New imaging applications are flourishing, from collaborative robots in Industry 4.0, to drones for firefighting or agriculture, to biometric facial recognition, and handheld medical devices for home care. A key factor behind the emergence of these new application scenarios is that embedded vision is more prevalent than ever. Embedded vision is not a new concept; it simply defines a system that includes a vision setup that controls and processes data without an external computer. It has been widely used in industrial quality control, with the most familiar example being the “smart camera.”
In recent years, the development of affordable hardware components from the consumer market has significantly reduced the bill of materials (BOM) costs and product size compared to previous computer-based solutions. For example, small system integrators (OEMs) can now source single-board computers or module systems like NVIDIA Jetson in small batches; larger OEMs can directly obtain image signal processors like Qualcomm Snapdragon. On the software side, available software libraries can accelerate the development speed of dedicated vision systems and reduce configuration difficulties, even for small batch production.
The second change driving the development of embedded vision systems is the emergence of machine learning, which enables neural networks in laboratories to be trained and then uploaded directly to processors so that they can automatically recognize features and make decisions in real-time.
Providing solutions suitable for embedded vision systems is crucial for imaging companies targeting these high-growth applications. Image sensors play an important role in large-scale adoption as they directly influence the performance and design of embedded vision systems, and their main driving factors can be summarized as: smaller size, weight, power consumption, and cost, abbreviated in English as “SWaP-C” (decreasing Size, Weight, Power, and Cost).
