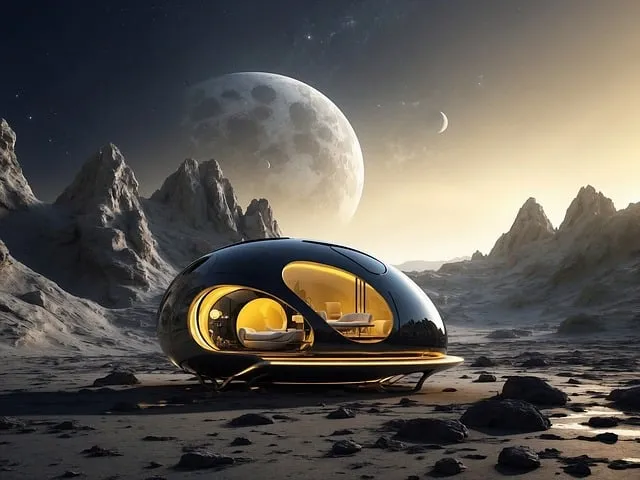
Author | littleshrimp
Produced By | Automotive Development Circle
Disassembling the Volkswagen Engine ECU:
EEWorld user littleshrimp received an engine ECU removed from a scrap Volkswagen. Through his detailed disassembly, he discovered many common classic chips, as well as many unique design aspects. (Original post from EEWorld forum, welcome to enter the link to communicate with the author of this article: https://www.eeworld.com.cn/aaXLy9K)
The lack of chips on the back is intriguing, while the chip combination on the front showcases its complex functionality. The internal PCB layout presents a unique design; however, it is puzzling that some chips, especially most of the ST chips, have no data sheets available, which greatly hinders a thorough understanding of their specific parameters and functions. Additionally, the method of securing the crystal oscillator is also different, using a base for fixation, contrasting sharply with the common practice of using solder on development boards. Moreover, the device has numerous interfaces, but due to the unclear purposes, effective pin testing cannot be conducted, which also sets obstacles for further exploration of its working principles and application scenarios. Let's follow our disassembly to explore further!
It is uncertain which car model this device is specifically used in.
There is also a suspected air hole on the back.
The shell of this device has unique craftsmanship, surrounded by a large amount of gray sealant. Despite years of exposure, its softness remains good, possibly to ensure that internal components are protected from external environmental interference, serving to prevent water and dust, as well as stabilizing the structure.
The back of the PCB has no chips, and the chips underneath are mostly Infineon and ST.
The main control chip uses Infineon’s C167CR solution, which should be the core brain of the entire system, responsible for coordinating and controlling the operation of various functions.
It is also equipped with AMD’s 4Mbit FLASH.
Used for storing programs and data; IDT (now acquired by Renesas) 256Kbit SRAM supports fast read and write of data.
TI’s TPIC8101 serves as the interface chip for vibration and engine knock sensors, playing a key role in sensing the engine’s operating state.
Various Infineon chips also demonstrate their capabilities, such as the TLE 7209–2R 7A H-bridge driver chip used to drive relevant components.
Infineon’s A2C56211 low-dropout triple voltage regulator ensures stable voltage supply.
Infineon’s BTS4140N high-side power switch effectively manages the power supply.
EPCOS’s telecom data line choke filters signals and resists interference, while Infineon’s TLE6250 high-speed CAN transceiver is responsible for data transmission.
The rest are some chips for which no data sheets can be found.
It is quite strange that most ST chips also have no data sheets available.
This type of crystal oscillator uses a base for fixation; previously, I only saw soldered directly on development boards.
With so many interfaces, it is impossible to test what these pins are for.
Although it is currently uncertain which model of Volkswagen this device is specifically used in, this disassembly undoubtedly opens a window for us to understand its internal structure, laying the foundation for further in-depth research and analysis, while also stimulating our interest in exploring its more unknown functions and application areas, providing valuable references for the development of automotive electronic technology.
