In the second half of 2020, the global chip shortage was caused by a supply-demand imbalance due to the outbreak of the pandemic and the rise of new energy.
The most typical example is the automotive MCU. The outbreak of the global pandemic led to a reduction in the capacity of wafer fabs, with companies like STMicroelectronics, NXP, and Microchip announcing extended delivery times, and inventories were quickly depleted. For the first time, the global automotive supply chain faced a shortage crisis.
By March 2021, the shortage crisis had still not been resolved. Renesas, the second largest MCU market share holder, experienced a noteworthy fire, further impacting the already strained chip supply chain.
Before that, NXP, the largest MCU market share holder, and Infineon, the third largest, were both affected by rare snowstorms, causing their U.S. factories to halt production.
In November, a factory of STMicroelectronics in Europe went on strike due to pandemic-related pay issues, igniting a global shortage of automotive MCUs.
The result of the supply-demand imbalance was that MCUs transformed from being a low-cost commodity to a highly sought-after product. Manufacturers raised prices; Renesas and NXP increased the prices of automotive MCUs by 20%-30%; STMicroelectronics raised its prices from over one dollar to over seven dollars, a staggering sevenfold increase, while also announcing price hikes for its MCU product lines in 2021; Microchip’s price increases varied from 5%-10%, with some products seeing increases of over 10%.
As a result, industry professionals expressed that MCUs, which used to be cheap, have now become hot commodities, something they had never seen in over a decade of work.
The pain was felt almost instantly in China. Due to the difficulty of obtaining automotive IC certification, domestic manufacturers were essentially unable to achieve domestic substitution, and the rising costs of foreign original chips could only be passed down to domestic car manufacturers.
Industry insiders suddenly realized that even today, as the largest automotive and consumer electronics market, China remains fragile in the critical MCU sector, with the entire industry chain’s lifeblood tightly held in the hands of others.
The MCU industry chain is an extremely complex global ecosystem, involving numerous links such as IP licensing, chip design, manufacturing, packaging and testing, and distribution, with a high degree of global division of labor.
To summarize the position of domestic manufacturers in this chain in one sentence: they are basically out of touch with the upper and middle streams.
The upstream of the MCU industry chain includes chip design, materials and equipment, wafer foundry, and packaging and testing, characterized by technology intensity and oligopoly. For example, the EDA software essential for chip design is dominated by the U.S. and Germany, holding nearly 80% of the global market share.
IP licensing is almost entirely dominated by ARM in the UK, with over 50% of MCUs designed based on ARM core architecture.
Materials and equipment are similarly dominated, with photolithography equipment primarily monopolized by ASML (Netherlands), which controls over 80% of the global market, while Japan’s Canon and Nikon share the remaining market share. Etching, polishing, cleaning, and other equipment are mainly dominated by giants from the U.S. and Japan.
As for wafer foundries providing chip manufacturing, domestic manufacturers have been striving to catch up in recent years. Although there is still a significant gap compared to the leading company, two Chinese companies, SMIC and Hua Hong, have appeared in the CR6 of Q2 2023.
The packaging and testing factories are mainly responsible for packaging the finished wafers produced by foundries into final products and conducting reliability tests. This link has a lower threshold than wafer foundry and a higher localization rate, with major players concentrated in mainland China and Taiwan, apart from Amkor from the U.S.
The midstream consists of chip design original manufacturers, primarily controlled by chip giants from the U.S., Europe, and Japan. Chinese companies currently hold a small market share but are rapidly catching up.
MCU original manufacturers can be divided into IDM and Fabless models based on their business models. The former is mainly dominated by foreign large enterprises, while domestic companies mostly adopt the Fabless model, relying more on foundries for support.
According to Omdia data, the global MCU market CR6 reached 83.4% in 2022, mainly dominated by U.S., European, and Japanese chip giants.
In contrast, in 2021, 85% of the domestic MCU (including consumer-grade) market was held by foreign capital (94% in 2019), with a total domestic production rate of less than 15%, mostly concentrated in consumer-grade products; the domestic production rate of automotive-grade MCUs, as the largest downstream market, was less than 5%, indicating significant room for domestic substitution.
MCUs have a wide range of downstream applications, primarily covering six major markets: automotive electronics, industrial control, consumer electronics, computing and storage, and network communication, with automotive electronics accounting for the highest proportion globally.
According to IC Insights, the market share of automotive electronics reached 39% in 2021, showing a trend of annual increase, closely related to the demand and performance requirements of the new energy vehicle revolution, while the automotive “chip shortage” since 2020 has also pushed up the ASP of MCUs to some extent.
