Source: Nano Research
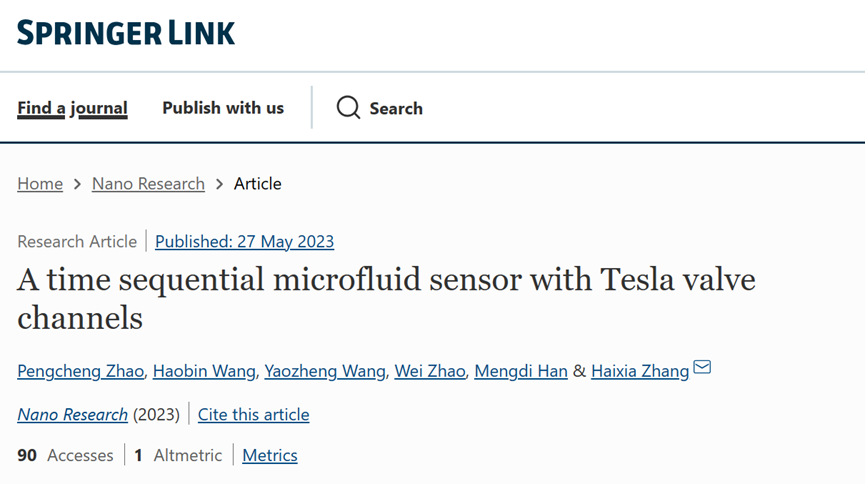
Paper Information: Pengcheng Zhao, Haobin Wang, Yaozheng Wang, Wei Zhao, Mengdi Han, Haixia Zhang. A time sequential microfluid sensor with Tesla valve channels. Nano Research, 2023: 1-7.
Paper Link: https://doi.org/10.1007/s12217-024-10127-7.
Research Background
Sweat is an important source of information about human health, providing insights into body temperature, ion concentration, metabolic products, and biomarkers. To non-invasively monitor sweat composition, researchers have begun to focus on the development of flexible sweat sensors. These sensors can collect and analyze sweat by being attached to the skin’s surface, flexibly adapting to its shape. Electrochemical methods are considered powerful tools for sweat analysis, using electrochemical sensors to detect chemical components in sweat, offering high sensitivity and selectivity. However, researchers face challenges in sweat collection. Current common methods use hydrogels and textiles to collect sweat, but the efficiency of sweat collection is easily affected by materials, driving forces, and channel designs. The Tesla valve, as a channel structure suitable for sweat sensing, can control fluid flow and has good blocking effects. Additionally, the preparation of graphene electrodes is mainly done using laser engraving technology, which significantly enhances electrode performance due to its high precision and resolution.
Research Content
This study developed a flexible wearable sweat patch using continuous Tesla channels (Figure 1a). The patch is attached to the front and back of the human body, utilizing gravity to provide natural liquid driving force. The patch’s inlet is directly connected to a storage chamber, which houses a graphene sensing electrode and is connected to a flow channel via a reverse Tesla valve. The patch’s outlet is a curved opening cut into a polyimide (PI) surface to balance air pressure and serve as an electrode connection point. Figure 1b shows detailed structural parameters of the Tesla valve, with an opening angle of 50° and a channel width of 300 μm, ensuring uniformity and consistency in laser processing. Figure 1c illustrates the laser-induced graphene electrode. As shown in Figure 1d, the patch device includes an adhesive layer, micro Tesla valve sweat channels on a polydimethylsiloxane (PDMS) substrate, graphene electrodes, and a PI layer. The actual device manufactured is shown in Figure 1e. When sweat is secreted by the human sweat glands, it is pushed into the sweat channel inlet, achieving sequential flow, storage, and sensing through gravity. Figure 1f illustrates the sensing mechanism of the device, where the graphene electrode in the microchannel adsorbs uric acid, generating electrons through a voltage oxidation reaction and converting them into a current signal, which serves as the detection signal for uric acid concentration.
