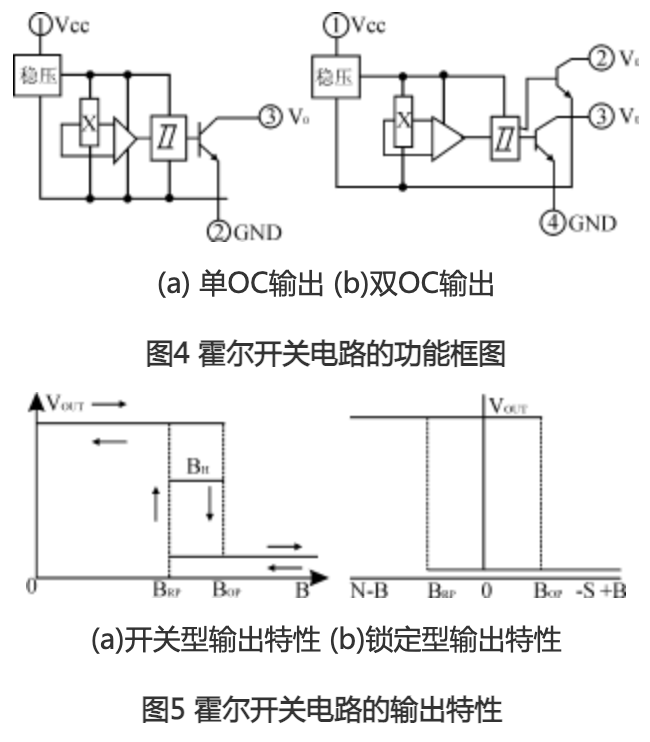
Directly reproduced from: Electric Control Knowledge Transporter, content sourced from the internet, copyright belongs to the original author.
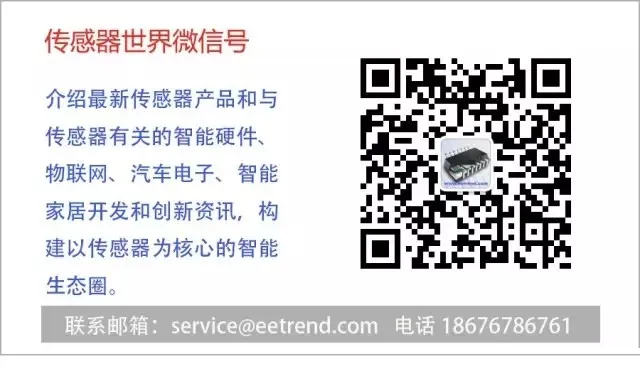
Directly reproduced from: Electric Control Knowledge Transporter, content sourced from the internet, copyright belongs to the original author.