However, from the perspective of the domestic market, the downstream market for MCUs is mainly concentrated in the consumer electronics field. In 2020, the downstream application of MCUs in the domestic market accounted for 26% in consumer electronics, while automotive electronics only accounted for 16%.
The significant difference between the domestic and global downstream composition is understandable:
1) China is the world’s factory, with the assembly and manufacturing of PCs, mobile phones, IoT, home appliances, and other consumer electronics highly concentrated, thus the demand for MCUs related to domestic consumer electronics is relatively higher;
2) Approximately 95% of the automotive electronics MCU market share is dominated by U.S., European, and Japanese IDM chip giants, and the downstream vehicle brands are also predominantly led by developed countries, making it challenging for domestic automotive-grade MCUs to achieve self-sufficiency, and local MCU companies find it difficult to penetrate.
However, entering the era of new energy vehicles, the strong rise of domestic electric vehicle brands, combined with the opportunity window brought by the automotive electronics chip shortage from 2020-2022, has provided a significant entry opportunity for domestic MCU companies, and their market share is expected to increase.
It should be noted that although domestic automotive-grade MCUs have begun to enter the automotive supply chain, they are mostly concentrated in the mid to low-end application range, such as body control, seating, and lighting, with only Guoxin Technology, Xinchi Technology, and Xinwangwei producing products for mid to high-end applications.
The reasons for the slow breakthrough of the domestic automotive-grade MCU industry can be summarized in three points:
1) The technical processes for automotive-grade MCUs are stringent, with long R&D cycles and insufficient motivation for companies to invest in R&D
Compared to consumer and industrial-grade MCUs, automotive-grade chips operate in complex and variable environments, characterized by high vibration, dust, electromagnetic interference, and wide temperature ranges, with temperature resistance requirements typically ranging from -40 to 155°C, while also needing to withstand vibration shock, temperature cycling, waterproofing, UV resistance, and anti-interference capabilities.
Due to the long lifecycle of automobiles, the required product lifespan is 15-20 years, with supply cycles exceeding 15 years, thus imposing extremely stringent standards for product defect rates and reliability.
2) The certification standards for automotive-grade chips are strict and lengthy, with significant uncertainty and high investment risks;
The certification standards for automotive-grade chips are stringent, with a lengthy process and high barriers to entry. From wafer fabrication to mass production and shipment, it often takes 2 to 3 years. However, once successfully integrated into the vehicle supply chain, manufacturers can enjoy a supply cycle of at least 10 years, establishing deep ties with downstream automakers.
3) For a long time, the traditional fuel vehicle market has been dominated by European, American, and Japanese brands, thus the entire vehicle supply chain has been predominantly controlled by foreign capital, making it extremely difficult for new domestic suppliers to enter the original equipment market.
During the global chip shortage peak from 2020 to 2022, domestic MCUs have gradually begun to penetrate the downstream vehicle supply chain, accelerating the localization process of automotive MCUs.
Especially in the era of new energy, the strong rise of independent brands has provided more market entry opportunities for local MCU manufacturers.
In the new energy era, China’s long-term investment in the new energy sector has established a mature industry chain and talent pool under the advantage of being a first mover, significantly lowering the barriers to vehicle manufacturing, allowing traditional independent brands and new forces like NIO, Xpeng, and Li Auto to achieve a leapfrog over traditional fuel vehicle giants.
According to the China Passenger Car Association, the market share of independent brands in China’s passenger car market was 35.7% in 2020, rapidly rising to 47.3% in 2022; by July 2023, the market share of independent brands reached a record 53.2%, surpassing 50% for the first time. In contrast, Japanese brands dropped sharply from 24.1% in 2020 to 17.3%, with German, Korean, and American brands also showing significant declines.
The power revolution in new energy vehicles is reshaping the competitive landscape of the global automotive market, as the traditional fuel vehicle brands’ moat (engine and transmission) is gradually being replaced by the three electrics system. Domestic brands are gradually achieving a leapfrog advantage due to the mature domestic industry chain and software and hardware innovation advantages, which is expected to drive the development of the local automotive electronics supply chain.
Additionally, it is also important to note that we are not starting from scratch in the upstream of the foundry and testing industry chain, which primarily depends on the characteristics of automotive-grade MCU processes.
Currently, the global automotive-grade MCUs mainly use 40nm-90nm process nodes, with only a few luxury models partially adopting 28nm process MCUs. This is because automotive MCUs do not require the same high computing power and integration level as consumer-grade chips, thus advanced processes are not necessary; at the same time, the embedded storage within MCUs limits the process improvement of MCUs.
Therefore, looking at the production process nodes of mainstream automotive-grade MCUs, domestic chip foundries like SMIC and Hua Hong already have the capability for independent manufacturing.
