The launch of powerful, compact single-board computers has driven the design of several new products, where its utility is particularly evident in applications that optimize cost and efficiency through miniaturization. Additionally, vision systems can leverage comprehensive board-level machine vision cameras to further reduce overall product size and achieve operational flexibility, while also supporting custom or non-standard optical components. They are used in: medical diagnostics, measurement, robotics, embedded vision, packaging and printing inspection, handheld scanners, desktop laboratories, and other space-constrained systems.
Today, I will provide a detailed analysis of
the important steps to consider when
choosing embedded vision cameras
such as: functional groups, form factors, and physical space requirements
interface options, lens mounts, software support
thermal management, and electromagnetic compatibility, etc.
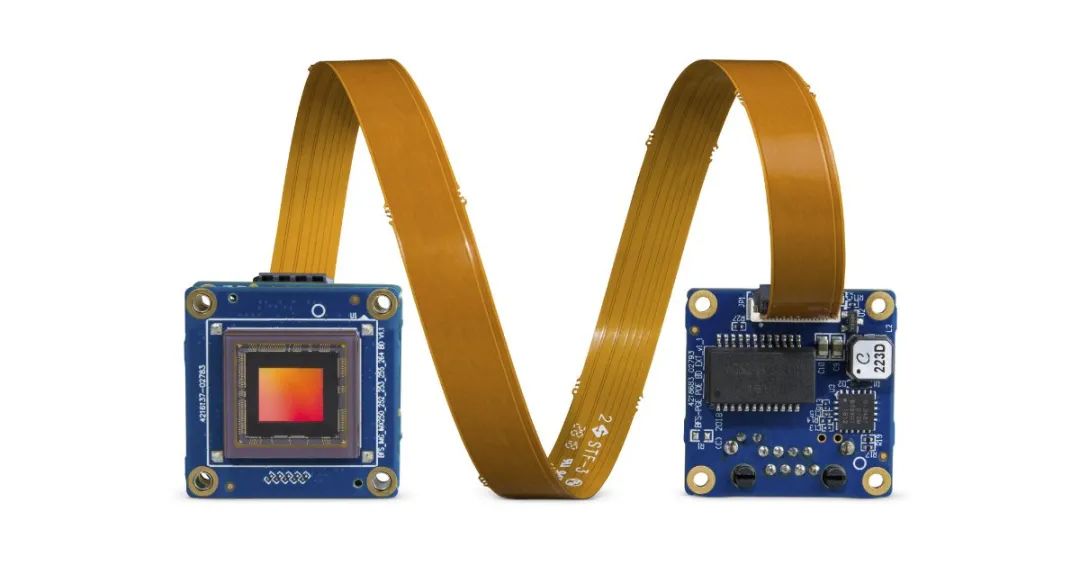
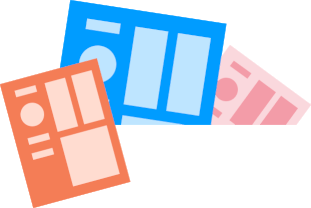
Form Factors and Functional Groups
When transitioning from packaged cameras to board-level cameras, system designers should carefully consider their imaging and camera performance requirements. Many small board-level cameras only support low-resolution sensors, a limited number of GPIO lines, and have restrictions on the internal functions of the camera. In contrast, many fully functional machine vision camera board models are merely standard cameras with the housing removed. While these cameras can achieve the desired imaging performance, their size may not be significantly smaller than standard packaged models. These types of cameras often use standard GPIO and interface connectors, making them unsuitable for embedded applications due to their larger size. For example, the size of traditional industrial locking connectors is similar to that of a Blackfly S board-level camera.
