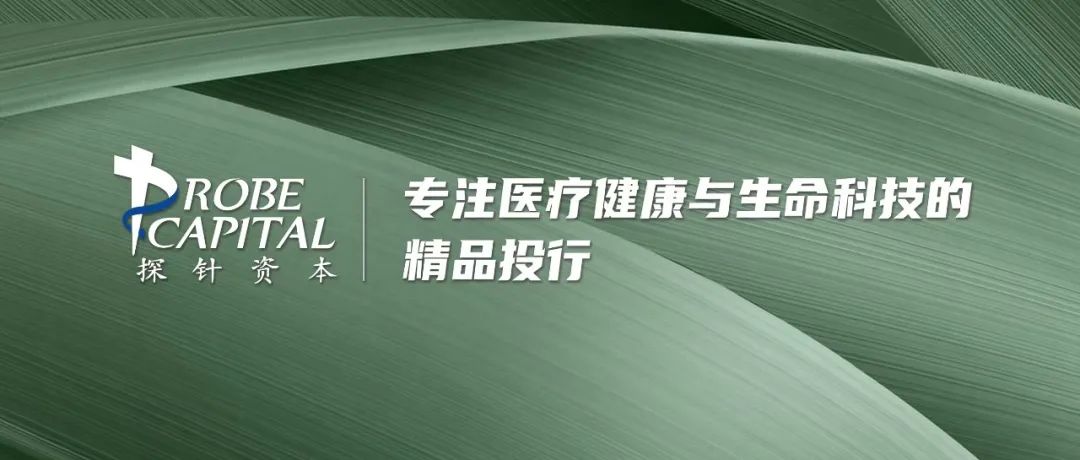
Table of Contents
“Medical Robots“
Table of Contents
1. Overview of Medical Robots
1.1 Definition and Classification of Medical Robots
1.2 Market and Industry Growth of Medical Robots
1.3 Analysis of the Medical Robot Industry Chain
2. Analysis of Core Components of Medical Robots
2.1 Servo Systems
2.2 Reducers
2.3 Sensors
2.4 Controllers
2.5 Navigation Systems (Magnetic Navigation, Ultrasound Probes, Optical, etc.)
2.6 Other Medical Devices (e.g., Ultrasound Scalpel)
3. Analysis of Medical Robots in Various Midstream Segments of the Industry Chain
3.1 Orthopedic Robots
3.2 Abdominal Robots
3.3 Neurosurgery Robots
3.4 Vascular Intervention Robots
3.5 Puncture Robots
3.6 Consumer Medical Robots
3.7 Rehabilitation Robots
3.8 Capsule Robots
3.9 Medical Service Robots
4. Analysis of Hospitals in the Downstream of the Industry Chain
4.1 Pricing and Medical Insurance for Robot Products in Various Provinces
4.2 Usage of Robots in Various Hospitals
5. Analysis of Major Companies
5.1 Foreign Companies
5.2 Domestic Listed Companies
5.3 Domestic Non-Listed Companies
6. Probe Capital’s Perspective
Note: Due to the length of this research, it is published in multiple parts; this is the second part.
Part One: Probe Capital Industry Research: Medical Robots (1)
3. Analysis of Medical Robots in Various Midstream Segments of the Industry Chain
3.1 Orthopedic Robots
3.1.1 Definition and Overview, Including Application Scenarios
3.1.1.1 Overview of Orthopedic Robots
Orthopedic robots refer to medical devices that are operated by strictly trained surgeons during orthopedic surgeries, capable of executing surgical plans set by the surgeons. Orthopedic surgery is a typical hard tissue operation, characterized by a wide variety of surgical techniques and extensive clinical needs, involving complex bone and muscle tissues in the human musculoskeletal system. Due to the complex structure of the skeletal system, which is adjacent to important blood vessels and nerves, the precision of positioning and operation is of utmost importance.
Orthopedic surgical robots are applied to hard tissues in the human body and can be considered rigid bodies in physics. Hence, orthopedic surgical robots may also be referred to as “hard tissue operation robots,” which gives robotic technology a natural advantage in clinical applications in this field. The entry of robots into orthopedics can be traced back to the 1980s, demonstrating good clinical practicality and significantly enhancing surgical precision, reducing surgical trauma, and alleviating the workload on surgeons.
