several vehicle-mounted OBU and roadside RSU products;
Guomin Technology’s series of security chips have been widely applied in T-Box, ETC/OBU, OBD and other vehicle-mounted devices;
Allwinner’s T7 chip was the first automotive-grade SOC chip launched in China in 2018, supporting multi-functional integration for intelligent driving including ADAS and DMS.
Shengbang Co. has begun small-batch production of some automotive high-efficiency low-power drive chips, with product performance quality meeting international advanced levels;
SiRuiPu products have entered the automotive market, with the first automotive-grade high-voltage precision amplifier achieving mass supply.
Shengbang Microelectronics officially launched the AEC-Q100 automotive standard upgrade for voltage reference chips in 2021, with the first AEC-Q100 compliant voltage reference chip LM431BQ officially delivered at scale;
Jiehuate has been applied in various aspects of automotive electronic circuits, including energy conversion, battery balancing, protection, and dynamic warning, and is gradually being promoted for market validation;
Lingxin Technology’s automotive-grade products are produced in factories certified with IATF16949, and all products have passed AEC-Q100 automotive verification, with each product’s production line audited according to VDA6.3.
Anshi provides dedicated discrete devices, MOSFET devices, and logic devices for connected vehicles, with products fully compliant with AEC-Q100/Q101 standards;
Huada Semiconductor’s drive chips serve as a bridge between controllers and power devices, aimed at industrial and automotive applications, providing complete solutions in conjunction with self-developed IGBT and SiC power devices.
Shanghai Xintai’s Mizar automotive safety chip is a SoC-level chip for intelligent connected vehicles, implementing domestically controllable hardware encryption algorithms, and has passed reliability tests meeting ACE Q100 Grade 1 requirements;
Fudan Micro has launched several security chips, which are widely used in ETC OBU, TBox, intelligent cockpits, FOTA, digital keys, smart hardware, metering, accessory certification, and copyright protection.
Silicon’s V-generation IGBT and FRD electric vehicle main motor drive modules have begun small-batch supply to some clients. As of August 2022, the company has the production capacity to manufacture 70,000 automotive-grade power modules monthly;
Xinjieneng’s 12-inch SGT-MOS platform products have successfully entered leading companies in the new energy vehicle sector;
SDIC’s automotive-grade IGBT modules supplied over 500,000 new energy vehicles in the first half of 2022, with over 200,000 of them being A-level or above models, while automotive-grade SiC MOSFET modules for passenger vehicle main controllers have begun mass installation.
Weir’s new generation OX08B40 CMOS image sensor is developed with the assistance of Xilinx MPSoC and Motovis IP, competing with ON Semiconductor;
Naxin Micro has launched the industry-leading NSR31/33/35 series LDO chips, designed for automotive battery power supply applications;
Qipuwei’s XL6600 series is an automotive microcontroller chip that meets AEC-Q100 and ISO26262 automotive safety ASILB standards. It is suitable for body control (BCM), in-vehicle air conditioning control (HVAC), etc.
Automotive-grade chips refer to chips that, compared to consumer-grade and industrial-grade chips, possess high reliability, safety, and stability. They are required to have zero defects and can be supplied long-term (typically 10-15 years), meeting the standards set by the AEC (Automotive Electronics Council).
2. The Certification Process for Automotive-grade Chips
As mentioned earlier, Xinchi possesses an internationally-level team with nearly 20 years of experience in automotive-grade mass production, being one of the few in China with the capability of defining core automotive chip products, conducting technical research and development, and large-scale mass production. In terms of automotive certification, Xinchi has successively obtained ISO 26262 functional safety process certification, AEC-Q100 reliability certification, ISO 26262 functional safety product certification, and national secret certification, becoming the first automotive chip enterprise in China to hold all four certifications. Currently, Xinchi has completed the tape-out of four series of chips, achieved the highest specifications for automotive certification, and has entered large-scale production, serving over 260 clients and covering more than 90% of automotive manufacturers in China. As early as 2020, it launched three vehicle-mounted SoC chips: X9 (smart cockpit), V9 (autonomous driving), G9 (central gateway), and in 2021, released upgraded chips X9U, V9T, G9Q/G9V, among which X9U has a CPU computing power of 100KDMIPS, GPU computing power of 300GFLOPS, and AI computing power of 1.2TOPS, capable of supporting up to 10 independent displays, integrating various smart cockpit and ADAS functions.
In other words, to enter the mainstream automotive electronic supply chain, several basic requirements must be met: compliance with the reliability standards AEC-Q100 (IC), 101 (discrete components), and 200 (passive components) established by the North American automotive industry; adherence to the international standards ISO 26262 for automotive electronics and software functional safety; compliance with ISO 21448 for expected functional safety, covering safety hazards caused by non-system failures; compliance with ISO 21434 for cybersecurity requirements, reasonably ensuring vehicle and system network security; and meeting the zero-failure supply chain quality management standard IATF 16949. Generally, the certification of automotive-grade chips takes about 3 to 5 years, which poses a significant technical, production, and time cost challenge for chip manufacturers. For instance, Mobileye took a full 8 years to receive its first automotive order, and NVIDIA’s current main chip, Xavier, cost $2 billion to develop.