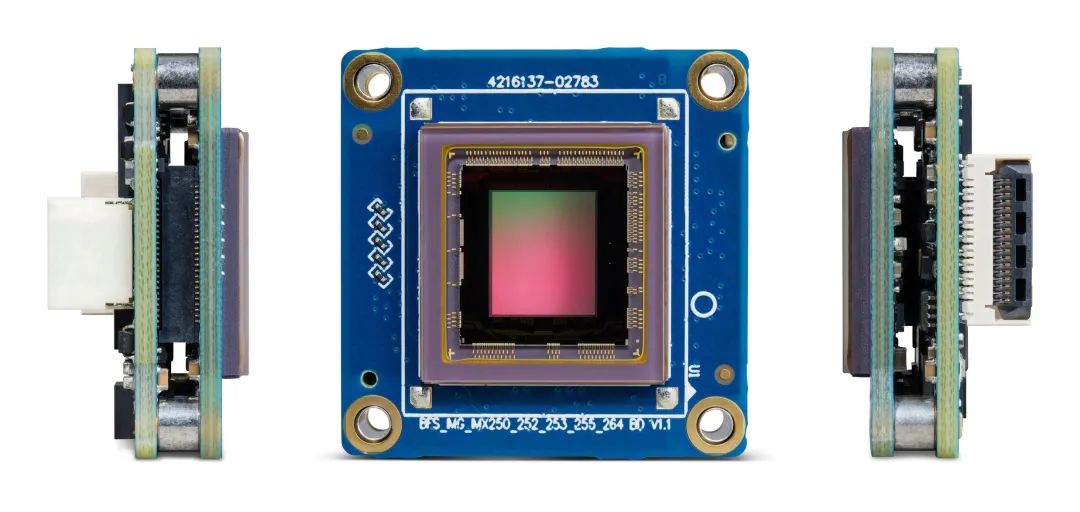
FLIR Blackfly S Board-Level Camera
The FLIR Blackfly S board-level cameras are designed specifically for embedded systems. They have a very compact size of only 29mmx29mmx10mm and provide the same imaging performance and full rich functionality as the packaged Blackfly S models; the compact GPIO and interface connectors save additional space. Another significant advantage of FLIR’s embedded vision camera products is that all cameras using sensor sizes from 1/3″ to 1.1″ share the same form factor, which simplifies the development and upgrade of systems and future product variations.
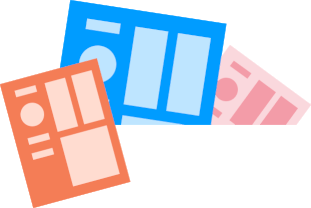
Lens Mounts
For customers looking to integrate non-standard optical components or place image sensors as close to the target as possible, board-level cameras are an attractive option. Board-level cameras do not have fixed lens mounts, allowing designers to freely choose optical components, and the machine vision industry typically does not use standard C, CS, or S interface lenses. This design is also very suitable for biotechnology and laser beam analysis applications that typically do not require lenses. Another common application for board-level cameras is to integrate the lens mount into another product component, thus referred to as “embedded vision.” Additionally, molding the lens mount directly into the product housing can effectively simplify manufacturing and assembly, thereby further reducing costs. To evaluate board-level cameras without lens mounts, installation accessories should also be purchased. If the packaged model has the same sensor and functionality as the board-level model, they can serve as a development platform.
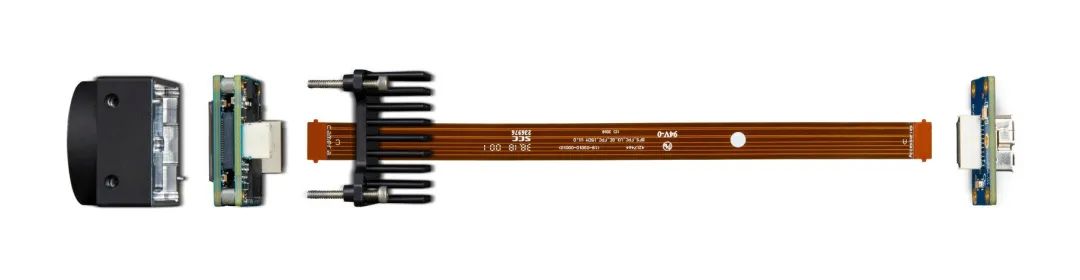
When selecting the right lens mount options for board-level cameras, one of the most important factors is the size of the sensor used. Typically, S-type mounts are designed for low-resolution sensors (usually less than 2MP) that are 1/3″ or smaller. CS-type mounts are designed for 1/3″ to 1/2″ sensors, and if the sensor size is 1/2″ or larger, it is best to use C-type mounts.
