👆If you wish to meet often,
Welcome to star 🌟 and collect it~
High-frequency communication has driven the development of dielectric materials, which need to have minimal signal delay or loss, as well as high power and long-term stability under extreme conditions. Although polyimide (PI) has many advantages, its dielectric constant (3.1-3.8) and dielectric loss are relatively high, which does not meet the demands of high-frequency communication. Although introducing air through a porous strategy (such as electrospun PI nanofiber membranes) can achieve a better dielectric constant, porous PI structures often have defects such as low dielectric strength, high dielectric loss, and poor tensile strength. In particular, the inherent hydrophilicity of PI poses challenges in maintaining stable dielectric performance in humid or submerged environments. Therefore, obtaining PI dielectric materials with excellent overall performance remains a significant challenge.
Recently, Professor Fu Yaqin’s team from Zhejiang Sci-Tech University published their latest research findings in the journal “Composites Science and Technology” titled “Electrospinning-impregnation: Producing hydrophobic polyimide composites with superior dielectric properties.” By immersing electrospun nanofiber membranes (PIfm) in polyamic acid (PAA) solution and undergoing secondary thermal imidization, PIfm/PI composites were formed. The dielectric constant (1.756) and dielectric loss (0.004) of these PIfm/PI composites are extremely low, with excellent dielectric strength (226.47 kV/mm) and a relatively high tensile strength (40.3 MPa). These excellent properties stem from the unique microstructure of the composites, which contains compression-rebound interactions that suppress γ-relaxation and dipole polarization in PI. Additionally, the PIfm/PI composites exhibit excellent thermal performance (5% decomposition temperature above 560°C), a suitable linear thermal expansion coefficient (approximately 50 ppm/℃), and outstanding hydrophobic properties (contact angle 108°-132°), maintaining relatively stable dielectric performance even in humid environments, which will greatly promote the advancement of PI nanofiber composites in high-frequency applications.

The impregnated PAA solution can be evenly distributed within the fiber network of PIfm, forming a “bridging” structure with the fibers after imidization. Figure 1 illustrates the preparation process of the PIfm/PI composite film. This process not only reduces the internal defects of PIfm at the microscopic level but also significantly improves the mechanical properties and dielectric strength of the fiber film at the macroscopic level, greatly enhancing the practicality of ultra-low dielectric fiber films.
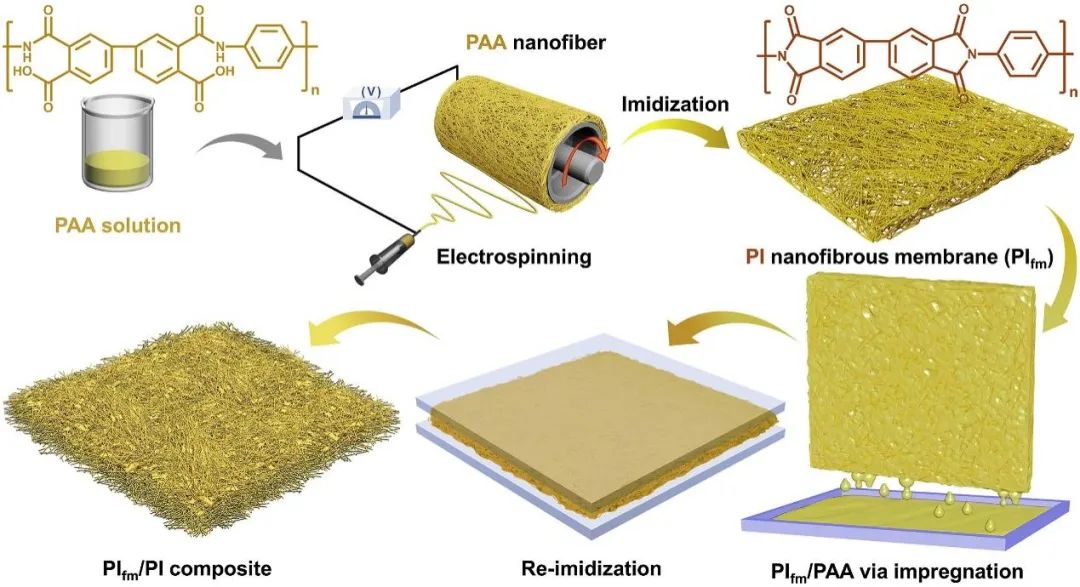
Figure 1. Schematic diagram of the preparation process of PIfm/PI composite film
From the scanning electron microscope (SEM) images in Figure 2, it can be seen that as the concentration of the PAA solution increases, the surface pores of the composite material gradually fill, and the PI nanofibers become tighter and more twisted, forming a more uniform interfacial structure, with a significant reduction in the surface pores of the PIfm/PI composite film. The viscosity of the PAA impregnating solution continues to increase and its volume continues to shrink, causing some PI fibers to shrink, which creates more bridging sites between the contracted parts of the PI fibers and the impregnated cured PI matrix, helping to enhance the mechanical properties of the fiber composite film.
