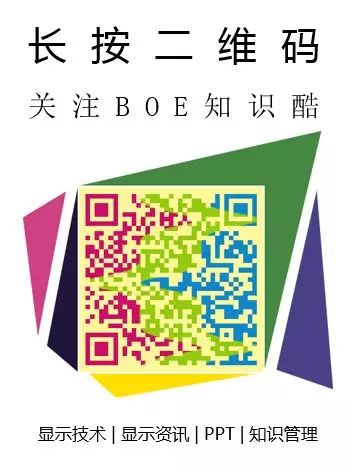
DAS BG CTO Knowledge Management Department Production
Article No. 654
Principle of LCD Display Chips
Figure 1 Structure of LCD Display Chip
As shown in Figure 1, the principle diagram of the LCD display chip shows that liquid crystal is contained between the upper and lower polarizers, and the polarization axes of the upper and lower polarizers are perpendicular to each other. In the absence of voltage, when incident light passes through the upper polarizer (polarizer), only unidirectional polarized light remains. After passing through the liquid crystal layer, the liquid crystal molecules rotate a total of 90 degrees, and the vibration direction becomes consistent with the lower polarizer (analyzer), so it can pass through the analyzer smoothly. At this time, the display is in a transparent state, i.e., non-display state. When voltage is applied, the liquid crystal molecules align along the direction of the electric field. The unidirectional polarized light emitted from the polarizer passes through the liquid crystal layer unchanged and reaches the analyzer. At this time, the vibration direction is perpendicular to the optical axis direction of the analyzer, and the polarized light cannot pass through the analyzer, resulting in a black display, which is in the display state. The light emitted through the upper and lower polarizers and the liquid crystal layer only contains grayscale information, so the light passing through the liquid crystal layer needs to pass through a color filter to produce red, green, and blue light, and finally, the output light intensity is determined by the angle between the vibration direction of the polarized light and the optical axis direction of the analyzer, displaying a color image.
Principle of LCOS Display Chips
LCOS display chips are an improvement based on LCD display chips, and both belong to liquid crystal display chips. LCD is based on transmission principle, while LCOS is based on reflection principle. The structure and display principle of LCOS display chips are shown in Figures 2 and 3:
Figure 2 Structure of LCOS Display Chip Figure 3 Display Principle of LCOS
In the silicon-based liquid crystal structure, liquid crystal is injected between the upper glass substrate and the lower CMOS active driving circuit. The bottom of the liquid crystal layer is an aluminum reflective mirror electrode. The LCOS display principle is as follows: incident S-polarized light is reflected by the PBS and illuminates the LCOS display chip. When the external voltage of a pixel in the liquid crystal layer is 0, the input S-polarized light passes through the liquid crystal layer without deflection of the polarization direction and reaches the bottom to be reflected back, outputting S-polarized light. After passing through the PBS prism, the S-polarized light returns along the original path and cannot enter the transmission light path, resulting in zero light output, and this pixel appears in the “dark state.” When external voltage is applied to this pixel, the input S-polarized light passes through the liquid crystal layer, and the polarization direction is deflected, reaching the bottom to be reflected back, outputting P-polarized light, which directly passes through the PBS prism and enters the transmission light path, resulting in this pixel appearing in the “bright state,” forming an image on the screen.
Silicon-Based Liquid Crystal Technology
Once regarded as a rare flower by many industry insiders, it has faced setbacks due to manufacturing difficulties and yield issues. However, LCoS (silicon-based liquid crystal) has still secured a place in the flat panel display field, especially in projection and high-definition television.
Silicon-based liquid crystal (LCoS) is a relatively novel and less-known display technology that is now making a significant entry into the high-definition television market. What is truly impressive is that, unlike traditional technologies that first occupy the bottom market with mediocre performance and then pursue superior image quality, LCoS has started from a high point in terms of image quality. LCoS offers the highest resolution, highest non-CRT contrast, and least distorted images among all display technologies. For people sensitive to image flicker and visual fatigue, LCoS has the highest refresh rate (120Hz), providing the smoothest images with the least flicker.
