Chips are hidden in the electronic devices that can be seen everywhere in the city, such as smartphones, computers, and home appliances, all of which rely on its control.
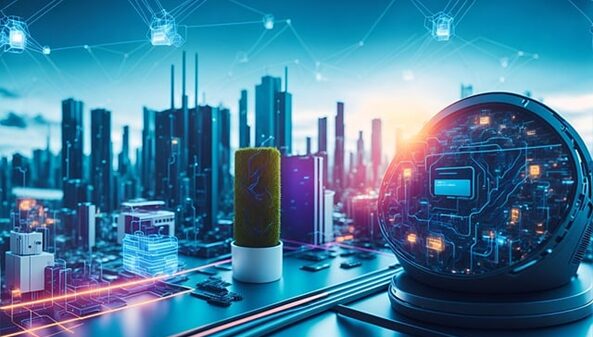
Image source: pixabay
The tiny chip integrates a large scale of circuits.
If we magnify the chip, we can see that there are densely arranged circuits inside, resembling a densely woven highway, as if a well-ordered circuit city has been built in an extremely small size.
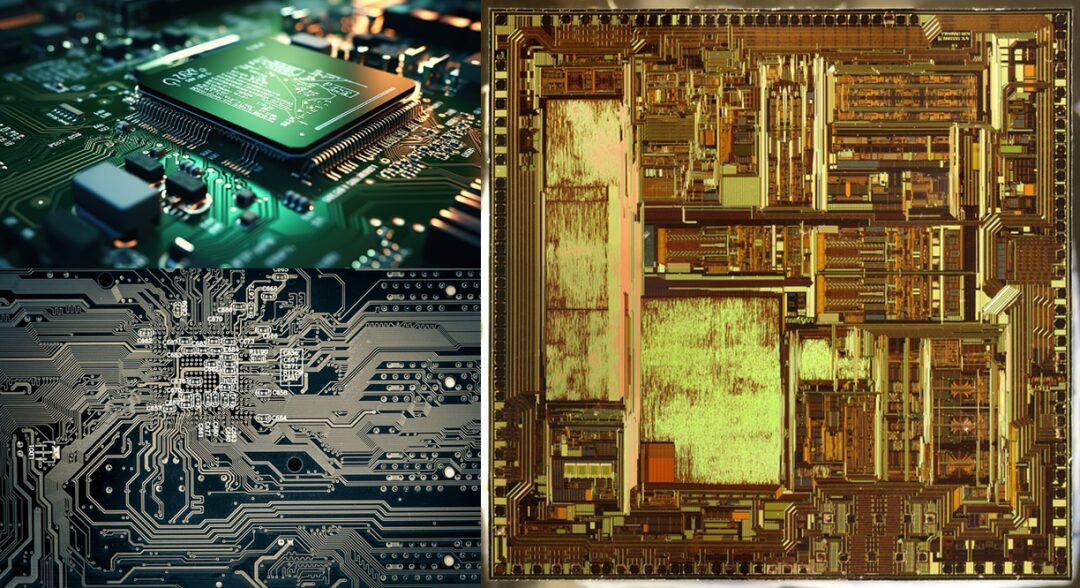
Chip structure diagram (naked eye and microscopic) | Image source: pixabay
How small is the chip inside? The smallest process we currently use in industry has reached 3nm, allowing the chip to integrate tens of billions of transistors.
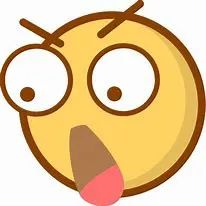
The “Multi-layer” Thinking of Chip Manufacturing
Countless nano-sized electronic components are arranged on the chip. Is each component pre-manufactured and then placed one by one?