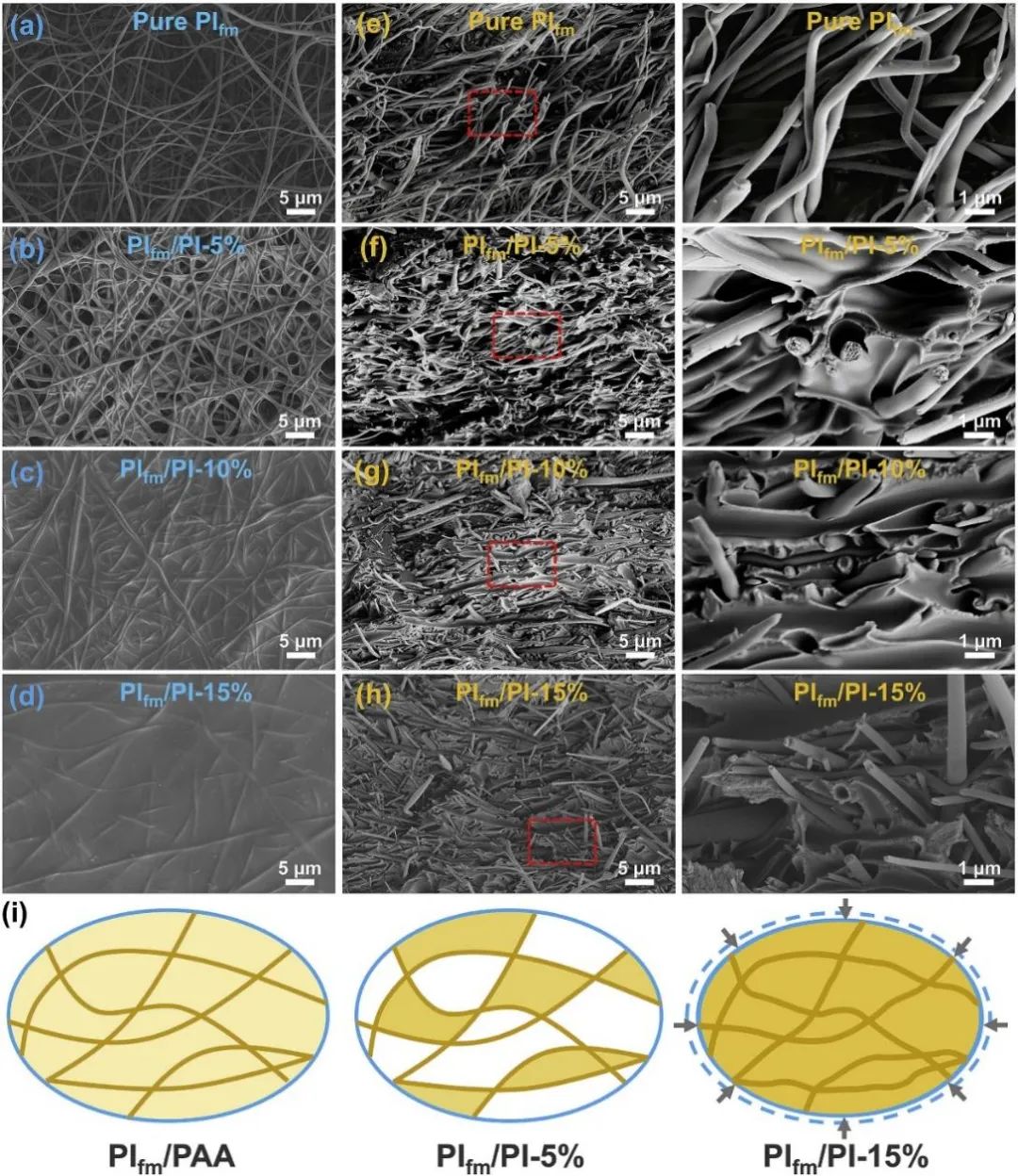
Figure 2. (a-d) SEM images of the surface of PIfm/PI composites. (e-h) Cross-sectional SEM images of PIfm/PI composites, using pure PIfm fiber film as a reference. (i) Schematic diagram of the microstructure of PIfm/PI composites when using different concentrations of PAA solution for impregnation.
