During a visit to a robotics technology exhibition, I observed that some robots used Mecanum wheels for movement. In specific working environments, the design of Mecanum wheels facilitates the robot’s ability to turn in place and translate.
However, I also identified two issues: Mecanum wheels must operate on relatively flat surfaces; and during long-distance straight movements, they are less convenient than traditional smooth wheels. Is it possible to design a switching device that allows the tire surface to switch freely between Mecanum wheels and smooth wheels?
I searched online using keywords such as “Mecanum wheel”, “Mecanum wheel switching device”, “variable size hub”, and “tire switching device”, and found patents on inventions like “a Mecanum wheel omnidirectional mobile robot”, “Mecanum wheel vehicles and operation methods”, and “Mecanum wheels with shock-absorbing devices, chassis, and supporting robots”. This indicates that there are already many applications of Mecanum wheels in our country, but currently, no device has been found that allows for the free switching between Mecanum wheels and smooth wheels.
While browsing the web, I saw a round table that can change its desktop size through rotation. This design inspired me greatly; I want to combine a retractable hub with Mecanum wheels using a rotating opening and closing device to achieve free switching between Mecanum wheels and smooth wheels.
My design focuses on the arrangement of Mecanum wheels, variable size hubs, link mechanical structures, drive circuits, and control modules. The components in the device, such as the Mecanum wheels, main wheels, and special structure hub links, are made using 3D printing. The main control module is programmed using Arduino.
Figure 1: Schematic of Mecanum Wheel and Traditional Wheel Switching Principle
(1) Mecanum Main Wheel Design
12 Mecanum small wheels are arranged on the main wheel at a 45° angle.
Figure 2: Mecanum Main Wheel Design
(2) Traditional Smooth Wheel Hub
The traditional smooth wheel hub consists of four fan-shaped rings, which form a circular ring when contracted, with the hub height lower than that of the Mecanum wheel. When expanded, the two side hubs extend 90° higher than the Mecanum wheel, entering the working state of traditional smooth wheels.
Figure 3: Traditional Smooth Wheel Hub Effect Diagram
(3) Link Structure
Four links distributed on the central circular hub connect to the traditional smooth wheel hub. By controlling the rotation of the central circular hub with a motor, the traditional smooth wheel hub can be extended and contracted.
Figure 4: Link Structure Diagram
(4) Circuit Electrical Connection Design
A four-channel slip ring is installed to solve the electrical connection problem of the servo (with three control wires), enabling infinite rotation motion while increasing service life and ensuring smoothness.
(1) Tools and Materials
Tools used: diagonal cutting pliers, wire strippers, files, electric drills, 300 W soldering iron, multimeters, Phillips screwdrivers, computers, etc.
Materials used: several structural components made of resin materials, several 10mm long M3 self-tapping screws, various types of wires, various types of heat shrink tubes, one 25 reduction motor, one Arduino UNO main control and expansion board, one rotary potentiometer, one toggle switch, one 7.4 V lithium battery, one 8.4 V charger, one four-channel slip ring, one MG996R servo, and one matching servo disk.
(2) Production Process
The assembly was completed step by step according to the screenshots from the computer software. It is important to maintain the order; otherwise, issues like the inability to secure equipment may occur.
(1) Purpose
To test the maximum extension and contraction of the outer ring hub under link control.
(2) Process
Control the extension and contraction of the outer ring hub using a control switch. Measure the extension stroke, maximum and minimum outer ring diameters with calipers, and record the experimental data.
(3) Experimental Records
(4) Experimental Conclusion
Through the built-in link structure, combined with the precise program control of the servo, a maximum rotation angle of 175° and a minimum precision of 2° for rotational angle control can be achieved. The link structure allows for a maximum linear extension of 20 mm, fully meeting my design requirements.
Additionally, with the separate outer ring hub design I created, the outer ring shape can change from approximately 175 mm to a standard 195 mm circle.
Figure 6: Minimum Outer Ring Hub Shape Achieving Mecanum Wheel Movement Form
Figure 7: Maximum Outer Ring Hub Shape Achieving Smooth Wheel Design with Complementary Outer Ring
The entire device achieves free switching between Mecanum wheels and smooth wheels, fully utilizing the advantages of different tires, allowing it to adapt to more working environments. In situations requiring in-place rotation and omnidirectional movement, the Mecanum wheel mode can be used. For long-distance transitions, the smooth wheel mode can be adopted to reduce wear on the Mecanum small wheels and enhance the smoothness of the movement process.