Next, we will introduce the certification process for automotive chips one by one.
① AEC Quality Standard, the most important certification standard.
AEC-Q100 is a failure mechanism based on stress testing of packaged integrated circuits. The Automotive Electronics Council (AEC) is headquartered in the United States and was originally established by three major automotive manufacturers (Chrysler, Ford, and General Motors) to establish a common qualification and quality system standard for components.
The idea of establishing AEC was conceived during a JEDEC meeting in the summer of 1992. The idea of a common qualification specification was proposed as a possible method to improve the situation. At subsequent JEDEC meetings, it was determined that the idea of a common qualification specification was feasible, and work on Q100 (integrated circuit stress testing qualification) began shortly thereafter.
The current application of AEC-Q100 in integrated circuits is primarily focused on discrete components AEC-Q101 and passive components AEC-Q200. AEC-Q100 is divided into five levels based on temperature ranges as the fundamental classification criterion. Level 0 is the highest (-40°C to +150°C), Level 1 is -40°C to +125°C, Level 2 is -40°C to +105°C (which is quite common), and the lowest is Level 4 (0°C to +70°C). Level 0 is primarily used under the worst environmental conditions, while Levels 1 and 2 are used in other parts of the vehicle.
② The ISO 26262 standard established by the International Organization for Standardization (ISO) has become the guiding standard for functional safety in automotive development processes.
The Automotive Safety Integrity Level (ASIL) is a risk classification scheme defined by the ISO 26262 – Road Vehicles Functional Safety Standard. It is an adjustment of the safety integrity levels used in the automotive industry from IEC 61508. This classification helps define the safety requirements necessary to comply with the ISO 26262 standard. ASIL is set by analyzing the severity, exposure, and controllability of potential hazards during vehicle operation. The safety goals for these hazards also comply with ASIL regulations.
From low to high, there are four levels: ASIL A, ASIL B, ASIL C, and ASIL D. For systems like airbags, anti-lock braking systems, and power steering systems, ASIL-D level is required — the most stringent system due to the highest associated risk of failure. On the other hand, parts like tail lights only require ASIL-A level. Headlights and brake lights are generally ASIL-B, while cruise control typically falls under ASIL-C.
③ National Secret Certification.
National Secret refers to the domestic encryption algorithms recognized by the National Cryptography Administration. The vehicle-mounted national secret module provides encryption services through software, with functions such as secure storage, secure communication, and identity authentication. For automotive manufacturers and users, the information security of the entire vehicle is a crucial guarantee of user interests.
The vehicle-mounted national secret certification assessment includes a total of eight major items, including encryption module specifications; encryption module interfaces; roles, services, and authentication; vehicle-mounted software encryption module adaptation; sensitive security parameter management; self-testing; lifecycle assurance; and validation tests for the correctness and consistency of algorithms.
With the development and application of intelligent connected technology, the Internet of Vehicles faces a series of potential security threats, such as the lack of encryption technology in the CAN bus protocol, which may lead to data leakage; vulnerabilities in data keys may trigger attacks or exploitation in multiple links such as identity authentication, encryption algorithms, key storage, and data transmission. In response, the International Organization for Standardization continuously improves the ISO/SAE 21434 Road Vehicles – Automotive Cybersecurity Engineering Standard, and China is about to release a draft of mandatory national standards such as “Technical Requirements for Automotive Information Security” to ensure vehicle information security from the design and development source.
④ IATF16949 and other quality system certifications.
IATF16949 certification, known as the “International Automotive Task Force Quality Management System,” is a widely recognized and adopted quality management system standard in the global automotive manufacturing industry. This system was established and released by the International Automotive Task Force (IATF) in 2002, aiming to coordinate global automotive manufacturers, suppliers, and related organizations to enhance the quality, safety performance, and overall efficiency of automotive products and supply chains.
Considering the overall vehicle project development process and the chip design and development process, it takes 3.5 to 5.5 years from chip design to mass production for vehicles, and once the chip is in use, it must meet the OTA (Over-The-Air) upgrade iteration requirements for automotive products within a lifecycle of 5 to 10 years.
In the product design phase, automotive-grade chip products must follow a design path different from that of general chip products, as the safety requirements of vehicles impose higher demands on the reliability, stability, and consistency of automotive-grade chips. Since chips in vehicles need to operate under harsh conditions such as wide temperature ranges (-40~+150°C), high vibration, dust, electromagnetic interference, and oil and gas pollution, automotive-grade chips generally use mature and reliable automotive-grade wafer manufacturing processes to ensure reliability in the above-mentioned harsh environments. Compared to more refined wafer processes, mature and reliable wafer manufacturing processes can withstand adverse environmental factors such as overcurrent, overvoltage, high temperatures, and high humidity encountered in actual automotive use.