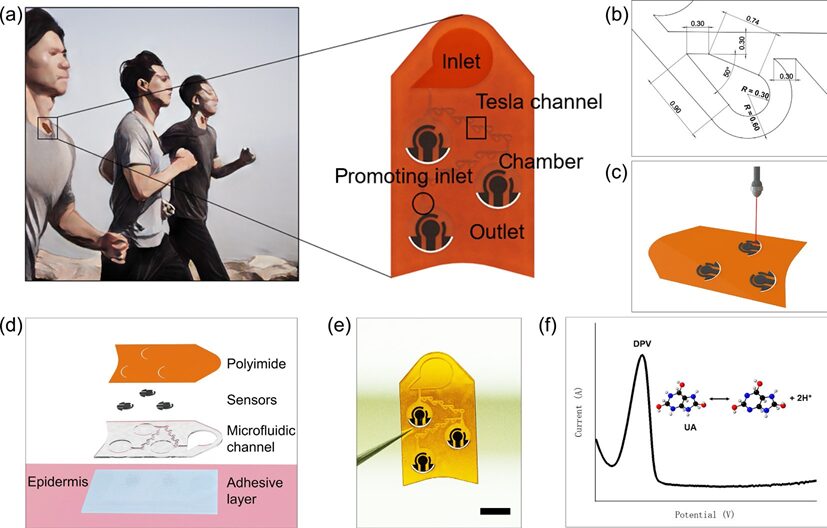
Figure 1 Schematic of the Tesla valve channel and uric acid detection in sweat. a) Wearable sweat collection and sensing patch: sweat collection and patch structure; b) Structural parameters of the Tesla valve; c) Schematic of laser engraving; d) Exploded view of the device; e) Physical illustration of the patch; f) Schematic of the differential pulse voltammetry method for uric acid detection.
Figure 2 shows the process of fabricating the sensor patch. Liquid A and liquid B of PDMS were mixed in a ratio of 1:10, vacuum sealed after stirring, and heated to cure. The cured PDMS was then sculpted for channel patterns and cut for the device outline using a laser scanner. Plasma treatment and immersion in aminopropyltriethoxysilane solution were carried out to prepare for subsequent thermal sealing. Meanwhile, the PI substrate was laser-cut for patterned electrodes and holes. The PDMS and PI substrates were then thermally pressed together to ensure strong adhesion. Finally, a bonding layer was cured on the skin surface, resulting in the final patch device.
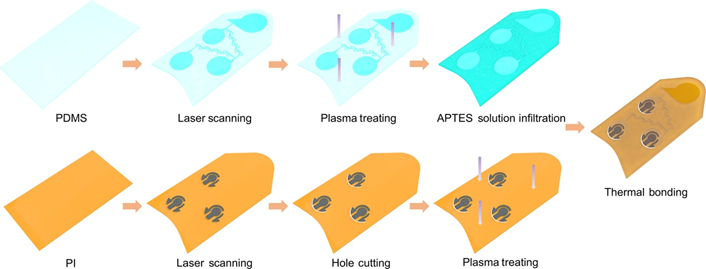
Figure 2 Fabrication process of the Tesla valve-based sweat sensing patch
The article used Ansys 2022 Workbench software to numerically simulate the flow conditions in the sensor. Figure 3 shows the simulation results. The streamline distribution verifies the effectiveness of the channel design (Figure 3a). Figure 3b illustrates the velocity vector distribution revealing the structural design of the Tesla valve, while the pressure distribution indicates that the pressure in the storage chamber varies with gravity, and the pressure in the flow channel is more balanced. The flow of sweat in the Tesla valve is balanced, which results in an expanded distribution in the flow channel. As shown in Figure 3c, a portion of the liquid in the main flow channel enters an annular branch and diverges, with these branches becoming resistance at the end of the main flow channel, limiting the driving effect of the liquid in the flow channel, thereby enhancing the movement into the storage chamber and achieving the desired sequential effect. Figure 3d simulates the process of filling the storage chamber, with simulation results consistent with actual conditions.
