The automotive camera is the “eye” of autonomous driving and a core component of the ADAS system in the autonomous driving field.When automotive radar cannot fully achieve environmental perception and object recognition, automotive cameras use lenses and image sensors to collect image information to compensate for this functionality.
An automotive camera includes optical lenses, image sensors, image signal processors (ISP), serializers, connectors, and other components. With the significant increase in camera pixels, there are higher demands not only on the computing power of chips but also on the power supply power and thermal management. Additionally, improvements in resolution, dynamic range, and frame rate require changes to the power supply architecture.
Currently, automotive camera module power design can be broadly categorized into three solutions: completely discrete, fully integrated, and partially integrated.
Completely Discrete Design Solution
First, let’s look at the completely discrete power design solution, where the power budget for the camera module needs to be determined first. Generally, the current requirements of the camera module are determined by the sensors and serializers/deserializers included in the system. Additionally, in some cases, the PoC voltage from the ECU is fixed, so it is also important to know whether the selected PoC cable can provide the required current for the power target.
(Completely discrete architecture design, TI)
The image above shows a module design by TI using MIPI CSI-2 video interface, FPD-Link III, and PoC. This camera uses a coaxial power connector powered by the central ECU, and through the same coaxial cable, the camera can transmit video data to the central processor and initialize through the processor’s I2C reverse channel. In a discrete design, a single coaxial cable connector meets the needs of digital video, power supply, control, and diagnostics.
The completely discrete design offers high layout flexibility, allowing for very compact solutions. Although this may require more design time to select each different IC, it has the highest flexibility among these solutions.
Fully Integrated Design Solution
The fully integrated solution is straightforward, using a dedicated power management IC (PMIC) to generate all power rails for the imager and external circuits. As a key component managing the power supply of electronic devices, PMICs can integrate multiple functions to utilize space more effectively and manage system power. Although PMICs may seem inconspicuous, they are one of the largest segments in the analog chip market.
(ADAS seven-channel PMIC, Renesas)
The high scalability and programmability of PMICs mean they can simplify the power design for multiple high-definition camera modules, reducing development time and BOM costs. PMICs provide power and voltage monitoring, transmitting data and power through coaxial cables, connecting remote automotive camera modules to displays or machine vision processing systems via high-speed serial interfaces. Besides size and efficiency, scalability is a critical factor in automotive camera module power design. PMICs with scalability/reusability clearly have advantages in shortening development time and saving costs.
(ADAS camera module power design, Infineon)
Automotive-grade PMICs can maximize performance per watt, minimize power loss, and improve system efficiency for compute-intensive platforms like SoCs, FPGAs, and application processors. However, this fully integrated solution has reduced layout flexibility due to fixed pins, which may lead to an increased area of the solution. However, current automotive-grade PMIC manufacturers are minimizing dimensions without compromising device performance.
Partially Integrated Design Solution
Compared with fully integrated PMICs, partially integrated designs simplify some designs through a mix of single-channel and multi-channel power usage. This allows for easier expansion while ensuring some layout flexibility. For example, a partially integrated solution using source switches can reduce the number of pins, as output pins are also used for current sensing, reducing IC costs and PCB space usage by merging pins.
Although partially integrated designs have some scalability, their expansion is not as free as PMICs, as most ICs have different voltage variations and compatible components occupy space.
When designing power for automotive camera applications, regardless of the design solution chosen, we need to minimize the size of the design to meet the small size requirements of the automotive camera module housing. It is also best to avoid lower switching frequencies, ideally using high-frequency solutions with automotive certification >2MHz. If additional protection is needed for devices, a voltage regulator with a wide input can be added.
Comparison of Camera Module Power Architectures
From a market perspective, fully integrated high-performance automotive-grade PMICs are the most favored choice for automotive camera module power.Currently, the domestic replacement rate of automotive-grade PMICs is not high, while the demand for them in autonomous driving scenarios is significant, keeping prices firm.Whether or not there are automotive-grade PMIC products can be seen as a watershed distinguishing the capabilities of PMIC manufacturers.
Leading foreign PMIC manufacturers such as TI, Infineon, ADI, ST, NXP, onsemi, Renesas, Microchip, and Rohm are continuously launching small-sized, low-EMI, and high-power-density PMICs that meet automotive standards. The direction of small size has almost become a key area of competition among manufacturers, such as Rohm’s automotive-grade PMIC launched this year, which integrates four power systems needed for automotive cameras in a package measuring just 3.5mm×3.5mm, which is also an ultra-small size in the industry.
There are also many domestic players, most of whom are in the stage of laying out automotive-grade PMICs, such as SIRUI, Singatron, Biyiwai, and Nanxin, who have been continuously investing in the supply capacity of automotive PMICs for many years. With a wide variety of automotive-grade PMICs and different application scenarios, domestic automotive-grade PMICs must not only choose the right development path but also enhance technological innovation to launch stable products to occupy a place in the automotive supply chain.
Programmable power management integrated circuits (PMICs) with integrated voltage monitors can extend from automotive non-functional safety applications to functional safety applications without needing to redesign the power supply. This fully integrated solution is highly favored in automotive camera design. Typically, the power circuit design for automotive camera modules needs to balance shortening development time and configuring smaller camera modules. In addition to size, thermal performance, electromagnetic compatibility issues, and power supply rejection ratio performance, scalability must not be overlooked.
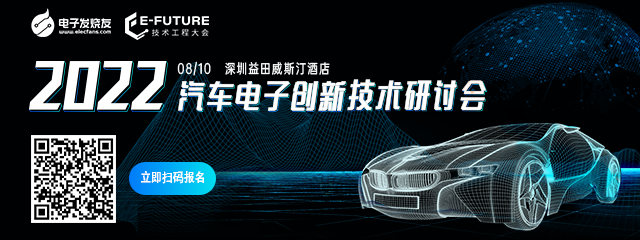

Disclaimer: This article is originally from Electronic Enthusiasts Network, please indicate the source above when reprinting. For group communication, please add WeChat elecfans999, for submission, reporting, and interview requests, please email [email protected].
More Hot Articles to Read
-
ASML warns the US: cutting off DUV lithography machines to China will interrupt the semiconductor supply chain, is it really so?
-
Do automakers need to build their own batteries, how will CATL play?
-
The shortage of automotive chips has eased! China’s chip shortage situation may last until 2023!
-
Baidu releases L4 autonomous driving car, costing only 250,000, Li Yanhong: future taxi fares will be half the price
-
The US chip bill “causes new problems”, restricting subsidized companies from investing in the mainland for the next 10 years, whether it passes is still pending