1
Reducing costs is crucial
The accelerators for new applications of embedded vision are the prices that meet market demand, and the cost of vision systems is a major constraint to achieving this requirement.
1
Saving optical costs
2
Cost-effective sensor interfaces
3
Reducing development costs
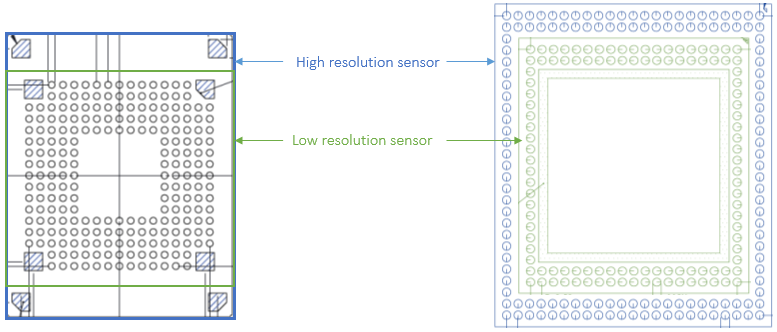
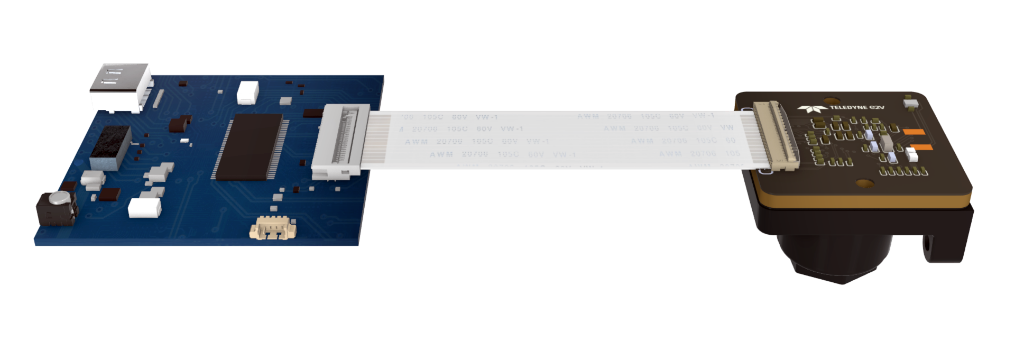
2
Improving autonomous energy efficiency
3
On-chip functions pave the way for programming vision systems
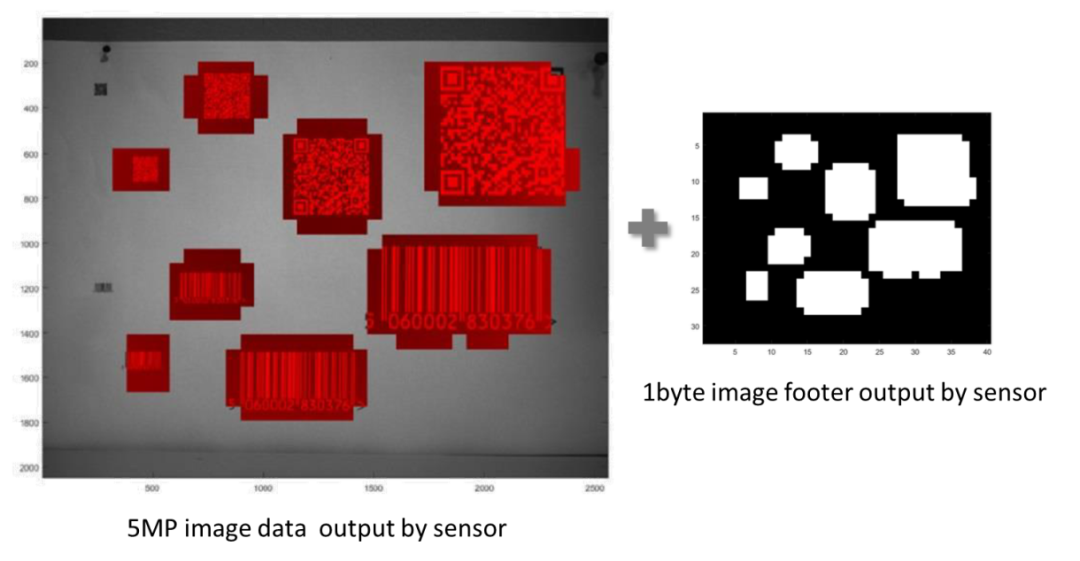
4
Reducing weight and size to fit minimal application spaces
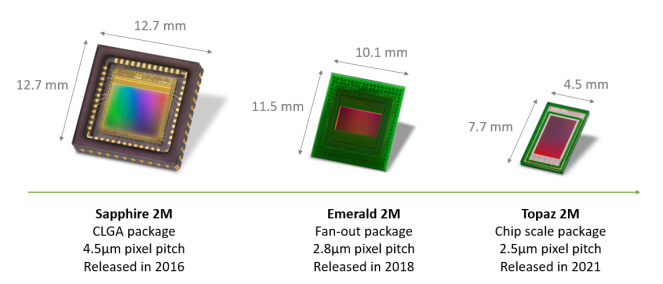
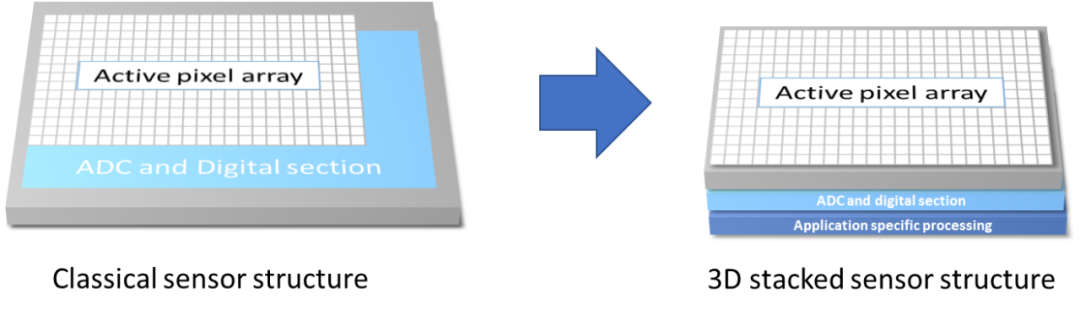
This public account is a high-paying long-term column author. Welcome technology practitioners or enthusiasts with excellent writing skills to contact Sensor Editor: YG18511751369 (WeChat ID)
Looking forward to the next article with 100,000+ views from you!
Disclaimer: The copyright of this article belongs to the original author. If any videos, images, or text used in this article involve copyright issues, please notify us as soon as possible, and we will confirm copyright based on the proof materials you provide and pay remuneration according to national standards or delete the content immediately! The content of this article reflects the original author’s views and does not represent the views of this public account or bear responsibility for its authenticity.

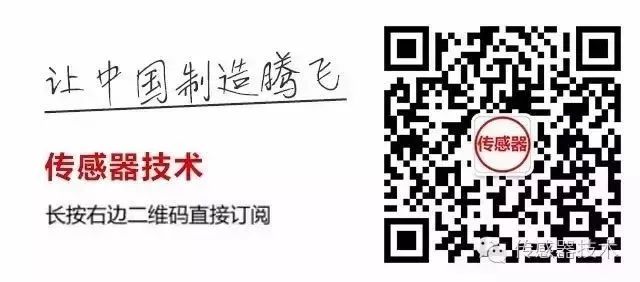
To publish your products, please click “Read the original text”
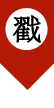