Although the market share of domestic automotive-grade MCUs is less than 5%, there are a few that are performing well in the automotive MCU space, such as Jiefa Technology under NavInfo, which is the only domestic automotive semiconductor manufacturer with all product lines certified for automotive-grade applications.
In 2018, they developed China’s first automotive-grade certified 32-bit MCU chip, which has since been mass-produced in over 500 vehicle models worldwide, with automotive-grade MCU shipments exceeding 10 million units.
Another example is BYD Semiconductor, which is the largest automotive-grade MCU chip manufacturer in China. Since launching the first mass-produced 8-bit automotive-grade MCU chip in 2018, followed by the first generation of 32-bit automotive-grade MCU chips in 2019, which have been mass-loaded in BYD’s entire series of vehicles, BYD’s automotive-grade MCU chip shipments have exceeded 10 million units, and they are about to launch a more advanced 32-bit dual-core high-performance MCU chip, mainly used in domain controllers and other body control areas.
Unlike CPUs and GPUs, the characteristics of MCU chip products are that although the total demand is large, there are many categories, with a small demand and low profit margin for each category. Therefore, mainstream manufacturers like Renesas, Infineon, and Texas Instruments adopt the IDM model—designing and producing themselves to control costs as much as possible.
Thus, the top six players in the MCU market are all following the IDM model. Even during the chip shortage, these manufacturers do not expand production due to overflowing orders; instead, they outsource to foundries like TSMC.
Although mainland China is one of the largest markets for mature process chips like MCUs, domestic manufacturers entered the market relatively late, leading to a greater reliance on the manufacturing capabilities of foundries, which is the Fabless model mentioned earlier.
The Fabless model, which means no foundry model, differs from IDM in that the original manufacturer focuses solely on the R&D, design, and sales of MCUs, outsourcing the capital-intensive wafer manufacturing, packaging, and testing processes to specialized foundries and testing factories like TSMC and ASE.
However, the emergence of the chip shortage has begun to change the established pattern.
IDM model MCU manufacturers do not expand production even when orders overflow due to cost control, instead outsourcing to foundries, a strategy that seems reasonable under normal circumstances. However, during the chip shortage phase, foundries prioritize the production of higher profit chips.
A typical example is TSMC, which even announced a 60% increase in MCU chip production capacity in 2021, but according to its financial reports, the proportion of processes below 28nm has remained largely unchanged in recent years. From Q1 2021 to Q1 2023, the proportion of TSMC’s processes below 28nm was 63%, 64%, and 64%, respectively.
Domestic manufacturers originally had no opportunity under normal conditions, but the overflow of orders from original manufacturers to foundries was not enough; they continued to flow down to second-tier foundries like Hua Hong, combined with insufficient upstream capacity and surging downstream demand, allowing domestic MCU manufacturers to enter the supply chain amidst the chip anxiety of automotive companies.
In the market for mature process chips, unlike advanced processes that draw global attention, the breakthrough of technology is less important than solid mass production and yield. The mature process is also less affected by sanctions, testing the cooperation of the entire upstream and downstream industry chain.
The explosive demand for automotive electronics downstream could not be met by major manufacturers during the chip shortage phase, thus providing an opportunity for domestic MCU chips to replace them. A large number of orders fed back to the midstream allowed domestic chips to enter the supply chain, utilizing the special time and path to complete certification, which in turn reflected upstream, allowing foundries like SMIC and Hua Hong to receive more orders.
In the long run, with domestic foundries continuously optimizing and expanding capacity in mature process technology, coupled with the development of open-source instruction set architectures like RISC-V, domestic MCU manufacturers, through close collaboration with upstream foundries, are expected to jointly promote the cost-effectiveness of domestic MCUs, leveraging mid to low-end automotive-grade MCUs as an entry point, seizing the time window of the rapid rise of independent brands and new forces in vehicle manufacturing, gradually integrating into the vehicle supply chain system, and ultimately achieving gradual domestic substitution.