Advantages of orthopedic surgical robots. Traditional orthopedic surgeries primarily rely on the surgeon’s experience and intraoperative imaging scans, which can lead to low surgical precision, high risks, significant trauma, and slow recovery. In contrast, orthopedic robots utilize high-precision imaging navigation systems to optimize surgical path planning and implement these paths through highly flexible robotic arms, achieving minimally invasive orthopedic surgeries. This results in increased surgical success rates, reduced trauma, and lower radiation exposure for surgeons. Specifically, the advantages are as follows: First, orthopedic robots can accurately reach the lesion according to the surgical plan set by the surgeon. Second, orthopedic robots often require only a few tiny incisions to perform surgeries, significantly reducing patient blood loss and radiation exposure. Third, the “arms” of orthopedic robots exhibit high stability, allowing surgeons to operate more steadily and naturally. Fourth, orthopedic robots accelerate postoperative recovery, reduce hospital stays and complications, and prevent patients from feeling self-conscious due to long scars post-surgery.
3.1.1.2 Application Scenarios of Orthopedic Robots
Application scenarios of orthopedic surgical robots. According to the existing classification methods for orthopedic surgeries, orthopedic surgical robots can be divided into joint orthopedic, trauma orthopedic, and spine surgery robots.
(1) Joint Replacement Robots
Joint orthopedic surgical robots are the first to achieve technological and commercial applications, primarily used for treating osteoarthritis. When the pain caused by osteoarthritis progresses to a point where painkillers are ineffective and joint activity is restricted, artificial joint replacement surgery becomes the primary treatment method.
In 1986, the Integrated Surgical Systems company, established by the IBM Thomas J. Watson Research Center and the University of California, Davis, developed the RoboDoc orthopedic surgical robot system (Figure a), which received FDA approval in 2008. RoboDoc is based on a horizontal joint-type serial robot structure combined with end-effectors, capable of performing knee and hip joint replacement surgeries; it can also perform autonomous surgical operations based on preoperative 3D planning and intraoperative navigation, assisting in bone shaping, prosthesis positioning, and implantation.
In 1997, the German company Orto Maquet developed the CASPAR robot system (Figure b), which uses an industrial robot structure and includes anterior cruciate ligament repair procedures, functioning similarly to RoboDoc. However, issues related to safety, surgical efficiency, and preparation time have limited the promotion and application of this system.
In 2001, the Acrobot company’s AcroBot robot system in the UK completed clinical trials (Figure c). This system was developed by Imperial College London in 1992. AcroBot was the first to adopt an active constraint control method (Surgeon-guided) to perform surgical operations, reconstructing, segmenting, and planning surgeries based on preoperative 3D images; during surgery, it achieves positioning based on registration technology, mapping preoperative planning information to the surgical operation area, providing operational area constraints, and allowing surgeons to drag and perform bone shaping operations.
In 2013, global orthopedic medical technology giant Stryker acquired MAKO Surgical and its RIO joint surgical robot system (Figure d), which received FDA approval in 2015. The RIO robot system also employs an active constraint control method to perform joint resection surgeries. In its mechanical arm design, it emphasizes the compliance of human-machine interaction, featuring six degrees of freedom and a screw transmission structure design, achieving compliant interactive operation through balanced design across various degrees of freedom.
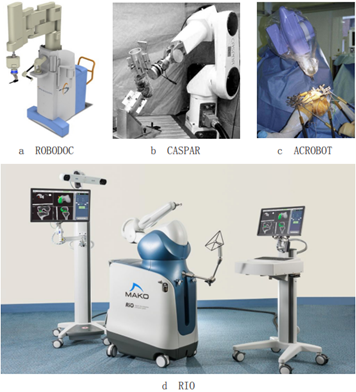
Four Types of Joint Replacement Surgical Robots
Image Source: Internet
(2) Spine Surgery Robots
Spine surgery robots are currently primarily used for pedicle screw fixation procedures. The robot utilizes medical imaging planning to achieve precise spatial positioning, autonomously completing or guiding surgeons in the drilling of implantation channels. The primary goal of spine surgical robots is to achieve precise, minimally invasive surgeries, minimizing the size of incisions during surgery and reducing the risk of nerve damage, maximizing the accuracy and safety of surgical operations.
