Industrial Control Systems generally refer to several types of control systems, including Supervisory Control and Data Acquisition (SCADA) systems, Distributed Control Systems (DCS), and Programmable Logic Controllers (PLC) among other control systems.
01
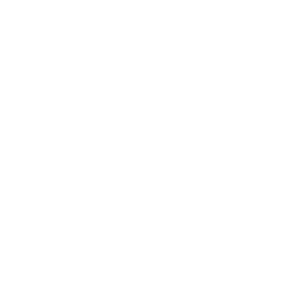
Five-Layer Architecture
The classic hierarchical model of industrial control systems in the international standard IEC62264-1 divides typical industrial control systems into five levels based on functionality, which are: Enterprise Resource Level (Decision Management Level), Production Management Level (Operational Management Level), Process Monitoring Level, Field Control Level, and Field Device Level (Physical Device Level).
The five-layer architecture is as follows:
-
L0 Physical Device Level: Composed of actuators, sensors, smart instruments, motors, and actuating devices, primarily responsible for converting various physical variables and electrical signals during the production process, collecting on-site production data, and executing control commands, forming the basis of digitalization in “smart manufacturing”.
-
L1 Field Control Level: Composed of DCS controllers, PLCs, and other devices with logical control functions, receiving data from the physical device layer (such as sensors, transmitters, or smart instruments), calculating the required control amount according to certain control strategies, and sending it back to on-site actuators (such as valves and motors). The operator stations and engineer stations at the field control level can simultaneously perform continuous control, sequential control, or logical control functions, achieving monitoring and control of field devices.
-
L2 Process Monitoring Level: Mainly composed of operator stations, engineer stations, OPC servers, SCADA systems, and DCS systems, centralized monitoring of production sites and production status, providing overall control of the enterprise’s production conditions.
-
L3 Production Operations Level: Mainly composed of MES, MIS systems, production command, operational scheduling, and office terminals, primarily achieving execution management of the production process (manufacturing data management, planning and scheduling management, production scheduling management, inventory management, quality management, work center/device management, tooling management, material management, production dashboard management, production process control, lower-level data integration analysis, upper-level data integration decomposition), recording data processing and production command scheduling.
-
L4 Decision Management Level: Mainly composed of ERP, CRM, procurement, portals, OA, Email, and office terminals, covering various information systems and information support systems of the enterprise, integrating various resources, combining and analyzing summarized data from various dimensions, providing operational decision support for the management operators of the group headquarters and its subsidiaries.
Next, let’s introduce industrial control systems. What is an industrial control system? It refers to an automatic control system composed of computers and industrial process control components, consisting of controllers, sensors, transmitters, actuators, and input/output interfaces. These components are connected through industrial communication lines according to certain communication protocols, forming an industrial production or processing system with automatic control capabilities.
It generally refers to several types of control systems, including Supervisory Control and Data Acquisition (SCADA) systems, Distributed Control Systems (DCS), and Programmable Logic Controllers (PLC) and other control systems.
02
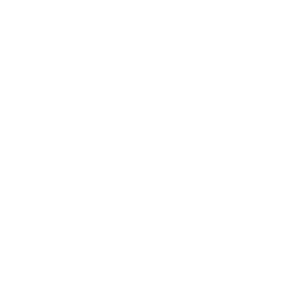
PLC
Coal Industry: In coal enterprises, the PLCs used mainly include brands like Siemens, AB, Mitsubishi, and Hengtong, primarily applied in transportation systems, coal selection systems, coal mining systems, etc.
Power Industry: In thermal power enterprises, PLC equipment is predominantly from brands like Siemens, Rockwell, and Schneider, mainly applied in auxiliary control facilities of thermal power; in wind power enterprises, the PLCs used mainly come from brands like Bafang, ABB, and Bachmann, primarily applied in the control of wind turbine motors.
Rail Transit Industry: In railway enterprises, the integration of industrial control systems is entirely undertaken by domestic manufacturers, and the main control systems are also mainly developed independently by domestic manufacturers, with key vendors including Casco, Tonghao Institute, Jiaotong University Micro-Link, Lanzhou Dacheng, and Iron Science Institute, mainly applied in centralized scheduling, traction power supply systems, etc.
Port Industry: In port enterprises, the PLC equipment used is primarily from Rockwell, mainly applied in tipping, transport belts, stackers, and loading processes.
Shipping Industry: In shipping enterprises, controllers from Kongsberg and SAM are mainly used in ship automation control systems.
Chemical Coal Industry: In coal chemical enterprises, the PLC equipment used mainly includes Honeywell, Siemens, AB, GE, and Schneider brands, applied in auxiliary control systems of coal chemical processes, such as coal selection, preparation, desulfurization, wastewater treatment, etc.