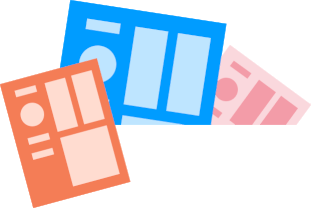
Thermal Management
Packaged machine vision cameras rely on their housing surface area to dissipate heat generated by sensors, FPGAs, and other components. Without a housing, there may be additional design requirements for high-performance board-level cameras to ensure they operate within the recommended temperature range. In this case, providing sufficient heat dissipation is key. Manufacturers typically provide the maximum junction temperature for the hottest components. For the FLIR Blackfly S camera, the specified maximum junction temperature for the FPGA is 105 ℃ (221 ℉).
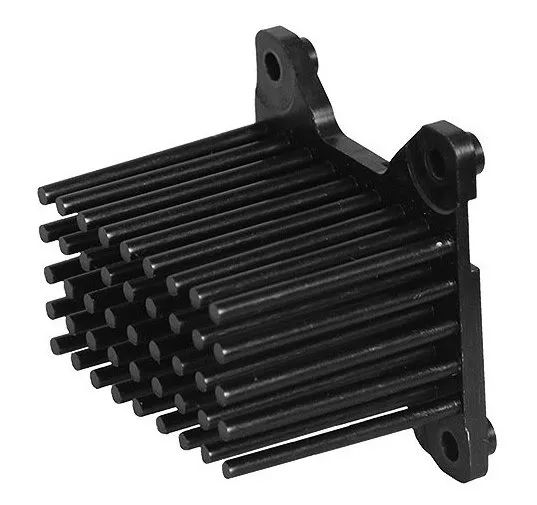
System designers must ensure that their thermal management solutions meet this specification. The size of the heat sink, the surface area of the rack on which the camera is mounted, or the type of active heat sink required depend on the sensor, frame rate, operating environment, and the number of camera image processing tasks being performed. To facilitate the installation of heat sinks on the camera, we recommend using thermal paste on thermal pads to minimize board stress on the camera.
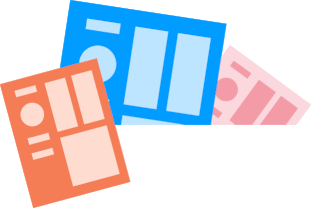
Housing Design and Rapid Prototyping
In most cases, board-level cameras are directly integrated into embedded vision systems/products without the need for housing. However, for applications where the camera is not integrated with a specific product and the internals are exposed to components, it may be necessary to prevent damage with a housing. In rapid prototyping, embedded system designers can easily design and print a camera housing using a 3D printer or use a universal plastic housing large enough to accommodate the camera, then install the camera in place using spacers and mounting brackets.