The first clinically applied spine surgical robot was the Spine Assist robot system from Mazor Robotics in Israel (Figure a). This system features a 6-degree-of-freedom Stewart parallel mechanism, with a diameter of 50mm, height of 80mm, weight of 250g, and a repeat positioning accuracy of 0.01mm. Its lightweight and compact design allows the Spine Assist robot to be placed directly on the patient’s spine during surgical operations, unaffected by vertebral position changes. In 2004, Spine Assist received FDA and EU CE certifications, and in 2011 it was upgraded to the Renaissance system (Figure b), which can achieve intraoperative 2D and 3D navigation.
In 2016, Medtronic launched the Mazor X Stealth robot system (Figure c), which was acquired from the Israeli medical device company Mazor Robotics. The Mazor X Stealth system uses a serial robot structure to achieve navigation for pedicle screw implantation, offering higher system rigidity, shorter preparation time for surgical operations compared to the Spine Assist and Renaissance systems.
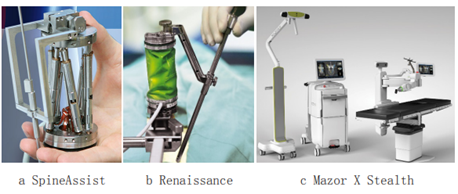
Three Types of Spine Surgery Robots
Image Source: Internet
Research on spine surgery robots in China started later, with the most representative robot systems being the spine surgical robot developed by Harbin Institute of Technology and the Tianzhi Navigation robot developed jointly by Jishuitan Hospital and Tianzhi Navigation Company. Other representative research institutions include the Shenzhen Institute of Advanced Technology, Chinese Academy of Sciences, and Beihang University.
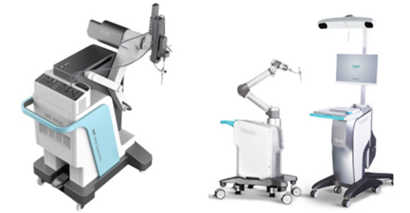
Spine Surgery Robots from Harbin Institute of Technology and Tianzhi Navigation
Image Source: Internet
(3) Trauma Orthopedic Surgical Robots
The trauma orthopedic surgical robot systems are mainly used for the reduction of long bone fractures, guided by medical imaging to perform reduction operations on fractured bones. They can be divided into serial and parallel types based on the robot structure, with representative foreign serial robots including the fracture reduction surgical robot systems developed by Hannover University in Germany and the University of Tokyo in Japan (Figures a and b).
Hannover University introduced the concept of remote operation, operating Staubli industrial robots through force feedback handles, combined with optical navigation systems and intraoperative 3D imaging acquisition C-arms to complete the registration of fractures. The robot-assisted fracture reduction system FRAC-Robo developed by the University of Tokyo employs a 6-degree-of-freedom serial robot with a force feedback device, fixing the foot and traction of the lower limb to complete the reduction of femoral shaft fractures.
In China, Harbin Institute of Technology developed a 6-PTRT parallel robot system for femoral shaft fracture reduction (Figure c) and established clinical reduction surgery protocols through human model and specimen experiments; Beihang University developed a dual-plane navigation robot system for femoral shaft fractures and conducted clinical application studies for intramedullary nail surgery of the tibia and femur, pelvic sacroiliac screw surgery, and femoral neck hollow screw surgery; the PLA General Hospital (301 Hospital) constructed a long bone fracture reduction robot system based on the Stewart platform (Figure e) and a general positioning robot system based on UR robotic arms, both of which adopted a strategy based on visual navigation and point cloud registration, completing model and specimen experiments.
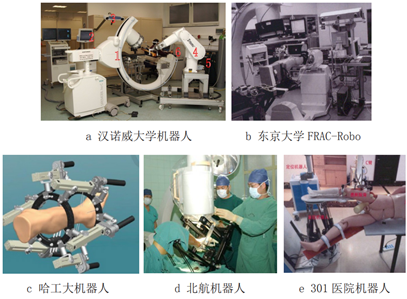
Five Types of Trauma Surgical Robots Image Source: Internet
3.1.1.3 Market Situation of Orthopedic Robots
Orthopedic robots are one of the more mature branches of surgical robots. According to data from the International Federation of Robotics in 2014, orthopedic surgical robots accounted for 23% of the total surgical robot market globally. According to Frost & Sullivan’s forecast, the orthopedic surgical robot industry began to rise in 2015, reaching $1.39 billion in 2020, and is expected to reach $4.69 billion by 2026, becoming the next widely used field after laparoscopic surgical robots.