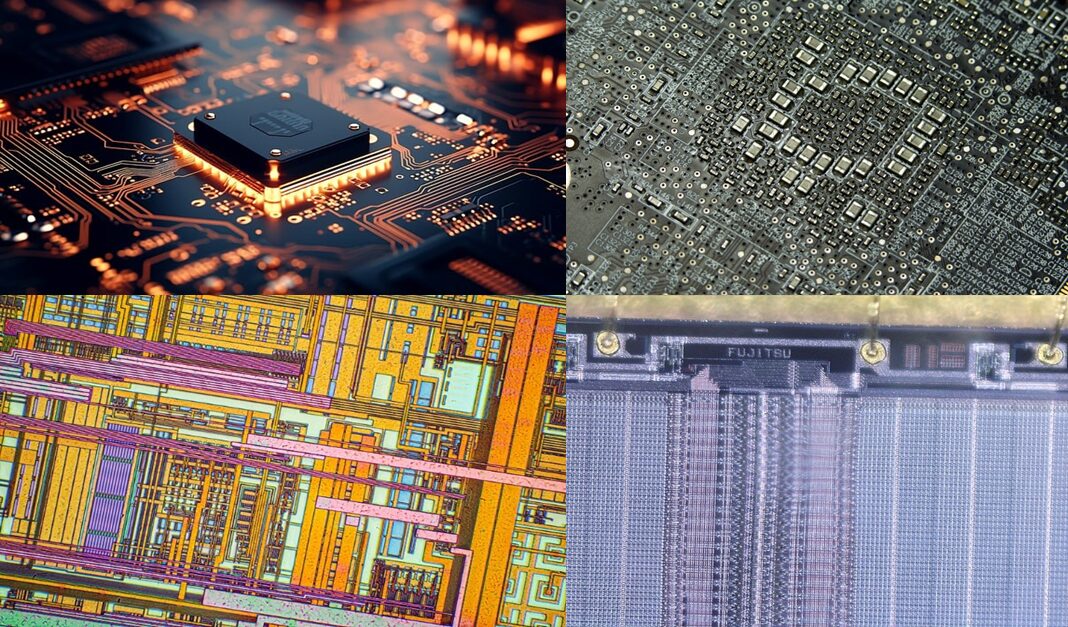
Image source: pixabay (above); Searchmedia – Wikimedia Commons (below)
No! We can look at this issue from a different angle. Upon careful observation from the vertical perspective, we can find that the chip is made up of layer upon layer of sheet structures with different patterns stacked vertically. If we pre-manufacture each layer and then stack them vertically, the two-dimensional structures can combine to form a three-dimensional device, ultimately resulting in a function-rich chip.
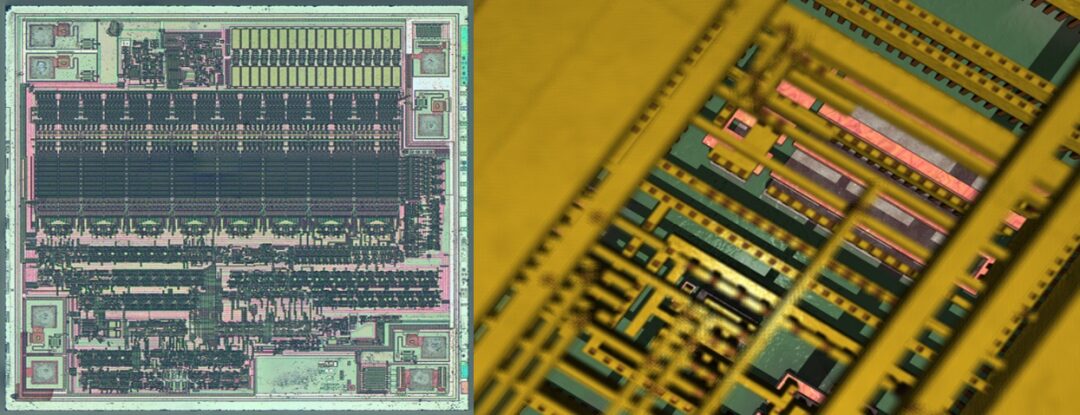
Vertical observation of the chip’s internal structure | Image source: Searchmedia – Wikimedia Commons
Now our goal is to figure out how to create sheet structures with specific patterns. First, we need a sheet material that can be used to print circuit diagrams, which is what we commonly refer to as silicon wafers. This is a type of silicon with extremely high purity, which is processed and then cut into smooth, extremely thin circular slices.