Of course, LCoS is not a brand new technology, as it has been under development for over a decade. Since 1998, Japan’s JVC has been delivering high-end, professional front-projection systems using this technology, but the scale has remained small until now. The design and manufacture of LCoS technology is very difficult, and many companies have given up or declared failure. RCA’s Thomson produced the first commercial LCoS high-definition television in 2001, followed by Toshiba (using Hitachi’s LCoS chips) and Philips, but by October 2004, all these manufacturers had withdrawn midway. In January 2004, Intel announced it would begin producing LCoS panels, shocking the entire industry, but it terminated the project in October 2004 without delivering any products. Therefore, the future of LCoS has been questioned by many analysts, but the situation has changed now.
JVC released the first rear-projection 1280Ă—720 high-definition television in July 2004, marking the advent of the second generation of LCoS. Subsequently, Sony joined the ranks in January 2005, launching high-end 1920Ă—1080 Qualia devices. Brillian followed suit, beginning to deliver its 1280Ă—720 products in mid-2005. So far, there are only a few LCoS high-definition televisions available for purchase worldwide. However, JVC and Sony recently announced the launch of their second-generation high-definition televisions, and LG announced its first-generation product (using SpatiaLight’s LCoS panels). Hitachi is another important manufacturer in the LCoS field, but it has indefinitely postponed the launch of its 60-inch and 70-inch LCoS high-definition televisions originally scheduled for November 2005.
Technical Principles
LCoS is the latest display technology that uses liquid crystals to control pixel brightness in images. The most common types of liquid crystal technology are applied to large-sized amorphous silicon liquid crystal panels, which are used in computer monitors, regular televisions, and high-definition televisions. Their sizes typically range from 5 inches to 82 inches (the highest record as of January 2006). Another type is the much smaller high-temperature polycrystalline silicon panels, which are used in video and data projectors. Their sizes are only about 1 inch, applied in various large-screen liquid crystal rear-projection televisions and high-definition televisions. In both technologies, the light source is behind the panel, and the light must completely pass through the panel from the back, including all electronic circuits and components used to control individual pixels within the panel. This blocks a lot of light, creating gaps between pixels. The higher the resolution, the more severe this issue becomes; the second major problem is that liquid crystals need to be relatively thick to provide high contrast. This slows down the response time, which can cause trailing effects (smearing) when motion or changes occur in the image.
The working principle of LCoS is to use a reflective mirror behind the liquid crystal layer, allowing light to enter from the front, pass through the liquid crystal, reflect off the mirror, and then pass through the liquid crystal again to reach the screen. This requires some slightly complex optical devices, but the results are excellent. It has obvious advantages: all electronic components are behind the mirror, so they do not obstruct light at all. There is also a lot of space behind, allowing for extremely high resolution, and devices produced using LCoS technology already have the highest resolution among all display technologies. Because light passes through the liquid crystal twice, it provides high contrast while being quite thin, significantly shortening response times and greatly reducing trailing effects.
So how does it work? Liquid crystals can rotate the polarization direction of light, and the number of rotations can be controlled by an electromagnetic field. The electromagnetic field of each pixel is formed by the silicon chip behind the mirror. In fact, the mirror is the top layer of the silicon chip, and the liquid crystal is directly coated on the mirror—this is where the name “silicon-based liquid crystal” comes from. Most panels are about three-quarters of an inch in size. To generate an image, a polarized light source is aligned with the panel. By changing the electromagnetic field at the pixel location, the brightness of each pixel can be altered. The local light’s polarization direction can be rotated, and then a polarization filter can block the portion of light that has been rotated. The silicon chip generating the electromagnetic field works similarly to a computer memory chip, arranged in numerous interlaced rows and columns of pixels. Each pixel has a corresponding memory location. Figure 1 shows a cross-section of the LCoS panel.
Like all display technologies, each manufacturer in the LCoS field has its proprietary implementation, giving its technology a specific marketing term, as indicated in Tables 1 and 2. All manufacturers specifically mention that they use vertically aligned nematic liquid crystals with inorganic alignment films. Vertical alignment improves contrast and makes the screen’s color appear naturally black when the driving signal is zero. Inorganic alignment films eliminate aging issues associated with early organic alignment films, so the lifespan of all these LCoS technologies is very long.
