In today’s digital age, the Internet of Things (IoT) is a profoundly influential technology that is penetrating various fields at an unprecedented speed, especially in manufacturing. Simply put, IoT connects objects to the internet through various sensors to achieve intelligent recognition, positioning, tracking, monitoring, and management. From remote control of smart appliances to the efficient operation of intelligent transportation systems and precise monitoring in the healthcare sector, the applications of IoT are ubiquitous, profoundly changing our ways of living and working.
For the manufacturing industry, IoT represents a significant transformation. It injects new vitality into traditional manufacturing, becoming a key force driving the digital transformation of the industry. In the context of increasingly fierce global competition, manufacturing enterprises face numerous challenges such as improving production efficiency, reducing costs, enhancing product quality, and optimizing supply chain management. The emergence of IoT technology provides innovative solutions to these problems, helping companies accelerate their digital transformation and reshape the future landscape of manufacturing.
Multi-Dimensional Applications of IoT in Manufacturing
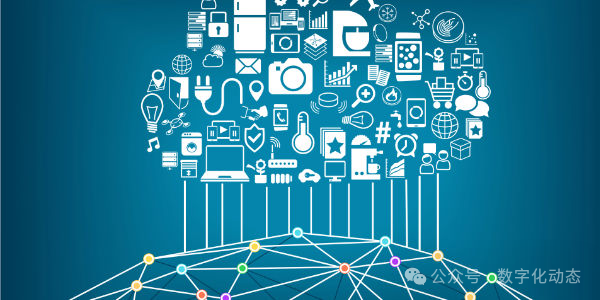
Intelligent Management and Maintenance of Equipment
The application of IoT technology in the intelligent management and maintenance of equipment is particularly prominent. By deploying various sensors, RFID, and other IoT devices on production equipment, it is possible to collect real-time data on key parameters such as operating status, temperature, humidity, and pressure, and transmit this data to a central control system or cloud platform. For example, in the engine production line of an automotive manufacturing company, high-precision temperature sensors and vibration sensors can be installed to monitor the operating status of engine processing equipment 24/7. Once an abnormal temperature rise or excessive vibration is detected, the system immediately issues a warning, notifying maintenance personnel to conduct timely checks and repairs. Additionally, utilizing big data analysis technology to delve into historical data allows enterprises to predict maintenance needs, develop maintenance plans in advance, and avoid production interruptions and losses caused by equipment failures. According to relevant data, using IoT technology for predictive maintenance can reduce equipment downtime by 30% – 50%, significantly enhancing production efficiency and equipment utilization.
Refined Optimization of Production Processes
IoT technology also plays a critical role in the refined optimization of production processes. By deploying numerous IoT devices on the production site, companies can collect various data in real-time, including production progress, material usage, and energy consumption. This data provides enterprises with comprehensive and accurate decision-making support, helping to achieve refined production and management. For instance, in electronics manufacturing, by installing smart sensors and data collection devices on the production line, companies can monitor the progress and material consumption of each production stage in real-time. When a process experiences delays or material shortages, the system automatically issues an alert and promptly adjusts production plans and material delivery to ensure smooth production processes. Furthermore, by analyzing production data, companies can identify bottlenecks and potential issues in the production process, allowing for targeted optimization and improvement, thereby enhancing product quality and production efficiency. For example, a smartphone manufacturer improved its product qualification rate by 10% and shortened its production cycle by 15% after optimizing its production process using IoT technology.
Visual Management of Supply Chain and Logistics
In the supply chain and logistics domain, IoT also demonstrates powerful advantages. By attaching RFID or NFC tags to products, companies can achieve visual management across various stages of the supply chain. In warehousing, with the help of IoT technology, staff can clearly know the exact location, quantity, and entry time of each product in the warehouse, achieving precise inventory control. During logistics transportation, utilizing GPS and sensor technology, companies can track the location and transportation status (such as temperature, humidity, vibration, etc.) of goods in real-time, ensuring the safety and quality of goods during transit. For example, in cold chain logistics, temperature sensors can monitor the temperature inside transport vehicles in real-time, and if the temperature exceeds the set range, the system immediately notifies relevant personnel to take corrective measures to ensure the quality of refrigerated goods. Additionally, IoT technology can enable intelligent sorting during the goods sorting phase, improving sorting efficiency and accuracy. Statistics show that logistics companies using IoT technology can increase sorting efficiency by 2-3 times and improve inventory turnover rates by 20%-30%, significantly enhancing the transparency and overall efficiency of the supply chain.
