When discussing expectations for the future intelligent world, the Internet of Things (IoT) is undoubtedly one of the standard answers.
While the vision is promising, achieving it is not easy, especially in industrial production processes, where “connectivity” means achieving higher interoperability, flexibility, and seamlessness.
To achieve this goal, we need to eliminate the data communication barriers in the Industrial Internet of Things (IIoT).
Once network integration is achieved, intelligent manufacturing can thrive.
However, there are still questions in practical operation: How can we solve the compatibility issues caused by different interface protocols in traditional industries? What requirements do massive data transmission and analysis impose on hardware architecture?
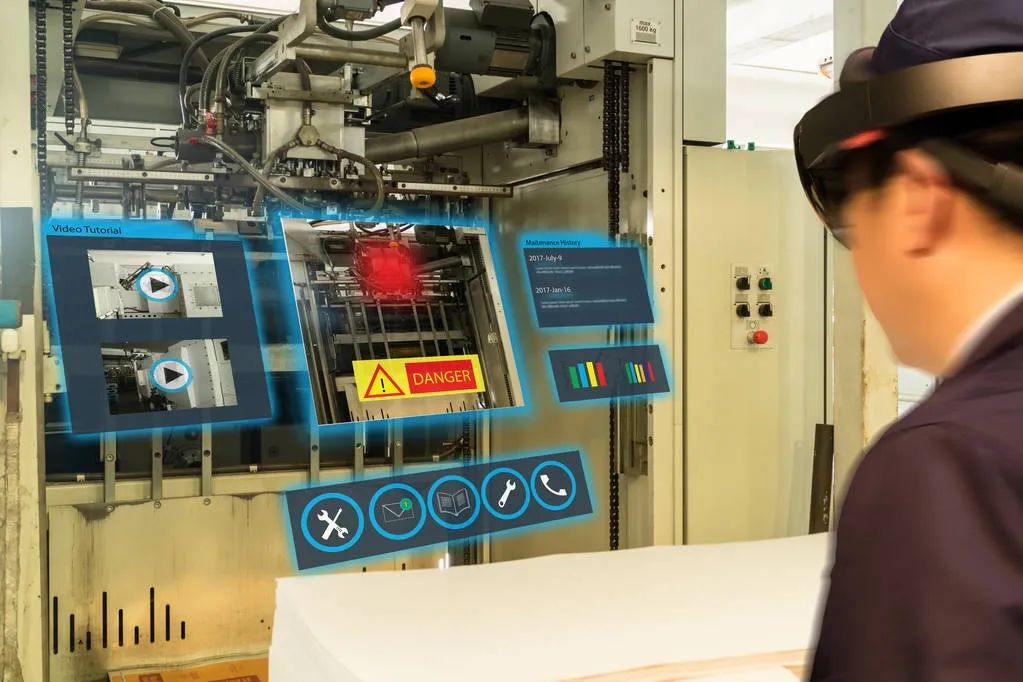
01
Solving Communication Barriers
What is the most suitable network for the Industrial Internet of Things?
The birth of IIoT technology is aimed at helping to solve the interconnection and data integration issues of production equipment.
For instance, Foxconn Industrial Internet (hereinafter referred to as “Industrial FII”), which has focused on intelligent manufacturing for many years, has been able to deploy a wealth of control, sensing, and data collection devices at the edge of production lines, thus providing effective data support for AI applications such as defect detection and predictive analysis.
However, data communication still faces two major gaps that need to be crossed:
First, the compatibility issues caused by different interface protocols in traditional industrial OT (Operational Technology) systems, such as buses and industrial Ethernet, often require complex protocol conversions to connect devices from different manufacturers on the production line;
Second, OT systems are often separated from IT (Information Technology) systems, leading to data isolation between the two.
Take the defective product detection system as an example. If data congestion, network delays, and other reasons prevent precise synchronization between the OT system (robot arm control, production line adjustments) and the IT system (high-definition image acquisition, transmission, and analysis), it may result in the robot arm or production line being unable to respond accurately based on detection results, thereby failing to effectively reduce the defect rate of products.
To address this, Shenzhen Zhuoxin Chuangchi Technology Co., Ltd. (hereinafter referred to as “Zhuoxin Chuangchi”) has chosen to leverage TSN (Time-Sensitive Networking) to help Industrial FII factories effectively tackle this issue.
TSN networks are precisely the “network” suitable for IIoT, and their characteristics can bridge the gaps.
First, as an open protocol standard (IEEE 802.1), TSN networks can eliminate compatibility issues between devices from different manufacturers, and their powerful open standards can further empower the Industrial Internet of Things;
At the same time, TSN networks break down the boundaries between control systems and analysis systems in traditional manufacturing production lines, making it easier to deploy AI applications on the production front line.
02
Intel Provides the Hardware Power Engine
TSN Networks Achieve AI Acceleration
However, the deployment of new solutions still faces many challenges. In addition to increased operational complexity, a more important consideration is how to choose the right hardware infrastructure to fully leverage the advantages of TSN networks.
When dealing with heavy traffic loads, TSN networks require operations such as timing, scheduling, synchronization, forwarding, queuing, seamless redundancy, and flow reservation for massive data, which fundamentally ensures system control of end-to-end latency, accelerates message transmission, and thus achieves high-speed communication.
Therefore, processors, Ethernet controllers, etc., also need to have workload integration and data acceleration capabilities, while I/O flexibility and functional safety must also meet the needs of the manufacturing industry.