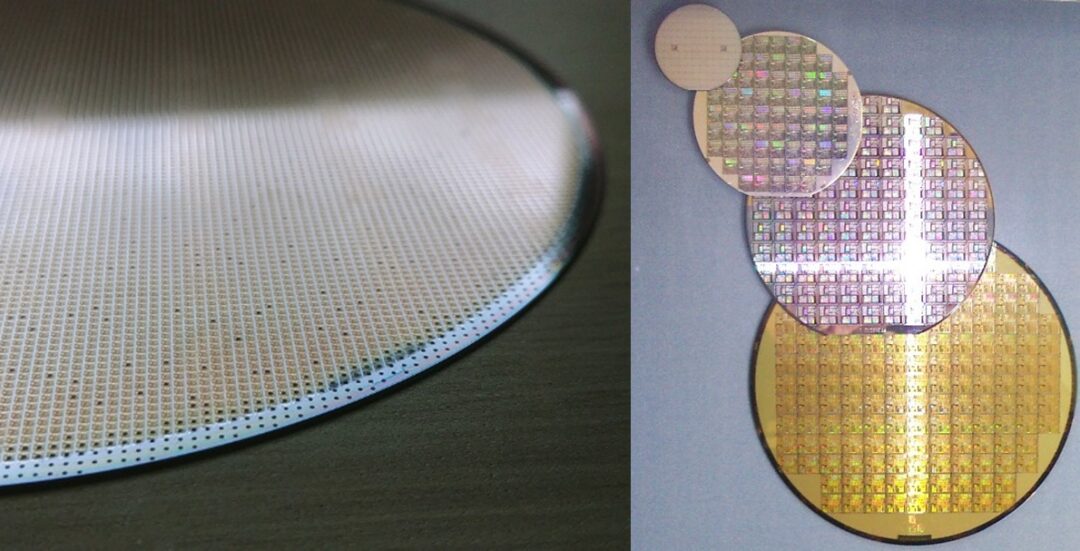
Silicon wafer | Image source: pixabay (left); Searchmedia – Wikimedia Commons (right)
Next, just like a carpenter, we need to find the right tools to carve patterns. To create a chip with a complex and extremely tiny internal structure, the requirements for processing tool dimensions are extremely high.
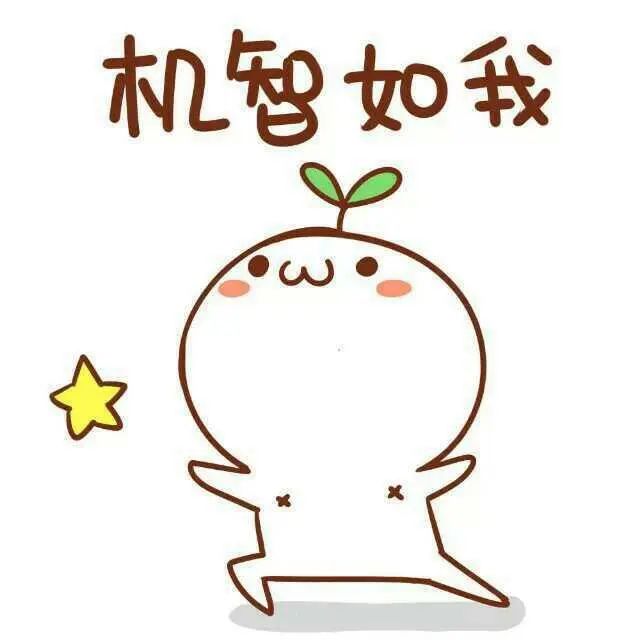
We smartly found light as our carving tool. Due to the rich wavelengths of light, we can use short wavelengths of light to achieve extremely fine processing.
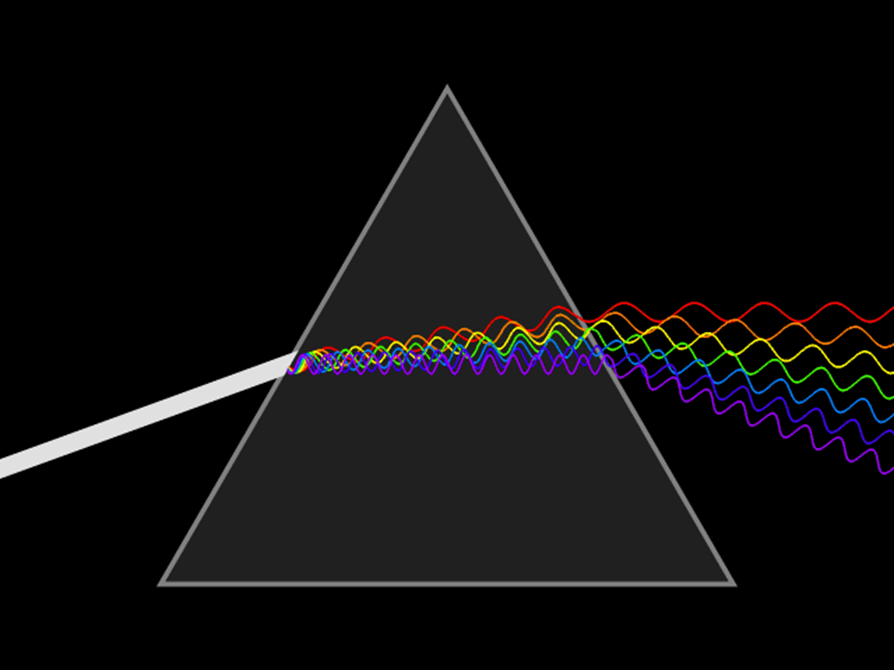
The rich wavelengths of visible light (invisible light has even richer wavelengths) | Image source: Searchmedia – Wikimedia Commons
We hope to transfer the circuit patterns designed on paper onto the silicon wafer using optical exposure, but light cannot affect silicon materials, so we need to use an intermediate material, which is a photoresist that can directly interact with light.
