Introduction:
The choice of sensors and lighting depends on the application, making optics very important. Optical product suppliers are struggling to keep up with the rapid development of the machine vision industry.
New applications and sensors often drive innovation in optics and lighting within the machine vision field, and this innovation often needs to happen simultaneously. The choice of sensor largely depends on the final application being discussed, and lighting is often similar.
For optical devices, sensors and lighting are often “problematic applications,” which frequently require challenging problem-solving tasks. Even very sensitive sensors may sometimes fail to operate unless light can be correctly and evenly distributed over the effective area of the lens. The challenge that optical product suppliers face is that the development of machine vision applications is so rapid that it is difficult to keep pace.
With the development of sensor and lighting technologies, the demand for new applications is so high. The issue faced by optical product suppliers has become “which lens designs need to be optimized to work in synergy with the applications occurring downstream?” said Greg Hollows, Vice President of Imaging Business at Edmund Optics.
Challenges in Optical Design
Remote sensing devices mounted on drones may prefer large-format sensors with high resolution, simply because more pixels can be packed into a larger array, allowing the drone to collect as much image data as possible within a limited flight time. If you are a sensor manufacturer, this application demand is easy to understand. Therefore, it makes sense to actively invest in the development of larger-sized sensors. However, for optical manufacturers, this choice is not so simple, as they cannot design larger lenses without considering other factors.
Many systems combine lens components and filters, which can become more complicated for the wide field of view applications typically associated with drones today.
Collaborative Design with Lighting
This call for a holistic design approach also extends to lighting components. Ideally, illumination and imaging optical systems should be designed as a whole to ensure that the lens collects the best light and does not collect suboptimal light. Collaborative design of lighting and optical components can more easily match the two for optimal performance. It can also minimize costs and shorten time to market.
The wavelength range of the light source in imaging systems also affects the choice of lens and the overall system performance. Narrowing the range to a few nanometers can often enhance image contrast. Using filters with broadband light sources can help, but such solutions are not always as flexible as narrowband light sources.
Utilizing the wavelength of the light source can accomplish a lot in machine vision. Using narrowband light sources such as LEDs can minimize the corrections needed in lens design and introduce interesting new options to enhance image contrast. How specific materials absorb or reflect certain wavelengths can also highlight defects that are invisible under broadband light sources.
Within the visible spectrum, each color has an opposite color that can be used to enhance image contrast. Therefore, illuminating a green object with green light will make it appear brighter on the image sensor, while illuminating it with red light (the opposite color of green) will make it look darker.
However, enhancing image contrast does not have to rely on narrowband light sources. For example, short wavelengths in the ultraviolet range scatter surface features more strongly than visible or infrared light. Alternatively, if ultraviolet light is absorbed, it tends to be absorbed at the surface. In either case, imaging how ultraviolet light interacts with materials using gas discharge tubes or UV LEDs can help detect contaminants or shallow scratches that are invisible in other spectral regions. The benefits of this are evident when inspecting glass displays, lenses, and other materials that appear transparent in the visible spectrum.
Key Concepts:
■ Unless light can be correctly and evenly distributed over the effective area of the lens, machine vision sensors will not function.
■ Lighting and imaging optical systems should be collaboratively designed to ensure that the lens collects the best light.
Consider this:
Where do you use machine vision, and what aspects are most beneficial to you?
– END –
This article is from the November-December 2019 issue of CONTROL ENGINEERING China, in the “Source of Technology” column, originally titled: The Importance of Optical and Lighting Design for Machine Vision Applications.
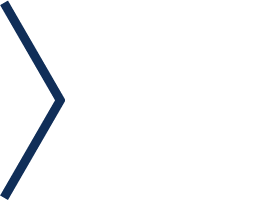
This Issue Magazine
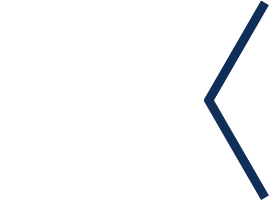
Good News: The WeChat mini-program for CONTROL ENGINEERING China is now online. Click the magazine cover to open the mini-program to read past magazines.
Recommended Reading
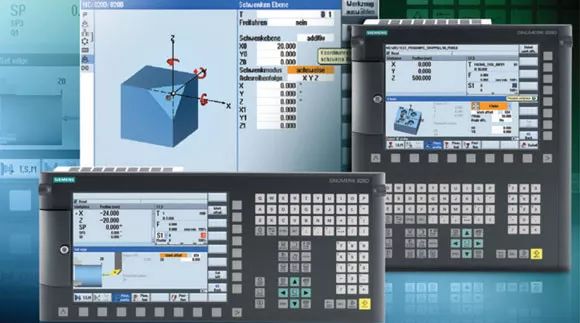
Do you really know these “pits”? – How to choose the right human-machine interface?
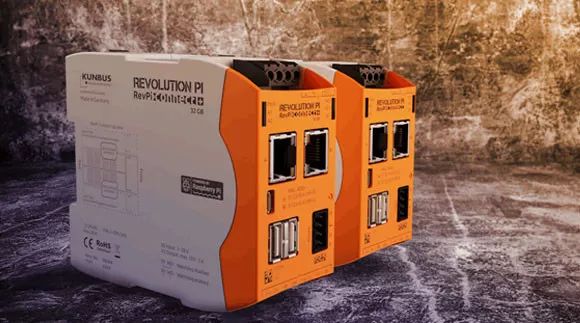
Has the wolf really come? igus has created an intelligent drag chain with Raspberry Pi industrial computer
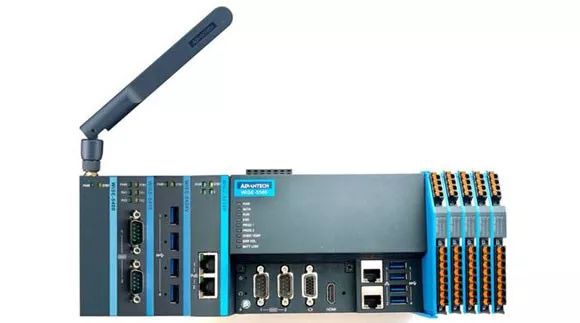
What is an edge controller? Is it IPC+PLC+Gateway? Let’s explain it with a physical object today!
An automation engineer entered the live broadcast room of the internet celebrity Jiaqi!