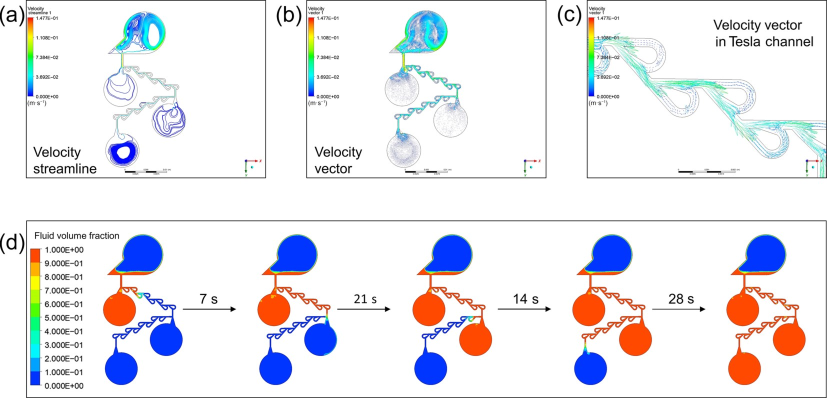
Figure 3 Stimulation of the sweat collection channel based on the Tesla valve a) Streamline distribution in the channel; b) Velocity vector distribution on the patch; c) Fixed velocity vector in the Tesla valve; d) VOF stimulation results in the device
Based on the simulation results, the study also fabricated the device and tested its timed filling performance. Figure 4a defines two Tesla valves as one valve, with the number of valves being a variable factor in the device structure. By comparing the filling times, it was found that the reverse Tesla valve provided greater resistance, while the filling times of direct and reverse Tesla valves were similar. Figure 4b shows the impact of flow shape on the storage chamber’s filling time. The filling time gradually increases from the first chamber to the last chamber, but the trend becomes flatter, indicating that the flow channel provides sufficient resistance. Figure 4c shows the effect of the number of connections on filling time. As the number of connections increases, the filling time increases since the effective path of the flow channel is longer. Figure 4d compares the impact of different channel widths on filling time. When the channel width increases, the filling time decreases, indicating that width affects filling time.
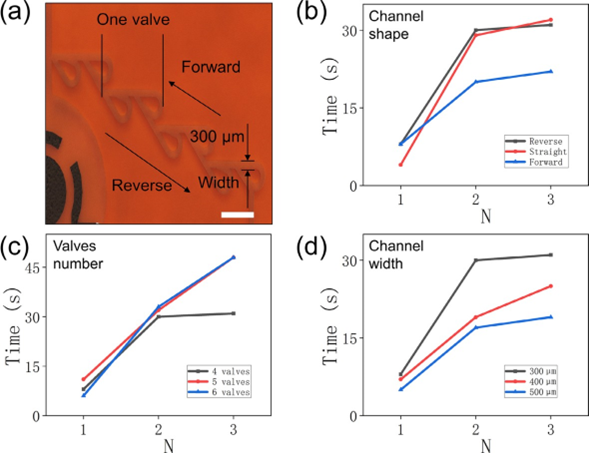
Figure 4 Filling time of devices with different structural parameters a) Schematic of parameters, including number, direction, and width of valves; b) Filling time of devices with reverse, straight, and forward channels; c) Filling time of devices with different numbers of valves; d) Filling time of devices with different channel widths
Figure 5a defines the time sequence of the device, including filling time and filling intervals. Filling time refers to the time from when sweat begins to flow until the storage chamber starts to fill. Filling interval refers to the time interval from one storage chamber filling to the next. Figure 5b shows the impact of different flow channel shapes on filling interval time. The straight channel device cannot provide sufficient resistance, resulting in low resistance in the channel, causing sweat to enter the next chamber before the previous storage chamber is filled, leading to mixing and interference with subsequent sensing. The article compares the effect of the number of valves on filling interval time, as shown in Figure 5c. Increasing the number of valves and the width of the flow channel leads to inconsistencies in filling interval time compared to expected results. This may be due to increased resistance and wall adhesion. Especially after prolonged filling times, wall adhesion plays a dominant role in the filling of sweat in the storage chamber. Figure 5d shows the effect of flow channel width on filling interval time. Under process constraints, 300 micrometers is the most suitable range for channel width. A larger channel width reduces resistance, breaking the balance between resistance and gravity, leading to the basic conditions for timing no longer being met.
