According to reports from Electronic Enthusiast Network (by Li Ningyuan), PLC, or Programmable Logic Controller, is a digital operation electronic system specifically designed for use in industrial environments. Generally speaking, a PLC consists of three parts: hardware, software, and compiler. Delving deeper, there are many components involved. The hardware includes I/O modules, CPU modules, terminal boards, backplanes, communication modules, power supplies, etc. The software part includes I/O software, CPU software, communication module software, etc., while the compiler part includes user programming interfaces, logic conversion, cross-compilation, and more.
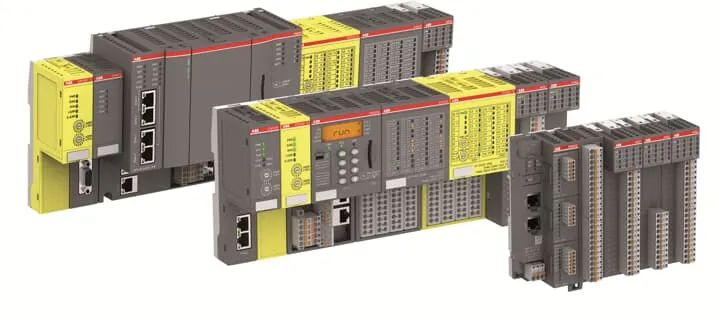
Of course, PLCs are not limited to these components. The mechanical structure design and heat dissipation treatment of the product also play a crucial role in PLC performance. As an important basic device in industrial scenarios, PLCs control various types of machinery or production processes through digital or analog input and output.
PLC Hardware Structure – I/O Module
PLCs typically obtain field signals from input modules via backplane communication. After processing through the user program, the results that need to be output are sent to the output module via the backplane bus, thereby driving the actuators to perform corresponding actions. As mentioned earlier, the main hardware structure of a PLC includes I/O modules, CPU modules, terminal boards, backplanes, communication modules, and power supplies. A 24V power supply is used to power the system, while the CPU module is responsible for user program calculations. For some field applications requiring high reliability, PLCs may need redundant CPUs and power supplies.
In previous PLC systems, I/O modules were generally designed as submodules under the CPU module, but more and more PLC devices are now making I/O modules independent. I/O modules are used to obtain signals from field sensors and control actuators, while communication module adapters are used to expand local or remote I/O.
The diagnostic functionality level of I/O modules is a consideration during selection, ranging from basic diagnostic functions to module diagnostic functions to channel diagnostic functions. Basic diagnostic functions and module diagnostic functions are module-level diagnostics used to diagnose module status and channel configurations, while channel diagnostics are the highest level, responsible for diagnosing channel configurations and statuses. Scenarios requiring high PLC performance need I/O modules to support oversampling, PWM, integrated counting, etc., necessitating the selection of I/O modules with high-level diagnostic functions, such as those with HF and HS.
I/O modules connect various field sensors and actuators, as well as the PLC/adapter, linking information through common communication protocols. In current PLC products, I/O modules have already defined various signals that may occur in industrial scenarios, including various digital inputs and outputs, analog inputs and outputs, and signals from various sensors.
PLC Hardware Structure – CPU Module
The CPU module is the core of the PLC hardware structure, and the choice of its processing core significantly impacts its performance. For small PLCs, a single MCU can be chosen as the processing core due to cost and functionality considerations, while medium to large PLCs often choose an MPU or a combination of MCU and FPGA.
MCU/MPU is responsible for user program calculations, while FPGA is needed to decode all external bus devices. Communication protocols like EtherCAT and ProfiNet generally use parallel bus interfaces; MCU/MPU may not provide enough chip select signals, whereas FPGA can flexibly provide more chip select signals.
Driving high-speed buses, data exchange, and interactions between communication modules and the CPU are also handled by FPGA. If the CPU module is designed with redundancy, synchronization logic is necessary. Tasks related to control algorithms, expansion of high-speed UART, and SPI expansion will also be managed by FPGA, which must also control external ADCs for synchronized sampling and perform simple data processing.
The selection of processors for small PLC devices is quite diverse. Manufacturers that produce MCUs for industrial scenarios generally have corresponding solutions. However, medium to large PLCs have higher requirements for processor clock speed, peripherals, and control capabilities, especially for control capabilities. Pulse output and high-speed pulse counting are two critical control requirements. Some MCU products can meet the control capabilities required by large PLCs, but for scenarios with very strict precision requirements, it is still more common to use FPGA for implementation, which is more reliable.
Leaving aside FPGA, the performance improvement of MCU and MPU is evident to all. PLCs do not have advantages in cost and performance, yet they remain highly trusted in industrial scenarios, or in other words, operations are still conducted using PLC models. PLCs are more easily accepted by users in terms of usability and flexibility in industrial automation scenarios.
In the wave of Industry 4.0, PLCs are also moving towards connectivity and intelligence, with comprehensive integration of software and hardware functionalities, and communication capabilities are further enhanced. One significant trend in recent years is that new PLCs place great emphasis on communication security and functional safety during the selection process, leading to a demand for hardware encryption units. Manufacturers are increasingly inclined to choose hardware with encryption modules and protocols with safety specifications. As technology continues to evolve, the functional safety of PLC hardware and communication security are becoming increasingly important.


Disclaimer: This article is original from Electronic Enthusiast Network. Please cite the source above when reprinting. For group communication, please add WeChat elecfans999. For submission, exposure, or interview requests, please email [email protected].
More Hot Articles to Read
-
Apple to Mass Produce the Market’s First Micro LED Wearable Product, These Supply Chain Companies Will Benefit First
-
GlobalFoundries and General Motors Reach Long-Term Direct Supply Agreement, Impacting More Than Just Intermediaries
-
The First Electric Car Price Dropped Less Than Half a Year After Launch, Is Toyota’s Loss Exposing the Decline of Japanese Car Manufacturers?
-
Microsoft Releases ChatGPT Version of Bing! Google and Baidu Join the Fray, Search Engines Enter a New Era!
-
NIO Faces “Charging” from BYD and Tesla, “One Car One Pile” Boosts the Charging Pile Industry Chain