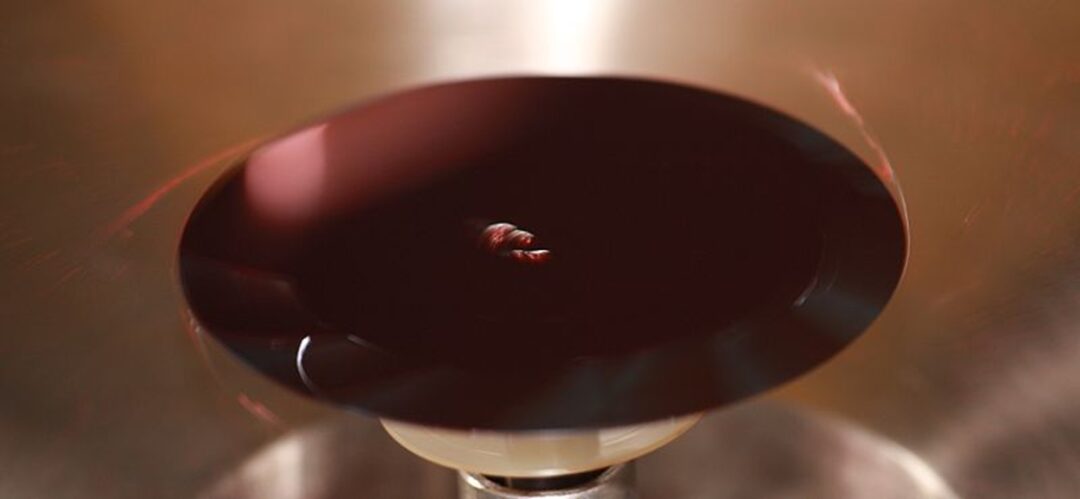
Photoresist spun onto the silicon wafer (evenly covered by centrifugal force) | Image source: Searchmedia – Wikimedia Commons
To allow light to achieve the transmission of pattern information, we can create a pattern of light and dark by completely blocking or completely allowing light to pass through. Light passes through the light-blocking plate with circuit patterns (mask) and can replicate the pattern information of the mask. Finally, after interacting with the photoresist evenly coated on the surface of the silicon wafer, the desired pattern information appears on the silicon wafer.
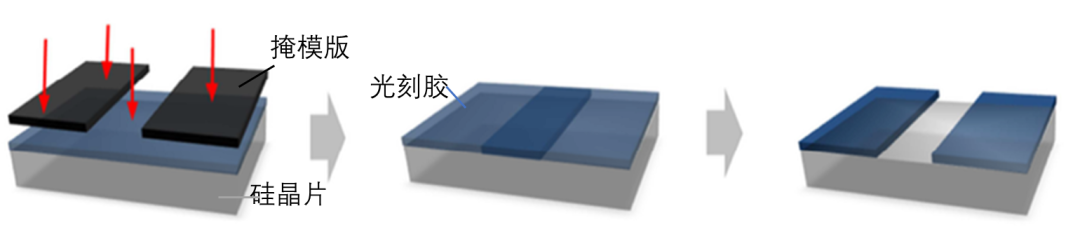
Photoresist imaging exposure process | Image source: Searchmedia – Wikimedia Commons
Photoresist is the main medium for photoresist imaging, which can be divided into positive and negative resists. The positive photoresist is more easily dissolved in the developer solution in the exposed area, while the negative photoresist is less likely to dissolve in the developer solution in the exposed area.
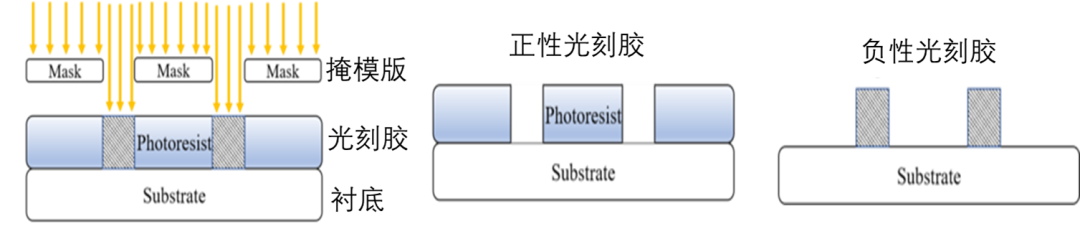
Two outcomes of the exposure process (positive and negative resists) | Image source: Searchmedia – Wikimedia Commons
Assuming we are using positive photoresist, after the exposure process is complete, the developer solution can dissolve the photoresist exposed to light. Then, we use chemical substances to dissolve the exposed silicon wafer, leaving the photoresist on the silicon wafer to protect it, which is the etching process.