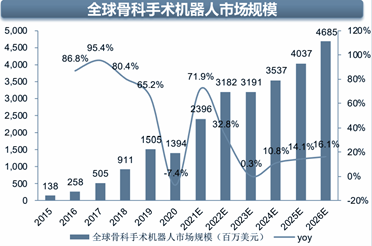
Global Market Size of Orthopedic Surgical Robots
Image Source: Frost & Sullivan, Tianzhi Navigation Prospectus
According to the Toubao Research Institute, based on factory prices, the market size of orthopedic surgical robots in China was $42.5 million in 2020. The orthopedic robot industry began large-scale industrialization around 2019, driven by China’s rapidly expanding elderly population and increasing incidence of orthopedic diseases. It is expected that from 2020 to 2026, the compound annual growth rate of the orthopedic robot market in China will be 48.2%, reaching $451 million by 2026, showing a rapid expansion trend.
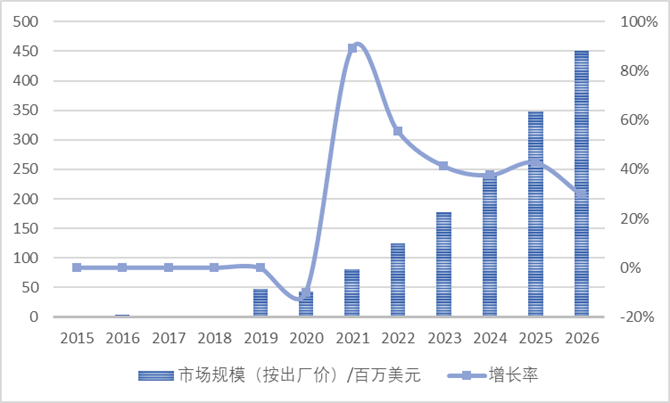
Market Size of Orthopedic Robots in China
Data Source: Toubao Research Institute, Probe Capital Compilation
The primary application scenario for orthopedic surgical robots is joint replacement surgery. In 2020, the global market size for joint replacement surgical robots was $730 million, accounting for 52% of the total orthopedic surgical robot share. In 2020, approximately 100,000 robot-assisted joint replacement surgeries were performed in the United States, with a penetration rate of 7.6%. In 2018, there were 439,000 artificial hip joint replacements and 249,000 total knee replacements in China, with significant room for improvement compared to the United States and OECD member countries. It is expected that the total number will exceed 3 million by 2030 (based on a compound growth rate of 15% from approximately 700,000 cases in 2018). In terms of penetration, robot-assisted joint replacement surgeries in China are just beginning. According to Frost & Sullivan data, there were only 243 robot-assisted joint replacement surgeries in China in 2020, with a penetration rate of 0.03%. It is expected that the number of surgeries will reach about 80,000 by 2026, with a penetration rate of 3%. Regarding installations, there were 17 joint replacement surgical robots installed in China in 2020, and this is expected to grow to 788 by 2026. The market size for joint replacement surgical robots in China was $14.8 million in 2020, and with the increase in the number of surgeries, installations, and penetration rates, it is expected to grow to $33 million by 2026.