In particular, the impregnation process can effectively suppress the polarization of the PI molecular chains on the fiber surface, enhancing the stability of the dielectric constant of the PIfm/PI composite film and reducing the dielectric loss under high-frequency conditions. As shown in Figure 3, the dielectric constants of all composites remain at ultra-low values (<1.8), and are far lower than that of pure PI films across the entire X-band. As the PAA concentration increases from 5 wt% to 15 wt%, the dielectric loss of the PIfm/PI composites significantly decreases from 0.042 to 0.004, and maintains ultra-low loss characteristics (<0.005) below 11.4 GHz, fully meeting the low loss requirements of high-frequency circuits. Furthermore, this fluorine-free (F) hydrophobic PI composite material possesses excellent thermal stability and sufficient mechanical strength, making it highly advantageous for practical applications in high-frequency communications.
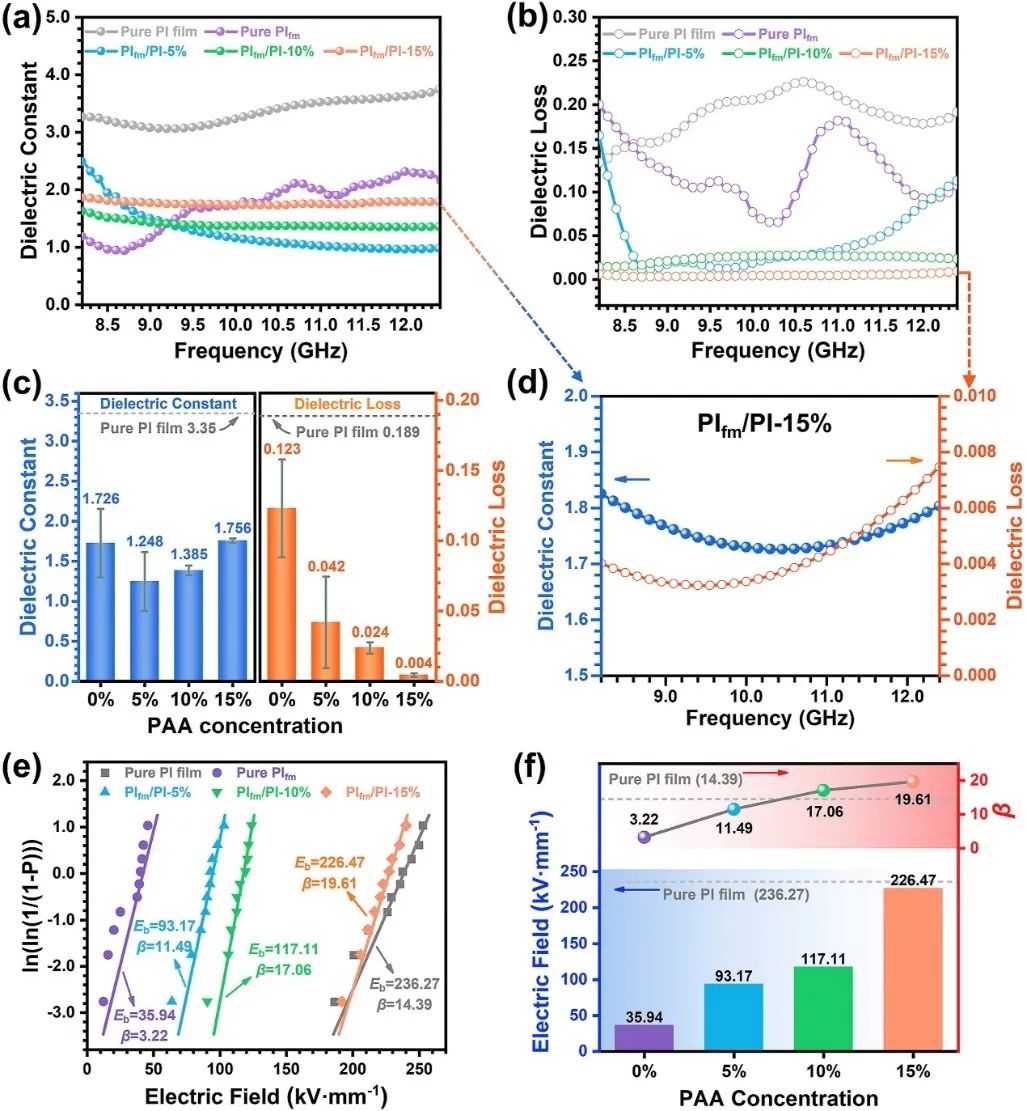