03
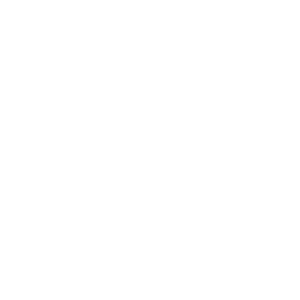
DCS System
DCS (Distributed Control System) implements real-time control of all devices, alarm management, collection and storage of historical data and events, report generation and storage, process operations, etc., mainly monitoring the DCS controllers and on-site processes in the field (production plant or workshop area). The field instrument signals are transmitted to the on-site cabinet room and the central control room, with data transmission commonly using cables or optical fibers. The DCS system uniformly processes these data, conducting all control, monitoring, alarms, and report operations in the central control room, as shown in the figure:
The DCS system is mainly used for continuous reaction process control, such as in power generation, chemical, and pharmaceutical industries. Foreign DCS products are mainly provided by vendors like FOXBORO, ABB, Emerson, Siemens, Honeywell, and Yokogawa, while domestic DCS products are mainly provided by Shanghai Xinhua, Hengtong, Zhejiang University Control, State Grid Zhishen, and Zhejiang Weisheng.
Power Industry: Mainly used for controlling the main and auxiliary machines of thermal power units in thermal power enterprises, with major brands including Siemens, ABB, Emerson, as well as domestic brands like State Grid Zhishen and Xinhua.
Chemical Coal Industry: Mainly applied in process control of coal chemical processes, with major brands including Honeywell, Hengtong, and GE Xinhua.
04
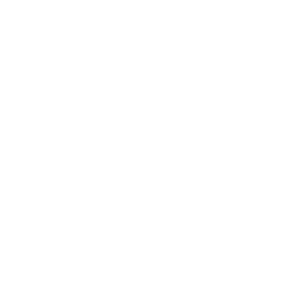
SCADA System
Coal Industry: The SCADA system in the coal mining sector is primarily used for its comprehensive automation monitoring, mainly using WinCC, IFix, Intouch, PSI, pSpace, etc., while also centrally monitoring systems such as power supply, transportation, ventilation, drainage, and coal selection.
Power Industry: In wind power enterprises, it is mainly used for unidirectional collection of data from the central monitoring layer of wind farms for statistical analysis; as a major subsystem of the Energy Management System (EMS), it has advantages such as complete information, improved efficiency, accurately grasping system operating status, accelerating decision-making, and helping quickly diagnose system fault states. The main SCADA system integrators include Goldwind, Xinjiang Goldwind Technology, State Grid Nanzhi, Siemens, Nari, and Suzlon Energy. Thermal power enterprises also have similar SCADA monitoring systems, such as the NCS system of power plant substations, with system integrators mainly being State Grid Nanzhi, Sifang Automation, etc.;
Rail Transit Industry: The traction power supply SCADA system is mainly used for remote monitoring of traction power supply equipment, with the main brand being Chengdu Jiaotong University Guangming Co., Ltd. Other systems, such as decentralized self-discipline scheduling centralized systems and vehicle operation monitoring systems, are similar to SCADA systems in terms of functions and attributes. The production and integration of related systems are primarily by domestic manufacturers.
Port Industry: The central control system of ports functions similarly to SCADA systems, mainly used for overall monitoring of the port’s automation systems, involving monitoring and controlling the status of transport belts and other individual machines.
Shipping Industry: In shipping enterprises, the ship’s engine room automation system is similar to SCADA systems, including engine room monitoring and alarm systems, main engine remote control systems, and ship power plant systems, with centralized monitoring of the engine room, main engine, and power plant conducted through a control room.
Chemical Coal Industry: The SCADA system is mainly applied in monitoring the power supply and distribution systems in coal chemical enterprises.
Two automation giants made the list: 2024 China Globalization TOP30
2024-12-01
Siemens, Schneider, Phoenix: Six Major Trends in Industrial Automation
2024-11-26
Control System, Hengtong, Yonyou, Huawei: 2024 China Industrial Software TOP50
2024-11-22
Siemens, Schneider, ABB, Mitsubishi Listed: Top 100 Electrical Industries in China
2024-11-19
87-Page Siemens Manufacturing MES-PLM-ERP Integrated Implementation Plan
2024-11-18
ABB, KUKA Four Giants vs. Inovance, Estun: Detailed Explanation of Industrial Robots/Gear Reduction Industry
2024-11-13
204-Page Solution for a Group’s MES/MOM Project Requirements
2024-10-26
Siemens, Schneider vs. Inovance, Control System: Major Players and Landscape in China’s Industrial Control (DCS\PLC\HMI)
2024-10-22
Inovance, Control System, Hengtong: Top 20 PLC Enterprises in China‼️
2024-10-23
This Industrial Control Giant is Number One Globally, Global Supply Chain TOP25, Siemens Ranked 16
2024-10-17