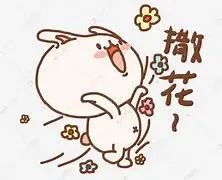
Now we have achieved our goal of obtaining a silicon wafer with a specific circuit pattern. Throughout this process, the general idea is quite smooth, but the precision engineering of chip manufacturing, representing the pinnacle of human intelligence, involves countless stringent requirements.
What Limits the Internal Size of Chips?
The main component of chips is transistors. A large chip can have tens of billions of transistors, and the smaller we can manufacture transistors, the more components the chip can accommodate, and the power consumption of the transistors will also be lower.
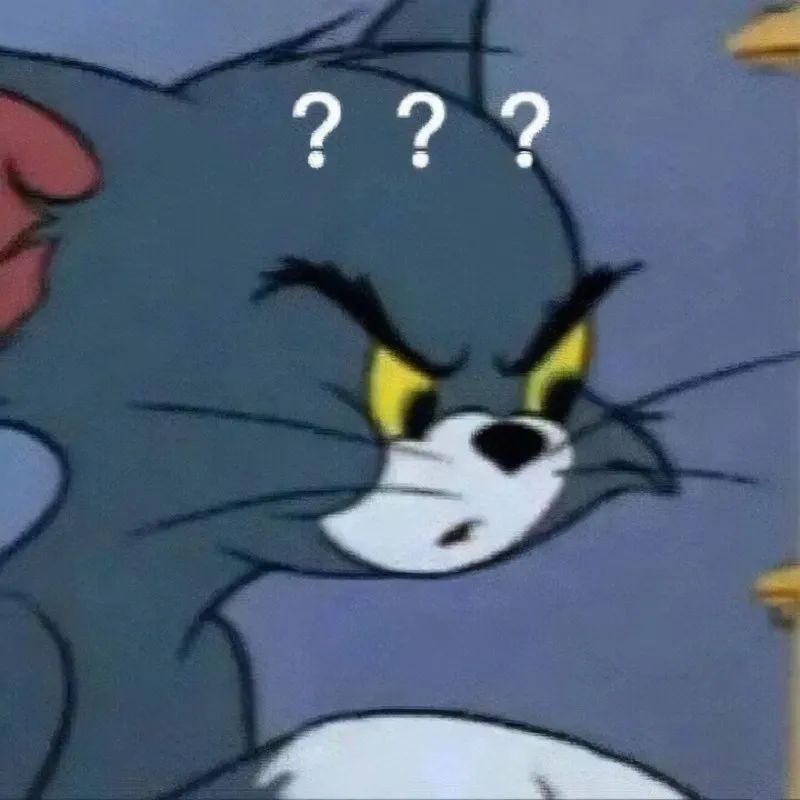
In chip manufacturing, we hope to use light to create circuit patterns on a small scale. So why can light achieve this effect? What are the limits of light’s sculpting capabilities?
Diffraction
The main reason affecting the level of light sculpting is the diffraction effect of light. Light is an electromagnetic wave, and diffraction is inevitable during the propagation of light in photolithography, which establishes the minimum feature size of the exposure range. The resolution of light, that is, the ability of the photoresist to reconstruct patterns based on light exposure is limited.
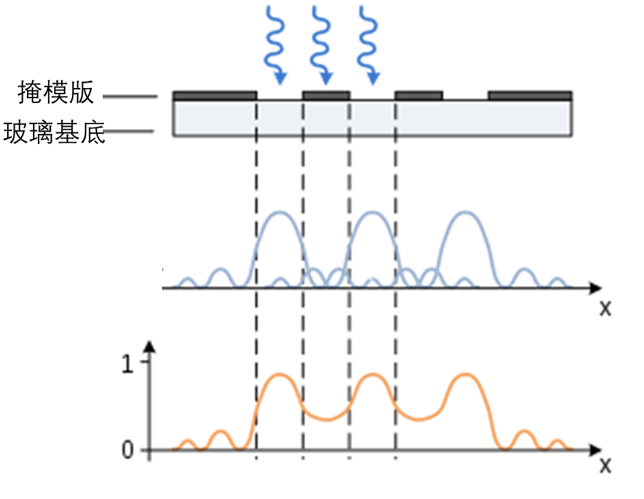
Diffraction during the exposure process | Image source: Searchmedia – Wikimedia Commons
As shown in the figure below, when a beam of parallel light passes through a narrow slit, light will interfere with countless sub-waves during propagation, forming light and dark diffraction patterns.
