Of course, display technology is not limited to LCD. In recent years, Organic Light-Emitting Diode (OLED) display technology, despite having its pros and cons, is considered the new mainstream.
Basically, the working principles of LCD and OLED are completely different. OLED has the characteristic of self-illumination, eliminating the need for backlight and color filters, resulting in a thinner structure, which is favored in the industry. Like LED, OLED also utilizes the recombination of electron holes between the conduction band and the valence band to emit energy in the form of light, but it uses polymer organic films as materials, requiring no complex epitaxial processes and achieving higher efficiency in light emission.
These numerous features have made OLED highly anticipated in the industry, and it has been widely adopted. Since 2018, when Apple’s iPhone began using OLED screens, OLED has gradually gained popularity. Compared to LCD, OLED has significant advantages in viewing angles, contrast, color gamut, and brightness, but due to cost and technical issues, OLED still struggles to compete with LCD in large-size products.
The Differences Between OLED and LCD
The basic structure of OLED is to create an organic light-emitting layer on indium tin oxide (ITO) glass, and then cover it with a layer of low work function metal electrode. Under the drive of external voltage, the positive hole and negative electron combine in the light-emitting layer and release photons, producing red, green, and blue primary colors due to material characteristics, forming basic colors.
▲ The biggest difference between OLED and LCD is self-illumination. (Source: TechNews)
To enhance the injection and transport capabilities of electrons and holes, a hole transport layer is typically added between the ITO and the light-emitting layer, and an electron transport layer is added between the light-emitting layer and the metal electrode to improve light-emitting performance. In fact, the active matrix OLED (AM-OLED) often mentioned also uses thin-film transistors, similar to TFT-LCD, to emit light based on the instructions received by the transistors. Another difference is that AM-OLED commonly uses circular polarizers to reduce display interference, rather than linear polarizers.
There is also passive matrix OLED (PM-OLED), but it has obvious drawbacks. The most criticized aspect of OLED screens is that their pixel points are limited by materials, leading to a significant lifespan limitation, with issues such as color fading and burn-in occurring over time. PM-OLED operates under high pulse currents, resulting in even shorter pixel lifespans and limited resolution, making it suitable only for small-sized products. Therefore, despite its lower cost, it is not favored, and the market generally has a higher acceptance of AM-OLED.
The manufacturing process of OLED is also divided into front, middle, and back stages, with the biggest difference from LCD being the cell manufacturing process, which primarily uses vacuum deposition methods. Under high vacuum conditions, organic materials are vaporized and deposited on the substrate surface through a fine metal mask (FMM) to form RGB pixels. Because the materials generated by this method have high purity, the device lifespan is longer, making it mainstream. However, this high-precision process makes the originally simple structure of OLED panels unable to reduce costs.
▲ Main manufacturing processes for OLED panels. (Source: TechNews)
Semi-Conductors and Panel Industry
Returning to the similarities between the panel industry and the semiconductor industry, whether in terms of process or large-scale capital expenditure, it makes one think of labeling the panel industry as semiconductor. However, in reality, there are significant differences between the two, primarily in the degree of product standardization. Semiconductor chip designs can have thousands of variations to meet different functionalities, but for panels, there is relatively less variability. In this context, capacity and cost control become the main pursuits. As mentioned earlier, the panel industry is moving towards Open Cell.
Regardless of the pros and cons, to be competitive, vertical integration (IDM) may be a more suitable model for the panel industry, and it may lead to larger companies becoming even larger. This is because building production capacity is not easy; key equipment like OLED deposition machines are difficult to obtain, creating barriers. Currently, OLED is primarily monopolized by Korean manufacturers, with Samsung alone accounting for nearly 90% of the market.
Thus, new entrants in the industry are actively pursuing lower-cost inkjet printing processes. Recently, domestic giants like BOE have begun to be seen as having the potential to challenge Samsung, particularly with hopes of achieving mass production of inkjet-printed OLEDs. OLED screens are currently the preferred choice for small smart mobile devices, outperforming LCD in terms of performance, especially with flexible substrates being indispensable in emerging foldable applications. However, it will take the realization of inkjet printing processes for OLED to potentially surpass LCD in large sizes and become the true market mainstream.
Challenges of Inkjet Printing
Using deposition processes for large-size panels can easily lead to issues such as warping and precision metal shielding, but inkjet printing can overcome these difficulties at a lower cost, as it does not require a vacuum environment or FMM, and has higher material utilization, making it more suitable for large-scale production. However, this does not mean it is easier; inkjet printing primarily uses solvents to dissolve OLED organic materials and directly print them onto the substrate surface to form pixels, but creating usable cathode inks and achieving uniform film formation over large areas are technical challenges.
▲ RGB organic inkjet printing technology. (Source: TechNews)
Furthermore, to produce high-resolution panels comparable to deposition methods, precise control over the positioning of inkjet heads and the droplet volume of ink is a challenge, especially while balancing printing errors and production speed. This requires not only a mechanical platform capable of very precise operations but also optimizing the chemical composition of the ink to better control the evaporation and film formation processes. The structural design of the substrate must also meet requirements to ensure the ink spreads and wets perfectly on its surface, all of which need equipment and processes to reach certain thresholds.
Nevertheless, the inkjet printing process will be an opportunity for domestic manufacturers to achieve a leapfrog advantage, bypassing the barriers set in advance by Korean manufacturers in equipment and materials. Companies like Huaxing and Tianma Microelectronics have collaborated to establish Guangdong Juhua to better realize this technology. Of course, Samsung will not sit idly by as competitors catch up; in recent years, it has also been actively investing in inkjet printing processes and patent layouts. If it can apply this technology to its QD-OLED panels first, Samsung’s market position may become even more unshakeable.
Part 1 of the Science Series: Understanding the Technical Differences Between LCD, OLED, Mini/Micro LED (Part 1)
Business Cooperation
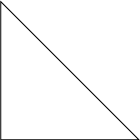
Taipei:
Contact: Cindy Li
Email: [email protected]
Shenzhen:
Contact: Calla Cheng
Email: [email protected]
Further Reading
★ Understanding the Technical Differences Between LCD, OLED, Mini/Micro LED (Part 1)
★ Visionox Releases In-Vehicle Display: Exploring Boundaries, Displaying the Future of Vehicles
★ ASUS’s Golden Triangle Layout for Floating Platforms; Acer’s Transformation to Promote Beverages
★ Pandemic Escalates! Apple Closes 7 Stores in Houston, Texas
Want to know more news?Click to read the original text and visit the WitsView website