
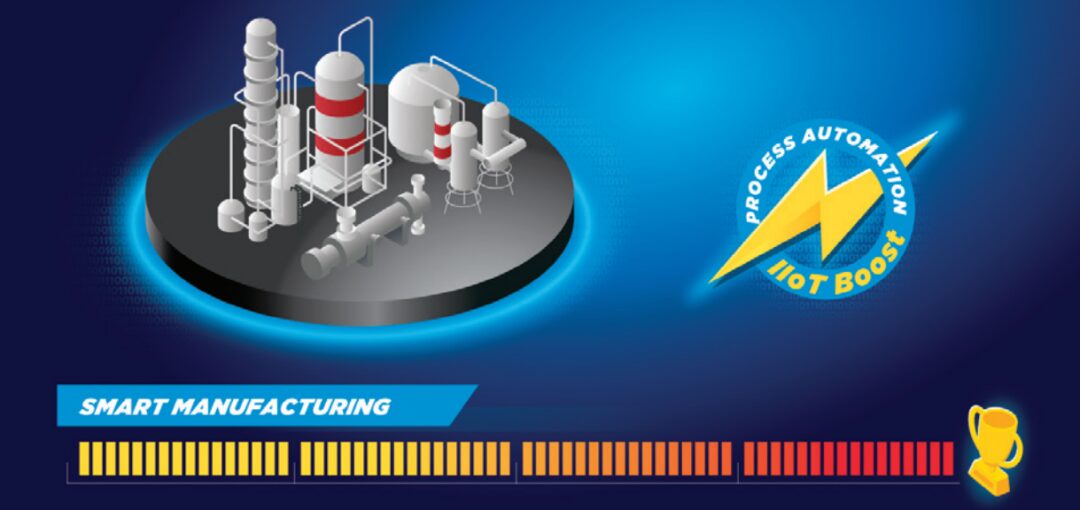
Image source: MAVERICK Technologies
Author: John Clemons
The Industrial Internet of Things (IIoT) is best suited for extending the capabilities of process control and automation systems while allowing them to operate as designed.
In recent years, the Internet of Things (IoT) has developed rapidly, connecting billions of devices and hundreds of millions of people, collecting and sharing vast amounts of data. It uses the internet to connect everyday physical objects. Of course, these physical objects must be embedded with sensors, processing power, software, and other technologies to enable them to connect and communicate over the internet.
When the IoT is used for industrial and manufacturing applications, it is referred to as the Industrial Internet of Things (IIoT). Like the IoT, IIoT connects devices and people, collecting and sharing vast amounts of data. It also enables intelligent and autonomous machines to communicate with each other and with higher-level systems such as Manufacturing Execution Systems (MES) or Enterprise Resource Planning (ERP).
IIoT has almost become synonymous with smart manufacturing and Industry 4.0. While smart manufacturing encompasses much more than IIoT, IIoT has become the foundational technology for nearly all smart manufacturing applications.
Contrary to some opinions, IIoT is not intended to replace traditional process control and automation systems. Process control and automation will always require real-time, closed-loop, standardized control of manufacturing processes—something that is not the design intent of IIoT.
IIoT is best used to extend the capabilities of process control and automation systems. It provides additional functionality that these systems do not often offer while still allowing them to complete their tasks as designed. The idea is to allow process control and automation systems and IIoT to do what they do best, enhancing automation and control systems in the following five ways.
1
Production Monitoring with Real-Time Contextual Information
Process control and automation systems always include real-time production monitoring, but it is typically localized, focusing on specific equipment, device operations, and production lines. With IIoT, it is possible to collect and share vast amounts of data from process control and automation systems, providing a broader real-time view of production operations.
For example, production schedules can be compared to actual production. Orders can be tracked based on production batches. The speed of machines and production lines can be monitored and linked to product timelines. Waste and rework can be tracked and associated with orders and batches. Quality results can be collected in real-time and matched with batches.
Product inventory can also be viewed based on batches and orders. Manufacturing key performance indicators (KPIs) such as quality, cost, and delivery can be monitored based on schedules, orders, and batches. All of this can be accomplished without interfering with the process control and automation systems.
2
Asset Performance Tracking for a Comprehensive View of Manufacturing Status
Process control and automation also include real-time asset performance tracking, but it is similarly localized and focused on specific assets, work centers, device operations, and production lines. Now, with IIoT using data from process control and automation systems, MES, and ERP, it is possible to elevate asset performance to a higher level.
