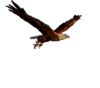
Welcome to follow “Thermal Control Circle” ID: rekongquan
Spreading thermal control knowledge, sharing technical essence!
PROFIBUS is a fieldbus standard used in automation technology, promoted in 1987 by Siemens and fourteen other companies along with five research institutions. PROFIBUS stands for Process Field Bus. PROFIBUS and PROFINET, which is used in industrial Ethernet, are two different communication protocols.
PROFIBUS can be divided into two types: the widely used PROFIBUS DP and the PROFIBUS PA used in process control:
(Decentralized Peripherals) is used in factory automation applications, allowing a central controller to manage many sensors and actuators, and it can utilize standard or optional diagnostic functions to determine the status of each module.
DP is one of the most commonly used variants of the PROFIBUS protocol, used to connect distributed automation devices such as PLCs, I/O modules, drives, and sensors. DP supports high-speed data transmission, allows real-time control and monitoring, and has high reliability. DP uses the RS-485 physical layer, supports multiple master connections, and has a maximum transmission distance of 1200 meters.
(Process Automation) is applied in process automation systems, monitored by process control systems to control measuring devices. It is an intrinsically safe communication protocol suitable for explosive areas (classified as Ex-zone 0 and Ex-zone 1 in industrial explosion hazard zones). Its physical layer (cable) matches IEC 61158-2, allowing power to be supplied to field devices via communication cables, even limiting current in the event of a fault to avoid situations that may cause explosions. Because it uses network power, the number of devices that can be connected in a PROFIBUS PA network is also limited. The communication rate of PROFIBUS PA is 31.25 kbit/s. The communication protocol used by PROFIBUS PA is the same as that of PROFIBUS DP, and it can connect to the PROFIBUS DP network with the help of conversion devices, using the faster PROFIBUS DP as the backbone to transmit signals to the controller. In applications that require simultaneous handling of automation and process control, both PROFIBUS DP and PROFIBUS PA can be used together.
PA is a variant of PROFIBUS specifically designed for process automation, suitable for connecting sensors and actuators, such as temperature sensors, flow meters, and control valves. PA has a lower data transmission rate but supports long-distance transmission and powered devices. PA uses a special physical layer (MBP), allowing multiple devices to be connected on one line, with a maximum transmission distance of 1900 meters.
3. PROFIBUS PA Network Topology Diagram
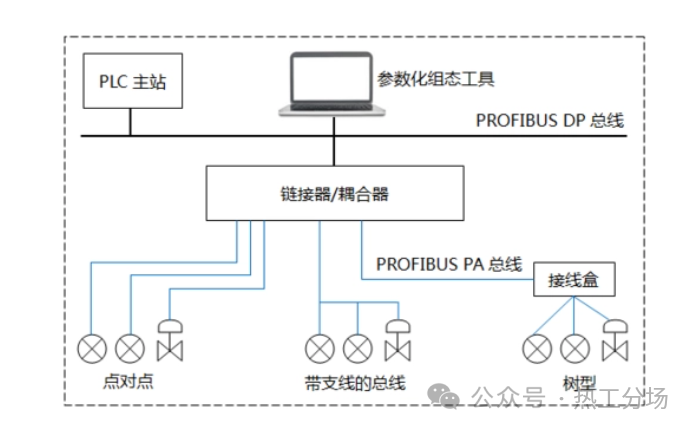
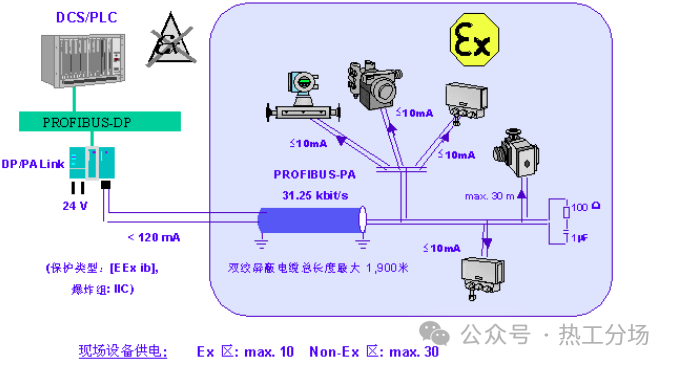
4. PROFIBUS DP Network Topology Diagram
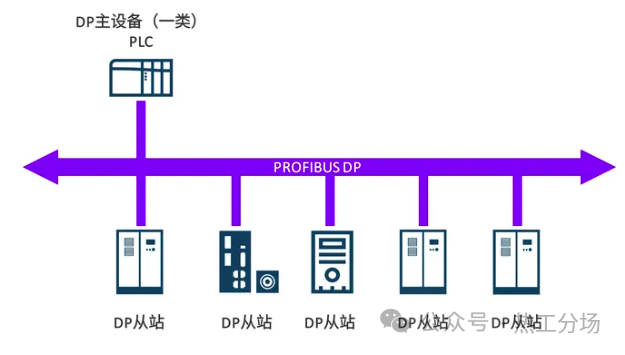
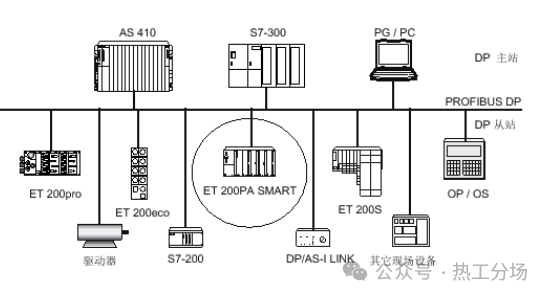
Editor: Lan Ling Wang
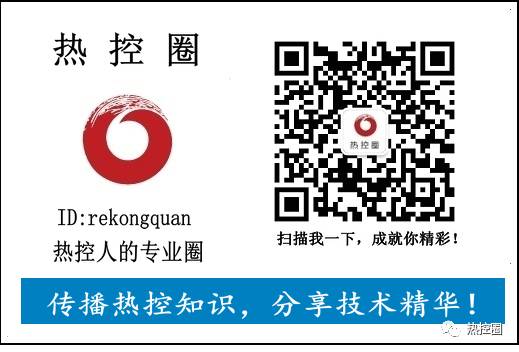
Thermal Control Technology Exchange Group
The world of thermal control is full of excitement. Welcome to join the “Thermal Control Circle” WeChat group and QQ group. How to join: 1. Official QQ group number 587444254 2. Official WeChat group: Please add Lan Ling Wang’s WeChat ID (yanghelou)