
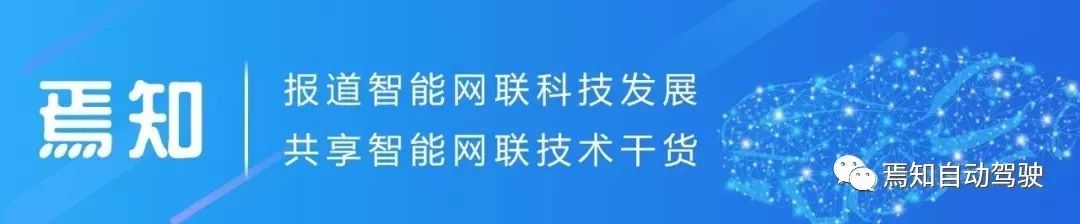
Source | Ab宝1990
Knowledge Circle | Add WeChat 13636581676 to join the “Electronic and Electrical Architecture Community”, note “Architecture”

Resolution is basically linearly related to the camera’s pixel count. To determine if a camera has high resolution, the most important factor is the number of pixels, typically in the millions.
Older reversing cameras had 300,000 pixels, which produced very blurry images. Nowadays, whether for front DVRs, rearview cameras, or 360-degree surround cameras, most start at 1,000,000 pixels. The Tesla Model 3 uses three CMOS image sensors with a resolution of 1280 x 960 pixels (1.2 million pixels), supplied by ON Semiconductor’s subsidiary, Aptina. The images captured are used for the Tesla Model 3’s driver assistance and autonomous driving control module.
Some might say that smartphones have cameras with tens of millions of pixels, so why don’t vehicle cameras have this capability? It’s not that they can’t; rather, smartphones require high-quality cameras to produce images akin to those from DSLRs, hence the high pixel count and direct MIPI transmission to the main control unit.
In contrast, in-vehicle cameras primarily capture images for machine use, such as for autonomous driving or driving monitoring. A camera with 1,000,000 pixels is sufficient for the data needs of machines, and while more data increases processing power, it doesn’t necessarily enhance autonomous driving performance.
Additionally, the signals from in-vehicle cameras require a serializer for transmission, which currently cannot handle tens of millions of pixel chips. Transmitting 2K video is already quite good, and the vehicle’s main unit needs to process 8-10 cameras. If each camera had tens of millions of pixels, the processing difficulty and costs would increase. Therefore, in-vehicle cameras are not about competing for pixel count like smartphones; the ability to process images is far more crucial.
Resolution testing is generally conducted using a standard resolution chart, which provides actual vertical and horizontal resolution values for auxiliary testing.
Resolution testing employs the international standard ISO12233 resolution chart, using a uniform shooting angle and environment. The resolution is calculated using HYRes software, separating vertical and horizontal resolution.
It can be simply understood as taking a picture of the card at a standard distance with the camera, and then using software to read the values captured by the camera. The software can directly obtain the center and surrounding resolution values. If the software is not purchased, one can also manually read the values, but this method can have significant errors due to human eyesight factors.
For a 2,000,000 pixel camera, the center resolution should be ≥800 lines, and the surrounding resolution should be ≥700.

Sensitivity is measured at a color temperature of 32,000K and an illuminance of 2000LUX shining on a gray card with a reflectance of 89-90%. The required aperture index F is determined when the image level reaches a specified value; the larger the F value, the higher the sensitivity.
The higher the sensitivity, the lower the minimum illuminance required, and the better the camera quality. If the illuminance is too low or too high, the image captured by the camera will degrade. Low illuminance may cause inertia trailing, while high illuminance may cause blooming effects in the image.

Camera Signal-to-Noise Ratio
The signal-to-noise ratio refers to the ratio of signal voltage to noise voltage, usually denoted as S/N. It can be divided into luminance S/N and chrominance S/N.
When the camera captures bright scenes, the displayed image is usually clear, and the observer may not easily notice noise interference. However, when capturing darker scenes, the displayed image can appear dim, making it easy for the observer to see snow-like interference noise. The higher the camera’s signal-to-noise ratio, the lesser the impact of interference noise on the image.
An acceptable signal-to-noise ratio for in-vehicle use is 40db, and when it reaches 55db, noise is almost undetectable.