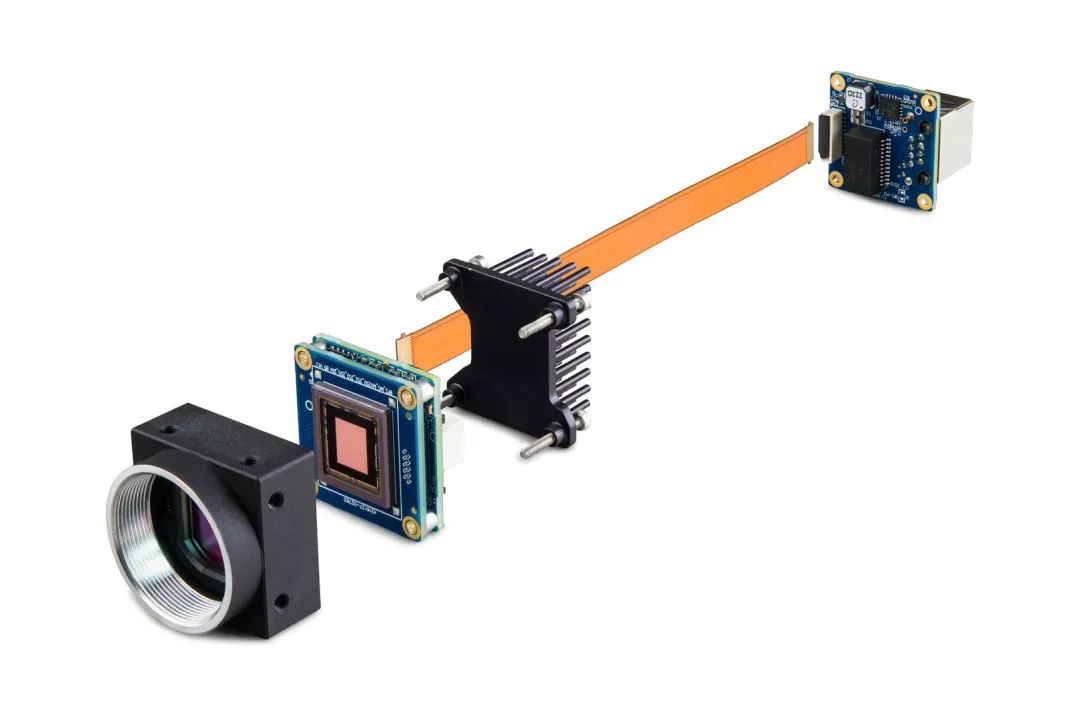
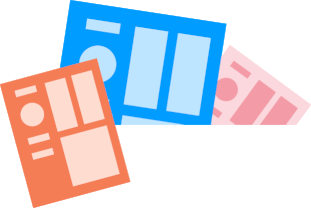
Interfaces and Connectors
The first-generation USB 3.1 is an ideal interface for embedded systems, as its universal functionality ensures support for a variety of hardware, from desktop computers to ARM processor-based single-board computers (SBC). Direct memory access (DMA) keeps latency to a minimum without using filter drivers. The first-generation USB 3.1 also uses a single cable for power and can provide data throughput of up to 480 MB/s, effectively simplifying mechanical and electrical design.
One important goal for embedded system designers includes miniaturization of existing designs. In this case, the maximum cable length is far less important than the size of the cable and connectors. Flexible printed circuit (FPC) cables support the first-generation USB 3.1 with lengths of up to 30 meters. FPC cables, as the name suggests, are cables that can be bent and twisted to fit tightly packaged systems. Additionally, high-quality locking connectors and shielded FPC cables with locking tabs ensure highly secure and reliable connections.
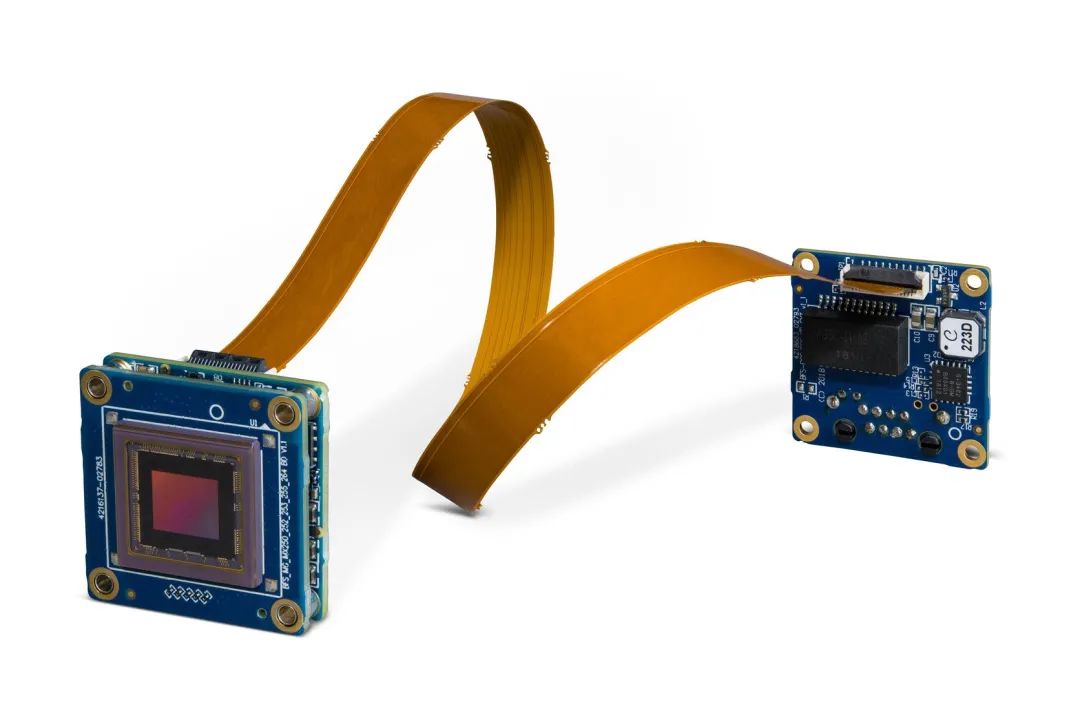
However, the USB 3.1 interface has a potential drawback, as its high-frequency signals can cause interference to wireless devices up to 5 GHz (such as GPS signals). For applications using such wireless frequencies, we also offer FLIR board-level cameras with GigE interfaces.
