Authors: Fu Haitian, Fan Xiaofang
In Disney’s animated movie “Big Hero 6,” a story is told about a young boy and his robot health assistant, Baymax. Baymax’s mission in the film is to care for others, acting as a professional health consultant. With just a simple and quick scan, Baymax can detect vital signs and treat ailments based on pain levels. Baymax can also continuously learn, upgrade its disease database, and improve its own system. In reality, Baymax is not just a purely fictional character; its image and functionality are based on the insights of leading research institutions such as Carnegie Mellon University, Harvard University, and MIT regarding the trends of next-generation robots, representing a scientific vision of the specific forms of future medical robots.
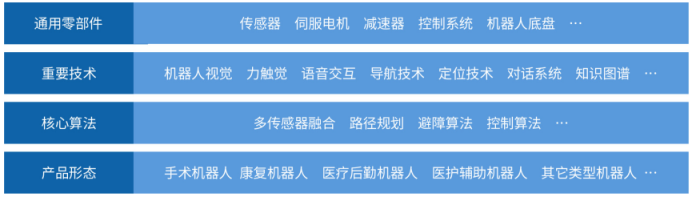