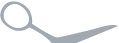
Only salt grain-sized computers, sensors, and robots are being developed that can move and detect light, sound, pressure, chemicals, and magnetic fields.
They are less than 1 millimeter long and only a few hundred micrometers thick, capable of processing information and wireless communication. Their applications are wide-ranging, from medical diagnostics, surgeries, brain monitoring to tracking butterflies and crop status.
So how do we power them?
The smallest battery currently has an area of about 2 square millimeters, which is several times that of a “dust” chip, and it is insufficient to continuously drive the complex functions of the devices. Therefore, smart “dust” chips generally rely on external power sources, such as solar panels. However, this means they cannot operate at night or in foggy weather.
Clearly, the batteries need to be miniaturized.
However, it is difficult to compress all components into a more compact space. Additionally, they need to be integrated into micro devices, similar to Tesla’s efforts to make batteries an essential part of its electric vehicles, but this is on a much smaller scale.
Compact batteries (such as lithium-ion batteries) are produced using wet chemical methods, such as coating slurries of materials onto metal foils. Adjusting the composition of the materials can only improve performance to a certain extent.
In contrast, microelectronic engineers use methods like etching and deposition to sculpt semiconductor wafers for certain improvements. However, these methods do not apply to battery materials. To improve batteries, a fundamental redesign is required.
Micro batteries need advancements in two areas to enhance charge storage capacity, namely energy-dense and durable materials, while also considering intricate architectures to miniaturize and combine components.
We have genuinely felt how difficult it is to combine electrochemistry and microelectronics. These disciplines have developed independently. Microelectronic engineers strive to incorporate new materials (such as active polymers) into their processes, and cross-contamination along with mismatches in thermal and electronic properties are common issues. At the same time, battery and materials scientists are often satisfied with optimizing one parameter of the materials without considering their practical application in devices and circuits. This is why we have established an interdisciplinary team in the lab.
▍Four Methods to Miniaturize Batteries
Batteries are essentially like a multi-layered sandwich.
Two electrodes store electrical energy in a chemical form. Between them, the electrolyte regulates the flow of charge without causing a short circuit. Two metal collectors connect the electrodes to the external circuit. However, the smaller the electrodes, the less charge they can hold. Cracks and other defects can impede the flow of electrons and lead to battery failure. The curved pathways for ions and electrons in the greasy material layer can also increase resistance.
To avoid some of these issues, the smallest batteries are very thin but not powerful. Their energy density per unit area is low, about 1/800 that of a one-centimeter-sized lithium-ion button battery. A thin-film battery with an area of 2 square millimeters and a thickness of 150 micrometers can power a simple temperature sensor for 2 days but cannot support an hour of data transmission.
The following diagram illustrates four methods to store more charge in a smaller space.
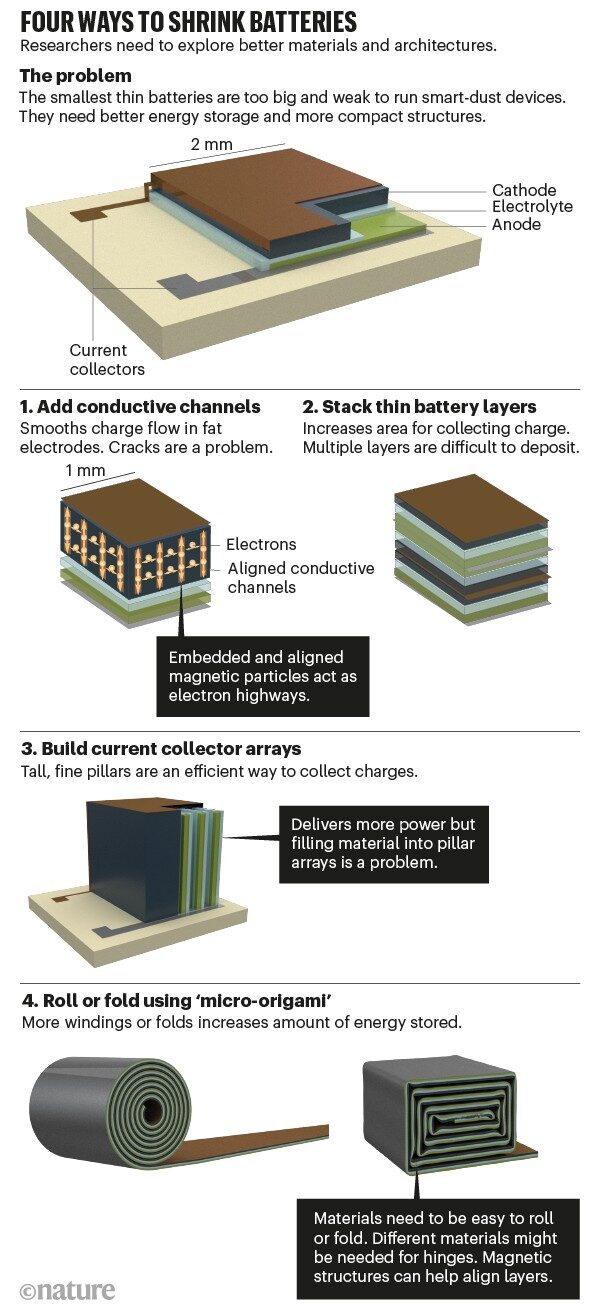
The first method is to increase conductive channels on thick electrodes. Like lanes on a highway painted with oil, embedded rows of magnetic particles can allow charges to move smoothly. However, this method has not yet been validated at the millimeter scale. Precisely setting the particle chains is difficult, and cracks remain a challenge.
