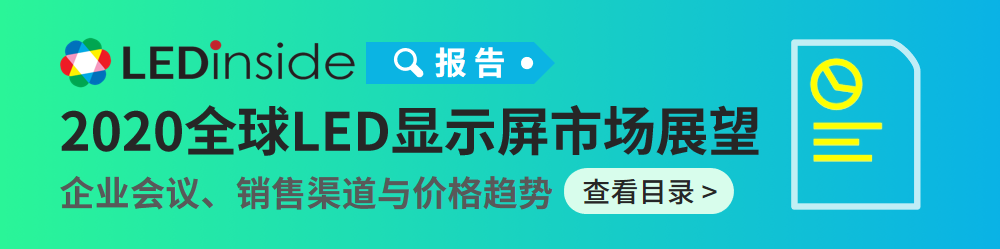
Types of Liquid Crystals
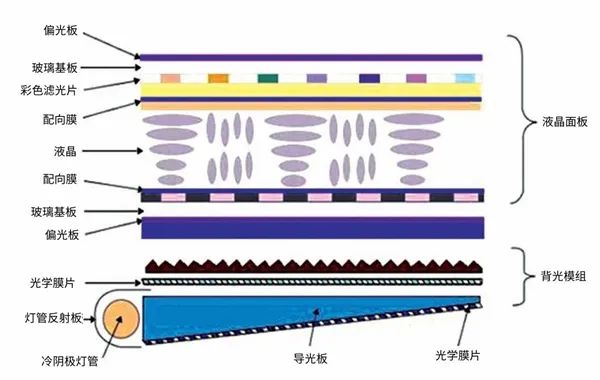
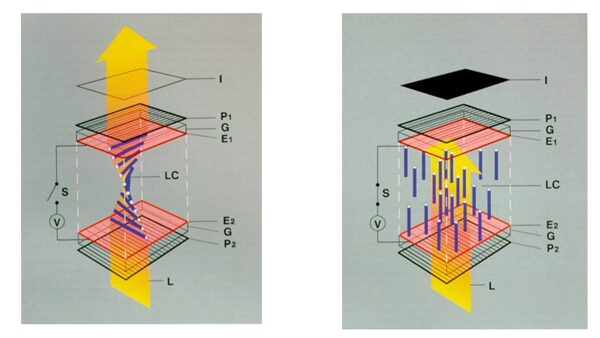
Success Lies in Open Cell
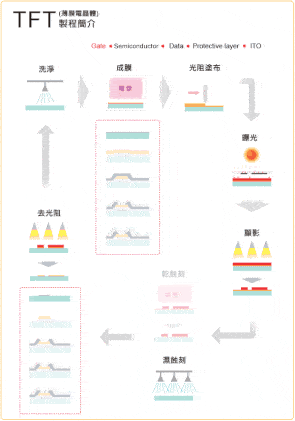
Differences Between OLED and LCD
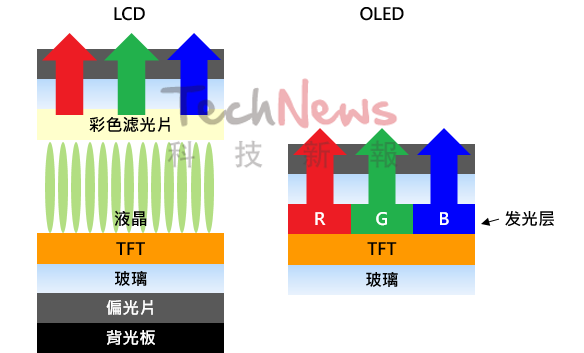
Semiconductors and the Panel Industry
Challenges of Inkjet Printing
