
For more details, please log in to www.cpcashow.com
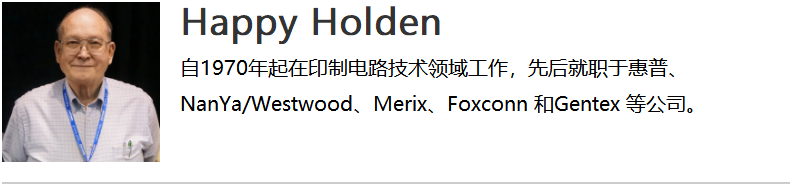
Process control is often overlooked by the industry, yet it is crucial for the successful operation of PCB factories. This involves controlling the concentration of chemicals in numerous PCB processes, especially in rapidly developing automated processes.
I have a knack for analysis, which is why I am fascinated by control projects. My second degree is in Electrical Engineering Control Theory, and my understanding of the industry comes from the perspectives of feedback loops and black boxes. When I first entered this industry, I volunteered for the California Circuits Association (CCA) technical project group, founded by my mentor Clyde Coombs. In discussions with process engineers, it became evident that small PCB factories cannot afford the chemical process control methods used by companies like HP, nor can they provide support for technicians like myself.
Since becoming a printed circuit process engineer, this has been my most interesting subject. Fortunately, I took an instrumental analysis chemistry course with a chemical engineering professor during my undergraduate studies. In that course, we built over 40 analyzers, spectrometers, and titrators using Lego-like model analysis systems (including electronic components). This made me realize that there is a solution to this problem.
For cutting-edge processes, chemical laboratories are an important part of process control. Of course, one can purchase complex measuring tools and laboratory equipment to accomplish this, but existing tools and methods can also simplify the solution.
Thus, I invented a low-cost, easy-to-analyze process that not only allows electroplating devices to autonomously control instruments that previously required chemical engineers to operate, but also increases the efficiency of analysis and testing. At the monthly meetings organized by CCA, we displayed the equipment on several tables, allowing everyone to review project costs and usage methods.
Some materials used in these methods are easy to find, such as Clinistix (urine test strips) for testing phenylketonuria (PKU) in infants, which can be purchased at any pharmacy. This plastic indicator costs $10 for 20, and can measure the concentration of hydrogen peroxide in mild etchants in less than a minute. Another example is using a liquid hydrometer costing $18 to control etchants, cleaners, acids, and electroplating. These simple measuring methods save costs, and lower chemical concentrations can also be measured (Figure 1).
Figure 1: Frequent or continuous monitoring of chemicals can reduce costs and improve yield
This project has been very successful, and I have put this idea into practice for the past 40 years. In 2009, I perfected a small cyclic voltammetry (CVS) device, costing only $200, to replace a $20,000 laboratory device, with the key being that each copper plating tank could sustain CVS measurements. At that time, this method was applied in 68 units/tanks of 2000L copper plating in factories in China, resulting in significant improvements in performance and yield.
Chemical processes are controlled by key chemical concentrations. Production management and technical personnel apply these two low-cost methods to chemical process monitoring, involving applications in PWB manufacturing, chemical coatings, sensor manufacturing, and electroplating/electroforming. With ion-specific electrodes and simple color wheel comparators, large-scale chemical chlorine analysis or battery-powered spectrophotometers can be operated for just a few hundred dollars, with some techniques costing only $20.
After training, production personnel can use all these methods. The project does not require a formal laboratory, but laboratories can use these technologies to enhance productivity and increase the number of chemicals that can be controlled. This is especially important for critical copper plating processes, such as HDI through-hole filling and SAP metallization. As shown in Figure 2, there are five very important indicators for copper plating.
-
Uniform plating;
-
Flatness;
-
Crack resistance;
-
Maximum current density;
-
Appearance.
Figure 2: The impact of electroplating parameters and changes that occur after an increase in concentration can be automatically analyzed and controlled for the first five parameters
These five properties are controlled by six parameters, five of which are chemical concentrations:
Although many parameters can affect the distribution of the electroplating layer, chemical concentrations are one of the most important and impactful parameters, changing faster than any other parameter. Better control of chemicals is important for:
-
Identifying process issues;
-
Reducing human error;
-
Enhancing processing reliability;
-
Narrowing process windows;
-
Reducing chemical operating costs.