Figure 3. (a) Dielectric constant, (b) Dielectric loss, (c) Statistical dielectric constant and dielectric loss of PIfm/PI composites in the X-band. (d) Dielectric constant and dielectric loss curve of PIfm/PI-15% composites. (e) Weibull distribution of breakdown strength. (f) Characteristic breakdown strength and Weibull parameters.
The high hydrophobicity of PIfm/PI composites comes from the excellent hydrophobicity of pure PIfm. The PIfm/PI composite film maintains hydrophobic characteristics above 100° without introducing F elements, as shown in Figure 4. More importantly, after being treated in an environment with a relative humidity of up to 90% for 24 hours, its average dielectric constant in the X-band remains below 3.0 even without any drying treatment, and continues to quickly recover the dielectric loss to 0.007 after another 24 hours under a relative humidity of 40%. This composite film’s good hydrophobicity can greatly enhance its practical value in IC devices.
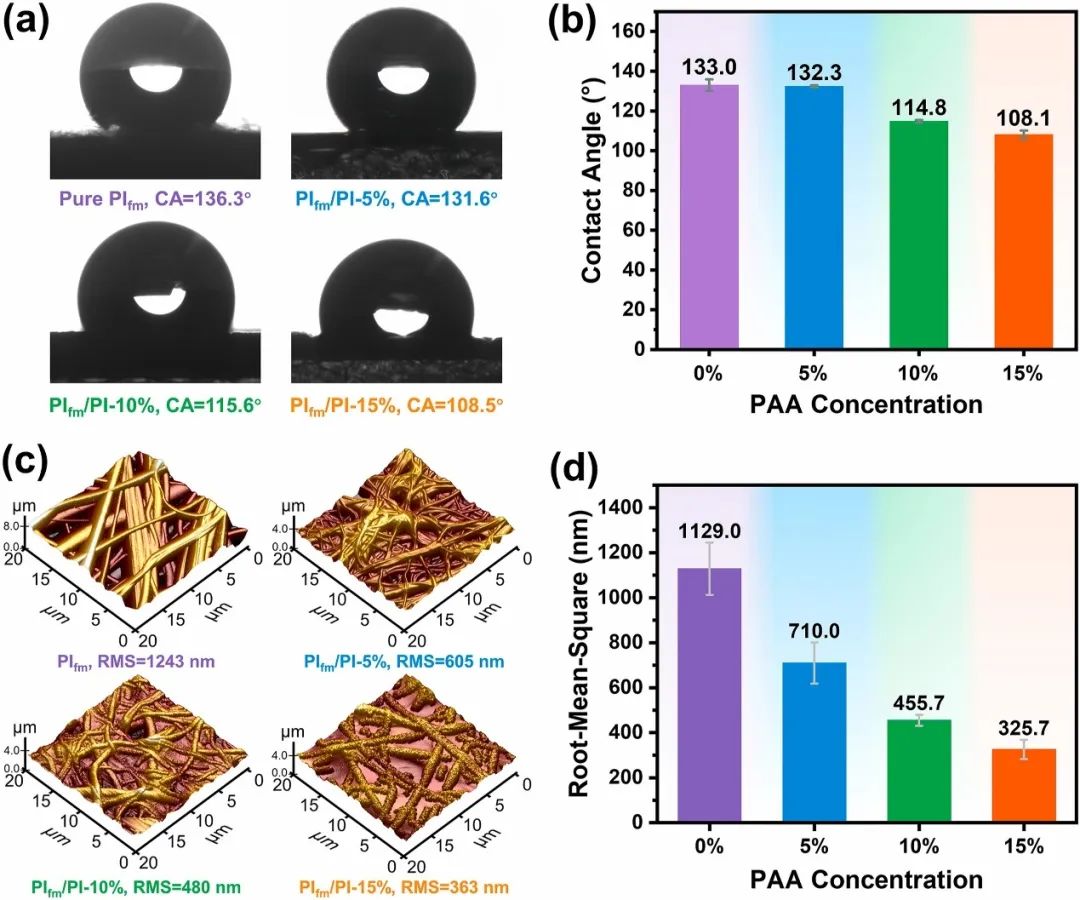
Figure 4. (a) Surface contact angle. (b) Surface contact angle statistics. (c) AFM images. (d) RMS roughness of PIfm and PIfm/PI composites.