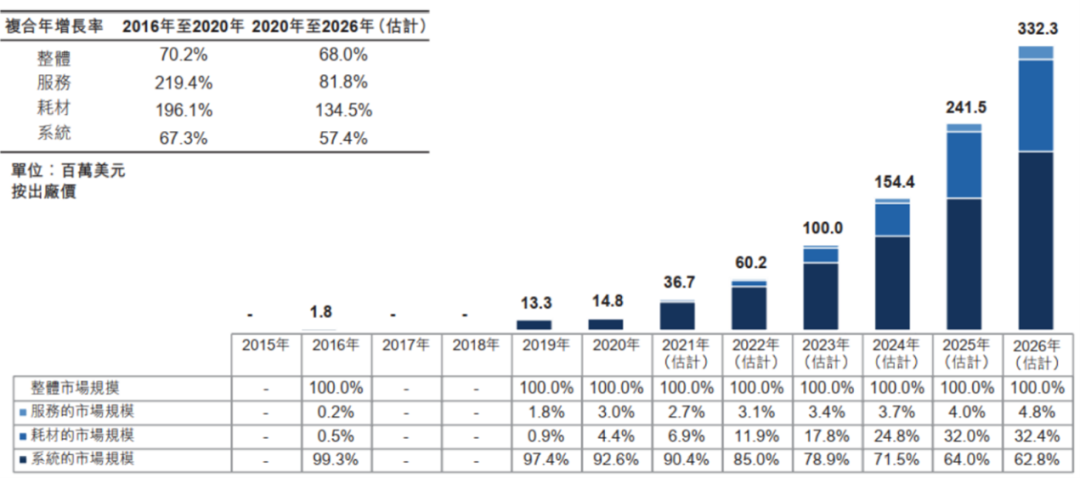
Market Size and Forecast of Joint Replacement Orthopedic Robots
Image Source: Frost & Sullivan
3.1.2 Major Technical Challenges
The robot-assisted orthopedic surgical system was proposed as a new orthopedic surgical solution as early as the last century. It uses computers to control and track the system states and robot movements. The aim is to achieve high precision and safety in orthopedic surgeries where surgical fields and paths are limited. For different surgical techniques, although the specific technical methods, surgical processes, and robot control methods used by orthopedic surgical robot systems differ, the basic design concepts of these systems share high similarities. As shown in Figure 5, in a typical robot-assisted orthopedic surgical system, virtual computer objects, navigation systems, and physical disease objects are three essential components, while imaging and planning technologies, navigation registration technologies, and target tracking technologies are several key technologies during the surgical process.
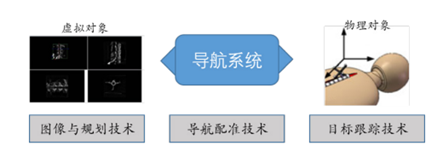
Key Technologies of Orthopedic Robots
Image Source: “Overview of the Development of Orthopedic Surgical Robot Technology”
(1) Imaging and Planning Technologies
One major advantage of robot-assisted orthopedic surgical systems compared to conventional surgical procedures is that surgeons can perform surgical planning on a relatively concrete computer virtual object, allowing the robot to complete part or all of the surgical operations. Most of the virtual objects mentioned above are derived from medical imaging data, which can be categorized into preoperative and intraoperative data based on time. Most orthopedic surgical robot systems use preoperative CT images to generate three-dimensional virtual objects, although there are some examples using MRI images.
Compared to MRI, CT images provide clearer contrasts between bone tissue and other soft tissues, resulting in higher image quality, but they also expose patients to higher radiation doses. Researchers generally recognize the limitations of preoperative images: the time gap between image acquisition and the actual surgery can lead to decreased surgical precision; thus, there has been increasing research on intraoperative images, including both 2D and 3D images.
In comparison to CT images, 2D transmission images obtained from C-arms have lower radiation doses, and navigation systems based on these virtual perspective images have been applied in many trauma orthopedic surgeries. However, due to the complexity of the registration methods, there are many practical issues in planning, especially for grinding surgeries such as laminectomy and joint replacement surgeries, where direct planning on these virtual perspective images is not feasible. To address these issues, a new type of intraoperative 3D imaging device has been developed, consisting of a motor and a C-arm, which can continuously acquire 50-100 2D perspective images within a certain timeframe and reconstruct a 3D CT dataset from them.
When planning using three-dimensional virtual objects, the surgical system generally needs to perform image segmentation and three-dimensional reconstruction display of the concerned tissues and anatomical structures to present the lesions in a more intuitive form. With the development of computer science, some methods based on machine learning and deep learning have been proposed, which can segment specific tissues or organs from medical images. For example, for cochlear implant surgeries, a research team at the University of Bern segmented the facial nerve from CT images and avoided dangerous areas during planning and surgery.
