-
Training on CiA402 Axes for CANopen/ETherCAT
-
Detailed Application Description of CANopen Bus on Codesys Controllers
-
Pure Content | Easily Apply CANopen Communication Protocol in PLC & Servo
-
Why is CANopen Communication So Popular in Servo Control???
-
Detailed Explanation of CANopen Application in TwinCAT2.1 by Beckhoff PLC
The CANopen protocol originated from the CAN protocol used in automotive communication and is popular in Europe. The first company to integrate the CANopen protocol was BECKOFF, WeChat Public Account: Industrial Control Sharing primarily promotes BECKOFF control solutions, combined with other third-party peripherals such as I/O, servo, and frequency converters.
CANopen consists of master and slave nodes, where one master can network with up to 127 slaves, forming a distributed control network with one entry and one exit between nodes. WeChat Public Account: Industrial Control Sharing generally does not support multi-master mode. Compared to traditional protocols like pulse and Modbus, its advantages include: WeChat Public Account: Industrial Control Sharing
1. Long transmission distance, up to 1 kilometer;
2. High speed, up to 1Mbit/S;
3. More I/O can be controlled with more nodes;
4. In motion control applications, it saves a significant amount of wiring labor and hardware costs compared to pulse types;
5. In scenarios requiring multiple axes, it reduces the number of pulse axis modules, resulting in a higher cost-performance ratio for the overall solution.
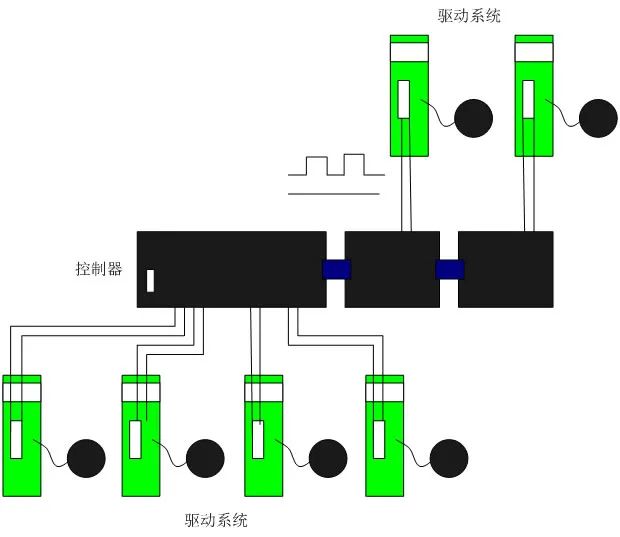
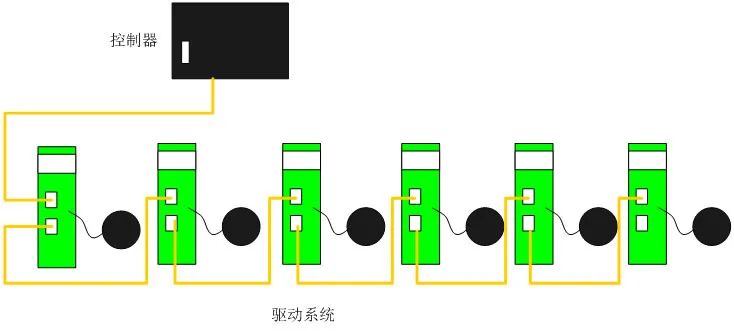
Due to the above advantages, a large number of products based on the CANopen protocol have emerged in recent years. Companies making PLCs and motion controllers/cards have integrated the CANopen protocol and launched various CANopen masters and remote slave I/Os; companies making servos have integrated the CANopen protocol and launched various CANopen slave servos; companies making frequency converters have integrated the CANopen protocol and launched various CANopen slave frequency converters; even manufacturers of stepper motors have launched CANopen protocol-based slave drivers. For example, BECKOFF’s CANopen PLC master/slave; a certain Taiwanese company’s CANopen WeChat Public Account: Industrial Control Sharing PLC master and frequency converter slave; a famous American company’s CANopen PLC master/slave; of course, there are also the SMC606 CANopen master/slave I/O and the CANopen protocol-based L6C series slave servos and DM3C series stepper slaves from Leadshine. In short, Leadshine can provide a full range of CANopen bus products from master to slave, open loop to closed loop.