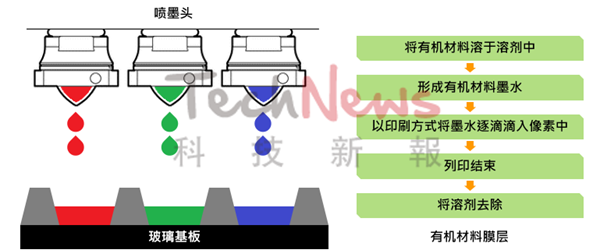
Positive Development, Difficult Mass Production
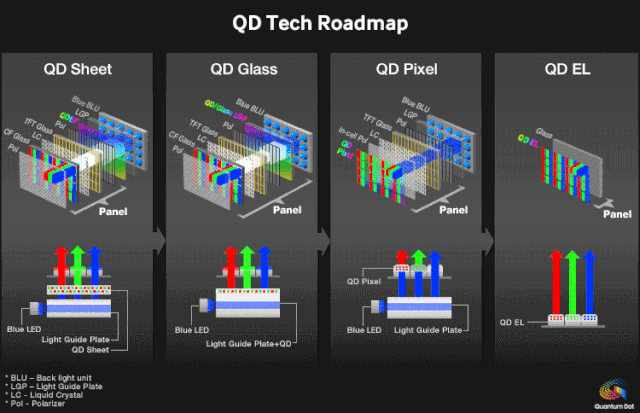
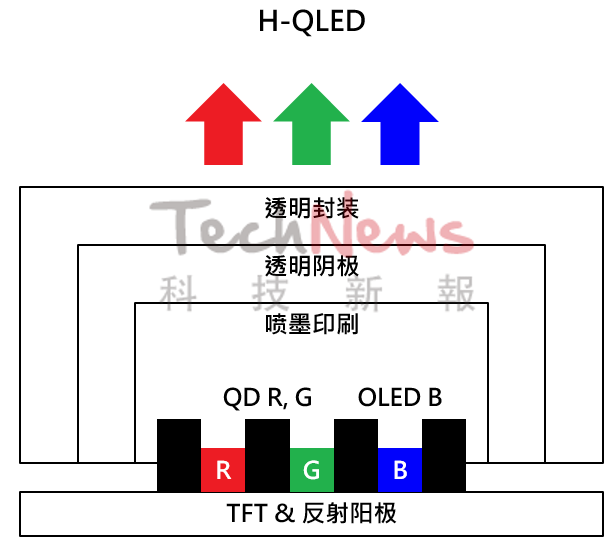
The Ambiguity of Mini LED and Micro LED
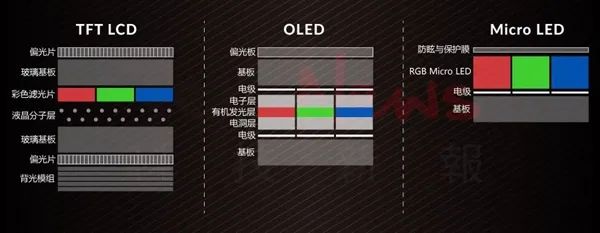
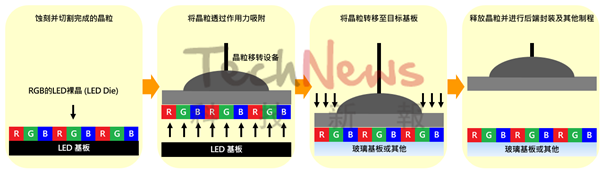

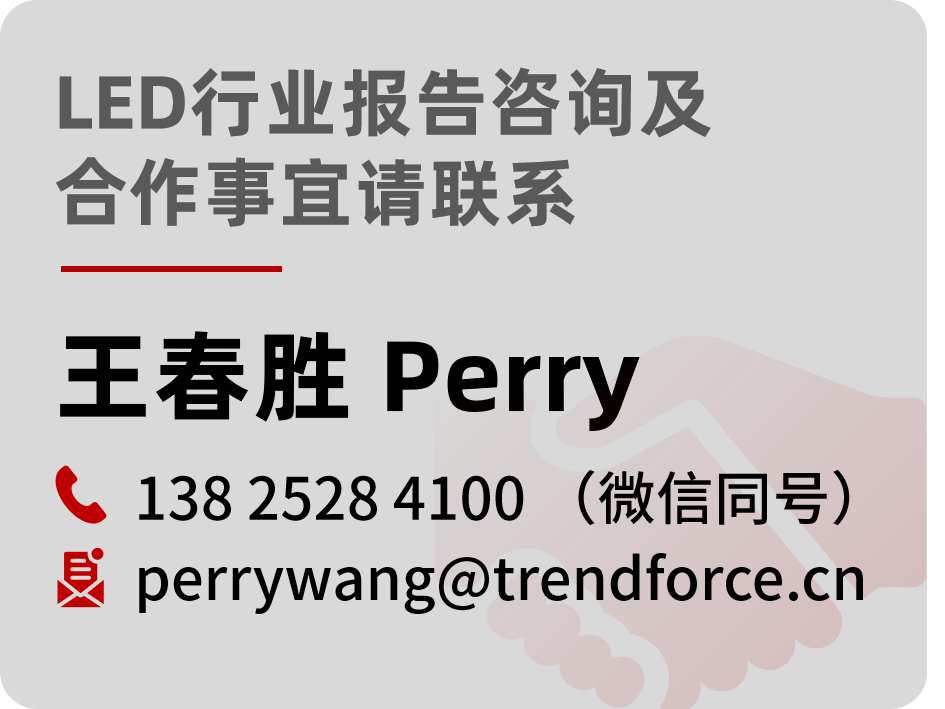