The most commonly used chemical sensors
Common chemical sensors used in PCB manufacturing:
1. Electrochemical Sensors
Electrochemical sensors such as pH sensors are the most commonly used in analysis, but oxidation-reduction potential (ORP), ion-selective electrodes, capacitance, and conductivity sensors are also important (Table 1).
Table 1: Functions of the five main electrochemical sensors
Conductivity sensors can measure the total solid content in electrolytes. This type of sensor is usually used to determine the concentration of known components such as salts, bases, and acids. The concentration of these solutions alters the resistance or conductivity of the solution.
The lower conductivity range is 0.01-100,000 micro-ohms/cm, used to indicate the purity of water (boiler water, cooling water, or deionized water). Higher concentrations of electrolytes (50 ohms/cm to 1000 ohms/cm) use chemical probes to avoid the polarization effect of electrolysis. The industry commonly measures conductivity (dissolved ion concentration) and pH (hydrogen ion concentration) with sensors.
Specific Ions
Specific applications require measuring the ion activity in the solution, and electrodes can be designed to be very sensitive to specific ions that need to be measured. These electrodes are visually similar to pH electrodes, but are actually made of glass membrane electrodes, solid-state membrane electrodes, liquid ion exchange membrane electrodes, and silica gel permeation electrodes. Reference electrodes and measuring electrodes used for pH are the same. The output of the electrodes is read on a voltmeter similar to a high-impedance voltmeter used with pH electrodes.
Using ion-selective technology, many applications can be achieved. In the printed circuit field, copper and chloride can be measured in acidic sulfate electroplating solutions, lead and fluoroborate in tin-lead fluoroborate electroplating solutions, cyanide (ductility promoters) in chemical copper solutions, permanganate in desmearing/etching solutions, and sulfate in nickel sulfate electroplating solutions for gold finger plating.
Specific ion electrodes are made specifically for certain ions, such as copper, chloride, and sulfate, with sensitivity ranges measured in ppm and preferred pH values. Many times, specific ion electrodes use the same measuring instruments as pH electrodes.
ORP, or oxidation-reduction potential, determines the oxidative or reductive characteristics of a chemical reaction. The processes of reduction and oxidation are opposites. Without reduction, there can be no oxidation. For example, if bivalent copper ions are reduced to univalent copper ions, ferrous ions will simultaneously lose an electron to become ferric ions (gaining a positive charge).
ORP or oxidation reaction sensors are used in automatic control technologies for chemical solutions (ACSC) to control oxidants in ferric chloride, cupric chloride, and hydrogen peroxide/sulfuric acid etching, and can also measure Au(III) to Au(I) in gold finger plating solutions and copper activity in chemical copper solutions.
2. Specific Gravity Sensors
Another commonly used type is specific gravity sensors (SG). Although they do not conduct chemical analysis, they can measure the concentration of dissolved solids in solutions. The industry commonly uses six methods:
The most economical way to measure SG is to use a liquid hydrometer (Figure 3). These instruments are very inexpensive and come in various ranges, but all need to be manually placed in a beaker.
Figure 3: Commercial liquid hydrometers with 48 different ranges
Hydrometers belong to the float type SG sensors. Another type of float hydrometer is fully immersed. The SG sensor shown in Figure 4 is made using GEM-grade switches. Specific depths (Dd) are drilled into a CPVC plastic shaft, and two CPVC plastic nuts are adjusted to the corresponding specific diameters (Nd). By screwing the rod in or out, the set point range of the SG can be varied from 1x to 50x. Figure 5 shows the calibration curve. The horizontal axis represents the SG operating set point, and the vertical axis represents the range. This determines the drilling depth (Dd) of the sensor and the diameter (Nd) of the nut.
Figure 4: The SG sensor in Figure 4 can be made extremely sensitive and accurate using GEM-grade switches, with a hollow screw and two threaded nuts.