MIPI CSI is another universal interface used by many embedded motherboards. However, compared to USB, the complexity of the MIPI protocol and drivers can make development more time-consuming. Low-voltage differential signaling (LVDS) interfaces are also available and are designed for direct connection to host-side FPGAs; however, each signal transmission channel requires two wires, which is a small yet significant drawback in some applications.
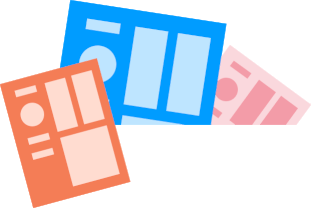
Software Support and Electromagnetic Compatibility
When selecting cameras for embedded systems, software support is an important consideration that cannot be overlooked. With SDKs that support both desktop and embedded systems, designers can easily develop vision applications with familiar tools and deploy them seamlessly on their chosen embedded platforms. FLIR’s Spinnaker SDK supports Windows and Linux desktop systems based on x86, x64, and ARM processors.
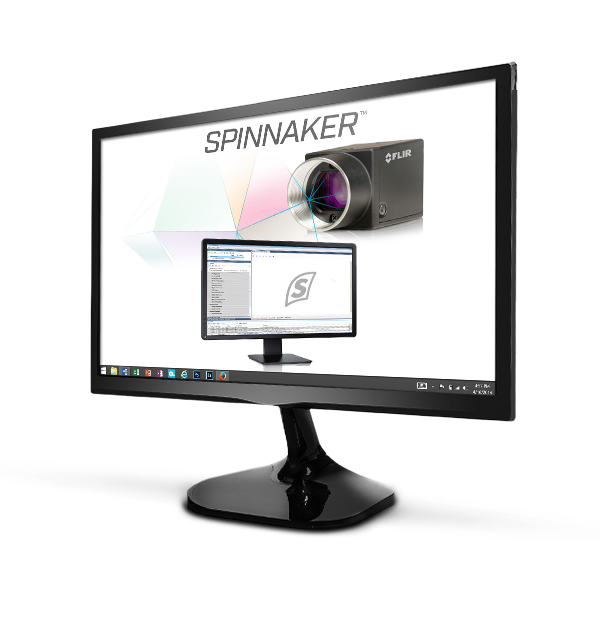
If there is no shielding provided by a housing, the electromagnetic compatibility (EMC) of board-level cameras will differ from packaged models. All packaged FLIR machine vision cameras are EMC certified, but board-level cameras have not undergone this certification. These board-level cameras are to be embedded in other products/systems, thus requiring separate certification for the finished product. For any application, we recommend following best practices for electromagnetic interference (EMI) management, just like other electrical components.
Blackfly S Board-Level
FLIR Blackfly board-level variants are high-performance machine vision area scan cameras designed for embedding in tight spaces. Unlike many other board-level cameras, they have rich functional groups suitable for the latest CMOS sensors; the functional groups are the same as those of the boxed version. With reliable compatibility, they can be integrated into mainstream SBCs and SOMs at any time. The Blackfly S board-level models use embedded system connections, with rich features that enable OEMs to develop smaller, lighter, and lower-cost solutions.
