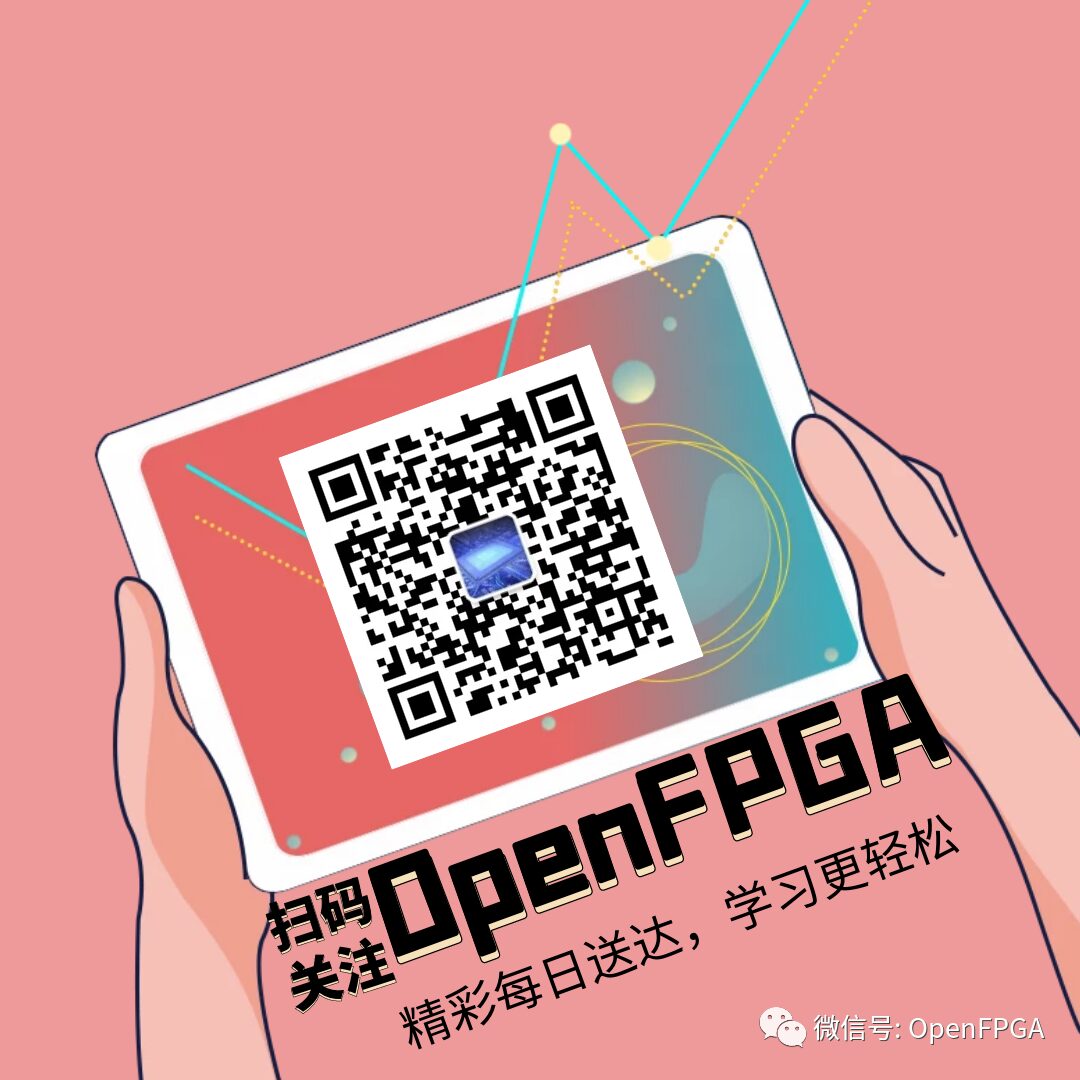
Let’s talk about Xilinx’s MIPI solution. Here, we take the ordinary 7 series as the discussion object, while Xilinx’s high-end KU+/MPSOC+ already support MIPI interface IO directly.
Due to the special nature of MIPI signals, low power consumption should be fully considered at the design stage. Therefore, the native signal levels of MIPI support both HS and LP modes, operating at different voltage standards:
From the figure, it can be clearly seen that MIPI electrical signals exist in two voltage modes simultaneously. If connected to the FPGA pins, it is evident that the FPGA cannot support this. Moreover, the voltage standard of HS mode is also not supported by the FPGA. Therefore, Xilinx has provided two schemes to achieve MIPI signal level conversion, which is detailed in document XAPP894. Below, only the MIPI DPHY Rx part is provided.