Paper Link: https://doi.org/10.1016/j.compscitech.2024.111016
50-day free sharing link (valid until 2025.2.9):
https://authors.elsevier.com/a/1kIrvyZzL47xq
Profile
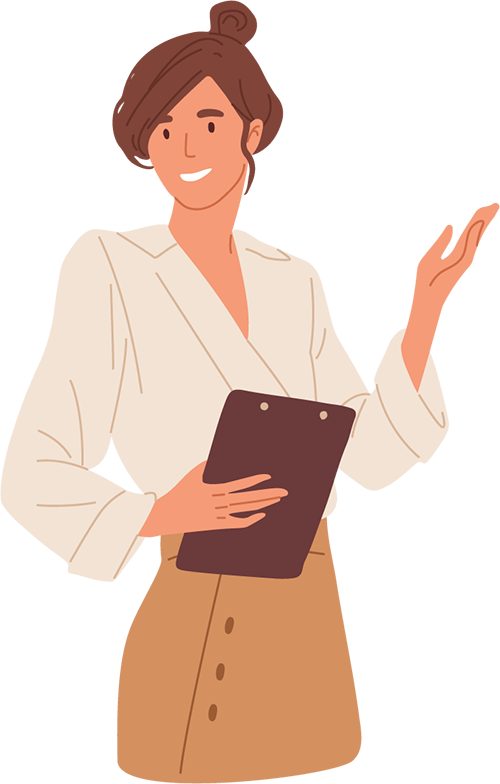
Si Yinsong
Ph.D., Associate Professor, Master’s Supervisor, mainly researching the preparation and thermal protection applications of electrospun inorganic nanofiber membranes, the synthesis and application of bionic porous microspheres, and the photocatalytic hydrogen production performance of graphitic carbon nitride. He has presided over one project each from the National Fund, Zhejiang Provincial Fund, and the Textile Light Applied Basic Research, and has published over 30 SCI papers (including 1 ESI highly cited paper and 1 cover paper) in journals such as Chem Soc Rev, Compos Part B, Compos Sci Technol, Chem Mater, J Mater Chem A, ACS Appl Mater Interfaces, Langmuir, Colloid Surface A. He holds 8 authorized invention patents. He serves as a guest editor for the journal Polymers, a member of the special advisory group, guest editor for the journal Catalysts, and reviewer for several domestic and international journals. He has participated in obtaining one second prize for scientific and technological progress from the China Textile Federation, two first prizes for teaching achievements, and one gold award for excellent patents.
Recently, Professor Fu Yaqin’s team has published a series of research papers on polyimide materials:
1) Composites Science and Technology, 2024, 249: 110508;
2) ACS Applied Materials & Interfaces 2024 16 (44), 61004-61015;
3) Journal of Applied Polymer Science, 2024, 141(40): e56025;
4) Polymer Composites, 2024, 45(10): 9530-9542;
5) Macromolecular Rapid Communications, 2023, 44(12): 2200956;
6) European Polymer Journal, 2023, 112543;
7) Composites Part B: Engineering, 2023, 254: 110542).
In the future, the team will continue to conduct in-depth research on the practical applications of polyimide materials in the field of high-frequency communication.
