Maurizio Di Paolo Emilio
EET Electronics Engineering Magazine Original
Power Management IC (PMIC) can provide complete power management functions within a single chip. It is often used to power small battery-operated devices, thus integrating multiple functions to improve space utilization and energy efficiency. Common features integrated into PMICs include voltage converters and regulators, battery chargers, battery level indicators, and LED drivers.
Low-power PMICs must provide a compact form factor and high efficiency to deliver longer battery life for wearable devices. In compute-intensive systems like system-on-chip (SoC), FPGA, and microcontrollers, the goal is to maximize performance per watt while optimizing overall system efficiency.
In critical vehicle electrical design, DC power management is a must for designers of Advanced Driver Assistance Systems (ADAS). PMIC solutions can achieve DC power protection, low quiescent current, and reduced EMI interference, providing a comfortable environment for the vehicle’s energy management.
Implementing PMIC solutions across various devices helps these platforms effectively utilize energy, thereby extending their lifespan. As designers continuously seek to integrate advanced technologies and features into products, the demand for PMICs is expected to grow rapidly.
Challenges
With the advancement of microelectronics and increasing power consumption requirements, the complexity and importance of power management are also on the rise. Wearable electronic devices serve as a prime example. Utilizing energy harvesting technologies and the latest generation of supercapacitors is a good strategy for achieving effective solutions.
Lightweight and compact wearable IoT devices require ultra-small batteries. The design focus has always been on extending the short operating time of the devices. To effectively manage the voltage bus in wearable IoT designs, PMICs can enable and disable power blocks as needed, providing high flexibility. PMICs can essentially allow wearable IoT devices to run longer between charges. In addition to design flexibility, PMICs also provide protection, monitoring, and control functions for batteries.
The power management system converts DC/DC power into three different forms, each differing in physical size, flexibility, and efficiency. Among them, linear regulators can be fully integrated and provide voltage scalability, but they are not very efficient; capacitor-based switch-mode regulators can also be fully integrated and are efficient, but do not support voltage scalability; inductor-based switch-mode regulators can be very efficient and achieve voltage scalability, but often cannot be fully integrated.
The overall design of the power management subsystem presents certain challenges. Designers must consider sufficient physical space for power supply and thermal design. When using natural convection power supplies, there must be enough space around the power supply for adequate cooling. If the design uses forced air cooling, designers must ensure there is sufficient space around the power supply for airflow.
“Powering high current rails poses thermal challenges, primarily to keep the internal temperature (junction temperature) of the devices within specified limits,” said Tom Sandoval, Senior Vice President of Automotive Business at Dialog Semiconductor. “But high current means high power consumption and more heat generation. It is a significant challenge to require devices that can provide high current without exceeding the specified junction temperature at specific system ambient temperatures.” The overall efficiency of circuit design has a significant impact on the heat generated at a given current level.
“Additionally, the type of package of the device can also affect the heat generated during operation,” Sandoval pointed out. “Therefore, various techniques must be employed at the system level to dissipate heat, ensuring the device operates within the specified junction temperature range.”
Designs can often be challenging and prone to issues, thus designers need a thorough understanding of compensation control cycles and the working principles of specific power management ICs. Utilizing design-oriented simulation tools can accelerate and simplify the development of PMIC solutions.
Solutions
Using PMICs with micro-power Single Inductor Multiple Output (SIMO) buck-boost DC/DC converters in wearable device designs can effectively extend battery life. By utilizing the entire battery voltage range and benefiting from the buck-boost configuration for each output, these converters can produce multiple output voltages that are above, below, or equal to the input voltage. By leveraging features like programmable peak inductor current for each output, designers can achieve a perfect balance between efficiency, output ripple, electromagnetic interference (EMI), PCB design, and load capability.
Maxim Integrated’s MAX77650 and MAX77651 PMICs integrate a 150mA low-dropout regulator (LDO) that can provide ripple suppression for noise-sensitive applications. Additionally, the controller in the SIMO control scheme ensures that all outputs are processed in a timely manner.
