Structures deform under load. If the structure can return to its original shape after the load is removed, this deformation is called elastic deformation. Within the range of elastic deformation, the stress-strain curve of the structure follows a consistent path back and forth.
(Stress-Strain Curve of Linear Elastic Material)
However, when the stress exceeds a certain value, the structure cannot return to its original state after unloading, resulting in a portion of permanent deformation, which is called plastic deformation. This stress is generally referred to as the yield stress σy.
(Stress-Strain Curve of Ideal Plastic Material)
For most metal materials, plasticity is another important mechanical property aside from elasticity. Reasonable use of material plasticity in engineering design can fully exploit the performance of materials, leading to better economic outcomes. For example, steel, commonly used in structural engineering, often has great ductility, allowing for considerable deformation without losing strength. If elastic design is adopted, the allowable stress remains elastic, meaning that the maximum stress experienced by the structure just reaches the yield point, marking the limit of the structure’s load-bearing capacity. However, if the plasticity of the material is considered, it can be assumed that when a specific area (for example, the entire cross-section) of the material enters plasticity, the limit load-bearing capacity is reached. Thus, the same structure can often carry a higher design load, or conversely, less material can be used for a given design load.
Unlike elastic deformation, which follows the generalized Hooke’s law, plastic deformation is a very complex process that varies with different materials and external conditions and is described by various theoretical models of its constitutive relations. These constitutive equations are usually nonlinear and depend on the history of deformation and loading, making the solution of such problems quite challenging.
Today, I will introduce a simulation APP developed on the Simdroid platform for calculating the ultimate load-bearing capacity of structures—”Structural APP Validation: Yielding of Circular Pipes.” This APP simulates the long straight thick-walled circular pipe under internal pressure load, reaching the material yield limit, and calculating the ultimate load of the structure.
(Geometric Diagram of Circular Pipe)
For long straight steel pipes, the deformation along the length of the pipe can be ignored, allowing the assumption of a plane strain state. In the simulation APP, the modeling of the circular pipe considers symmetry, with an angle alpha being taken, and the length of the pipe being a parameter w, with the inner and outer radii of the pipe being r1 and r2, respectively. The overall constraint in the z-direction simulates the plane strain state, with symmetric constraints applied to the circumferential planes on both sides. Pressure P is applied to the inner surface of the pipe, gradually increasing from 0 to the ultimate load. The material constitutive model used is the ideal Mises plastic model, with a yield stress of 240MPa.
(APP Annotated View)
(APP Geometric View)
The calculation uses second-order tetrahedral elements, with the meshing situation shown below: 17196 nodes, 12774 elements, and 34392 degrees of freedom.
(APP Mesh View)
The displacement cloud map result when the structure reaches the ultimate load-bearing capacity calculated by the APP is shown below, with the black lines in the image indicating the position before deformation of the structure.
(APP Displacement Cloud Map)
As the load increases, the inner surface of the circular pipe first reaches yielding, then the plastic region gradually expands outward until it reaches the outer surface of the pipe, with all materials entering plasticity. At this point, even if the load does not increase, the structure can still undergo continuous deformation, indicating that the structure’s stiffness is 0, and the current pressure load is the ultimate load-bearing capacity of the structure. Hill derived the analytical solution to this problem[1]. The relationship between pressure and the outer radius of the plastic zone is as follows:
(Formula ①)
For the Mises yield criterion, we have.
(Partial Yielding in the Cross-section of Circular Pipe)
Whenr=r1, the inner wall of the circular pipe begins to yield, and the load at this time is:
The radial displacement of the structure is:
Where E is the material’s elastic modulus, and υ is the Poisson’s ratio. When P≥P0, the relationship between r and P is given by Formula ①.
When r=r1, all materials yield, and the pressure at this time is the ultimate load-bearing capacity, expressed as:
For this case, Plimit=0.192091GPa.
