
Digital Signal Processor (DSP) is increasingly applied in the field of industrial automation. DSP is a technology specifically designed to convert and process analog signals into digital signals, enabling functions such as digital filtering, reconstruction, modulation, and demodulation, ensuring the precision and stability of signal processing. Especially in motor control systems, the application of DSP is crucial as it can precisely control the motor’s speed, position, and acceleration, making it an indispensable core component of modern automation control systems.
The motor control system is a combination of circuits and software that manages and controls the operation of electric motors, aiming to accurately adjust key parameters such as starting, stopping, speed, direction, and torque to achieve precise control over motor mechanisms. In this process, DSP technology plays a core role, not only enabling precise control of various motor parameters but also optimizing the overall performance of the motor. This control system is widely used in various fields such as industrial automation, robotics, automotive manufacturing, and household appliances, playing a vital role in ensuring the efficient and stable operation of equipment.
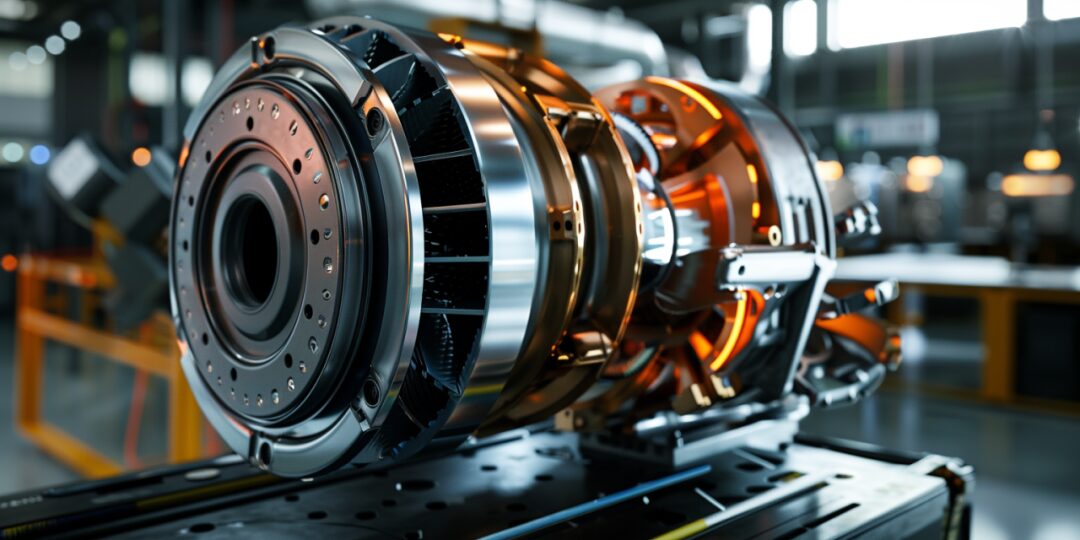
▲ Motor Schematic
Motor control algorithms and motor control software are key technologies that constitute the motor control system. Motor control algorithms are a set of programs used for real-time management and optimization of motor control systems, aimed at ensuring the motor operates according to the expected performance requirements. The DSP (Digital Signal Processor) technology can integrate various advanced algorithms into the motor control algorithms, achieving higher precision in motor control. Motor control software is the specific program used to implement motor control algorithms and process control; leveraging DSP technology can significantly enhance the execution efficiency and control accuracy of the software, thereby improving the performance and stability of the entire motor control system.
This article introduces a motor control system built on SkyEye, where the control core utilizes a DSP processor to execute the software program containing the control algorithms, achieving control based on the principle of FOC (Field-Oriented Control).
SkyEye, fully known as Tianmu All-Digital Real-Time Simulation Software, is a hardware behavioral-level simulation platform based on visual modeling, allowing users to perform behavioral-level simulation and modeling of hardware through a drag-and-drop method.
FOC is an advanced motor control technology particularly suitable for precise control of Permanent Magnet Synchronous Motors (PMSM) and Alternating Current Induction Motors (ACIM). This technology achieves performance close to that of DC motors for AC motors through complex coordinate transformations and independent control mechanisms, enabling high efficiency and precise control of the motors. The FOC control process mainly includes three-loop control: current loop, speed loop, and position loop, supplemented by various adjustment algorithms to complete the closed-loop control of the motor system.
The motor control system realized through all-digital real-time simulation technology can not only quickly and accurately simulate the motor’s operating state but also accelerate the testing and optimization process of control algorithms. This method breaks through the limitations of traditional physical motors and experimental sites, significantly reducing development costs and cycles while greatly enhancing system performance and reliability, providing strong support for the research and application of motor control technology, and promoting technological innovation and development.