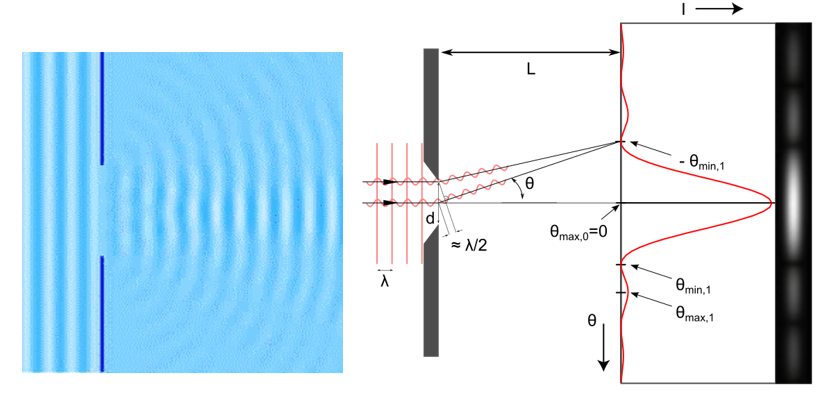
Single-slit diffraction | Image source: Searchmedia – Wikimedia Commons
This means that when considering light propagation at a small scale, there is no longer a clear distinction between the light and dark areas, but rather blurry zones appear. A point of light emitted from an ideal object will deviate from the geometric optical straight line after passing the edge of an obstacle, no longer forming an ideal image point.
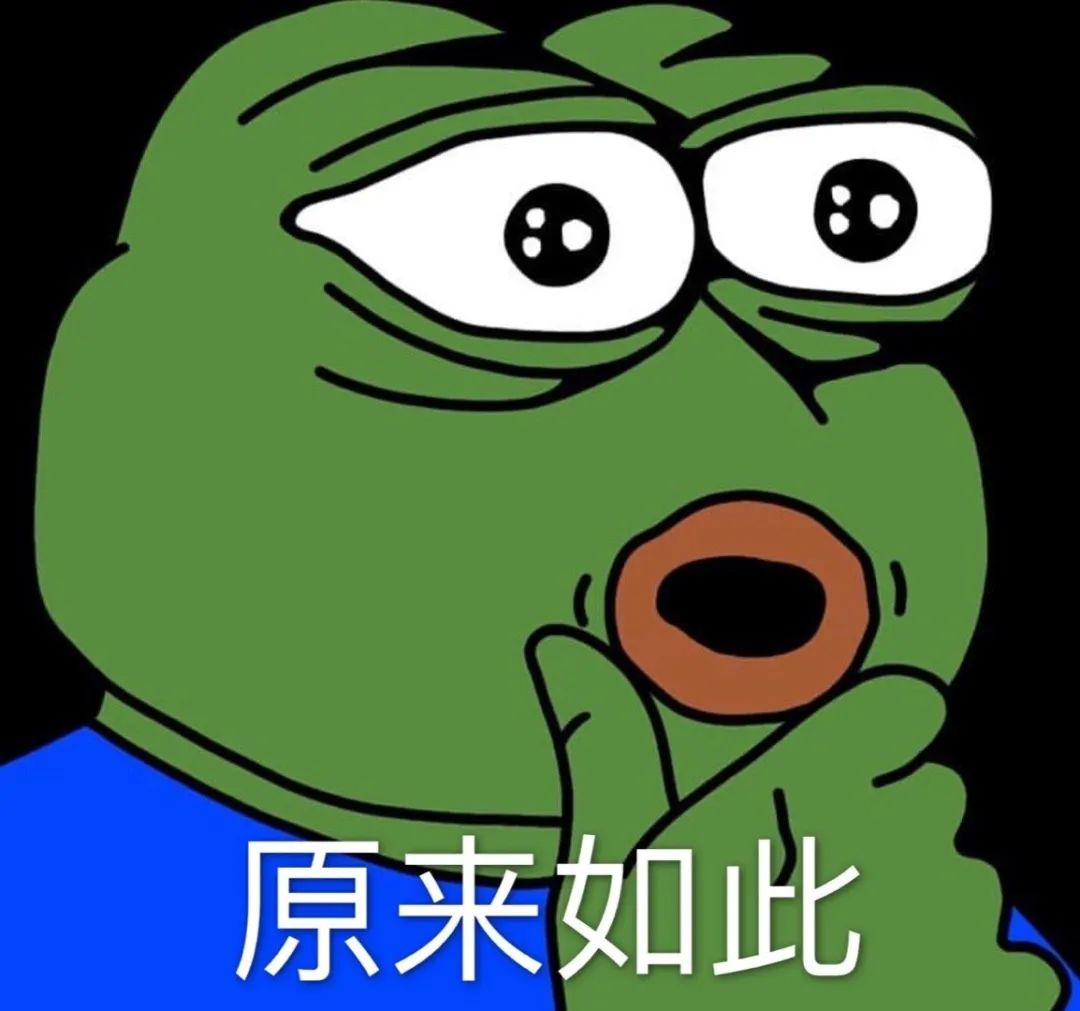
This is precisely because when the width of the slit is comparable to the wavelength of light, the wave effects of light come into play. Light can use wave effects to bypass obstacles, dispersing in space, resulting in the diffraction effect of light, leading to imprecise exposure area, and the resolution of light has limits.
