Reminder: This long article contains valuable information. If you don’t read it all, you’ll miss out!
When we place orders at PCB factories, we often have a type of FR-4 material to choose from, such as the one frequently used by Jialichuang, which currently offers three types of materials: FR-4, aluminum substrate, and thermally separated copper substrate.
It seems that FR-4 is a necessary type of material in every PCB factory’s material library. But what exactly is FR-4?
1. FR-4, also written as FR4, is both a name and a standard grade.
The organic substrate materials used for manufacturing PCBs consist of three components: resin, reinforcement material, and conductive copper foil.[1]
Composition of FR-4 copper-clad laminate
As a name, FR-4 refers to laminated boards that use glass fiber cloth as reinforcement material, with an epoxy resin system. This is similar to greeting someone on the streets of Guangdong, calling them ‘handsome’; anyone who thinks they have a bit of good looks will turn around and smile at you
Similar to the term ‘handsome’, FR-4 is just a general term for a category of materials. The glass fiber cloth is woven from electronic-grade glass fiber into a thin, fabric-like material. The glass fiber gives FR-4 the necessary structural stability. This glass fiber cloth is surrounded and bound by epoxy resin with flame-retardant additives. The resin provides rigidity and other physical properties.
The FR-4 specifications are established by NEMA (National Electrical Manufacturers Association), and the commonly used PCB NEMA substrate grade classification is shown in the table below.
Common NEMA PCB substrate grade classification
FR in the NEMA classification standard stands for Flame-Retardant or Fire-Resistant, indicating a fire-resistance grade. Therefore, FR grade materials are flame-retardant materials, while the number “4” distinguishes this material from others of the same grade, indicating that the resin is epoxy resin, the reinforcement material is glass fiber cloth, and the flame-retardant grade is UL94 V-0. The flame-retardant grades FR-1, FR-2, and FR-3 have a UL 94V-1 grade, and the resins and reinforcement materials used differ.
In the 1950s, paper phenolic copper-clad laminates were introduced and widely used in radios and televisions; however, this material had low electrical insulation and was not flame-retardant. Several fire incidents caused by electrical faults in televisions occurred in the USA, prompting NEMA to classify different PCB substrate grades based on the flammability, high-temperature stability, and moisture absorption characteristics of the circuit board substrates, without specifying the electrical performance of the substrates, such as dielectric constant and loss tangent.
I want to emphasize that FR-4 is just one grade in the NEMA substrate classification, representing a category of materials, not a specific material. A common misconception is that FR-4 is often confused with a specific dielectric; for example, in our simulation software, the default dielectric constant for FR-4 is 4.2 and the loss tangent is 0.02, but many low-loss materials are also FR-4 grade materials.
I mentioned at the beginning of the article that it seems that FR-4 is a must-have in every PCB factory’s material library. Why is FR-4 so favored by PCB factories?
2. Why is FR-4 a common material in PCB factories?
The initially widely used PCB materials were paper phenolic copper-clad laminates, such as XPC and XXXPC, due to their relatively low cost, but they are non-flame-retardant materials. After fire incidents in the 1970s caused by circuit faults, major electrical devices began to switch to flame-retardant substrates, and the use of flame-retardant paper phenolic copper-clad laminates FR-1 and FR-2 gradually surpassed that of non-flame-retardant XPC and XXXPC laminates.
In the 1980s, multimedia portable devices became popular, such as portable cassette players and pagers, leading to a trend toward miniaturization and high density in PCBs, and multilayer PCB applications became increasingly common, driving the development of PCB substrates.
Although paper substrates like XPC and FR-1 are cheaper than epoxy glass cloth substrates FR-4, they are inferior to FR-4 in terms of moisture absorption, heat resistance, and mechanical strength. Early on, paper substrates were typically used for price-sensitive consumer products, while FR-4 was more commonly used for industrial products.
However, as consumer devices evolved towards being smaller, lighter, and thinner, the use of FR-4 materials also increased. With standard thicknesses of PCBs ranging from 1.6mm to 0.8mm becoming widespread, the mechanical strength and moisture resistance of paper substrates became problematic. Additionally, paper substrates are unsuitable for multilayer board production, and as devices became smaller, PCB wiring density increased, leading to a higher market share for multilayer boards. Therefore, despite the relatively higher cost of FR-4 materials, consumer products gradually began to shift towards FR-4 materials.
Another important reason why PCB prototype factories widely choose FR-4 over cheaper paper substrates is that paper substrates are not suitable for drilling processes and can only be used for punching processes, while FR-4 is very easy to process.
With the continued expansion of production capacity for epoxy resin and glass fiber cloth materials, standard FR-4 substrates have now become a low-cost material with excellent mechanical properties and outstanding processability, making them favored by global mid-to-low-cost electronic product manufacturers.
Speaking of substrates, I am reminded of last month’s article about PCB quality: PCB prices have dropped, but what about quality?
Today, with increasing price competition, various cost-cutting materials are emerging, unintentionally increasing the risk of product quality for customers. Of course, Jialichuang has always promised to provide genuine A-grade materials, clearly distinguishing themselves from low-grade, less fabric, and non-flame-retardant materials, fully ensuring product quality, which is one of the reasons I love using Jialichuang.
Additionally, Jialichuang has long provided material quality inspection services and can issue free inspection reports for reference. Whether or not the PCB is produced by Jialichuang, you can send it for inspection; if you need, you can try it out.
Enter the Jialichuang order assistant, find the “Material Inspection Service” option on the left side of the page, click “I want to apply for inspection,” and fill out the process (as shown in the image below).