This invention emphasizes the realization of structural prototypes, suitable for light loads in terms of load capacity and motor drive. The motor used in this prototype design is a laboratory-grade motor, and the structure material is made of 3D printed resin, which needs improvement in load-bearing capacity. In the future, high-torque motors and steel material structures can be used, along with self-locking positioning devices to enhance the system’s load capacity.
In practical applications in industrial scenarios, high-torque motors with self-locking devices and flexible materials can be selected to meet increasingly stringent environmental requirements. This invention can also be applied in industries such as sorting and transportation.
I would like to express my gratitude to teachers He Bin from Beijing No. 80 Middle School and Xu Bo from outside the school for their significant help and support during the development of this project, as well as to Beijing No. 80 Middle School for providing a good research platform for me. (Advisors: He Bin, Xu Bo)
Student Liu Jin’s Mecanum Wheel and Smooth Wheel Automatic Switching Device is a typical invention project. The completion of this work reflects the inventor’s critical thinking ability, skill in identifying and analyzing problems, and innovative consciousness in proposing solutions based on the shortcomings of existing things. It also demonstrates the inventor’s strong innovative design capability. Liu Jin has laid the direction and foundation for the implementation of the project through the design of the Mecanum main wheel, application of traditional smooth wheel hubs, link structure design, hub bracket