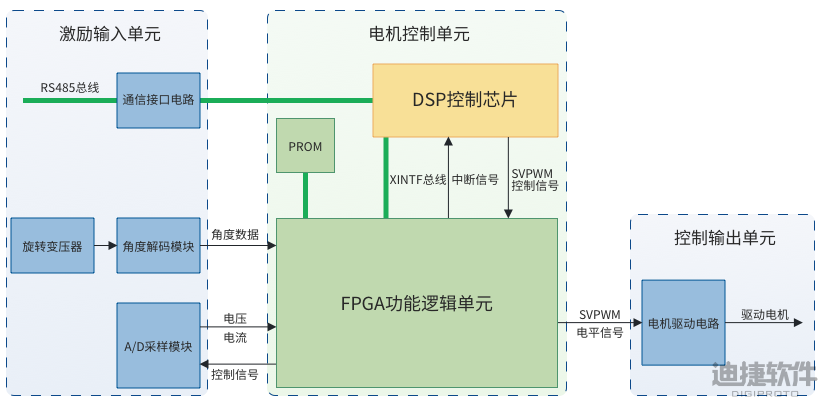
▲ Simulation Structure Diagram of Motor Control System Based on SkyEye
The motor control system built on SkyEye uses a DSP chip as the core, running motor control algorithms and logic programs. The entire simulation system consists of three parts: excitation input unit, motor control unit, and control output unit, working collaboratively.
The architecture of the motor control unit adopts a collaborative control mode of DSP control chip + FPGA functional logic unit. The FPGA (Field-Programmable Gate Array) model is realized through functional-level logical modeling and interacts with the DSP chip via the XINTF (Extended Internal Memory Interface) bus for data exchange, serving as peripheral functional devices. The DSP chip is equipped with necessary peripheral models and communication interface circuit models to ensure efficient communication with the outside world.
In the motor control unit, the DSP chip mainly undertakes the implementation of advanced control algorithms, such as position control, speed control, and current control. The DSP reads various motor state data collected by the FPGA, executes complex computational tasks, performs real-time PID (Proportional-Integral-Derivative) adjustment processing, and generates SvPWM (Space Vector Pulse Width Modulation) control signals required for the drive circuit, thereby achieving precise control over the entire motor system’s operating state.
The FPGA is primarily responsible for real-time data collection and preliminary processing, including angle data generated by the rotary transformer and angle modules, as well as current data received from the A/D (Analog-to-Digital) sampling module. Using PROM (Programmable Read-Only Memory) models helps the FPGA achieve data storage, allowing preprocessed data to be stored in PROM and shared with the DSP via the XINTF bus. Meanwhile, the FPGA receives the SvPWM signals output by the DSP after calculations and converts them into control level signals required for the drive circuit. This collaborative mode of division of labor enables the system to achieve high performance, high precision, and high reliability in control, ensuring the system’s real-time and stability.
The excitation input unit is mainly responsible for generating various excitation signals and data in the simulation system, including state excitations produced by the motor rotary transformer and A/D modules, as well as data excitations from the communication bus. By constructing a 485 bus model, it enables interaction and communication control with the outside world, facilitating real-time control of the motor system during simulation. It supports communication with upper-level control devices and allows interaction with upper computer testing and monitoring devices, facilitating external monitoring of the motor control system’s status.
RS-485 is a commonly used serial communication protocol, fully known as Recommended Standard 485, widely applied in industrial automation, building control, instrumentation, and intelligent transportation systems, particularly suitable for long-distance communication and environments with high anti-interference requirements.
During the simulation process, the motor control unit outputs control signals in real-time to the motor drive circuit, which is responsible for driving the motor. Each unit model works collaboratively to complete information collection and real-time feedback, achieving precise closed-loop control. Ultimately, the motor control system, supported by all-digital simulation technology, not only enhances system performance and reliability but also accelerates the validation and optimization of control algorithms, significantly shortening the development cycle and promoting innovation and development in motor control technology.
For more information related to SkyEye, please click here or visit www.digiproto.com for more details!