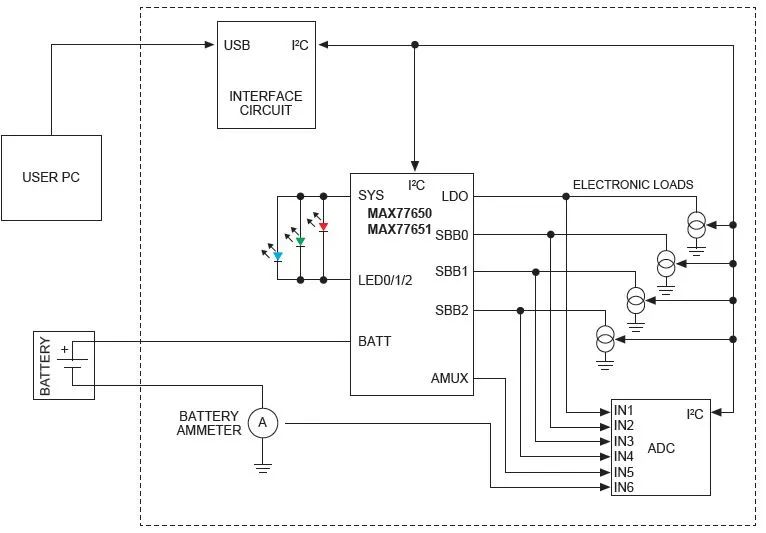
Figure 1: Functional Block Diagram of MAX77650
Karthi Gopalan, Director of Mobile Power Product Line at Maxim Integrated, stated, “Our customers in the wearable, headphone, and low-power IoT sectors are at the crossroads of high-end technology and aesthetics. With the increasing global reliance on smart AI assistants, real-time biometric tracking, and precise location tracking, these markets will have tremendous traction.”
She added that Maxim’s low-power PMIC provides “the highest system efficiency at minimal size” for these space-constrained designs. “Our PMIC can reduce the solution size by half. The space saved can be used to add value-added modules such as voice commands, payments, GPS receivers, biometrics, gesture control, 3D recognition, and camera modules.”
In automotive applications, the three main challenges PMICs must address are temperature, certification, and safety. Automotive applications require operation in an environmental temperature range of -40°C to 105°C (at least); thus, any semiconductor device for automotive platforms must deliver excellent performance across a wide temperature range.
Sandoval from Dialog Semiconductor stated, “Automotive applications demand high quality levels to ensure a failure rate close to zero over a usage period exceeding 10 years. This involves aspects like device design, certification, as well as testing and screening, to ensure the highest quality level is achieved throughout the automotive lifespan.”
Many aspects of ensuring safety in automotive applications focus on fault prevention. Power management devices must have the capability to manage electrical faults and provide feasible solutions in the event of a failure. Sandoval said, “Additional circuits need to be integrated into device design to support this functionality, but this leads to higher complexity and cost.”
Dialog offers the integrated DA913X-A, which achieves lower system material costs and smaller size. Its efficiency exceeds 90%, thereby reducing the thermal design challenges of powering high current rails in systems like ADAS.
The DA913X-A series includes three devices that can be configured as single-output or dual-output buck converters. The DA9130-A is a single-channel two-phase buck converter that can deliver up to 10A of output current. The DA9131-A integrates two single-phase buck converters, each capable of providing up to 5A of output. The DA9132-A also integrates two single-phase buck converters, each capable of providing up to 3A of current. All three devices support an input voltage range of 2.5V to 5.5V, with an output voltage range of 0.3V to 1.9V, suitable for various low-voltage systems. These devices also provide external resistor dividers to support output voltages above 1.9V.
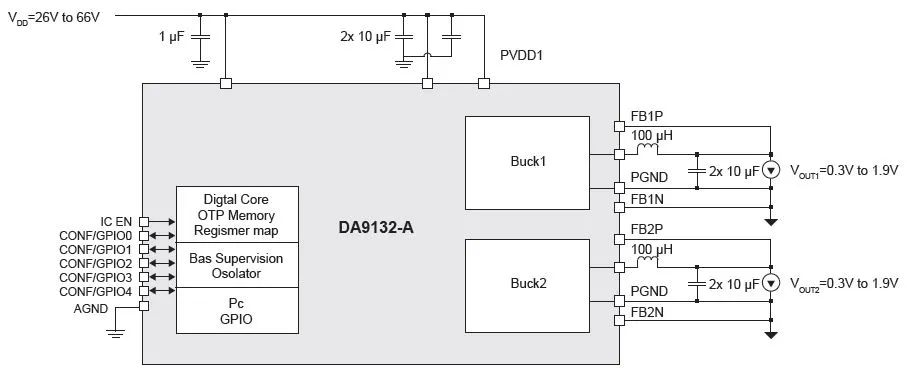
Figure 2: Functional Block Diagram of DA913X-A
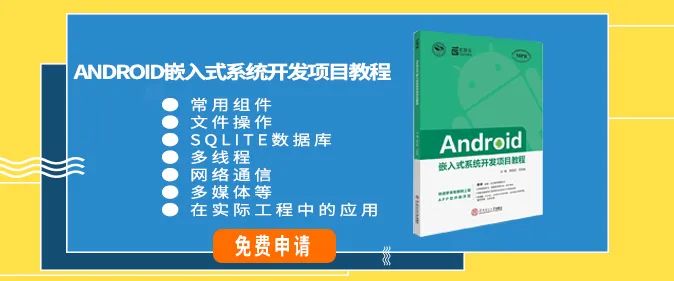