Disassembly Reveals Lynk & Co 360-Degree Surround View:
For drivers, blind spots during driving are undoubtedly a safety hazard that cannot be ignored. Fortunately, the 360-degree surround view system provides an effective solution. Its working principle is quite straightforward: the system captures images of the surrounding environment through multiple high-definition cameras installed around the vehicle and then utilizes the onboard processor to synthesize these scattered images into a seamless panoramic view. This panoramic view is clearly displayed on the vehicle’s central control display or streaming rearview mirror. Additionally, the system offers a range of auxiliary functions, such as dynamic trajectory lines and distance prompts, to help drivers better understand the situation around the vehicle.
As an automotive safety feature, the chip selection and technical scheme inside the 360-degree surround view system undoubtedly arouses our strong interest. Today, we will disassemble a Lynk & Co brand 360-degree surround view computer to satisfy everyone’s curiosity about the secrets behind this technology.
This is a Lynk & Co 360 surround computer that has been exposed to water, and most of the screws have been removed by someone else.
After opening the shell, the internal rust is quite severe.
The board supports 4 camera inputs and one display output interface, and it overall uses NXP’s solution. After being cleaned with tap water, it looks pretty good.
The video processor is MCIMX6DP6AVT1AA, NXP’s i.MX 6DualPlus Automotive Applications Processors.
The coprocessor is SPC5604CAMLL6, NXP’s 32-bit microcontroller – MCU NXP 32-bit MCU, Power Arch core, 512KB Flash, 64MHz, -40/+125degC, Automotive Grade, QFP 100.
The display interface uses MAX9277GTM/V, Maxim’s 3.12Gbps GMSL Serializers for Coax or STP Output Drive and LVDS Input.
The camera data acquisition uses MAX9286GTN+, Maxim’s four-channel 1.5Gbps GMSL deserializer, with coaxial or STP input and CSI-2 output.
The flash memory is SDINBDG4-8G, SanDisk’s SanDisk® iNAND® 7250 Industrial Embedded Flash Drives.
The memory consists of 2 chips on the front and 2 on the back, totaling 4 chips of Nanya’s NT5CC128M16JR-EK Commercial and Industrial DDR3(L) 2Gb SDRAM, totaling 8Gb.
The power management chip is MMPF0100FAAZES, NXP’s 14 channel configurable power management integrated circuit.
A TJA1043 NXP High-speed CAN transceiver is used for communication with the bus.
This chip is quite rare, likely the PCF8563T NXP real-time clock ULTRA LO PWR CLK/CAL RTC IC. It is unclear why the surround computer needs a real-time clock chip.
The main power uses two LMR23630AQDDAQ1 TI switching regulators, Automotive Qualified SIMPLE SWITCHER 4V to 36V, 3A Synchronous Step-Down Converter 8-SO PowerPAD -40 to 125.
And an LM22677/-Q1 TI’s 42V, 5A SIMPLE SWITCHER® buck regulator.
The overall workmanship is quite good, and the materials used are quite “solid”. Finally, I supplied it with 12V from an adjustable power supply. I found that some places had data output.
Using a multimeter to test each power module’s voltage should be normal. After working for a while, using thermal imaging, it can be seen that the overall temperature rise is quite normal, indicating that most chips are working properly.
The screen output interface shows no waveform, speculating that the i.MX 6 needs the coprocessor to receive commands from the host before it can operate.
The board is overall in good condition except for slight corrosion on some components. It seems to work normally now, but I’m not sure how to wake it up without the ECU. For now, it is at least a development-ready i.MX 6 video development board.
Disassembling BMW Night Vision System: Infrared Camera
I bought several night vision cameras on a certain fish platform, this is the NV3 version using a 4-pin HSD connector, slightly smaller than NV2. (For the specific disassembly process and high-definition images, please browse the forum:https://www.eeworld.com.cn/abrzDy1)
Removing the lens and protective lens reveals the heating coil inside, with a 0603 thermistor on the heating coil that can be used to detect the temperature on the lens to decide whether to heat the lens.