END
Recommended Reading
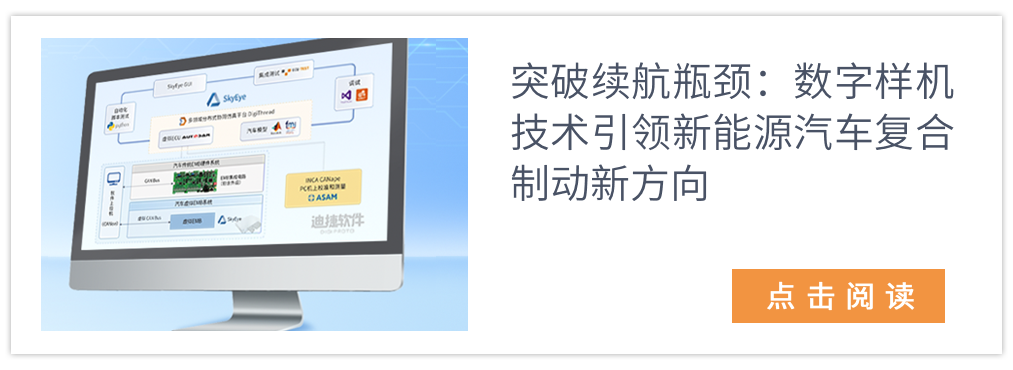
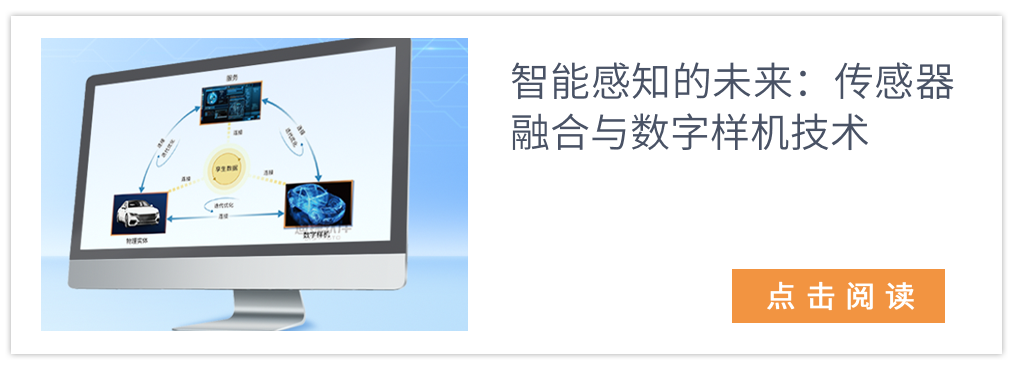
Product Introduction
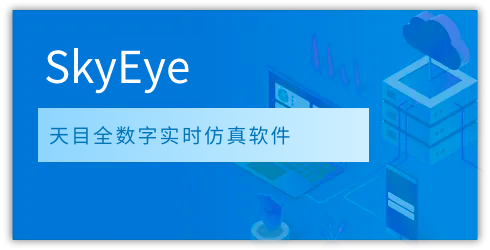

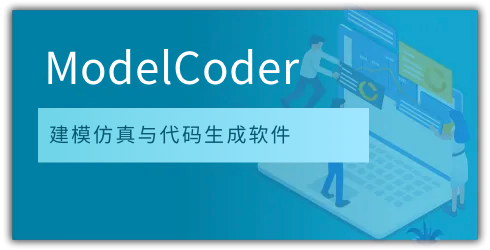
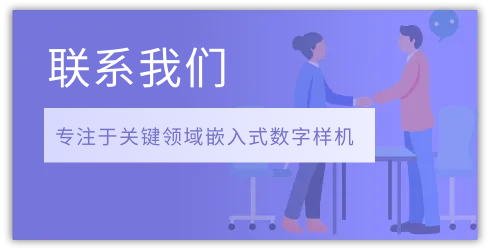
Digiproto Software is a leading provider of embedded digital prototypes in China, with the mission of “Supporting the Leap of China’s High-End Equipment Manufacturing Industry”, and is committed to “Becoming a World-Class Basic Software Supplier”.
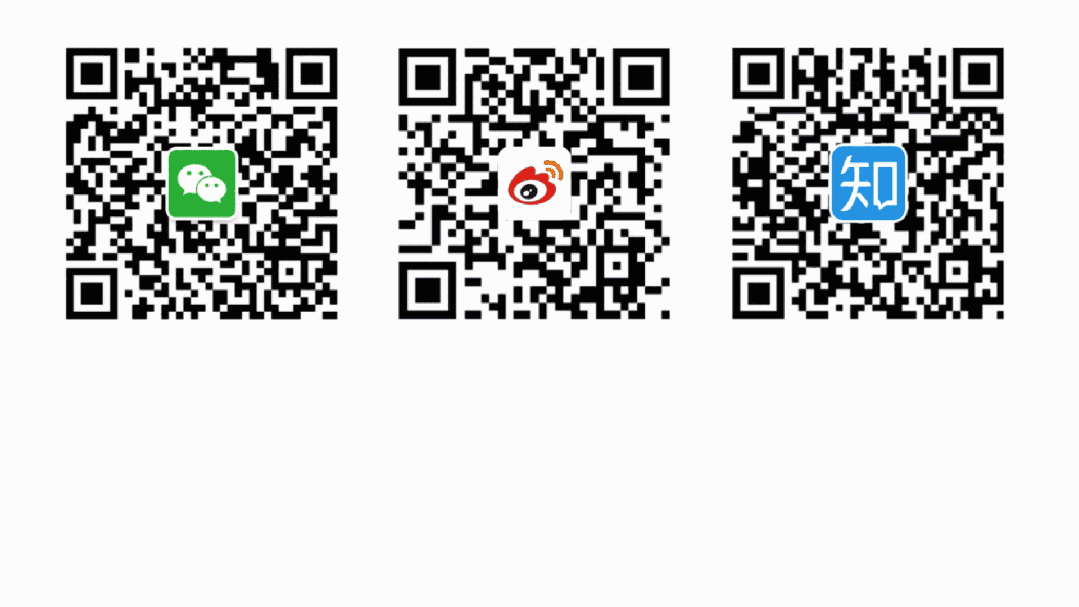