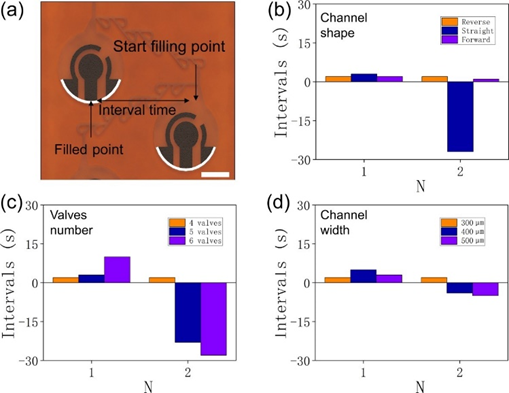
Figure 5 Filling sequence of devices with different structural parameters a) Schematic definition of interval time; b) Interval time of devices with reverse, straight, and forward channel shapes; c) Interval time of devices with different numbers of valves; d) Interval time of devices with different channel widths
When sweat flows through the Tesla valve channel, electrodes in each storage chamber can be used for detection. Figure 6a illustrates the working principle of a three-electrode uric acid sensor. When uric acid is oxidized at the working electrode, it outputs a corresponding current signal under the influence of differential voltage signals. Figure 6b shows the structure of the working electrode obtained through scanning electron microscopy. The porous graphene structure can enhance the contact area with sweat, increasing sensitivity when uric acid molecules adsorb onto it. Figure 6c displays the output signal of different concentrations of uric acid obtained using differential pulse voltammetry, showing a linear range of 0.5 to 250 mM, with a nonlinear relationship as the concentration increases. To verify the flexible performance, experiments were conducted at bending angles of 0°, 20°, 40°, and 60°, finding that peak values remained relatively stable, as shown in Figure 6d. After hundreds of bending cycles, peak current also remained stable, as shown in Figure 6e, indicating the stability of the device. The experimental results in Figure 6f demonstrate the repeatability of the peak current response for uric acid over several cycles. The results in Figure 6g indicate that the sensor does not respond to glucose, urea, and lactic acid.
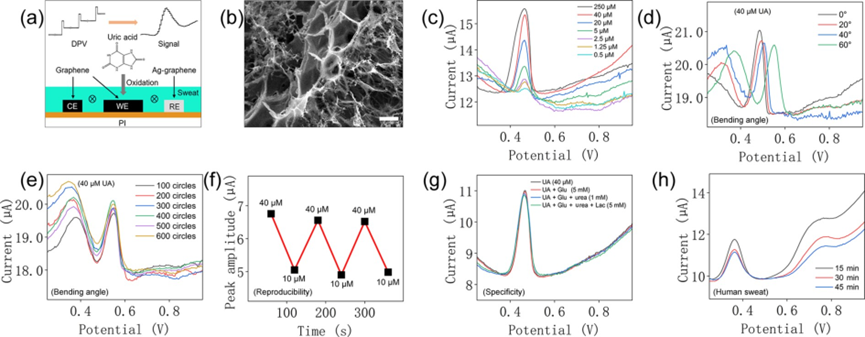
Figure 6 Performance of the uric acid sensing patch a) Schematic of the three-electrode uric acid sensing reaction; b) Scanning electron microscope image of the graphene electrode; c) Uric acid sensing using differential pulse voltammetry; d) Differential pulse voltammetry curves at different bending angles; e) Differential pulse voltammetry curves after bending cycles; f) Current peak response curve for different uric acid concentrations; g) Specificity verification through stepwise addition of glucose, urea, and lactic acid; h) Uric acid sensing curve from actual human sweat generated during running at different time intervals
Summary and Outlook
This study designed a wearable sweat uric acid sensing patch inspired by the Tesla valve. The design combines the directional characteristics of the Tesla valve with gravity to achieve sequential collection and storage of sweat, thereby improving the accuracy of sweat sensors. Through laser-induced graphene technology, the concentration of uric acid in sweat can be scientifically measured in the patch. This research provides a solution for enriching human health management data and is significant for real-time transmission of health data via wearable devices.
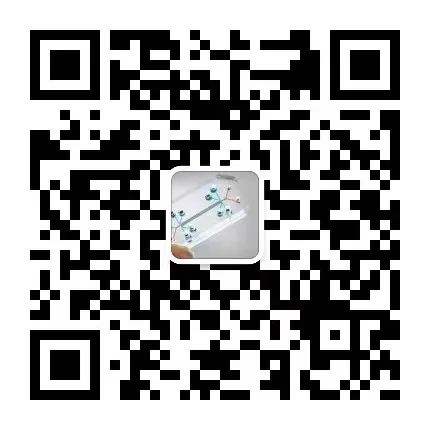
WeChat ID | Heat Transfer and Mass Transfer