Table 2 lists the specifications of 1080 LCoS panels using more advanced technologies provided by each manufacturer. One of Sony’s two products uses the first-generation panel, the Qualia 004 and 006 products, while the other was announced in August 2005 using the second-generation panel, the XBR product.
Main Technical Parameters
The panel contrast ratio is probably the most important value in the table because the contrast ratio of high-definition television screens is always less than that of the panel. Pixel pitch refers to the center distance of pixels on the panel. The inter-pixel gap refers to the inactive space between pixels. The fill factor, sometimes called the aperture ratio, refers to the percentage of the active pixel area, which is close to 100%, so the gaps between pixels on the screen are usually not noticeable. The fill factor of DLP microdisplays can be several percentage points higher, but the values for high-temperature polycrystalline silicon liquid crystal projector panels are usually much lower, ranging from 50% to 70%, so their pixel structures often go unnoticed.
The lifespan value includes many factors, but can only be inferred through experimental results and estimated using statistical methods. All provided values exceed 100,000 hours, which means continuous use 24 hours a day for 11 years. The biggest issue with LCoS is that over time, brightness or contrast gradually decreases, known as aging. All manufacturers claim that the signal level refers to the number of data bits used in the panel’s circuit board to control LCoS devices. The more data bits used, the smoother the grayscale, and the less likely false contours will appear.
The response time is an industry standard that specifies the time required for a pixel to change from black to white (called rise time or Ton) plus the time required for a pixel to change from white to black (called fall time or Toff). This metric indicates how quickly the image changes and to what extent motion smear may occur in moving images.
Generally speaking, the smaller the value, the better, but motion smear involves many factors. Unfortunately, some manufacturers publish response times that actually refer to the average of rise and fall times rather than the sum of both. This can make it seem like it is twice as fast as it actually is. Therefore, when reading response time parameters, be particularly careful—ensure you know what method the manufacturer is using (for example, Sony’s Qualia SXRD panel takes a total time of 5 milliseconds as the response time parameter, while the latest XBR SXRD panel takes an average of 2.5 milliseconds as the response time, making it seem like the latter is twice as fast as the former, but it is not).
For LCoS and all other liquid crystal-based technologies, controlling each pixel’s physical process is essentially an analog process. This is an advantage because human vision is also an analog process. This eliminates the color distortion issues (dithering artifacts) present in fully digital display technologies like DLP and plasma. However, it is possible to design a silicon backplane for the panel that can work using either analog voltage or pulse-width modulation (PWM). PWM is, in fact, a digital signal. The end result is that liquid crystal remains an analog response but can be achieved in two entirely different ways, each with its own advantages and disadvantages (the digital method is similar to how a standard dimmer uses electrical pulses to control an analog tungsten bulb).
Tables 1 and 2 in the device control section list the methods used for each device. The yield of digital backplanes is generally higher, making them easier to produce (though not all manufacturers agree with this statement), and the associated driving electronic components are also cheaper. However, achieving smooth grayscale using digital control is currently quite difficult (especially in the dark end of the grayscale), which is why most models use analog backplanes.
Optical and Electronic Components
In addition to the panel, LCoS high-definition televisions also have many other important components. The projection light engine contains all optical components from the bulb to the projection lens. It first prepares the light beam for illuminating the micro LCoS panel and then magnifies the image by a linear factor of approximately 80:1, which is equivalent to 6400:1 in the area of the screen (taking a typical diagonal screen length of 60 inches as an example). The technology used in the projection light engine is as astonishing as the LCoS panel itself and is equally important for the image and picture quality that users see on the screen. It is usually the most expensive component in any projection high-definition television.
Figure 2 Structure of the LCoS Projection Light Engine
Figure 2 shows the image of the projection light engine. It should be noted that all these high-definition televisions use three LCoS panels, one for each primary color channel: red, green, and blue. A set of prisms is then used to recombine the three primary colors into a single beam of light, displayed right in front of the projection lens. The screen itself is another important component in the optical system, which also plays a crucial role in the image and picture quality. High-quality screens are quite expensive. Additionally, there are two other important optical components: the projection lens, which creates a very dark internal space between itself and the screen that absorbs stray light; and the front plane mirror at the back of the casing, which is responsible for transmitting light from the projection lens to the screen.