Breaking News
Yisibang Electrospinning Laboratory, top industry collaboration, full technical support, cutting-edge equipment one-stop experience. Facing technical challenges or innovation bottlenecks? We offer one-on-one answers and invite you to explore new realms of “electrospinning technology” together!
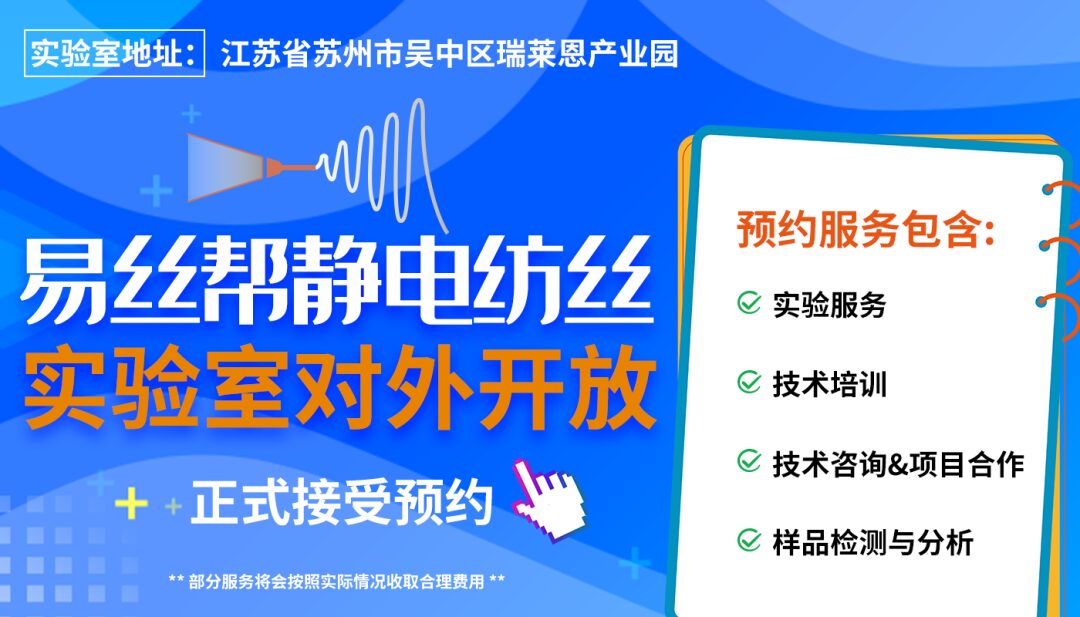
Click to view image details
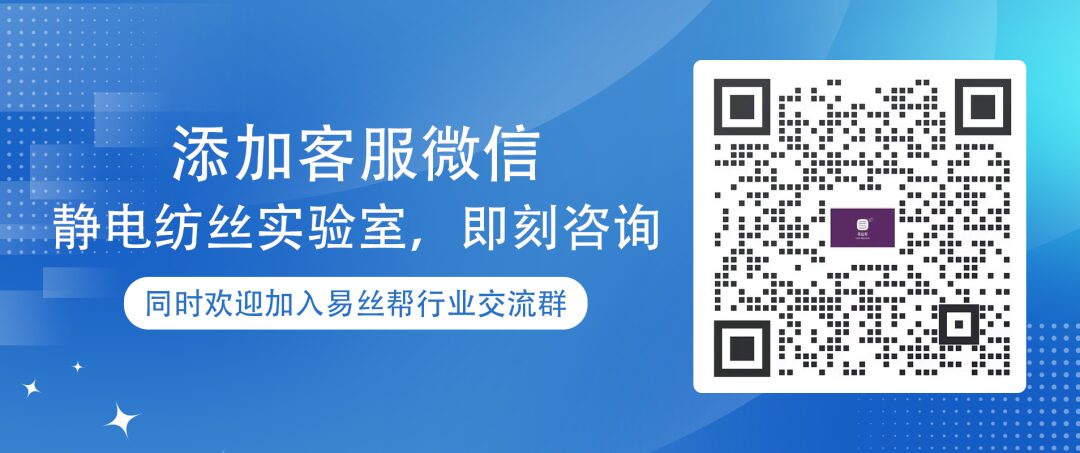