Figure 5: The calibration curve and operating curve of the SG sensor in Figure 4, selecting the operating point and span, can determine the outer nut diameter and the drilling depth of the plastic rod.
To determine the operating curve, the operating criteria must be established based on Archimedes’ principle. Depending on the position of the nut, the fixed weight of the rod and nut is affected by the center of gravity (CoG). For the sensor to float and turn off the switch, regardless of the position of the nut, the volume and center of gravity of the float will not change, and only the SG (buoyancy) can oppose the CoG. The sensitivity of SG sensors is 25 times that of any sensors available on the market, yet the cost is only one-thousandth of those sensors, with a minimum range of 0.02 and an accuracy of 0.04% higher than 0.8-1.5 units of aqueous solution.
For example, when analyzing the concentration of copper sulfate in a sulfuric micro-etchant, the temperature is measured first, followed by the specific gravity. The intersection of these two points indicates the concentration of sulfuric acid and copper sulfate.
3. Colorimetric Sensors (Spectrophotometry)
The third common tool is color indicators. Sensor strips or chemical additives are added to the solution and compared to standard color bands, but this method requires the operator to visually judge whether the colors match. This method is not problematic in itself, but it cannot be applied if the staff is colorblind (Figure 6).
Figure 6: Simple color comparison can be very accurate, such as testing the pH and chlorine concentration of a swimming pool at home.
As for spectrophotometric sensors, or more appropriately named, electromagnetic radiation energy sensors, among the most commonly used are visible light colorimeters, UV-visible spectrophotometers, and infrared spectrophotometers. Only the first two are used in PCB processes. Spectrophotometers are used to analyze the concentration of copper in chemical copper, sulfuric electroplating, and hydrogen peroxide sulfuric etching solutions, as well as nickel, cobalt, palladium, and chromium in corresponding plating solutions.
The reason for using UV-visible spectrophotometers is that they have microprocessor control units that selectively scan wavelengths and use the first and second derivative curves of absorbance to automatically calculate concentrations by comparing these spectra with stored spectra. Many units can directly control the replenishment and sampling of plating solutions.
Using this method, the concentrations of Au(I) and Au(III) in gold plating solutions can be analyzed, as well as the contents of patented additives, nickel, and impurities in nickel plating solutions for gold plating, along with various copper concentration analyses. The entire process eliminates manual operations, and the wavelengths have been extended with commonly used UV-VIS spectrophotometers. Below are six commonly used UV-VIS spectrophotometers, with a light-sensitive range of 340 nm to 1000 nm (Figure 7).
Figure 7: Six commonly used UV-VIS spectrophotometers provided by laboratory suppliers, some of which have been on the market for 60 years (such as Spectronic 20).
Recently, with the emergence of mobile phone camera devices, many DIY spectrophotometers have been developed. All of the work is based on the specific wavelengths of LED light, and expensive optical filters or monochromatic optical gratings are no longer needed. Figure 8 shows 12 different LEDs’ wavelengths, as well as DIY spectrophotometers commonly used in middle and high schools.
Figure 8: DIY spectrophotometers are common online, and middle and high school students can make them. Using specific wavelength LEDs or any CD’s optical grating, simple colorimeters can be created. Detectors can be common mobile phone cameras or specific cameras purchased for Raspberry Pi or Arduino. The common Lego spectrophotometer is displayed here.
A specific DIY spectrophotometer called the Lego spectrophotometer is made from children’s Lego and optical gratings cut from CDs. The camera module of Raspberry Pi or Arduino has a sensitivity range from 400nm to 900nm. Designs and parts can be viewed online. If high school students can make and use these spectrophotometers, then factories can too.
IR and UV/VIS spectrophotometers use white tungsten lamps, fine linear gratings, and photodetectors. In 1980, HP developed a new IR/UV/VIS spectrophotometer without moving parts, using a fixed holographic grating and a 2000-pixel diode array detector (DAS). It can quickly complete spectral scans in less than 1 millisecond, after which wavelength concentration calculations can be arranged, and the extent to which reaction kinetics will be suppressed by the baseline can be determined.