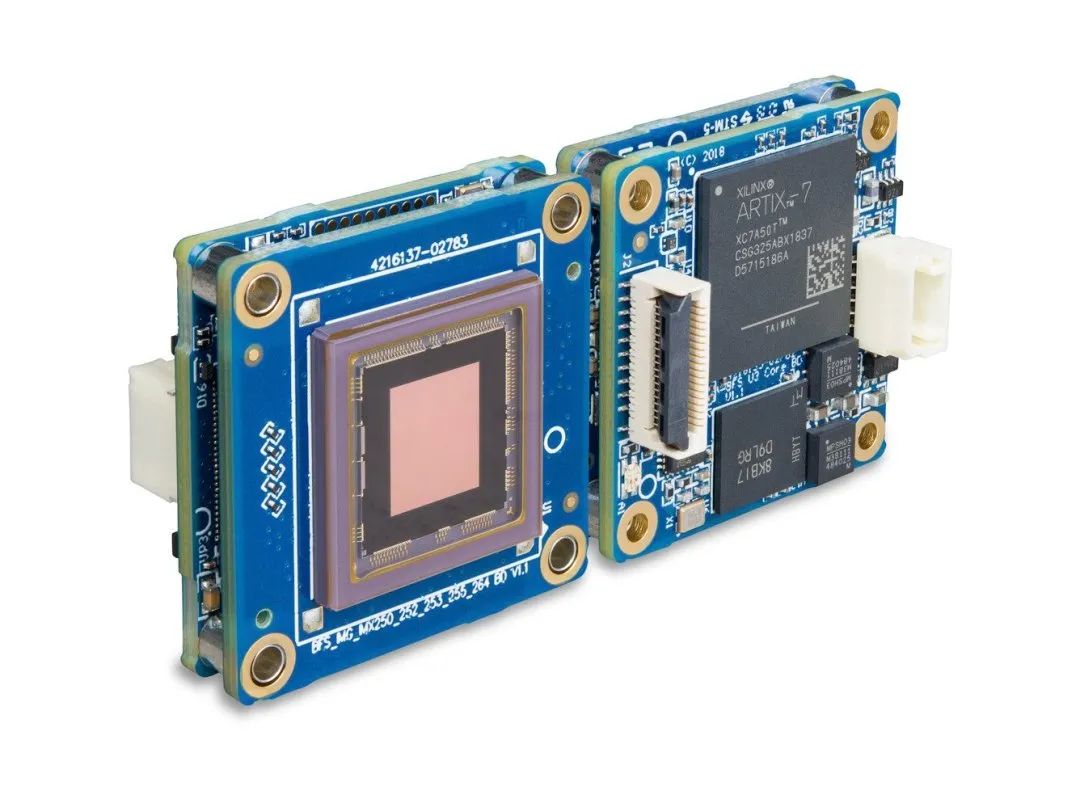
The innovation of board-level cameras in embedded vision systems allows for more freedom and flexibility in the design of compact, multifunctional innovative products. In addition to the factors mentioned above, attention should also be paid to using high-quality sensors, optical components, and reliable parts to ensure your embedded system is future-proof. FLIR’s full range of board-level cameras is designed for these applications and offers an industry-leading 3-year warranty.
For friends who want to learn more about FLIR machine vision products
you can click to follow the official WeChat account of “FLIR”
to discuss more professional knowledge~
Click “Read the original” to discover more secrets~
FLIR Machine Vision
FLIR’s machine vision department produces and sells over 250 models of visible light cameras, with resolutions ranging from 0.3 megapixels to 31 megapixels. Cameras come in various forms, including board-level and closed user interface options such as USB3, GigE, and 10GigE. FLIR’s machine vision department designs, manufactures, and distributes its cameras and related software to customers worldwide to establish systems that improve the efficiency, quality, analysis, and safety of various processes and products.
Scan to follow us
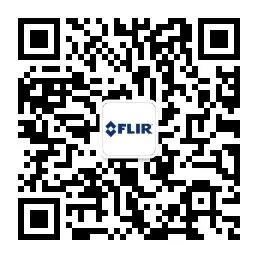
WeChat ID: FLIR-China