In cases of higher MIPI line rate, this method is not recommended.
When used for receiving a camera, only the MC20901 is needed.
The premise for MIPI debugging is that you have correctly completed the sensor configuration. It is recommended to obtain a set of verified configurations from the internet or FAE to drive the sensor. This way, the focus of debugging can be placed on the MIPI part. (To add, one concept I remember most from high school biology is: when conducting experiments, variables must be controlled, and only by satisfying the repeated comparison of a single variable can issues be explained. However, in work, many times when problems arise, the positioning is often just random guessing.)
Since the Xilinx MIPI RX Subsystem IP solution is used, the parts that users can configure are actually quite limited. However, this subsystem is composed of two IPs: one is MIPI-DPHY, and the other is MIPI-CSI2 interface, and the two IPs are interconnected via PPI interface.
MIPI DPHY receives the bitstream data and then recovers the packet according to the frame format. The protocol includes ECC checks for the packets, providing a certain ability to identify and correct errors. However, if the signal quality is poor and many errors occur, unrecoverable errors will appear, resulting in artifacts on the image, such as misalignment causing lines to appear or even color distortion. After synthesis is completed, open the synthesized schematic, enter the MIPI DPHY section, mark the signals with the suffix err in the physical layer for debugging, and then save them to the xdc file for later debugging.
From the figure, it can be seen that the error signal errorths in the Xilinx MIPI IP PPI interface is pulled high, indicating that there is a row loss situation. If this occurs and the physical layer error signals continue, then after checking that the FPGA project itself is fine, hardware issues should be considered.
This article is reprinted from Blog Garden:
https://blog.csdn.net/wuyanbei24/article/details/104603426/
The content of this article only represents the author’s views and does not represent the platform’s views.
If there are any objections, please feel free to contact us.
– END –
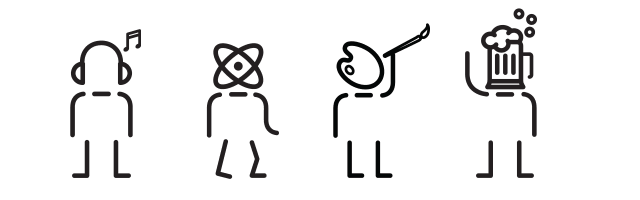
NOW act now!
Recommended Reading
【Vivado那些事】如何查找官网例程及如何使用官网例程
【Vivado使用误区与进阶】总结篇
【Vivado那些事】Vivado中常用的快捷键(二)其他常用快捷键
SystemVerilog数字系统设计_夏宇闻 PDF
Verilog 里面,always,assign和always@(*)区别
图书推荐|ARM Cortex-M0 全可编程SoC原理及实现
简谈:如何学习FPGA
Vitis尝鲜(一)
拆解1968年的美国军用电脑,真的怀疑是“穿越”啊!
一文最全科普FPGA技术知识
你见过1-bit CPU吗?
高级FPGA设计技巧!多时钟域和异步信号处理解决方案
【Vivado那些事】Vivado中电路结构的网表描述
现代计算机的雏形-微型计算机MCS-4
世界上第一个微处理器真的是Intel 4004吗?其实这是个很复杂的故事…
【每周一问】如何控制加载FPGA程序时,Xilinx FPGA的IO管脚输出高低电平
【Vivado那些事】vivado生成.bit文件时报错-ERROR: [Drc 23-20]
AD9361 和Zynq及其参考设计说明
1202年了,还在使用虚拟机吗?Win10安装Ubuntu子系统及图形化界面详细教程
谈谈Xilinx FPGA设计的实现过程
Github 上有哪些优秀的 VHDL/Verilog/FPGA 项目
AD936x+ZYNQ搭建收音机(一)
AD936x+ZYNQ搭建收音机(二)含视频演示
AD936x+ZYNQ搭建收音机(三)-终篇
AD936x+ZYNQ搭建OpenWIFI
Verilog 版本:Verilog-95、Verilog-2001与System Verilog区别简谈
FPGA时钟设计方案
无招胜有招-Vivado非工程模式下的详细设计
追寻ARM的起源-Acorn电脑简史及FPGA实现
面试中经常会遇到的FPGA基本概念,你会几个?
点击上方字体即可跳转阅读