(2) Navigation Registration Technologies
The navigation system is the core part of orthopedic surgical robot systems, acting as the bridge connecting physical disease objects and computer virtual objects, converting the surgeon’s planning on the computer virtual object into the physical object coordinate system of the disease. This process is also referred to as navigation registration. In different orthopedic surgical robot systems, the registration methods vary due to different surgical methods and equipment.
The simplest registration method involves the surgeon selecting some anatomical landmarks on the virtual object and using a tracking probe to pick corresponding points on the physical disease object, allowing the computer to calculate the transformation relationship between the two. Although this mathematical solution is relatively simple, the consistency of the points selected by the surgeon on both objects may be low, potentially leading to low accuracy in registration results. If some artificial landmarks are implanted into the patient’s body, this problem can be effectively resolved, as these landmarks can be easily selected by the surgeon on both the virtual and physical objects. However, implanting landmarks in the patient’s body may pose additional risks of infection and discomfort, which is why these methods have not been widely promoted.
Additionally, some robotic systems utilize several X-ray images collected from different positions during surgery for registration. After image correction, these X-ray images are registered together to the 3D virtual object, referred to as 2D-3D registration. For example, in some systems, surgeons can complete planning tasks based solely on a few 2D perspective images, making it feasible to use several intraoperative X-ray images as virtual objects for registration.
Intraoperative ultrasound images have advantages such as real-time feedback and no radiation. Some researchers have utilized calibrated ultrasound devices in orthopedic surgical robot systems to obtain the morphology of bone tissue at the lesion site, thus achieving navigation registration. Specifically, ultrasound devices have two different tracking modes: amplitude-based A-mode and brightness-based B-mode. In A-mode, the surgeon must maintain the ultrasound probe perpendicular to the surface of the bone being measured, which can be challenging when soft tissue is too thick. Furthermore, the measurement accuracy depends on the speed of ultrasound waves in human tissues, which varies among patients, necessitating a significant amount of experimental data to support accurate measurements. Therefore, successful applications of navigation registration in A-mode are relatively rare. B-mode, on the other hand, can scan the tissue within a fan-shaped area, making it easier for surgeons to use, but this type of image is usually noisy and requires additional processing.
(3) Target Tracking Technologies
In some surgical systems, tracking devices are employed to monitor potential displacements or respiratory movements of patients during surgery. In some early orthopedic surgeries, tracking devices based on acoustics, magnetics, and mechanical methods were used. Nowadays, most orthopedic surgical systems utilize infrared-based active/passive tracking devices: the former uses LEDs that actively emit infrared light as tracking points, while the latter uses reflective balls as tracking points. By tracking these points and identifying specific geometric shapes, the tracker can obtain the transformation relationships among multiple coordinate systems. Furthermore, some researchers have extracted the positions of known geometric-shaped objects from video information, providing a simple alternative to infrared optical trackers.
The optical tracking devices mentioned above require an unobstructed line of sight between the tracker and the tracked point during surgery, necessitating adjustments by the surgeon during the procedure. To address this issue, electromagnetic tracking systems have been proposed, which utilize built-in magnetic field generators to create magnetic fields within the surgical area and measure the positions and attitudes of receiving coils placed within this magnetic field, thus achieving tracking without concerns about line-of-sight obstructions. However, since magnetic fields are easily disturbed, some metallic objects that may be used during surgery can significantly affect measurement accuracy.
Recently, inertial tracking devices have been successfully applied in some orthopedic surgeries, such as knee replacement, pedicle screw fixation, and periacetabular osteotomy. This method does not have issues with line-of-sight obstructions or electromagnetic interference, but it has lower positioning accuracy and more complex measurements.
3.1.3 Major Company Situations
The research and industrialization of orthopedic surgical robots originated in the 1990s, and after decades of development, the companies that have achieved industrialization in orthopedic surgical robots are concentrated in the United States, Israel, France, and China. Although China started later in the research of orthopedic surgical robots, some products have reached the level of similar international products in the next generation of orthopedic surgical robots.
The orthopedic robot field presents a competitive landscape. Companies that have laid out the orthopedic surgical robot track abroad include Stryker, Johnson & Johnson, Zimmer Biomet, Medtronic, and Smith & Nephew. In China, the development of orthopedic surgical robots is still in its early stages, with several companies entering the field recently, such as Tianzhi Navigation, MicroPort Medical, Weigao Group, Rosenbot, and Santan Medical. South Korea and Germany have also successfully developed robot prototypes in the spine and trauma fields and are actively pursuing commercialization.