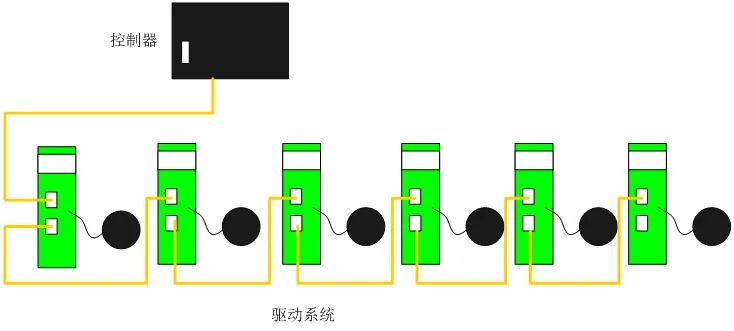
1. Production line applications with high axis and I/O requirements;
2. Applications for distributed sites over long distances;
3. Applications with multiple axes in a single machine, such as electronic devices;
4. Multi-joint robot applications.
5. WeChat Public Account: Industrial Control Sharing
1. The speed of 1Mbit/S is fast compared to other protocols, but it also has distance requirements;
2. Although it saves wiring, if one node fails, the entire network will be disrupted;
3. The stability of most domestic products still does not meet customer requirements.
1. When networking, choose shielded cables and connectors, or simply select those provided by manufacturers specializing in industrial buses;
2. When there are many axes, do not forget to choose terminal resistors for the end axes;
3. Try to select master and slave devices from the same company for easier debugging and maintenance.
Source: Leadshine
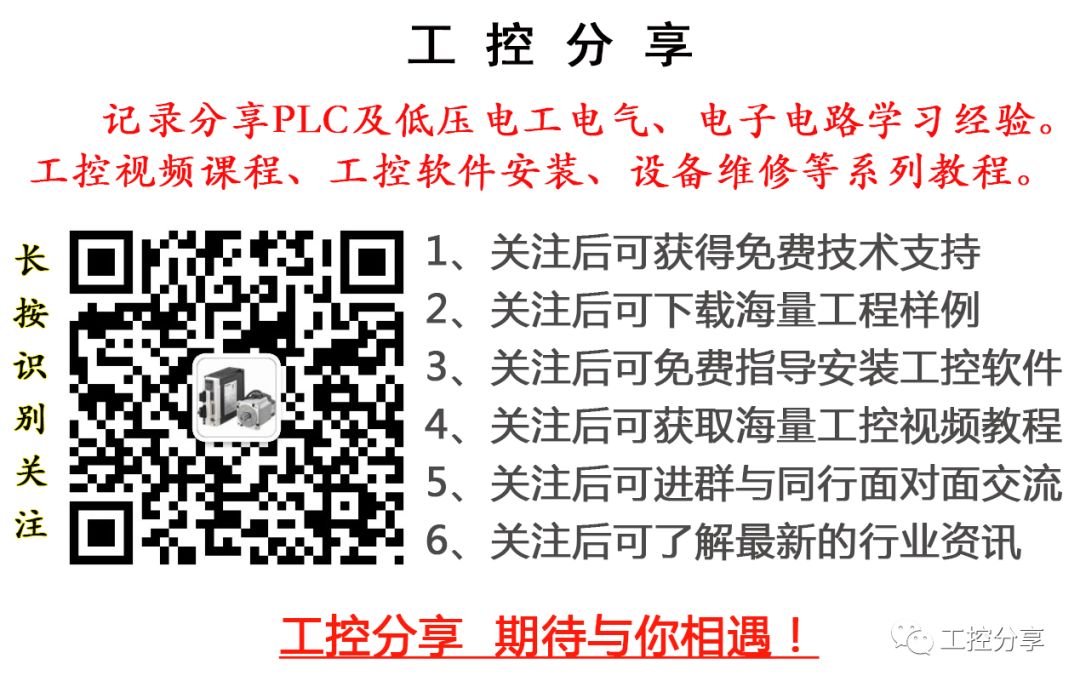