design, and structural design of the work. Furthermore, it showcases the inventor’s scientific research potential. The tools and materials used in the production process, assembly, etc., are all accurate, especially as he conducted experimental tests on the performance of the work and drew relatively complete conclusions, showing a clear process of scientific and technological exploration.
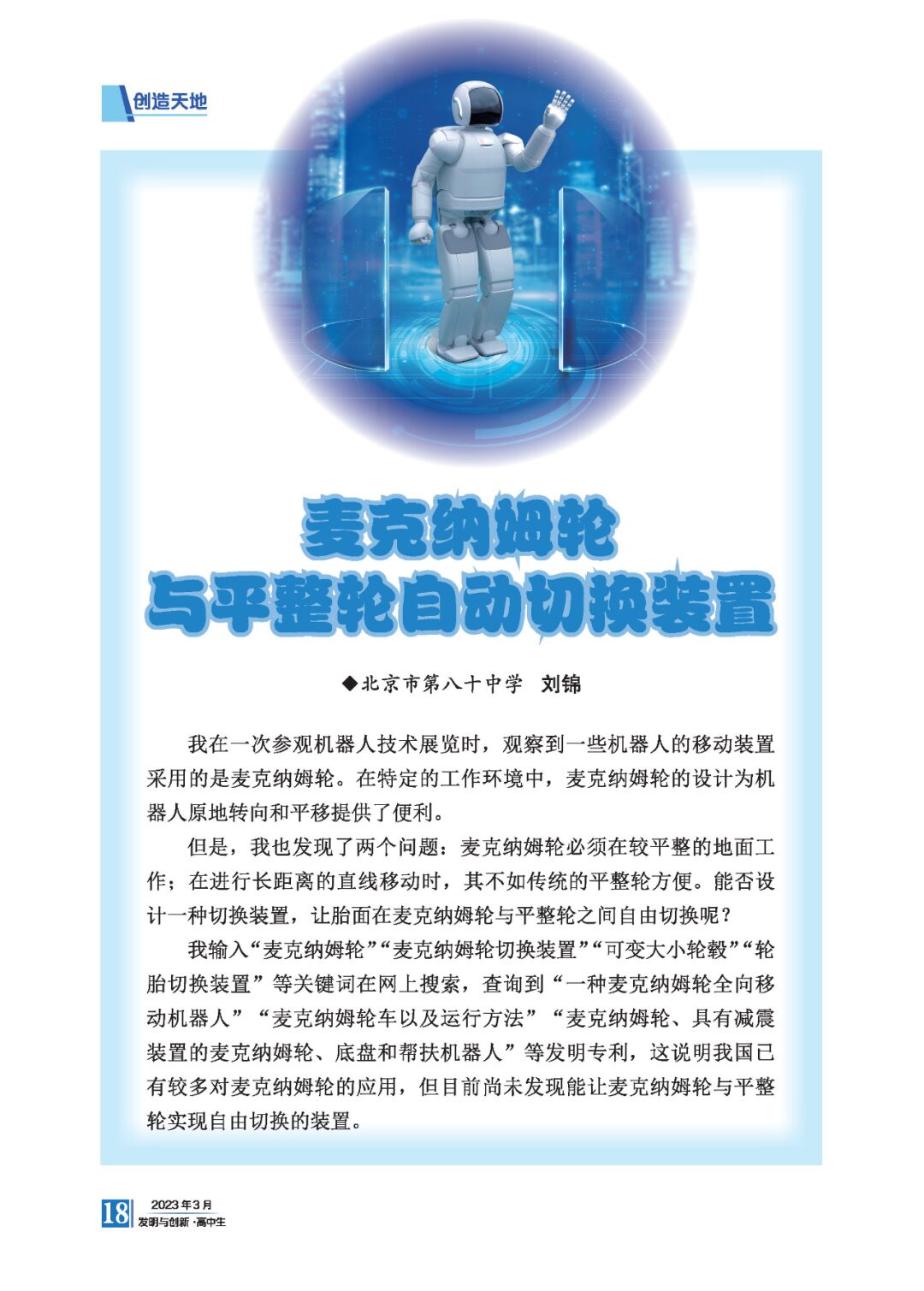
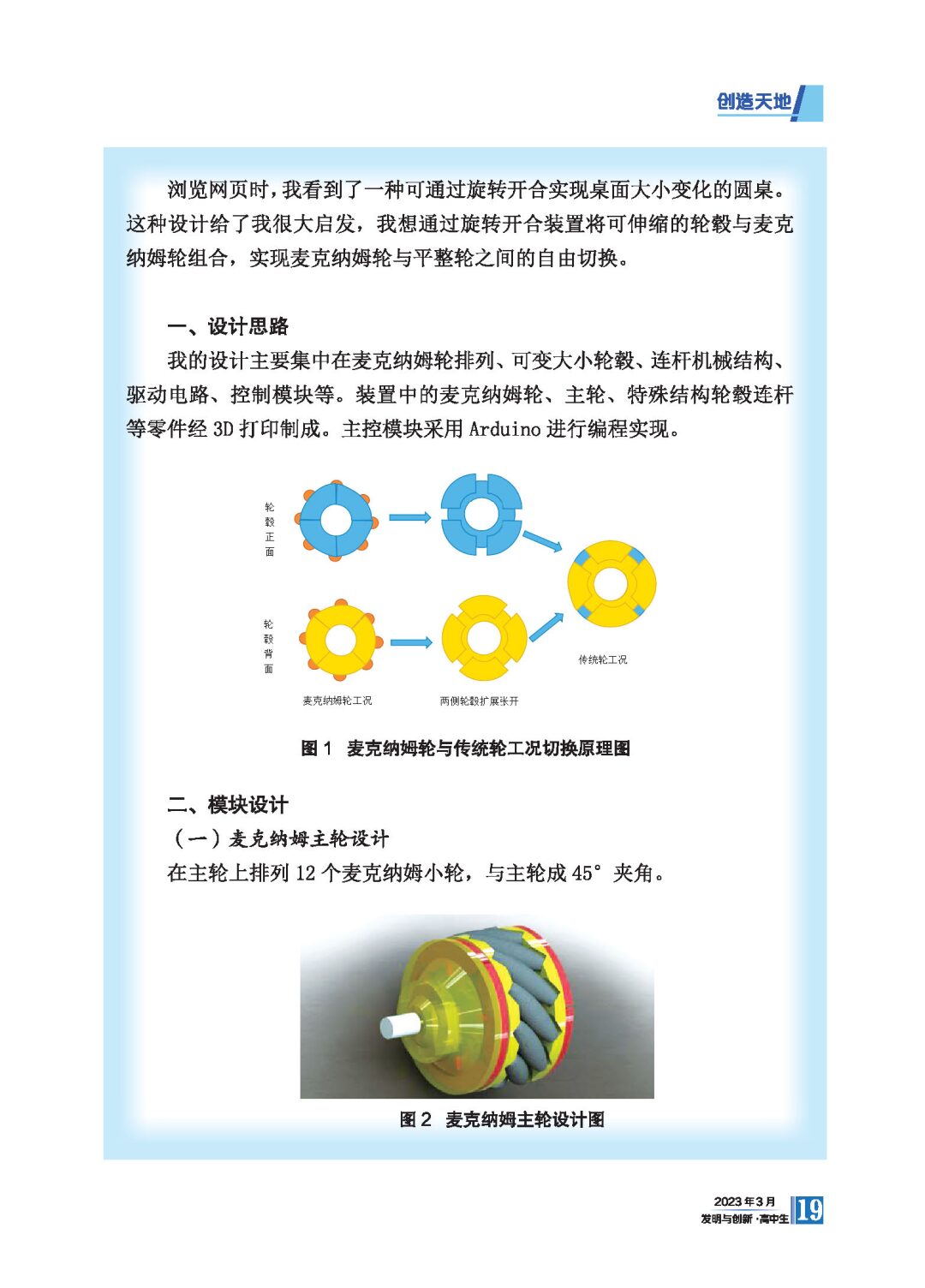
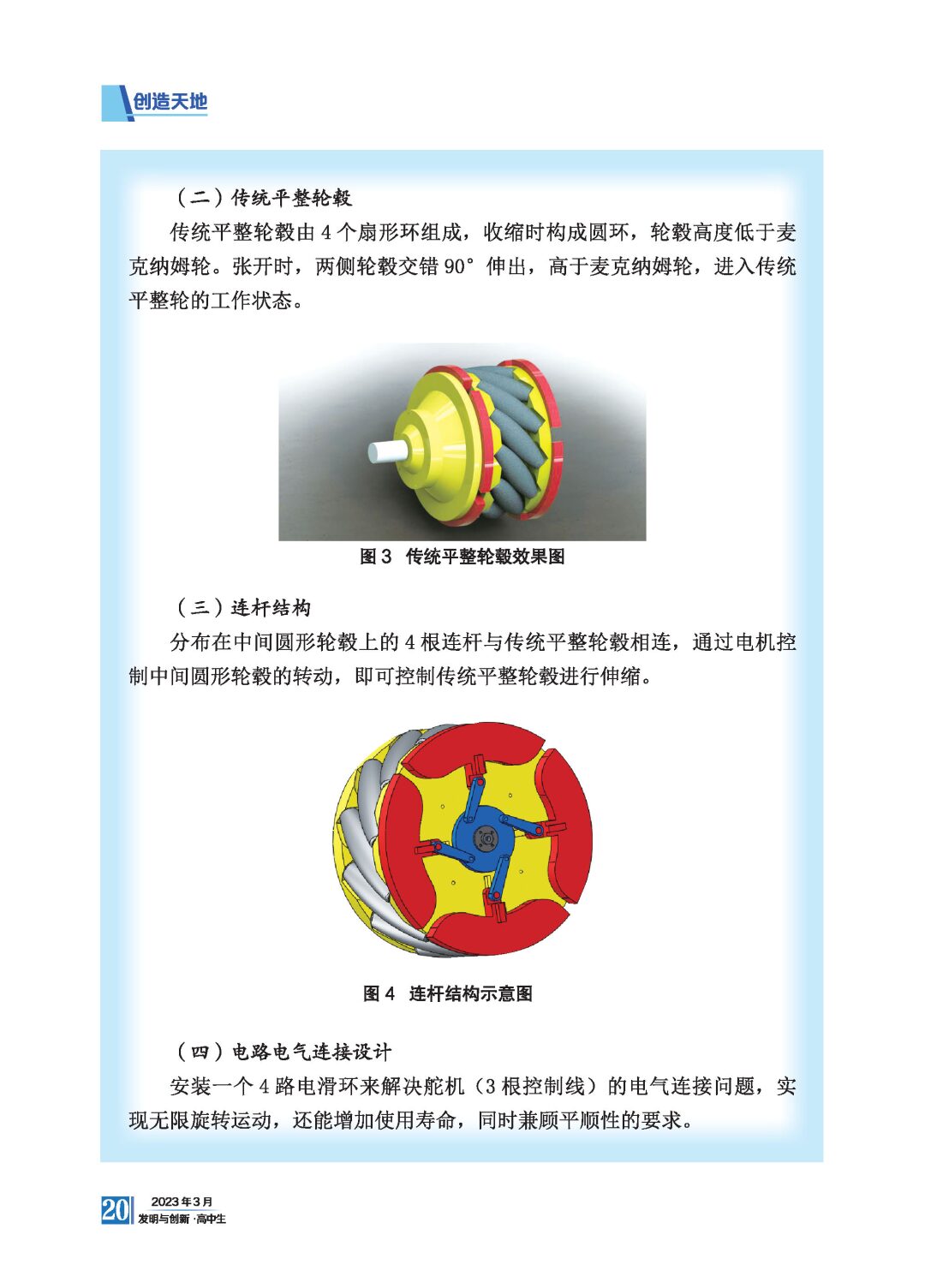
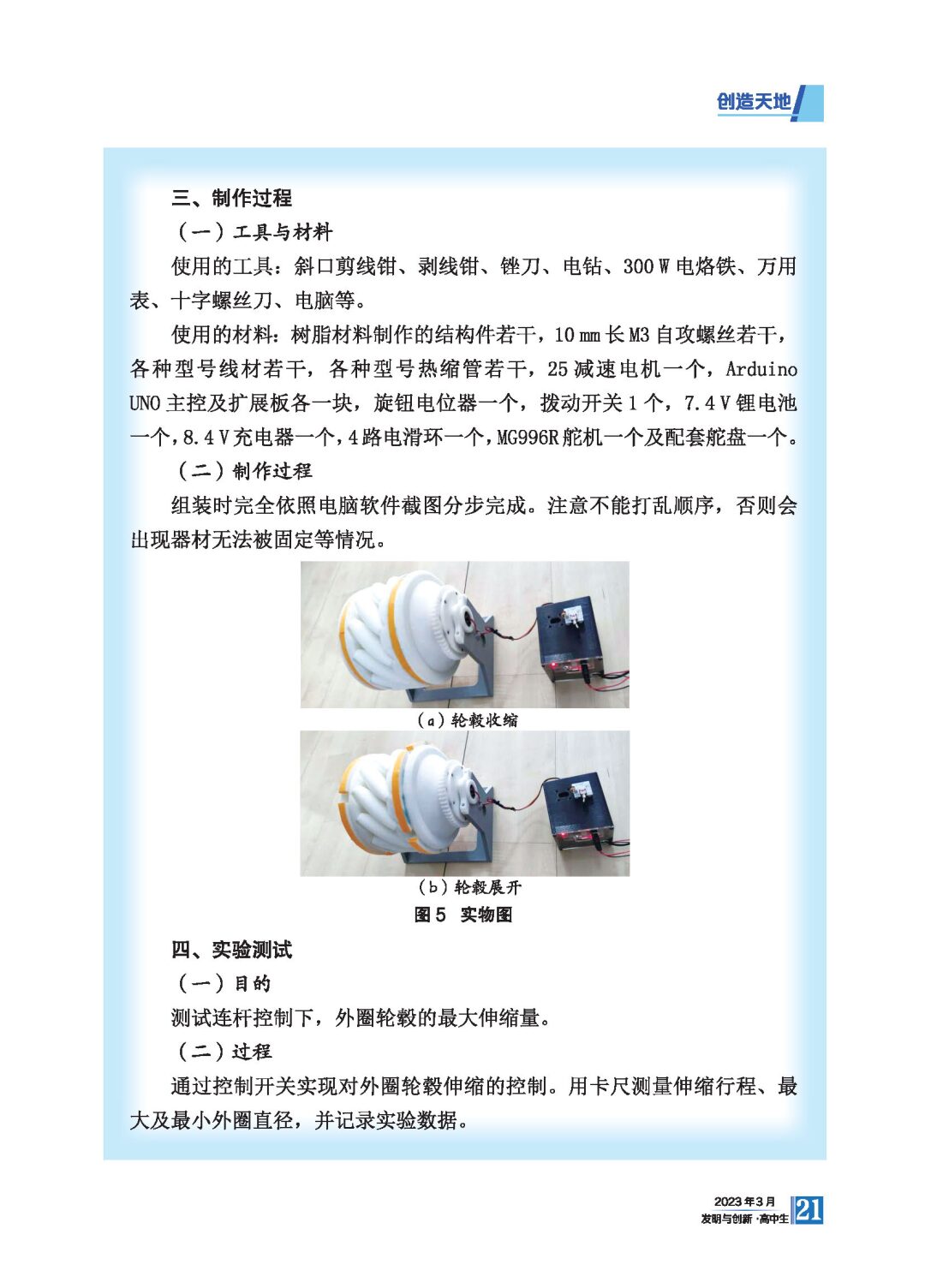