(1) Stryker
Stryker (NYSE:SYK.N) is one of the largest orthopedic and medical technology companies globally, headquartered in Kalamazoo, Michigan, USA, with 14 production, research, and sales divisions worldwide and over 16,000 employees. Its products cover joint replacement, trauma, craniofacial, spine, surgical equipment, neurosurgery, ENT, interventional pain management, minimally invasive surgery, navigation surgery, intelligent operating rooms, and biomedical technology.
Due to its good performance, Stryker has been recognized as one of the Fortune 500 companies and one of the top 50 medical companies in the United States by Fortune magazine and Business Week.
On September 25, 2013, Stryker announced its acquisition of Mako Surgical and its robotic-assisted surgical technology for $1.65 billion. Mako Surgical, headquartered in Fort Lauderdale, Florida, includes the Rio robotic interactive orthopedic system and Restoris orthopedic implant series, and recently launched the Makoplasty total hip replacement system. The MAKO orthopedic robot received FDA approval in August 2015 and is a semi-active surgical robot that can be used for unicompartmental, total knee, and total hip replacement surgeries. It designs surgical plans based on preoperative CT scans and corrects them in real-time according to individualized models during surgery, preventing excessive manipulation through a tactile feedback system. Between 2015 and 2017, the Mako robot was used in 65 hospitals across the United States, the United Kingdom, Australia, and Germany, performing over 1,400 surgeries.
As of December 12, 2021, the market capitalization of SYK.N was $94.8 billion, with a revenue of $14.351 billion and a net profit of $1.6 billion in 2020.
(2) IBM
The International Business Machines Corporation, or IBM, is the largest information technology and business solutions company globally, founded in 1911 by Thomas Watson in Armonk, New York. IBM has over 310,000 employees and operates in over 160 countries and regions. Today, IBM’s innovative solutions flourish in important fields of concern for governments, businesses, and the public, including smart energy, smart transportation, smart healthcare, smart retail, and smart water resources, covering topics such as energy conservation, food safety, environmental protection, transportation, healthcare, modern services, software and services, cloud computing, and virtualization.
In 1986, IBM and the University of California, Davis, jointly developed an intelligent system for hip joint replacement surgery, which was FDA-approved. Based on this, Integrated Surgical Systems launched the active operation orthopedic surgical robot product RoboDoc in 1992 for assisting in joint replacement surgeries. Studies have shown that the effects of RoboDoc robotic surgeries can achieve levels comparable to traditional surgeries, providing unique advantages in preoperative planning software, OrthoDoc. However, issues such as system failures, long handling times for femoral shafts, and high complication rates have hindered the widespread use of this system.
As of December 12, 2021, the market capitalization of IBM.N was $114.3 billion, with a revenue of $73.6 billion and a net profit of $5.6 billion in 2020.
(3) Think Surgical
Think Surgical is headquartered in Fremont, California, and its TSolution One system is designed specifically for knee and hip joint replacement surgeries, approved for total hip surgeries in the United States and Europe. In December 2017, Think Surgical’s total knee surgery received CE Mark certification. Think Surgical is currently conducting IDE studies and hopes to obtain FDA approval. The TSolution One system aims to assist surgeons in developing personalized preoperative joint replacement plans using CT-based three-dimensional planning and an open implant library.
In 2019, American medical device manufacturer Think Surgical announced it had completed $134 million in financing to enhance its TSolution One robot-assisted orthopedic surgical equipment.
(4) Zimmer Biomet
Zimmer Biomet (NYSE:ZBH.N) is a global leader in musculoskeletal healthcare, helping patients with bone, joint, or supportive soft tissue diseases return to normal life. The company manufactures and sells medical products related to orthopedics, including biologics, dental implants, spine, craniofacial, and chest products, operating in over 25 countries and selling products in over 100 countries.
In July 2016, the cross-border medical investment fund Huichuan Capital Group announced the sale of its stake in Medtech to Zimmer Biomet. Medtech is a new surgical robot system developer headquartered in France, previously listed on the pan-European stock exchange. Its flagship products include the brain surgery robot (