Two main electronic component assemblies of the LCoS silicon chip are: the panel circuit board, which is responsible for the low-level direct control of the LCoS panel; and the front-end circuit board, which contains all input connectors for the high-definition television. The front-end circuit board can convert various input signals (composite video, S-video, component video, RGB, DVI, and HDMI) into the digital format required by the panel circuit board. It also manages the adjustment and control menus that allow users to make changes. The panel circuit board generally contains controls that only the manufacturer can use, including the gamma tables used to control the LCoS panel.
Continuous Improvement of Digital High-Definition Micro-Display Television Technology①LCD Micro-Display Television  Due to the low aperture ratio of LCD rear-projection, which originally was only 54%, this year we visited Epson in Japan, and the company has launched the D5 generation LCD, with the aperture ratio increased to 70%, contrast improved by 50%, and brightness also significantly enhanced; new technology for developing liquid crystal (HTPS) using inorganic alignment films further improves the aperture ratio, enhances contrast, and improves black reproduction capability, making images more refined, and the display clearer and more realistic, which Epson calls “Crystal Clear Fine” technology.  Recently, SONY has launched a 50-inch 3LCD digital high-definition micro-display television with a physical resolution of 1920×1080, priced at only 17,000 yuan, making it very competitive in terms of cost-performance ratio.②DLP Micro-Display Television   To improve the poor color reproduction of single-chip DLP projectors, American TI has adopted a new color processing technology called Brilliant Color, which uses RGB three primary colors and corresponding complementary colors of cyan, magenta, and yellow in a six-segment color wheel, enhancing the color gamut and saturation, increasing brightness by 20-40%; using Darkchip technology, a black coating is added under the micro-mirrors to reduce light reflection, decrease gaps between pixels, and improve contrast and brightness; to meet the requirements of 1080p high-definition digital television and reduce chip costs, TI has developed a method to display 1920×1080 (i.e., 1080p) images using a micro-mirror array similar to 960×1080, called “Smooth Picture” technology, which relies on three balanced angles of -12, 0, and +12 degrees at symmetrical pixel positions to produce a certain grayscale white or black pixel through pulse-width modulation (PWM), while the remaining angle is used for a dual-pixel fully black state, achieving the effect of single micro-mirror dual-pixel display.③LCOS Micro-Display Television  Since LCOS can be said to absorb the advantages of both LCD and DLP technologies, it is a reflective liquid crystal with a high aperture ratio, thus it has high resolution, high pixel area occupancy, low light consumption, fast response speed, small size, and light weight, making it the best display technology for 1080p high-definition digital television. Recently, the yield of packaged products has improved, especially with rapid advancements in optical engine technology. The three-chip machines mainly include IBM, Colorlinlc, 3M, Shichuang, and Jdsu; while single-chip devices include sequential color and rolling shutter methods, as well as a new color control method from American Everbright Technology that lies between the two. The optical engine solutions from Shichuang and Jdsu indicate that they are low-cost solutions, with Jdsu believing its optical engine is similar to the 3LCD structure, while Shichuang considers its optical engine solution to offer good cost-performance ratio, as shown in Table 1, Figures 3, 4, and 5.
â‘ Imaging Devices  The three micro-display imaging devices LCD, DLP, and LCOS each have different situations: A) LCD imaging devices are controlled by Japanese Sony, Epson, and South Korea’s Nitto; B) DMD imaging devices are produced exclusively by American TI; C) LCOS imaging devices are open technology and have not been monopolized by any company.②Light Source   This is a crucial component for digital high-definition micro-display televisions to meet challenges, as the extended lifespan of ultra-high-pressure mercury lamps is difficult to resolve, and foreign companies producing ultra-high-pressure mercury lamps do not sell bulbs to maintenance units, leading to bulbs being sold at prices 2-3 times higher than normal, which is one reason many consumers are reluctant to buy digital high-definition micro-display televisions and is also an excuse for some to criticize them.  To address the light source issue, we take the following measures:  a) Encourage domestic ultra-high-pressure mercury lamp manufacturers to improve quality.  b) Develop new light sources.  c) Strengthen after-sales service for micro-display rear-projection television bulbs to ensure consumers do not incur losses due to bulb failures.  d) Accelerate the formulation of bulb standards.③Optical Engine   There are about thirty domestic enterprises (including foreign-funded enterprises) that research and produce optical engines for digital high-definition micro-display televisions. Except for foreign wholly-owned, joint-venture, and cooperative enterprises, most do not produce on a large scale. To respond to the price drop of flat-panel televisions, we must industrialize the domestic research and production of optical engines for digital high-definition micro-display televisions to improve quality and lower costs. We plan to choose better condition enterprises to support their rapid industrialization in conjunction with the opportunity to establish standards for optical engines.④Rear Projection Screen   The price difference between domestic and imported rear-projection screens is significant. There are about ten domestic enterprises that research and produce rear-projection screens, but only a few can supply rear-projection television screens. Localizing rear-projection screens is one of the important measures to reduce the cost of digital high-definition micro-display televisions. To meet challenges, we must support capable enterprises to achieve large-scale production.