Introduction to Camera Image Processing ISP
Let’s take a look at the key parameters of in-vehicle camera modules. Some aspects, such as white balance, automatic gain control, and color reproduction, have not yet been addressed. The above camera descriptions pertain to the main control, and there is a key component that needs explanation: the Image Signal Processor (ISP), which handles various image processing tasks.
The diagram below illustrates the basic components of the vehicle system: the yellow arrows represent data transmission, while the blue arrows represent control signal transmission.
The image processing flow of the camera is roughly as follows:
After the camera senses the charge, it converts it into a digital signal for each pixel, which we can call a Bayer pattern. Once the Bayer pattern enters the ISP, a series of image processing steps are performed to create an image that can be previewed or captured.
Key steps in image processing include white balance adjustment, as the human eye corrects the perceived colors. For example, under yellow light, white paper appears less white. Therefore, correcting white balance is crucial, followed by demosaicing to restore all color channels for each pixel.
Each sensor’s characteristics or color shifts due to various reasons need to be corrected through matrix multiplication for color correction. Afterward, it needs to be converted to the YCbCr domain for noise reduction or compensation targeting the luminance or color channels. Overall, this is a very simplified flow; in vehicle applications, the process is much more complex, involving HDR multi-frame exposure, synthesis, tone mapping, and other algorithms.
The placement of the ISP is very critical:
Some may place the ISP image processing chip at the camera end, transmitting processed signals to the main unit, while others do not place the ISP chip, allowing the main unit’s built-in ISP chip to handle image processing. This can significantly improve heat dissipation and reduce radiation.
For instance, in reversing cameras, the distance from the camera to the main unit is typically 5-8 meters, depending on the vehicle length. This part usually places the ISP at the camera module end, ensuring that the transmitted signals are processed and noise-reduced by the ISP, enhancing anti-interference capability. The downside is that this increases the size and heat dissipation requirements.
In contrast, for some DVR cameras, the distance to the control CPU is very close, and there are high design requirements, so the ISP is placed at the CPU side (many DVR CPUs have built-in ISP chips), which is the optimal solution in terms of both cost and design.
1、https://mp.weixin.qq.com/s/RVIOlT_Yr5GmpNQ12mfBFQ
2、https://mp.weixin.qq.com/s/y1CCWyG8pJ8tONZTiiYXfw
3、https://mp.weixin.qq.com/s/ZZX6NyGKTpC8awscJV6PFg
4、https://mp.weixin.qq.com/s/bQ_-FJbxDr-h9tYw1G1KZA
5、https://mp.weixin.qq.com/s/GfJ_u81VoxgE4BCAYm4IOQ
6、https://mp.weixin.qq.com/s/ewmX5qFkidvL8z21SE8DFg
7、https://mp.weixin.qq.com/s/XRZ197HIiYDuBF55MaNsog
8、https://mp.weixin.qq.com/s/YS_2agnfZl6Otm6tvGy_7A
9、https://mp.weixin.qq.com/s/2E0aQeb_9BFAvbVlu-tdIg
10、https://mp.weixin.qq.com/s/bxubsR_8orap8GRsUB1xHQ
11、https://mp.weixin.qq.com/s/eNjbHZaaaa2YRt_X0Ke1pw
12、https://mp.weixin.qq.com/s/oq_fMnMMlF0HC_J5VJ-xUQ
13、https://mp.weixin.qq.com/s/iA1cOzz5tLiUREQIaNsNXw
14、https://mp.weixin.qq.com/s/XWpwgZ_nlx7pjewVtjckWQ
15、https://mp.weixin.qq.com/s/FiW0S6PRjdFWW8eeCiJWxQ