Intelligent Upgrading of Energy Management
Energy management is a crucial aspect for manufacturing enterprises to reduce costs and achieve sustainable development, and IoT plays an indispensable role in this. By installing smart meters for electricity, water, and gas in production equipment and energy supply systems, companies can monitor energy usage data in real-time and gain precise insights into energy consumption. For instance, in steel production enterprises, real-time monitoring and analysis of energy consumption in large equipment such as blast furnaces and rolling mills can help identify points of energy waste and implement corresponding optimization measures, such as adjusting equipment operating parameters and optimizing production processes, to achieve rational allocation and efficient utilization of energy. Practical cases indicate that a chemical enterprise that introduced an IoT energy management system reduced its energy consumption by 15%-20%, effectively lowering operational costs while also making a positive contribution to energy conservation and emissions reduction.
Analysis of Successful Cases of Digital Upgrading in Manufacturing
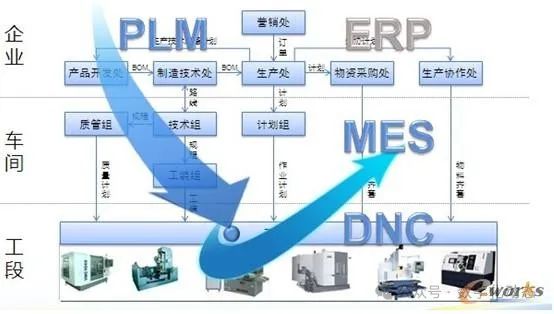
SANY Heavy Industry: A Model for Intelligent Transformation of Lighthouse Factories
SANY Heavy Industry, as a leading enterprise in the digital transformation of manufacturing, has achieved exemplary results in the application of IoT technology. SANY Heavy Industry has built a comprehensive marketing platform and customer relationship management system (CRM) to integrate customer information and achieve precise marketing, using big data analysis technology to offer personalized custom services, significantly enhancing the customer purchasing experience. In the production manufacturing phase, SANY Heavy Industry has vigorously promoted the application of automation technology, introducing automated assembly lines, flow line operations, and precision machining, effectively reducing manual intervention, improving production efficiency, and ensuring product reliability and accuracy. For instance, SANY tower cranes employ fully automated production processes, combined with an IoT big data platform, achieving efficient production with a standard product rolling off the line every 11 minutes, greatly enhancing production efficiency. Additionally, SANY Heavy Industry has established an intelligent flexible supply chain, leveraging a factory control center (FCC) to accurately schedule production lines, equipment, and workers, enabling rapid decomposition and delivery of orders. Furthermore, through an intelligent production management system, the company can collect and monitor production data in real-time, gaining full control over the production process, enhancing transparency and controllability, and effectively improving product quality and overall operational efficiency. Notably, during its internal transformation and upgrading process, SANY Heavy Industry successfully incubated an industrial internet company—Root Interconnection, which focuses on creating an industrial internet operating system to provide low-cost, low-threshold, high-efficiency, and high-reliability digital transformation services for industrial enterprises, further promoting the digital development of the industry.