Breaking News!
We invite you to join the industrial automation circle
Starting in 2020, to enhance communication between editors and readers, as well as between readers, we will establish various WeChat groups for professional readers focused on industrial automation technology.
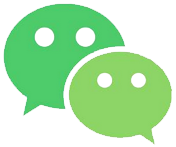
Industrial Network Group
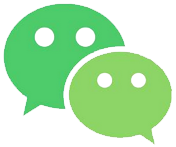
PLC Group
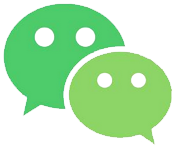
DCS Group
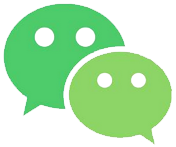
Machine Vision Group
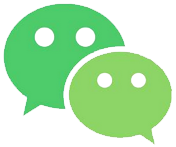
Robot Group
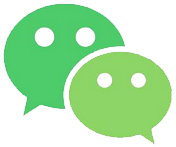
Industrial Software Group
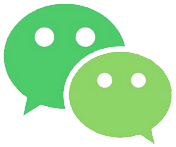
Human-Machine Interface Group
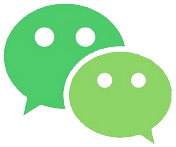
Motion Control Group
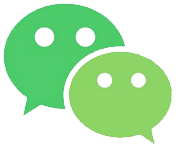
Sensor Group
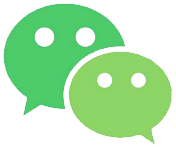
Industrial Safety Group

Instrumentation Group
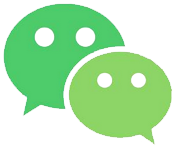
AI/AR/Group
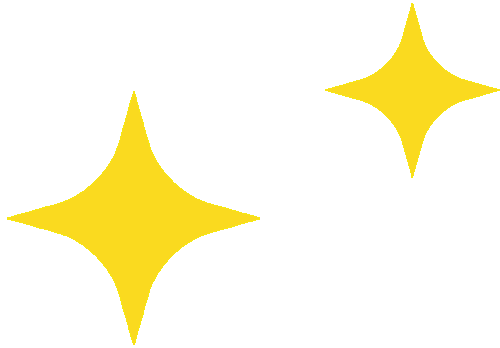
Scan the QR code on the right
Send “Name + Technical Interest + City” to add the editor on WeChat, and after review, you will be invited to join the corresponding technical group.

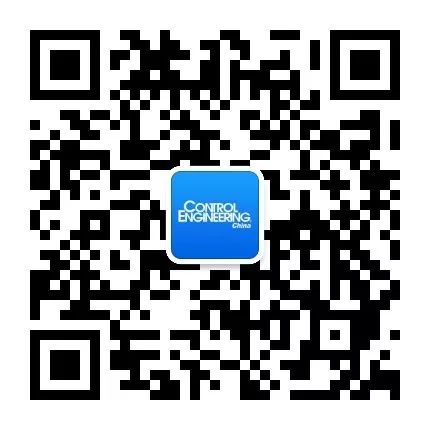