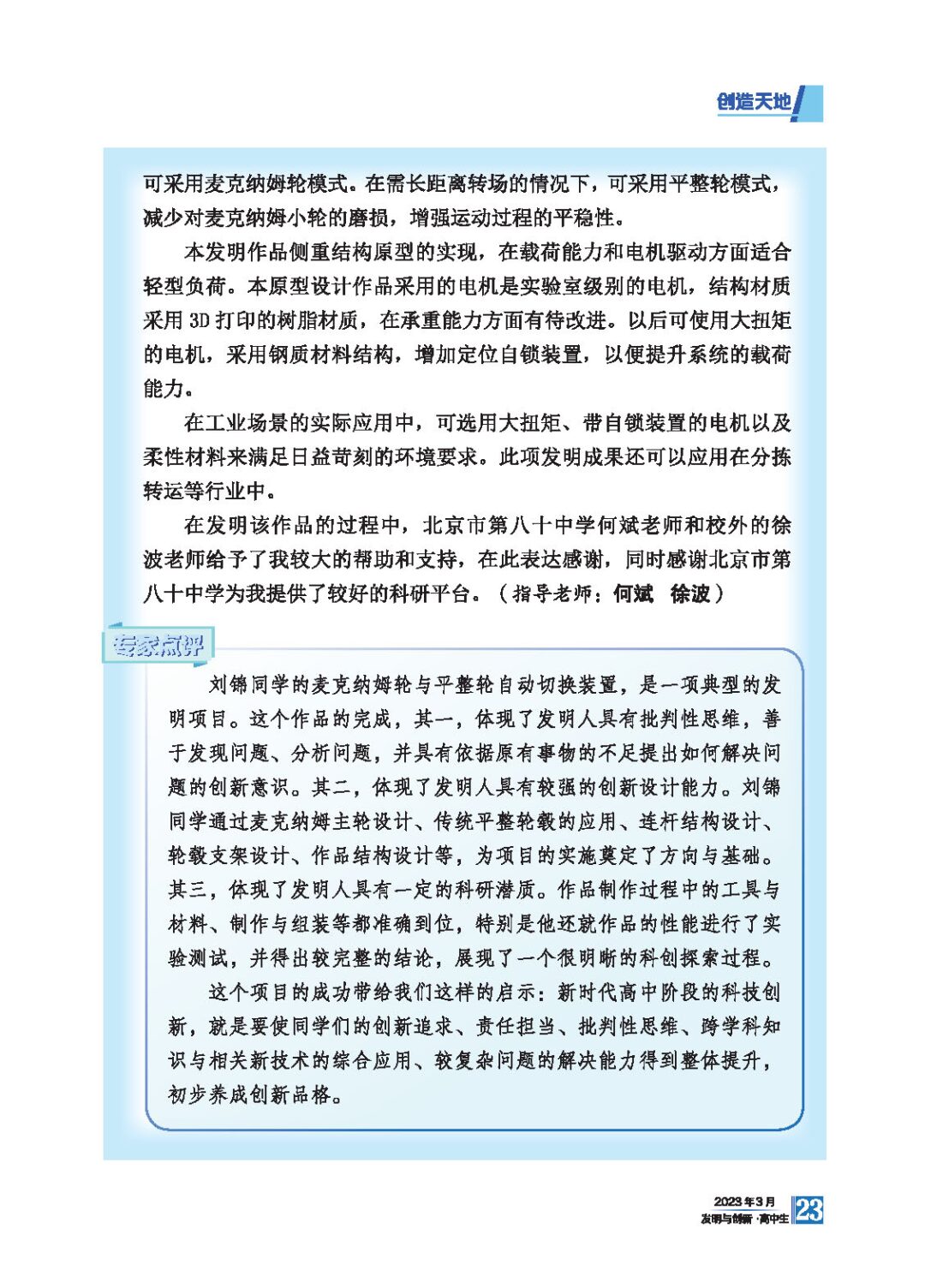
1. Everything You Want to Know About “Invention and Innovation” is Here
2. “Invention and Innovation” has a New Look, Welcome to Subscribe!
3.[Special Report] “Scientific Innovation Mentor Team” Mentor – Wu Yao
4.[Special Report] “Scientific Innovation Mentor Team” Mentor – Pei Jing
5.[Special Report] “Scientific Innovation Mentor Team” Mentor – Chen Ran
Innovation is the most distinctive quality of this era.
Innovation is the most significant symbol of this magazine.
As the winds of change blow, only innovation leads the way!