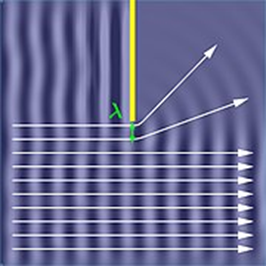
Light wave effect diagram (comparing straight line propagation and wave effect) | Image source: Searchmedia – Wikimedia Commons
Resolution
In the field of optical imaging, resolution is the ability to distinguish between two adjacent object points. Ideally, we hope each object point can produce sharp image points, but due to diffraction, the actual result is light spots of a certain size. If the overlap of two light spots (diffraction patterns) is too great, the image points become difficult to distinguish.
Rayleigh proposed an effective criterion, and the resolution calculation formula is:
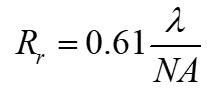
This resolution expression describes the limit position at which two light spots can just be distinguished—when the peak position of one light spot coincides with the first zero point of the other light spot. Here, λ is the wavelength of the illuminating light.
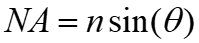
The limit cases of indistinguishable and just distinguishable light spots | Image source: Searchmedia – Wikimedia Commons
NA is the numerical aperture, which describes the ability of the lens to converge light, specifically expressed as the degree of deflection of parallel light after incidence (converging to a focus), calculated as:
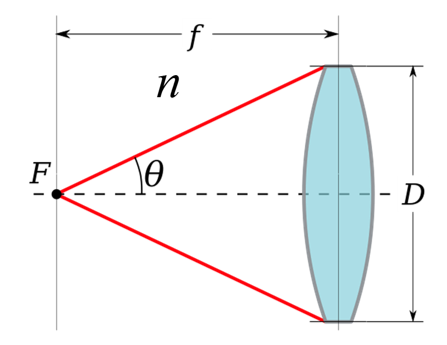
Numerical aperture (n is the refractive index) | Image source: Searchmedia – Wikimedia Commons
Rayleigh’s criterion is commonly used to evaluate imaging quality, while the photolithography system images in the photoresist. Photoresist is a high-contrast imaging medium, and under certain exposure conditions, although the optical resolution has reached below the limit of Rayleigh’s criterion, the photoresist can still present good imaging results, achieving processing goals.
The resolution of photolithography imaging is:
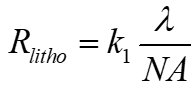
Rlitho is the pattern period that the photolithography system can resolve; k1 is the process factor.
Photolithography
Photolithography is the most complex, expensive, and critical process in chip manufacturing, typically using projection photolithography systems to project the circuit structure diagram of the mask onto the surface of the silicon wafer.
Optical lenses can converge diffracted light to improve imaging quality. In photolithography technology, to achieve the smallest possible pattern, a projection imaging objective with a reduction ratio is used between the mask and photoresist.
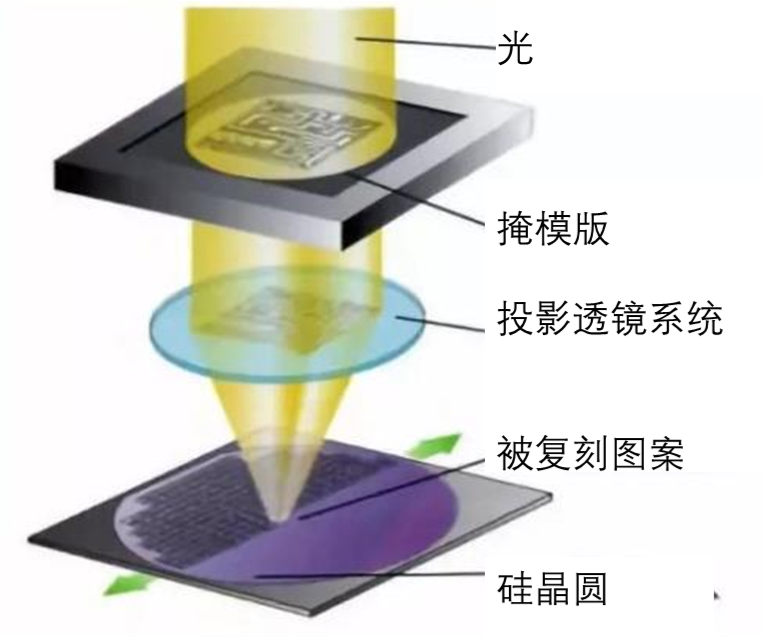
Projection photolithography system | Image source: network
How to Polish this Carving Tool of Light?