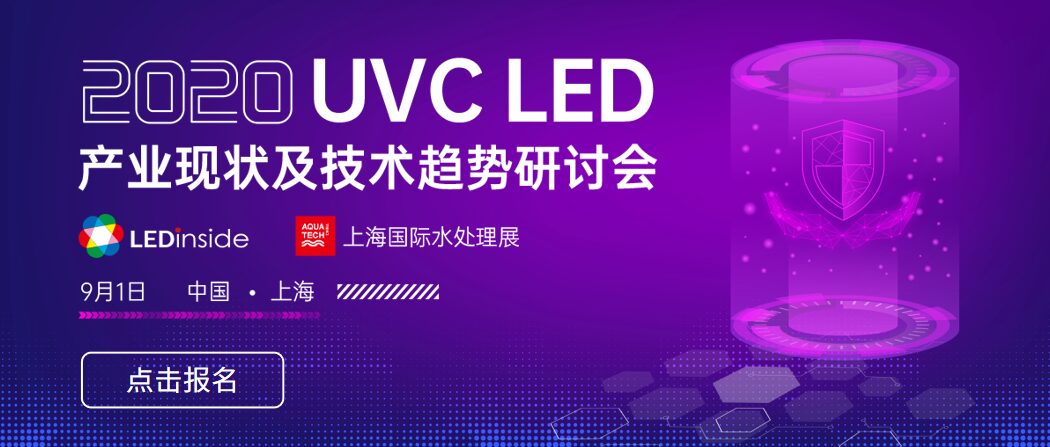
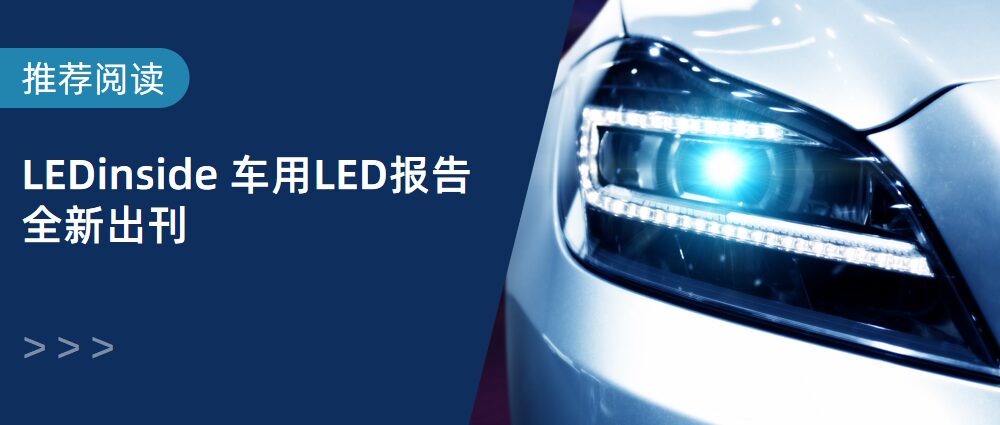
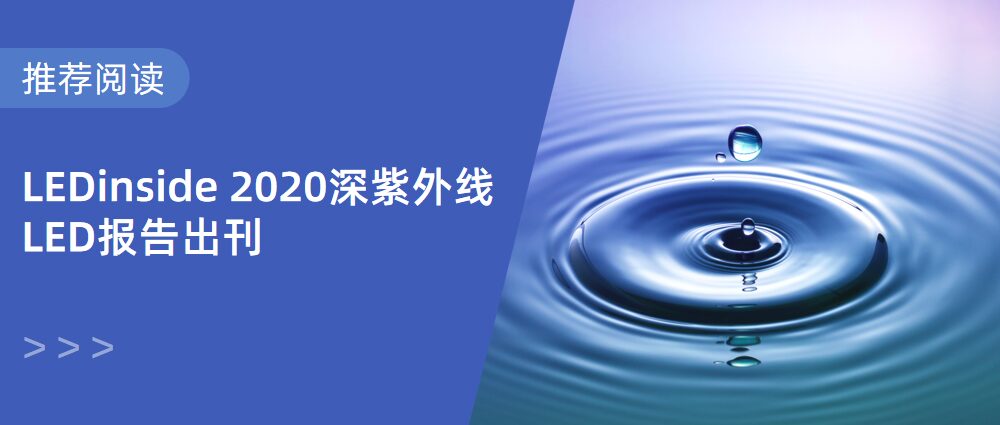
Types of Liquid Crystals
Success Lies in Open Cell
Differences Between OLED and LCD
Semiconductors and the Panel Industry
Challenges of Inkjet Printing
Positive Development, Difficult Mass Production
The Ambiguity of Mini LED and Micro LED