Recently, the call for micro-displays has grown louder. Micro-display refers to making display devices very small. However, these very small display devices can show high-density and high-information content. For example, a display area of less than 1 square inch can display a pixel density of 1024*768. This micro-display can be magnified through an optical system to any size for viewing. It can project a large screen image or be made into a goggle-style portable viewing system, enlarging the displayed content into a virtual image. In short, it is a very meaningful innovation to create highly technical display devices in a small form and then use other optical systems to process them into any suitable form for human use and viewing.
There are many ways to create micro-displays, with the following being the main methods:
1. Liquid Crystal on Silicon (LCOS)
2. Organic Light Emitting Diode (OLED)
3. Digital Micromirror Device (DMD) and several others.
Among these, LCOS is the most promising type of micro-display. It can be divided into reflective and transmissive types. This article will mainly introduce the structure, principle, and application of reflective LCOS micro-displays.
1. Structure and Principle of LCOS Micro-Displays
LCOS stands for liquid crystal on silicon. As the name suggests, it means that the liquid crystal display is made on a silicon chip.
From the diagram, it can be seen that it is essentially a liquid crystal display device where the lower glass substrate has been replaced with a single crystal silicon substrate used for making TFT and IC circuits.
Why adopt this structure?
We know that ordinary TFT active liquid crystal display devices generally generate a layer of amorphous silicon film on a glass substrate to make the TFT active matrix. Amorphous silicon has a low electron mobility, so the area of the TFT devices made is large. For a fixed pixel area, it occupies a large area proportion, meaning a low aperture ratio, resulting in less light passing through the pixels. As can be seen from the diagram, a pixel is occupied by the TFT device and edges. If we add various factors like front and back polarizers and color filters, the transmittance of ordinary TFT liquid crystal display devices is only about 10%. Therefore, it is necessary to equip it with a high-power backlight source during application, greatly weakening the micro-power consumption advantage of liquid crystal display devices.
Later, people changed the amorphous silicon TFT devices to polycrystalline silicon TFT devices. Due to the electron mobility of polycrystalline silicon being an order of magnitude higher than that of amorphous silicon, the area of the TFT devices can be significantly reduced, thus greatly increasing the aperture ratio. However, the increase in light transmittance is still not sufficient, and the light utilization remains low.
People began to think of single crystal silicon, which has an electron mobility an order of magnitude higher than that of polycrystalline silicon, allowing the area of the TFT devices to be made smaller, achieving an aperture ratio of over 95%. However, single crystal silicon cannot be generated on glass, so people simply made the TFT devices directly on single crystal silicon wafers. Single crystal silicon wafers are opaque, so people made the liquid crystal display devices into reflective types. Reflective devices do not absorb light like transmissive devices, so the light utilization is higher. To further improve light utilization, a layer of reflective mirror is vapor-deposited on the surface of the TFT matrix pixels, maximizing light utilization. Since the substrate is single crystal silicon, it is best not to waste it; therefore, all peripheral circuits such as row and column drivers, controllers, etc., are also made on the silicon wafer. Thus, this hybrid of large-scale integrated circuits and liquid crystal display devices is born. Similar to the hybrid advantages in the biological world, this technological hybrid also has strong advantages.