Hikvision: Intelligent IoT Empowers Comprehensive Upgrading of Enterprises
Hikvision, with its deep technical accumulation in video surveillance and artificial intelligence, provides comprehensive intelligent IoT solutions for many enterprises, helping them achieve digital upgrades. In equipment management, Hikvision deploys various IoT sensors on production equipment to achieve real-time monitoring and precise diagnostics of equipment operating status. For instance, in Zijin Mining’s mining and selection processes, Hikvision’s intelligent IoT technology helps create augmented reality (AR) maps, enabling centralized control centers to manage various production units through a secure “one map,” gaining real-time insights into vehicle entry and exit, safety operation management, tailings pond sensor collection, and other safety production data, achieving coordinated collaboration and intelligent control, effectively ensuring the safe operation of frontline production. In the Tibet Julong Copper Mine, Hikvision’s dual-spectrum heavy-duty cloud platform, laser heavy-duty cloud platform, and black light camera allow managers to monitor on-site selection conditions in real-time from the control center. At the same time, the intelligent weighing system utilizes license plate recognition and measurement detection to achieve a fully unattended weighing process, and the vehicle speed monitoring system effectively curbs speeding and other violations, reducing the risk of vehicle safety accidents. In the field of production operations, Hikvision’s intelligent IoT solutions cover the entire process from raw material procurement, production processing to finished product sales. In Sun Paper’s paper making, pulping, chemical, and power generation plants, Hikvision has deployed a series of information and intelligent solutions that optimize production processes and resource allocation through real-time data collection and analysis, improving production efficiency and product quality. Furthermore, Hikvision plays a crucial role in safety monitoring, with its video AI detection technology covering various scenarios from train number recognition during cargo transportation to temperature detection warnings in production workshops, equipment inspections, and safety prevention during crane operations, significantly enhancing the quality and efficiency of safety monitoring, helping enterprises reduce safety production risks and ensuring stable production.
Core Advantages of IoT in Driving Upgrades in Manufacturing
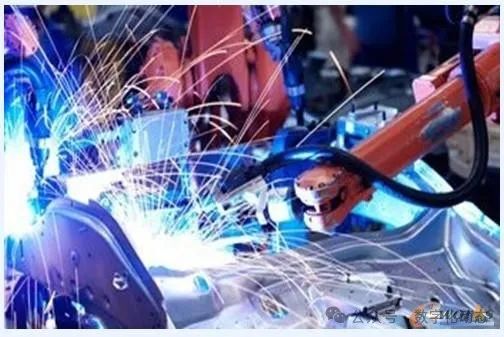
Enhancing Production Efficiency and Quality
IoT technology has significant advantages in enhancing production efficiency and quality. In production processes, real-time monitoring of equipment operating status, production progress, and material usage through sensors can help detect and resolve issues promptly, minimizing downtime. For example, intelligent sensors in automated production lines can accurately sense equipment working conditions, and once an anomaly occurs, they can automatically adjust or notify maintenance personnel to repair, avoiding prolonged downtime caused by equipment failures. Moreover, real-time analysis of production data helps optimize production plans and process parameters, improving precision and consistency, thereby enhancing product quality. For instance, automotive manufacturers utilize IoT technology to monitor and optimize welding, painting, and other process stages, effectively reducing the defect rate and improving overall production efficiency.
Reducing Operational Costs and Risks
IoT plays an important role in reducing operational costs and risks in the manufacturing sector. In energy management, smart meters for electricity, water, and gas can monitor energy consumption in real-time, helping companies accurately grasp energy usage conditions, identify energy waste points, and implement corresponding optimization measures, such as adjusting equipment operating parameters and optimizing production processes, to achieve rational allocation and efficient utilization of energy, thereby reducing energy costs. In equipment maintenance, IoT-based predictive maintenance systems analyze equipment operating data to predict potential failures in advance and develop maintenance plans, avoiding high repair costs and production losses caused by unexpected failures. Additionally, in supply chain management, IoT technology achieves visibility across various stages of the supply chain, effectively reducing inventory and logistics costs and improving overall supply chain efficiency. For instance, companies can accurately control inventory levels by monitoring inventory status and logistics conditions in real-time, avoiding inventory buildup or stockouts, thus reducing capital occupation and losses during logistics transportation.