The first generation DAS HP 8450A consists of five sample chambers, one beam indicator, and software that automates data collection/analysis. The second generation 8452A reduced costs by 38% and used a color display. The third generation Agilent 8453E costs only 68% of the initial DAS, yet the sensitivity range has expanded by 25%. Agilent DAS is the ideal instrument in PCB chemical laboratories, capable of easily testing wavelengths, calibrating concentrations, and automating chemical analysis.
Due to space limitations, this article is an excerpt. For more content, please clickRead the original text to read online. This article was published in the December issue of “PCB007 China Online Magazine”. For more exciting original content, please follow the “PCB007 Chinese Online Magazine” public account.
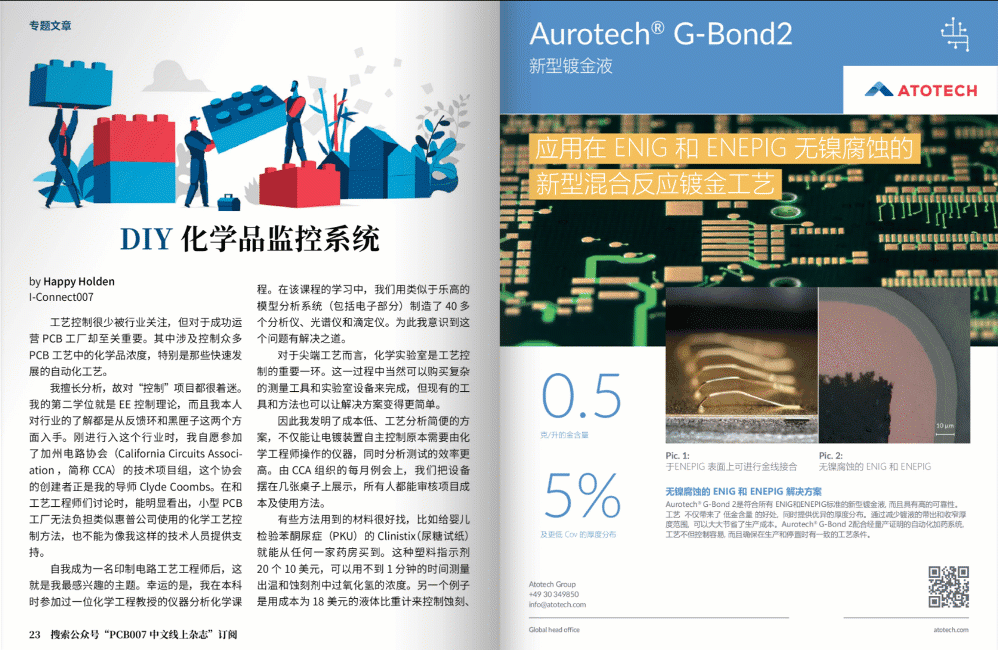
Previous Featured Articles
Dana Korf and Kelly Dack, former chief PCB technology experts at Huawei, explain manufacturing instructions
[The Future is Here] Vertical Conductive Structures—New Ideas for High-Density Printed Circuit Interconnections
[PCB Design] Vertical Conductor Structure: Allegro PCB Editor
Vertical Conductor Structure: Adjusting Signal Performance
[New Book Recommendation] Guide to Printed Circuit Assembly Manufacturers on Low-Temperature Soldering, sincerely produced by Alpha
[PCB Manufacturing] Vertical Conductive Structure VeCS and Microfabrication
Copper-clad laminate manufacturer Panasonic talks about the stability of the CCL supply chain
Copper-clad laminate manufacturer Panasonic discusses the past, present, and future of CCL
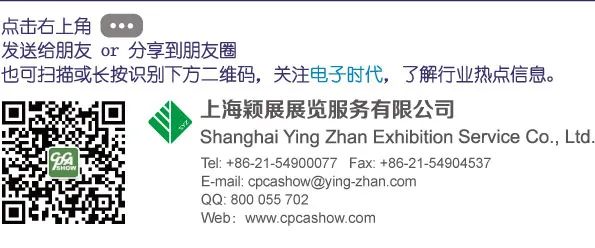