As education moves towards a dual reduction, innovation accompanies our growth!
Welcome to subscribe to the national excellent periodical,
Hunan Province’s “Double Ten Best” periodical,
youth innovation education popular science periodical
——“Invention and Innovation”.
Click the image below to subscribe online directly!
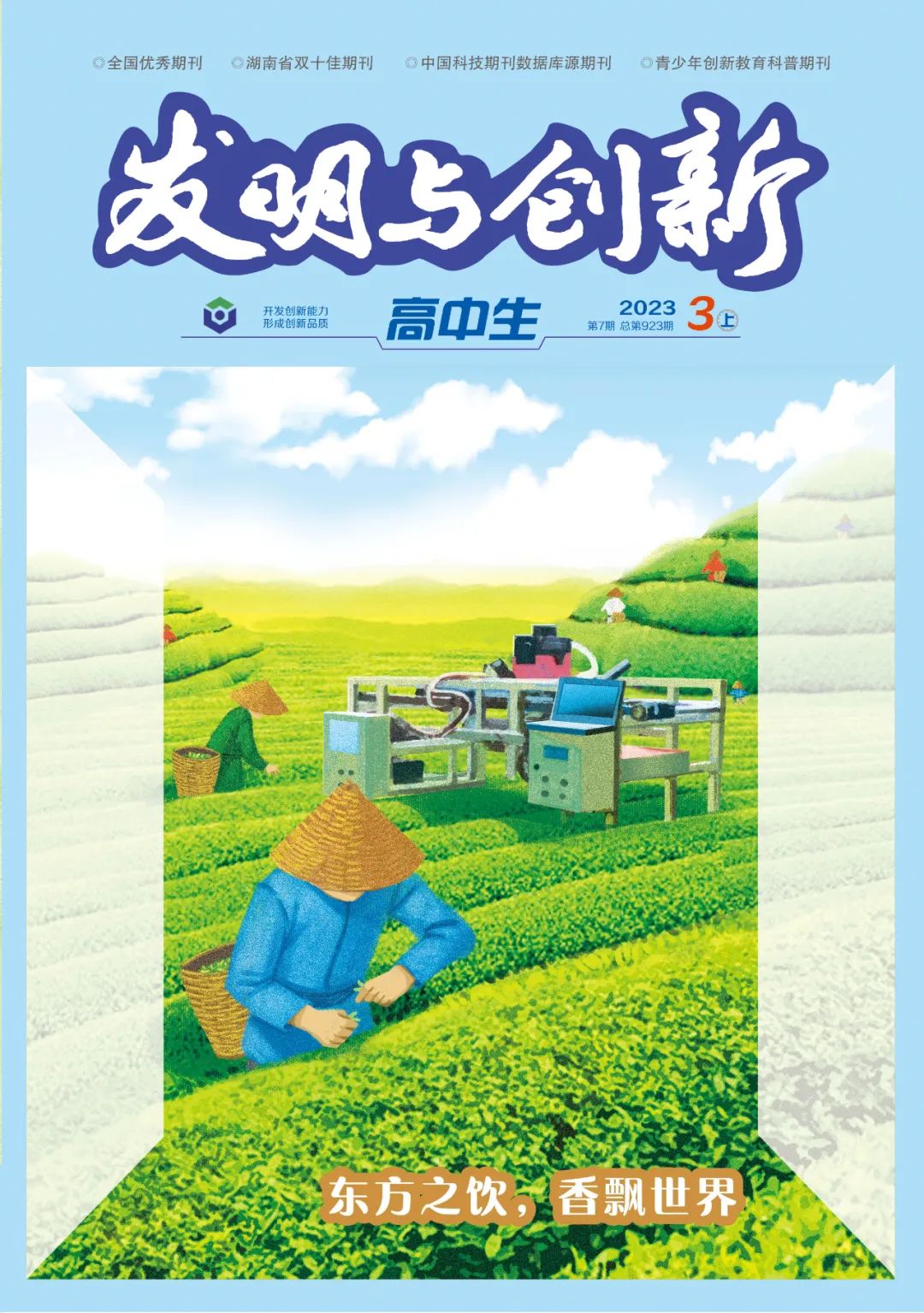
Source: “Invention and Innovation” March 2023 High School Edition
Editor: Qin Yinyin, Xia Yanhui
Review: Qin Yinyin
Final Review: Li Baichun