Performance of assets, work centers, device operations, and production lines can be measured using many key performance indicators. Some of the most common KPIs include availability, performance, quality, overall equipment efficiency (OEE), mean time to repair (MTTR), and mean time between failures (MTBF). They can also be associated with orders, operations, and batches across the entire manufacturing operation. These KPIs can also be mapped to maintenance and cleaning activities, even to individuals and crews.
This enables broader analysis of asset performance against factors that have a greater impact on performance. It can also delve deeper into the root causes of underperforming assets. It relies on data from automation and control systems and combines it with data from other sources to provide a more reliable view of assets and their performance.
3
Equipment Maintenance with Deeper Analysis
Process control and automation systems typically do not directly involve equipment maintenance. However, they often collect vast amounts of equipment data that Enterprise Asset Management (EAM) systems or Computerized Maintenance Management Systems (CMMS) use in condition-based maintenance programs. IIoT does not directly involve equipment maintenance but relies on the aforementioned management systems to do their work.
The expanded capabilities of IIoT can better connect these systems and provide greater visibility into asset maintenance. Condition-based maintenance (CBM) alerts can be implemented using IIoT. Maintenance activities can be linked to production schedules and associated with specific orders, operations, batches, and quality results. By analyzing multiple batches before and after repairs, a deeper analysis of the impact on individual batches can be conducted.
Costs of failures can also be analyzed based on more parameters and KPI metrics. More detailed analysis can be conducted on preventive maintenance, postponement, or even cancellation of maintenance and their actual impacts on key KPIs such as cost, on-time delivery, and customer satisfaction.
The analytics portion in automation systems is typically about various charts of key manufacturing parameters like pressure, temperature, flow, and speed. With IIoT, analytics is no longer just a few charts or graphs of key data but includes descriptive, diagnostic, predictive, and prescriptive data using data from a very wide range of sources.
This allows these analytics to map manufacturing data based on customers, inventory, orders, schedules, maintenance, costs, labor, and other data. It provides a better overall view of operational performance, allowing for analysis of actual time to market, cost changes, material variations, quality trends, customer satisfaction trends, supplier quality, and supply chain performance.
4
Item Identification: RFID and Barcode Integration
Barcodes and Radio Frequency Identification (RFID) are two of the most common identification technologies in manufacturing operations. Process control and automation systems often use barcode and RFID readers as part of their automation activities, but the scope of these activities is often limited.
IIoT extends the use of barcodes and RFID and integrates them with process control and automation systems. This allows barcodes and RFID to be applied across multiple aspects of manufacturing operations, such as managing raw materials and packaging materials inventory, work-in-progress inventory throughout the plant, and finished goods inventory.
It also allows for more widespread application of barcode and RFID technologies throughout manufacturing operations, supporting traceability of materials used at each step of the process. With IIoT, barcode and RFID technologies can collect and share product, material, work-in-progress, location, and movement data while supporting real-time management of these materials.
5
Continuous Improvement: Aggregation of Product and Process Data
All manufacturing operations have a continuous improvement process. Lean manufacturing and Six Sigma are two common improvement processes. Process control and automation systems support these continuous improvement processes by providing them with data about manufacturing activities.
IIoT elevates this to a new level by aggregating product data and process data (including data from process control and automation systems, MES, and ERP systems, as well as data from many other systems) into the right hands. This is precisely what is needed as part of the continuous improvement process to identify issues, analyze root causes, implement necessary improvements, and then confirm the effectiveness of those improvements.
IIoT is a Complement to Manufacturing Processes
Process control and automation systems will continue to exist; they are not going away and are needed to provide real-time closed-loop regulatory control of manufacturing processes. IIoT is a complement to these processes, not a means to replace them.
IIoT extends the capabilities of process control and automation systems, providing them with additional functionalities, using their data in new ways, and combining it with data from many other sources. It offers some functionalities beyond process control and automation systems while still allowing these systems to do what they do best.
The synergy of process control and automation systems working together with IIoT is greater than the sum of the parts working independently. IIoT is a multiplier that, together with process control and automation systems, provides capabilities beyond what either could provide alone.
Key Concepts:
■ While smart manufacturing encompasses much more than IIoT, IIoT has become the foundational technology for nearly all smart manufacturing applications.
■ IIoT extends the capabilities of process control and automation systems, providing them with additional functionalities and enabling new uses of their data.
Consider This:
In what ways does IIoT impact your facility the most?
– END –
Source: Control Engineering China, 2022, September, Technical Article