After opening the back cover, the un-soldered pads on the power board are white, probably using a silver plating process. The solder pads in contact with the shell show severe oxidation, indicating that this camera has likely been exposed to moisture.
The back of the power board has fewer components, and compared to NV2, a lot of BOM costs have definitely been cut.
The main chips on the power board include a MAX9259GCB LVDS communication chip. MAX9259 is the transmitter, and paired with MAX9260 can achieve 3.125Gbps data communication. The most amazing part is that it can achieve low-speed bidirectional data communication, such as I2C or UART, on two LVDS lines while also adjusting the data transmission, making device interconnection more convenient.
MAX1793EE33 is a 3.3V LDO that can provide 1A of current.
Silk print Q20C is TI’s ADC104S021Q, a 4-channel 10-bit ADC chip supporting a sampling rate of 50K~200KSPS.
Silk print 504WG is an SPI interface EEPROM chip M95040 from ST.
The back 2938 is ADI (Linear)’s LTC2938, a voltage monitoring chip.
PHH1 is TI’s TPS79318, a fixed output LDO with 200mA at 1.8V.
541GQ is TI’s TPS57140QDGQRQ1, a Buck converter with 3.5V~42V input and 1.5A output.
After removing the power board, there is also an FPGA core board inside, which includes the FPGA, FLASH, DDR chips, and a MOLEX 40-pin board-to-board connector for connecting to the sensor.
The back includes a DC-DC converter and a MOLEX 80-pin board-to-board connector for connecting to the power board.
The back 07QJJXP is TI’s LP3907-Q1, a high-current I2C configurable buck converter that provides default outputs of 1.2V and 3.3V along with 0.8V and 2.5V LDO outputs, totaling 4 outputs.
The front includes an automotive-grade FPGA.
Silk print D9PGM is Micron’s 512M (16MX32) DDR memory.
Silk print DCERZN is ON Semiconductor’s NCP1403, a boost converter.
L0DB is TI’s LP2951-N, a 100mA LDO with 2.3V~30V input.
PHU1 is TI’s TPS79333DBVRQ1, a 200mA LDO.
After removing the FPGA core board, the sensor can be seen on the edge, FLIR ISC0901B0, a 17um 366*256 60fps 14-bit data output thermal imaging sensor.
Compared to the NV2, the ISC0601 size is smaller, and it looks simpler without the protective lens.
The gold wire on the side of the sensor is easily broken if not careful.
Upon zooming in, the FLIR ISC9001B0 label can be seen.
The shell bears the logos of BMW and Autoliv manufacturers.
The shutter in front of the lens is used for flat-field calibration, closing when powered on.
Internal lens image after removing the sensor.
Removing the lens requires a “special” disassembly tool.
After removing the lens, there is a metal spring and a thin film gasket inside.
The lens assembly is much simpler compared to the NV2 camera.
NV3 has a black ring and a white ring version.
The white ring’s lens size is larger than that of the black ring, and there are more components for installation and vibration reduction compared to the black ring.
I’m starting to prepare to reverse engineer the Altera board and then develop on it, as it communicates with numerous buses on the power board. I could draw a power board myself and use it to communicate with MAX9259GCB to drive the LCD or TF card. However, it seems quite challenging, and I probably won’t have time to do it. Next, I plan to add a data acquisition board between the sensor and the FPGA board to read the data directly and see what comes out.
This account maintains neutrality regarding all original and reprinted articles’ statements and viewpoints, and the articles pushed are for readers’ learning and exchange purposes only. The copyright of articles, images, etc., belongs to the original authors. If there is any infringement, please contact to delete.
Summary of Four Common RS-485 Isolation Solutions
RJ45 Network Unable to Connect After ESD Testing: Debugging Case Study
Buck DC-DC Circuit 300MHz~400MHz Frequency Point Radiation Emission Case Analysis
Share 💬 Like 👍 Looking ❤️
Support quality content with a “three-click” action!