Enhancing Innovation and Competitiveness of Enterprises
IoT brings rich innovation opportunities to manufacturing enterprises, helping to enhance their core competitiveness. With IoT technology, enterprises can develop smart products and services, providing customers with more personalized and intelligent experiences. For example, smart home products achieve interconnectivity between devices through IoT, allowing users to control home appliances and lighting remotely via their smartphones, greatly enhancing convenience and comfort in life. In terms of business model innovation, IoT also opens new paths for enterprises. Some companies have transformed product sales into service provision through a product-as-a-service (PaaS) model, increasing customer stickiness and revenue sources. For instance, elevator manufacturers have utilized IoT technology to achieve remote monitoring and maintenance of elevators, offering on-demand maintenance services that not only enhance the safety and reliability of elevators but also create new profit growth points for enterprises. These innovative initiatives allow companies to stand out in the market, enhancing their status and influence within the industry.
Future Prospects and Challenges of IoT Applications in Manufacturing

Looking ahead, the application prospects of IoT in the manufacturing sector are extremely broad. With the continuous development and integration of emerging technologies such as 5G, artificial intelligence, big data, and cloud computing, IoT will demonstrate even more powerful capabilities. For example, the high speed, low latency, and large capacity characteristics of 5G technology will make communication between IoT devices more efficient and real-time, further enhancing the automation and intelligence of production processes; artificial intelligence technology will assist IoT in achieving more precise data analysis and predictions, providing smarter decision-making support for enterprises; big data and cloud computing technologies will better process and store the massive data generated by IoT, uncovering more valuable information to drive innovation and business expansion for enterprises. In smart factories, IoT will enable deep interconnectivity and collaborative operations among production equipment, robots, sensors, etc., creating highly flexible and efficient production models that can quickly respond to changes in market demand and achieve personalized custom production. At the same time, the application of IoT in supply chain management will become more in-depth, achieving full traceability and transparency through integration with technologies like blockchain, enhancing the security and reliability of the supply chain. Furthermore, IoT will also promote cross-industry integration of manufacturing with energy, transportation, healthcare, and other fields, creating more new application scenarios and business models, such as industrial internet platforms, smart connected vehicles, and remote medical devices, bringing new opportunities and momentum for the transformation and upgrading of manufacturing.
However, the application of IoT in manufacturing also faces numerous challenges. Among them, security and privacy issues are the most prominent concerns. With the massive access of IoT devices, the attack surface increases, and the risk of data breaches rises. Manufacturing enterprises’ production data, process parameters, etc., often involve core business secrets, and if stolen or tampered with by hackers, it may lead to production interruptions, product quality issues, or even damage to the company’s reputation. Therefore, strengthening the construction of IoT security protection systems, including device security, network security, data encryption, identity authentication, and access control, is crucial for ensuring the stable operation of IoT applications in manufacturing. The unification of technical standards and compatibility is also an urgent problem to be solved. Currently, there are numerous devices and platforms from different manufacturers in the IoT market, and the lack of unified standards for communication protocols and data formats makes interconnectivity difficult, increasing the cost and complexity of integrating and applying IoT technology for enterprises. To promote the widespread application of IoT in manufacturing, industry organizations, standardization agencies, and enterprises need to work together to accelerate the development and promotion of unified IoT technology standards, improving the compatibility and interoperability of devices. Additionally, talent cultivation is also an important challenge faced by manufacturing. The application of IoT technology requires professionals who understand both manufacturing and information technology, and currently, there is a relative shortage of such talent. Enterprises need to strengthen training for employees, enhance cooperation with universities and research institutions, and establish a comprehensive talent cultivation system to train and attract a batch of professionals capable of applying IoT technology, providing talent support for the digital transformation of enterprises.
In summary, as a core force driving the digital upgrade of manufacturing, IoT has demonstrated enormous advantages and potential in equipment management, production process optimization, supply chain collaboration, and energy management, bringing significant economic and social benefits to the manufacturing industry. The practical experiences of successful cases such as SANY Heavy Industry and Hikvision indicate that actively applying IoT technology can help enterprises enhance production efficiency, reduce costs, strengthen innovation capabilities, and market competitiveness, achieving sustainable development. However, to fully leverage the role of IoT in manufacturing, a series of challenges such as security and privacy, standardization of technology, and talent cultivation must be addressed. In the future, with continuous technological advancement and innovation, IoT will deeply integrate with manufacturing, opening up broader prospects for the transformation and upgrading of the manufacturing industry, helping manufacturing enterprises stand out in the global digital economy wave and move towards a new stage of intelligent, efficient, and green development.