The second method is to stack many thin “battery sandwiches” together. This allows charges to flow cleanly. But the difficulty lies in reliably stacking many layers, not to mention keeping them aligned. For example, the high temperatures required to anneal one electrode layer can damage another layer below. Some materials do not sit well on top of others. As the stacking builds up, mismatches can increase. Defects may lead to short circuits between closely spaced electrodes.
The third method is to redesign the collectors. Constructing them as pillars instead of sheets forms a three-dimensional structure, increasing the contact area with the electrodes and electrolyte to enhance power absorption efficiency. For example, it is feasible to build such fine three-dimensional structures by etching into silicon wafers. However, including other steps (like coating electrode materials) to assemble an entire device using this technology is extremely impractical and has not yet been achieved at the microscale.
The fourth method is to use “micro origami” to fold or curl thin films. This process can be done manually at larger scales. In commercial block or cylindrical batteries, this step is performed using folding or winding machines. At the millimeter scale, self-assembly is another way to achieve this. The film can be rolled up by built-in and released tension. Our team uses micro capacitors to accomplish this, which are dielectric sheets sandwiched between metals. However, just like rolling up a poster, it is challenging to wind the film hundreds of times without misalignment. Magnetic guidance methods can help somewhat: adding a small amount of ferromagnetic material into the battery film and applying a magnetic field can help maintain the curling process. Although we have achieved this with capacitors, battery packs are difficult to handle. They are thicker, and their mechanical properties are harder to predict.
Folding is more challenging. Just like repeatedly folding a piece of paper, the force required to bend increases with the number of layers. Hinges can accumulate stress and cracks. The “self-folding” process needs to consider all these details, such as integrating different materials into the hinges. However, aligning all layers and components remains difficult.
We estimate that folding thin-film batteries 30 times to fit the area of the smallest computer (0.14 mm²) could power it for at least 100 days on a single charge. Many smart “dust” applications will require more powerful batteries, which will need to be folded hundreds of times.
▍Enhancing Materials
Micro batteries also need material advancements so that thin films can be made as thin as possible to assist micro origami and enhance charge storage. Lithium-ion and aqueous zinc batteries are the most mature chemical methods. The challenge is to manufacture them in a way that is compatible with semiconductor technology.
In lithium-ion batteries, cathode materials (usually metal oxides like LiMn2O4 and LiCoO2) can be achieved on a small scale through etching or stripping excess material. Anodes (usually graphite) and electrolytes are more challenging to handle; the electrolyte is typically made from liquid organic compounds that are soaked into a matrix or separator, which can form a solid electrolyte. However, ceramics lose conductivity and become brittle when very thin. Polymers can be shaped, but they need to be molded (for example, ion etching and photopolymerization) to create links in the easily formed or broken molecular chains. Other methods also need improvement, such as rotating coating or depositing polymer electrolytes in a gas phase. The conductivity of polymer electrolytes also needs to be improved to compete with liquid electrolytes.
Anodes need to accommodate more charge. Silicon and lithium anodes are under research. However, they need stabilization. Silicon reacts with lithium, expanding during battery charging, which eventually crushes the electrode. Nanotechnology can prevent this damage, for example, by wrapping silicon in graphene nanosheets and using polymers to accommodate volume changes. At the same time, these solutions must also be applicable to chip manufacturing.