2. Advantages of LCOS Micro-Displays
1. Since it combines the display device and large-scale integrated circuits into one, it gives the display device some intelligent functions, which we can call intelligent display devices.
Liquid crystal display devices are called twin brothers of large-scale integrated circuits. The lightweight, thin, small, and micro (low power consumption) characteristics of display devices have made information display personalized, and the result of personalization has provided a vast market for large-scale integrated circuits. In the 1970s, with the rise of personal calculators, liquid crystal display devices and large-scale integrated circuits rapidly developed together, gradually forming the world’s largest industry. In the 1990s, liquid crystal display devices collaborated with large-scale integrated circuits to achieve breakthroughs in portable computers.
Liquid crystal display devices cannot leave large-scale integrated circuits for even a moment. Without large-scale integrated circuits, the lightweight, thin, small, and micro (low power consumption) characteristics of display devices lose their significance. Conversely, if large-scale integrated circuits cannot use liquid crystal displays to present their vast, rich, and timely processed information to human vision conveniently and accurately, their abilities will also be greatly buried. They must be combined to unleash their potential. Fortunately, they have finally merged into one product, with large-scale integrated circuits providing intelligence to liquid crystal display devices, and liquid crystal display devices enabling the intelligence of large-scale integrated circuits to connect more directly with human vision.
2. Products can be made smaller and more precise.
Ordinary LCDs require photolithography on glass substrates to manufacture pixels. Generally, achieving a pixel size of 0.28mm is already quite challenging, as an active device must be made on each pixel. However, pixels in LCOS are made on single crystal silicon wafers, which can be processed using large-scale integrated circuit techniques to achieve pixel sizes below 4µm. Therefore, a silicon wafer of only 0.1 inches can produce products with pixel densities of 1024×768 or even 1920×1240.
One can imagine that the information density of the product display increases while the area decreases. The material cost will naturally decrease significantly. Currently, the trial production cost of LCOS screens is only 50 dollars.
There is no need to worry about devices being too small to see the displayed content; as long as a suitable optical system is used for magnification, any display area can be obtained.
3. It solves the problem of low aperture ratio in ordinary TFT-LCDs, improving light utilization.
The aperture ratio refers to the proportion of the effective display area on the display pixel. Generally, for each pixel area of ordinary TFT-LCD, a region must be delineated to manufacture a field-effect transistor and capacitor. Since ordinary TFT-LCDs are made on amorphous silicon film layers on glass substrates, the area occupied by field-effect transistors and other active devices is relatively large due to the low electron mobility of amorphous and polycrystalline silicon. In contrast, the silicon wafer of LCOS is single crystal silicon, which has a much higher electron mobility than amorphous and polycrystalline silicon, allowing for much smaller devices and achieving a high aperture ratio of over 96%.
We know that liquid crystal display devices are passive display devices, modulating external light to achieve display. Ordinary LCDs have a polarizer on the front and back, and LCDs act as switches, modulating polarized light to complete the display. The polarizers absorb light to generate polarized light, resulting in low transmittance for the produced liquid crystal display devices. Generally, the transmittance of TFT-LCDs is only a few percent, so a strong backlight source must be installed behind the liquid crystal display devices for clear display. This backlight source consumes a lot of power, negating the low power consumption advantage of liquid crystal display devices.
Since the back substrate of LCOS is a single crystal silicon substrate, LCOS is generally made into reflective types. The pixel of the silicon wafer is also coated with an optical mirror, allowing most incident light to be utilized.
When comparing ordinary transmissive projection televisions made with TFT-LCDs and reflective projection televisions made with LCOS, the latter requires only 1/5 the power consumption of the light source to achieve several times the brightness of ordinary transmissive TFT-LCOS projection televisions. A 400-watt light source of LCOS reflective back-projection 74″ high-definition television can exceed the brightness of CRT televisions. This is a level that no other projection television can currently reach.
4. It diversifies the display methods.
Because the size of LCOS screens is very small, an optical system must be used to achieve display. Common methods include:
(1) Projection magnification method: can use both front projection and rear projection.
(2) Direct magnification method: usually used in handheld devices.
(3) Virtual image magnification method: can be monocular or binocular, further divided into external shadow cutting and external scene overlay.