Reference Materials
[1] The price of a chip skyrocketed 7 times: The Truth Behind the Global Chip Shortage: 38 MCUs control the automotive industry chain, International Electronic Business Review
[2] A fire at Renesas’ Naka factory may affect the global automotive chip market, The Paper
[3] Automotive MCU Research: “Chip Shortage” Environment, Domestic Suppliers Seek Self-Replacement, Zosi Automotive Research
[4] Hua Hong Semiconductor’s IPO: An Alternative Breakthrough in China’s Chip Foundry, Yuanchuan Technology Review
[5] Semiconductor Industry In-Depth Report (IV): MCU: Automotive + Industrial Control + New Consumer IoT Three Major Driving Forces Promote, Broad Prospects for Domestic Substitution, Donghai Securities
[6] 2023 TOP 50 Domestic MCU Manufacturer Research Statistics and Industry Analysis Report
[7] An Interesting Data Point: TSMC’s Mature Chip Proportion hasn’t changed in three years, Just Talk Technology

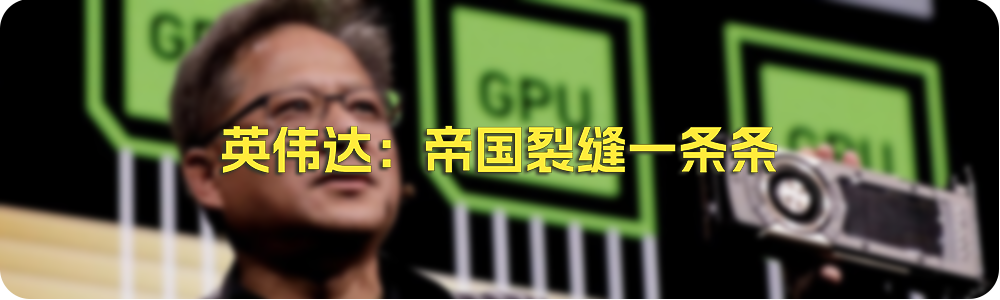
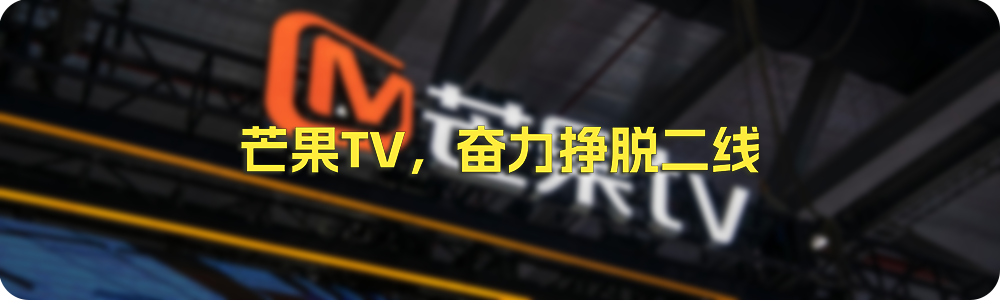
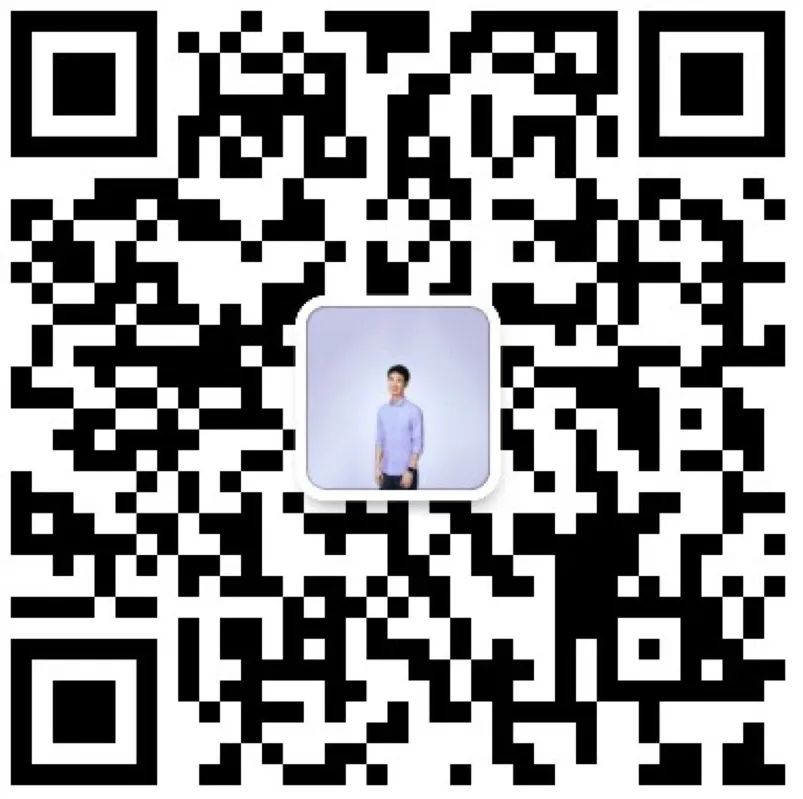
Welcome to cooperate and reprint
Please add WeChat with company and position noted
<span>Account articles visible on platforms such as Huxiu, 36kr, Titanium Media, Interface News, Everyone is a Product Manager, Entrepreneur, Chuangshiji, The Paper, Investment界, Donews, NetEase, Tencent News, and more</span>