Driven by these demands, Zhuoxin Chuangchi has introduced a series of products based on Intel architecture, creating a new solution that helps Industrial FII further enhance the efficiency of implementing anomaly detection and predictive analysis in factories through good support for TSN networks.
As shown in the figure above, CNC machines often encounter abnormal situations such as tool breakage and misalignment during the processing. By installing various sensors at key locations such as the tool holder, spindle, and power supply, the new solution can use data collectors for real-time data collection, uploading it to a Programmable Automation Controller (PAC),which then performs rapid inference based on algorithm models and responds to abnormal situations with corresponding reverse control, forming a closed-loop network for anomaly detection.
The PAC device plays a core role in the entire solution: it is responsible for data collection, preprocessing, model inference, etc., and also needs to control devices such as robot arms in real time based on AI inference results.
At the same time, for TSN networks to function, providing guarantees for time-sensitive traffic also requires PAC devices to have the capability to handle configuration information parsing, status information reporting, clock synchronization, and IP data frame fragmentation and reassembly tasks.
To empower PAC devices with strong performance, Zhuoxin Chuangchi has chosen Intel Core processors as their power engine in the solution. The 11th generation Core processors not only meet the requirements for low-latency deterministic computing in high-speed data preprocessing and AI model inference with the third-generation 10nm microarchitecture and higher single-thread/multi-thread performance but have also been specially optimized for harsh environments such as production lines.
More importantly, for TSN networks, all Core processors have integrated Intel® Time Coordinated Computing (Intel® TCC) technology to minimize network or system latency, meeting the manufacturing industry’s demands for critical real-time computing applications.
03
Promoting the Integration of Industrial OT and IT Systems
Unlocking Data Potential
A basic fact that intelligent manufacturing must recognize is that it must start from interconnecting OT infrastructure and normalizing data to tackle it from the bottom up.
Thanks to the excellent performance of hardware products based on Intel architecture, TSN network solutions can effectively promote the integration of industrial OT and IT systems, ensuring that the Industrial Internet of Things can maintain high-efficiency data transmission while also considering industrial-grade robustness and reliability.
By deploying IoT devices on the production front line and leveraging the efficient transmission capabilities provided by TSN networks, effective control can be achieved when anomalies occur on the production line, and predictive analysis using AI methods can be utilized to forecast equipment usage.
In some scenarios, the new solution has improved the good product rate of Industrial FII’s production line by about 8% through the collection and analysis of temperature or pressure data.
In some cases, issues such as network congestion, data packet loss, or retransmission caused by excessive data volume, which previously resulted in data transmission efficiency below 90%, have been effectively controlled after adopting the new solution based on TSN networks, with data transmission efficiency increasing to over 99%.
With the concept of driving intelligent manufacturing development through data insights, the accelerated deployment of IoT devices and the increasing demand for massive data transmission and analysis are bound to usher in a new wave of intelligent transformation in the manufacturing industry.
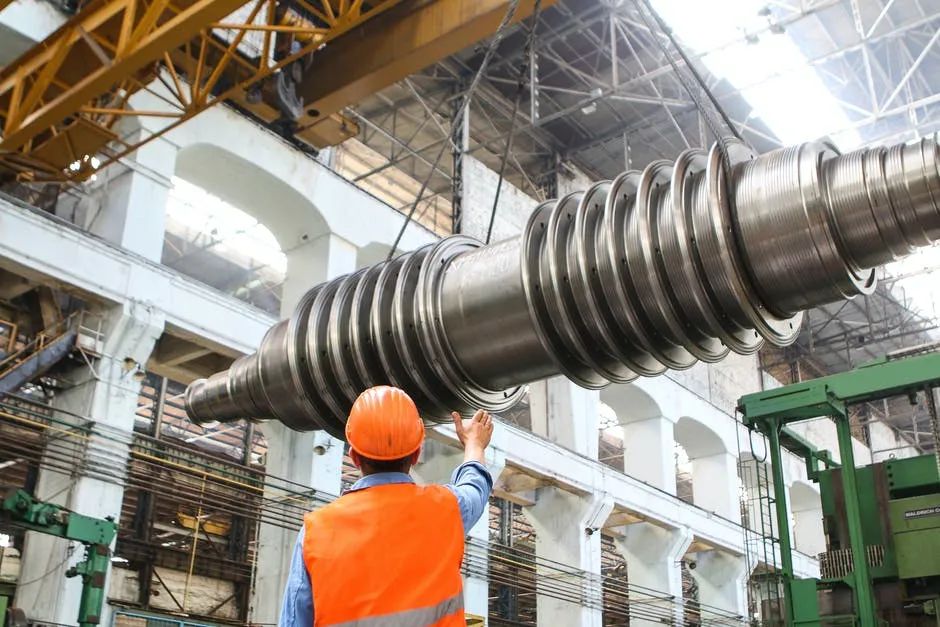
To empower innovation in intelligent manufacturing, Intel has launched a series of chip products, software solutions, and reference solutions to promote the integration of IT and OT, laying the foundation for the digital transformation of the manufacturing industry.
In the era of the Internet of Things:
Whether it is the selection of “things” — devices,
or “connect” — methods of interconnection,
or “network” — communication transmission.
Every aspect requires finding the right technical support to efficiently unleash data potential.
Click the “Read Original” button below to learn more