In this example, the APP’s input load Pin=0.2GPa is greater than the ultimate load-bearing capacity. Because the structure solver of the Simdroid platform uses an automatic load increment algorithm, pressure starts from 0 and gradually increases. The program requires nonlinear iterative solutions for each load level. As the pressure approaches the ultimate load-bearing capacity, the incremental step size calculated by the automatic increment algorithm continuously decreases until an attempt with a very small load increment (generally less than 10-5Pin) fails to yield a convergent solution, at which point it can be considered that the ultimate load-bearing capacity of the structure has been reached. The cumulative increment step size multiplied by the input load is the ultimate load-bearing capacity calculated by the program.
(APP Stress Cloud Map)
The value behind the play button in the image【0.961】 is the cumulative increment step size. More precise data can be obtained in the FEAPResult folder under the APP directory, with a value of 0.9605957.
The ultimate load calculated by this APP is:
The ultimate load calculated by the APP in this case is slightly larger than the analytical solution, with an error of only 0.0152%, verifying the accuracy of the APP’s calculations.
Selecting the outermost node on the x-axis, the load-displacement curve is shown below:
(Load-Displacement Curve)
From the curve graph, it can be seen that when the load is small (less than 5.2E7 Pa), the relationship between load and displacement is linear. When the load is large, the relationship becomes nonlinear, and as it approaches the ultimate load-bearing capacity, a very small load increment can cause a large radial displacement, indicating that the structure loses stability due to material yielding.
As seen in the video above, when the cumulative increment step size is less than 0.5, the distribution of the Mises stress cloud map does not change, and only the stress values gradually increase, which is the linear elastic response of the structure. After the cumulative increment step size reaches 0.5, the stress begins to yield from the inner surface, and the plastic region (red area) gradually expands outward until it reaches the outer surface, covering all materials, and the structure undergoes significant radial displacement, indicating the nonlinear response of the structure after entering plasticity.
References:
[1] Hill R. The mathematical theory of plasticity [M]. London: Oxford University Press, 1950
[2] E. A. de Souza Neto, D. Perić, D. R. J. Owen, Computational Methods for Plasticity: Theory and Applications, Wiley, 2008, 10 (1-2): 161–174
[3] Xia Zhigao, Plastic Mechanics, Tongji University Press, 1991
[4] O. C. Zienkiewicz, R. L. Taylor, The Finite Element Method for Solid and Structural Mechanics, Elsevier Butterworth-Heinemann, 2005, 2
This APP has been uploaded to theIBE APP Store, please click“Read the Original Text”or copy the link below visit the store, search for “Structural APP Validation: Yielding of Circular Pipes” to download and try.
https://appstore.iadiae.com/
[Kármán Vortex Street]
[Stirrer Flow Field Simulation and APP]
[Temperature Rise Calculation of High-Pressure Wire Current]
[Vibration Hammer Vibration Characteristics Calculation APP]
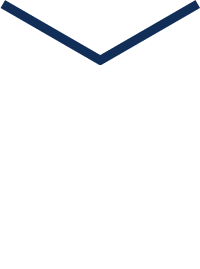
APP Development File Download
Please go to the 【Simulation Platform Forum】 in the 【Simdroid Communication section to download the APP development files. We will continue to update other APP development files in the forum, please stay tuned.
Simulation Platform Forum
1. Copy the link to open in a browser, http://bbs.iadiae.com:8888/discuz/forum.php
2. Access the forum through the 【Cloud Manufacturing Official Website】 – 【Community】.
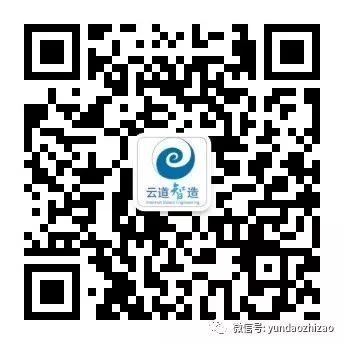