Generally, when used for television, the projection magnification method is adopted. It can produce high-definition televisions ranging from 54″ to 100″ at a cost not exceeding 10,000 yuan and a weight not exceeding 10 kilograms. Of course, it can also be made into rear projection computer displays.
Through an optical magnification system, images can be projected onto a suitably sized screen for mobile communication or video calls, and it can also be made into goggle-style (binocular or monocular) portable viewing systems, creating a magnified virtual image in front of the viewer’s eyes.
5. Easy to colorize.
Typically, liquid crystal display colorization is done using micro-color film methods, i.e., making three sub-pixels into red, green, and blue primary color sub-pixels to synthesize a full-color pixel. This is a spatial mixing method that occupies a large number of pixel spaces and reduces resolution. In contrast, LCOS is inherently monochrome and uses red, green, and blue cyclical illumination to achieve color display through temporal mixing. Since the response speed of LCOS can reach microsecond levels, this method is entirely feasible and greatly reduces device costs while increasing display resolution.
6. Fewer external leads, simple connections, and easy overall assembly.
Ordinary liquid crystal display devices have a large number of dense external leads; for example, a 1024*768 dot matrix liquid crystal display device requires 2592 external leads, causing many inconveniences for assembly. However, since LCOS is made on single crystal silicon wafers, the row and column leads are internally connected to integrated circuits through semiconductor processes, leaving only a few data control lines, timing lines, power lines, etc., outside. It can connect with the front-end circuit through a universal connection port, which is very convenient. Figure 4 is the system block diagram of LCOS.
7. Low investment, easy to scale production.
A TFT-LCD production line requires significant investment due to the need to generate amorphous or polycrystalline silicon on glass and perform special and unique processes like micro-color films. Therefore, the investment is substantial, generally amounting to hundreds of millions to over a billion dollars, with long construction cycles and slow recovery. In contrast, the structure of LCOS products means it does not require a separate investment in a full production line; it can separately invest in semiconductor and liquid crystal factories, with the semiconductor factory’s requirements being lower. The liquid crystal factory only needs to invest in alignment, packaging, filling, and module processes. During production, the semiconductor integrated circuit factory and the liquid crystal factory can produce separately. Thus, the investment level is significantly reduced.
Since the semiconductor process is fast and yields high, and the liquid crystal packaging and filling processes are few, the production volume is large and efficiency is high. One can imagine that, coupled with the fact that the materials used in LCOS are minimal, the relative cost will naturally be much lower.
Advantages of LCOS:1. High resolution2. Strong heat blocking capability of light sources3. High light utilization and brightness4. Fast response speed5. High contrast6. Low cost7. High aperture ratio and detailed images8. Long lifespan of 20,000 hours9. Retains the low power consumption driving characteristics of LCDsDisadvantages of LCOS:1. Multiple manufacturers, standards are not yet unified2. High technical threshold, certain technical difficulties
DLP Projector DMD Display Chip
Figure 4 Structure of DMD Micro-Mirror Chip
The display chip used in DLP projection technology is the DMD chip, which consists of thousands of micro-mirrors. The structure of the micro-mirror unit is shown in Figure 4. As seen in Figure 4, the DMD micro-mirror unit is fixed on a yoke and connected to the yoke and pillar by a torsion hinge structure, allowing the mirror to rotate 12 degrees. The working principle of DMD is to reflect the required light using the micro-mirror device while absorbing unwanted light through a light absorber to achieve image projection, with the light direction controlled electrostatically by adjusting the angle of the micro-mirrors.
Source: Optoelectronics and Display
| BOE Knowledge Cool · BOE’s Only Knowledge Platform |
Exciting materials available for download
Follow BOE Knowledge Cool, and reply in the public account dialog box with keywords like OLED, 8D, 8K, workplace skills,team leader, knowledge managementto obtain relatedvaluable thematic articles.
Recommended Reading:
-
Samsung Galaxy Fold Pre-Sale Experience in the US
-
Surface Phone, OPPO, LG’s New Patents on ‘Folding’
-
The Advanced Edition is Here! See How These OLED Structures Are Cultivated
-
What is the Common PWM Frequency Used in OLED?
BOE Knowledge Cool
BOE’s Only Technical Public Platform