Now we know: the minimum processing scale of light (resolution) determines how small chips can be. How can we make chips smaller? We need to enhance the resolution and refine the functions of the circuit city on the chip.
Based on the three factors in the photolithography resolution formula, we have three solutions to polish this carving tool of light.
Increase the Numerical Aperture of the Photolithography System
The larger the numerical aperture of the projection objective in the photolithography imaging system, the better the resolution. The specific operation is to design immersion photolithography machines, which means filling a high refractive index medium between the last lens of the wafer and the projection objective.
Shorten the Wavelength
The wavelength of light used in the photolithography process has undergone a development history from G-line (432nm), I-line (365nm), KrF (248nm), to ArF (193nm) in the deep ultraviolet range. Currently, extreme ultraviolet lithography (EUV) with a wavelength of 13.5nm has been put into use.
Reduce the Process Factor
By optimizing photolithography process parameters, we can also improve photolithography resolution, such as improving illumination conditions, photoresist processes, and mask design. These methods can reduce the process factor k1, known as resolution enhancement technology (RET).
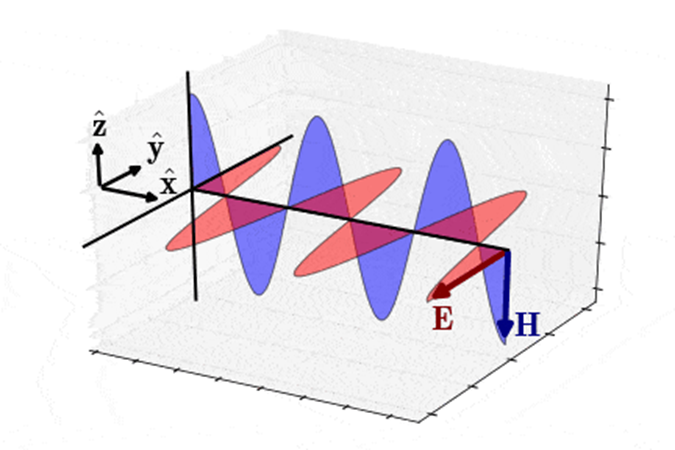
Electromagnetic waves | Image source: network
Light is electromagnetic waves, thus containing information such as amplitude, phase, polarization state, and propagation direction. Photolithography resolution enhancement technology is achieved by controlling these four types of information about light to obtain finer graphic structures on the photoresist. For example, off-axis illumination technology can change amplitude and phase, optical proximity effect correction technology can change the amplitude of the light wave, and source-mask optimization can change the propagation direction, amplitude, and phase of the light wave.
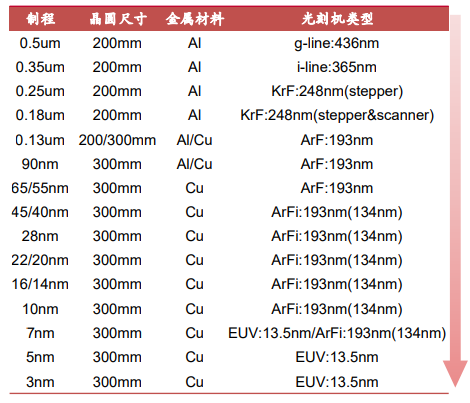
Table of relationships between various process nodes and photolithography technology | Source: Sako Microelectronics website, ASML, Zhongtai Securities Research Institute
Looking at the development history of photolithography machines, we are indeed running along the path of continuously shortening wavelengths. Observing the data in the table, even when the wavelength of the light source is the same, we are still continuously reducing the process, which is attributed to the numerical aperture, process factor, and other complex technologies.
References
[1] Wei Ya Yi. Calculating Lithography and Layout Optimization [M]. 1. Electronic Industry Press, 2021.
[2] Stephen A. Campbell. Micro and Nano Scale Manufacturing Engineering [M]. 3. Electronic Industry Press, 2010.
Editor: Xiao Xian
↓ Click the title to view ↓