To improve the reliability of automotive-grade chips, special designs for products include: i) considering the impact of environmental factors on chip performance during vehicle operation, companies will leave some margin in performance indicators. Circuits that do not meet the expected margin during simulation testing need to be redesigned; ii) adding diagnostic and alarm circuits during the design phase for common failure modes; iii) implementing anti-interference measures through external shielding structures and protection circuits for key components in the chip to address the complex electronic environment inside vehicles, such as electromagnetic interference and current-voltage shocks.
For the high stability requirements of automotive-grade chips, outsourcing processing (foundry) requires wafer and packaging testing factories to obtain IATF16949 certification. Additionally, the automotive-grade production lines of outsourced processing manufacturers are audited according to the German automotive industry quality standard VDA6.3 process audit standard and PPAP production part approval process to ensure process stability, compliance, and high product quality.
Automotive-grade products belong to the highest control level, Class A. The R&D process for this type of product has also been specially regulated based on the basic process. Automotive-grade chip products must complete reliability testing before mass production, strictly following AEC-Q testing procedures and standards to validate three batches of products to ensure the quality stability of automotive-grade chips produced. Once all three validations pass, an AEC-Q test report is generated, indicating that the product meets AEC-Q reliability testing standards.
3. The Uniqueness of Automotive-grade Chips
The lifecycle of a smartphone is typically 3 years, and at most 5 years, while the design life of a vehicle is generally around 15 years or 200,000 kilometers, far exceeding the lifecycle requirements of consumer electronic products. Therefore, the product lifecycle requirements for automotive chips are over 15 years, with supply cycles potentially lasting up to 30 years. This necessitates consistency and reliability in chips.
Additionally, when designing automotive chips, functional safety must be prioritized from the outset of architecture design, becoming an essential component of automotive-grade chips. This involves using independent safety islands in the design, with ECC and CRC data verification incorporated into key modules, computing modules, buses, and memory, including the entire production process utilizing automotive-grade chip processes to ensure functional safety.
Less reliance on advanced processes. In domestic automotive-grade chips, MCU, CIS, display driver ICs, MEMS sensors, etc., mainly use mature processes (28nm and above), which overlap significantly with the processes used in consumer electronics; AI chips, SoCs, and GPUs mainly use advanced processes (below 28nm).
4. Supply Competition Analysis
Since 2020, due to mismatched supply and demand, as well as the capacity squeeze from consumer electronics demand, the production capacity of automotive-grade chips has gradually tightened, with the average delivery cycle extending from 6-9 weeks to about 26 weeks; by 2023, the supply of automotive-grade chips has gradually recovered, and in the second half of 2023, there is a situation of high inventory of automotive-grade chips, with clients tightening their chip procurement orders; however, in terms of demand structure, high-end MCUs and IGBTs still face a supply-demand imbalance.
The localization of automotive-grade chips has made breakthroughs, especially in the fields of power semiconductors, computing chips, and control chips, where a certain market share has been established.
MCU: Foreign MCU manufacturers dominate the global automotive MCU market due to their first-mover advantage. According to IHS data, in 2022, Renesas, NXP, Infineon, TI, Microchip, and ST together accounted for about 98% of the global automotive MCU market share. This high market share is closely related to the significant position of Japanese, European, and American automotive brands in the global automotive industry chain.
SOC: In the automotive-grade SoC chip market, domestic suppliers have emerged for intelligent cockpit chips, but the main suppliers are still foreign manufacturers, especially in the market for vehicles priced over 400,000 yuan, where NVIDIA, Intel, and Qualcomm hold significant shares.
In 2022, in the global high-performance (over 50 Tops) autonomous driving SoC chip market, giants like NVIDIA, Horizon, Black Sesame Intelligence, Huawei HiSilicon, and Qualcomm occupied 94.7% of the global market share.
Power chips: According to data, the top three manufacturers in the IGBT device industry accounted for 53% of the market share in 2021, with Infineon leading at 29%, followed by Fuji Electric at 15%, and Mitsubishi at 9%.
The global SiC MOSFET industry chain is primarily dominated by the United States and Japan, with the top six silicon carbide companies, including ST, Infineon, Wolfspeed, ROHM, Onsemi, and Mitsubishi, accounting for 95% of the market share.
In the automotive-grade sensor chip market, domestic manufacturers mainly focus on humidity, temperature, light-sensitive, and pressure sensors, while radar sensors are still dominated by foreign manufacturers. According to revenue metrics related to vehicle-mounted LiDAR, Hesai Technology ranks first in the world with a market share of 48%, followed by Valeo at 25%, and RoboSense at third.
In the CIS field, in 2022, ON Semiconductor and OmniVision accounted for 44% and 30% of the market share, respectively, with the top two accounting for 74%, indicating a high industry concentration.
The road is long and arduous, but we will arrive. We hope that during this new era of automotive industry transformation, domestic chip manufacturers can seize this valuable window and accelerate their entry into the market.
Disclaimer: This article is purely for practical discussion purposes, and the copyright belongs to the original author and related rights holders. The views expressed represent the author’s personal opinion. If there are any issues, please contact us, and we will address them promptly.