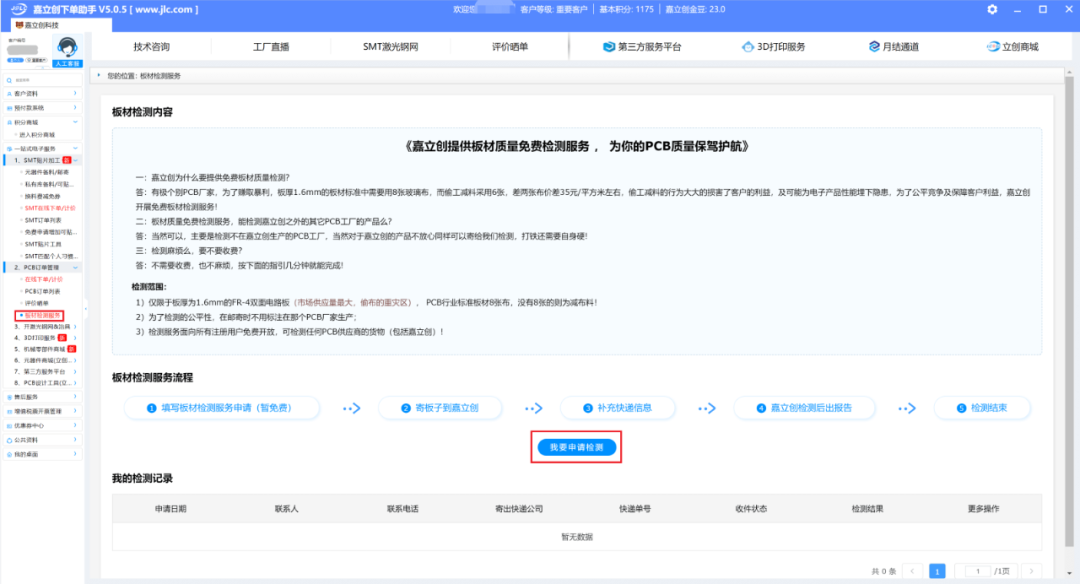
3. Performance indicators of FR-4
FR-4 substrates are based on an epoxy resin system, so the Tg value has long been the most common indicator used to classify FR-4 substrate grades, and it is also one of the main performance indicators in the IPC-4101 specification.
Glass Transition Temperature Tg
The Tg value of the resin system refers to the temperature transition point at which the material changes from a relatively rigid or “glass” state to a deformable or softening state. As long as the resin does not decompose, this thermodynamic change is always reversible. This means that when the material is heated above the Tg value and then cooled back down below the Tg value, it can revert to its previous rigid state with the same properties. However, when the temperature to which the material is heated is far above its Tg value, it may lead to irreversible phase changes. The impact of this temperature is greatly related to the type of material and the thermal decomposition of the resin.
Generally speaking, the higher the Tg of the substrate, the higher the reliability of the material. If lead-free soldering processes are used, the thermal decomposition temperature (Td) of the substrate must also be considered.
Other important performance indicators include the coefficient of thermal expansion (CTE), water absorption rate, adhesion characteristics of the material, and commonly used delamination time tests, such as T260 and T288 tests.[1]
4. Diversity of FR-4
Using glass fiber cloth as reinforcement material, with an epoxy resin system and a flame-retardant grade of UL 94V-0, are all considered FR-4. So, what specific distinctions exist within this broad category of materials?
Classification by Tg value
The most obvious distinction among FR-4 materials is based on the Tg value. Typically, FR-4 laminates are divided into low Tg, medium Tg, and high Tg laminates based on the Tg temperature.
In the industry, FR-4 with a Tg of around 135°C is generally classified as low Tg; FR-4 with a Tg of around 150°C is classified as medium Tg; and FR-4 with a Tg of around 170°C is classified as high Tg.
If the PCB processing involves many pressing cycles, or if the PCB has many layers (more than 14 layers), or if the soldering temperature is high (≥230°C), or if the operating temperature is high (over 100°C), or if there is significant thermal stress during soldering (e.g., wave soldering), high Tg materials should be selected.
Classification by loss
FR-4 can be divided into:
-
Standard loss materials (Df≥0.02)
-
Medium loss materials (0.01<Df<0.02)
-
Low loss materials (0.005<Df<0.01)
-
Ultra-low loss materials (Df<0.005)
Classification by supplier
Different suppliers’ FR-4 grade materials may exhibit different performance characteristics, and even within the same supplier’s FR-4 grade, there are different product specifications. Therefore, the most precise specification for the selected substrate is to specify the exact product name from the specific material supplier.
5. Tips for correctly selecting FR-4 materials when ordering from Jialichuang
Jialichuang currently offers three types of materials: FR-4, aluminum substrate, and thermally separated copper substrate. When placing an order, it is important to choose the appropriate material type.
When selecting the appropriate laminate, it is necessary to consider electrical, mechanical, chemical, and thermal properties comprehensively. However, in general scenarios, medium and low Tg FR-4 will be sufficient.
For high-layer PCBs, Jialichuang also offers high Tg FR-4 options, such as Jialichuang’s “High Multilayer High Precision PCB Manufacturing”, which currently offers a maximum of 20 layers of PCB manufacturing capability. Of course, Jialichuang also provides high Tg, low CTE materials to meet the challenges of high-layer PCB manufacturing.
References:
[1] Printed Circuit Handbook (6th Edition, Chinese Revised Version)