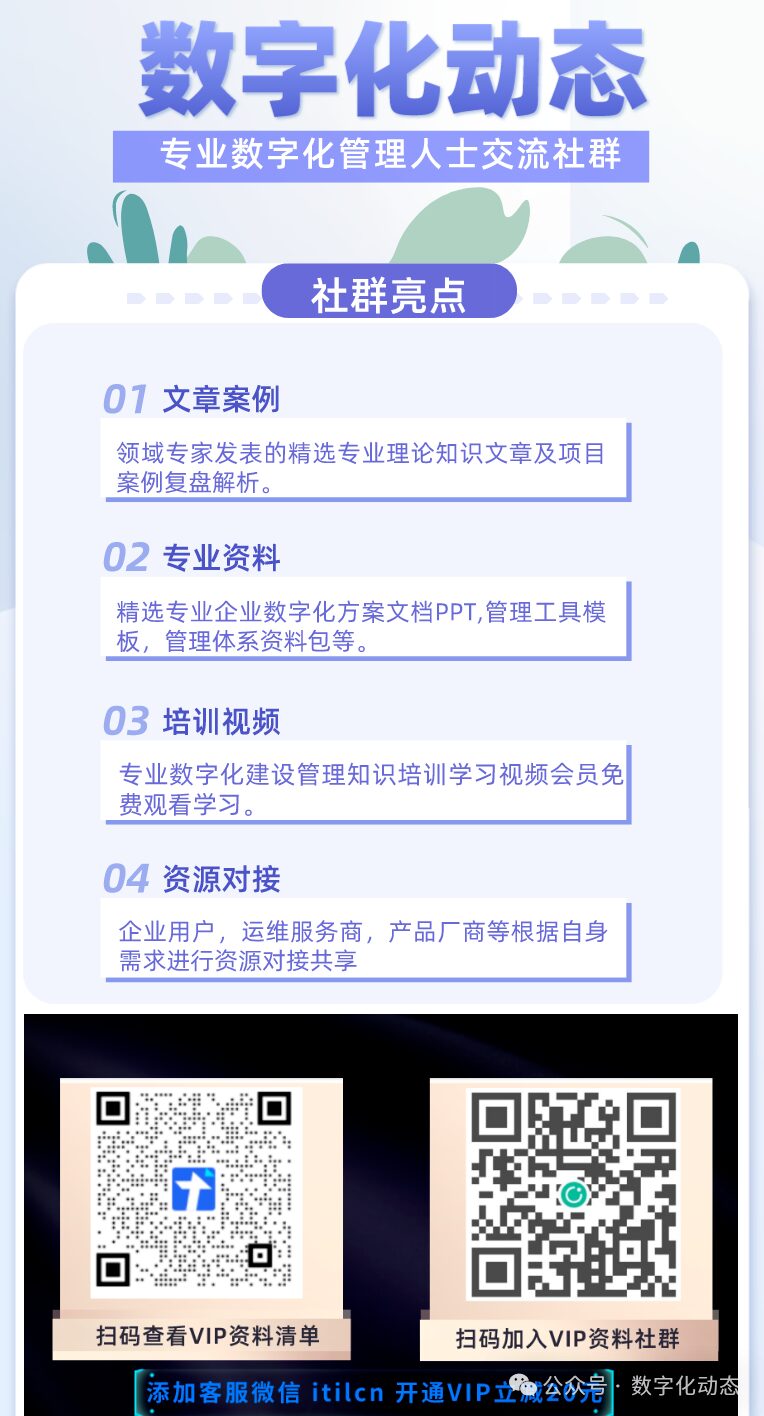