The lifespan of anodes made from lithium metal strips is also short. Lithium is stripped during battery operation and after charging. However, the replacement process is not perfect, and the anode gradually wears down over hundreds of cycles. Lithium needs better management during microfabrication. One approach is to avoid using metal strips and effectively build lithium electrodes during charging from ions still present in the electrolyte. This battery on a 5 square millimeter chip can be charged and cycled 80 times. This is still far from the 5–25 years of lifespan required for implantable medical devices.
Aqueous zinc batteries also need better electrodes. Zinc, used as an anode, can effectively store and release ions. Acidic electrolytes can perform better than typical alkaline electrolytes. However, zinc dissolves in acid and releases hydrogen, so the anode must be protected with a corrosion-resistant layer, or the electrolyte needs modification to release fewer protons. Similarly, cathodes (usually made from metal oxides like MnO2 and V2O5) are susceptible to acid corrosion and need blocking layers.
Such batteries also need to operate at higher voltages, at least greater than 2V, to avoid water decomposition reactions. This reaction consumes energy, so this issue needs to be overcome. All pathways involving charged intermediates (including H+, Zn2+, Mn2+, and OH-) and their interactions with electrode materials need to be explored. Polymer-based electrolytes may provide buffering for water decomposition.
Other battery chemical methods are emerging, such as those using Mg, Ca, K, and Na ions. However, these are not mature enough to manufacture micro batteries.
▍What’s Next?
Material and microelectronics researchers need to learn from each other. It is very frustrating when a material performs well in the lab but is nearly impossible to apply in real devices. We must work side by side at each other’s lab benches, spending days designing and fabricating each other’s prototypes and understanding each other’s challenges. For example, how can polymer electrolytes withstand the wet chemical processes required for modeling metal layers above them? New processes are needed to synthesize materials at given positions and layers on chip wafers in battery stacks.
Materials conferences such as the American Materials Research Society, the American Chemical Society, and the American Physical Society should invite electronic engineers to participate in energy storage agendas. Meanwhile, electronic conferences like the VLSI International Symposium should invite materials scientists to share their latest knowledge in battery chemistry. An important goal is to establish a joint technical roadmap for improving micro battery performance and target specifications.
With the help of machine learning algorithms, computer modeling is essential. Experimentally, optimizing structures and materials is required. Any changes in materials (crystallinity, thickness, and synthesis routes) will alter the mechanical properties, stability, and folding performance of thin films. Tedious work is needed to optimize each parameter, such as tension or battery chemical composition. Designers need to understand how electrochemical and mechanical properties affect the self-assembly process.
Plans need to be developed to generate and share reproducible data for batteries and micro devices. The Illinois Energy Storage Research Center and the “European 2030+ Battery Program” initiative have promoted collaboration toward next-generation batteries, including smart applications, durable materials, and industrial manufacturing.
Universities need to offer interdisciplinary courses in materials chemistry and microelectronics. Funding should come from both fields. China is rapidly moving in this direction. In August, the Chinese Ministry of Education established an interdisciplinary discipline that combines electronics, engineering, materials, chemistry, and physics, placing it on par with pure disciplines like natural sciences. Over $2 billion has been invested in establishing a new campus for the globally leading research institution, Hong Kong University of Science and Technology, in Guangzhou, China. It will follow a central integrated model. For example, functional centers will merge knowledge of materials and microelectronics to enhance the ability to integrate micro or nano devices into multifunctional components. Chemnitz University of Technology in Germany offers a similar program called Materials in Micro- and Nanotechnology. It integrates photonics, electronics, biotechnology, microrobotics, and energy storage to prepare students for future complex microsystems engineering careers.
Through collaborative efforts, micro batteries will pave the way for unobtrusive computing and ubiquitous computing technologies within a decade.
This article is reprinted from Big Data Digest
More Exciting Content
Join the Community
The Robotics Lecture Community is Recruiting! If you are engaged in or want to engage in the robotics industry and want to learn in this direction, you are welcome to join us to discuss cutting-edge robotics technology.
Additionally, discussion groups for legged robots, medical robots, industrial robots, and special robots are also recruiting, and professionals in various fields are welcome to join.
Reply “Discussion Group” in the Robotics Lecture public account dialog box to get group joining methods!
Recruiting Authors
The Robotics Lecture is recruiting part-time content creators and column writers
Please send your resume and original works to: [email protected]
We have no requirements regarding profession or location, and we welcome interested and capable friends to join!

Feeling tired? Tap “Read” to support us!