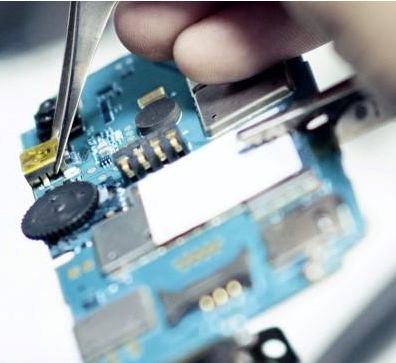
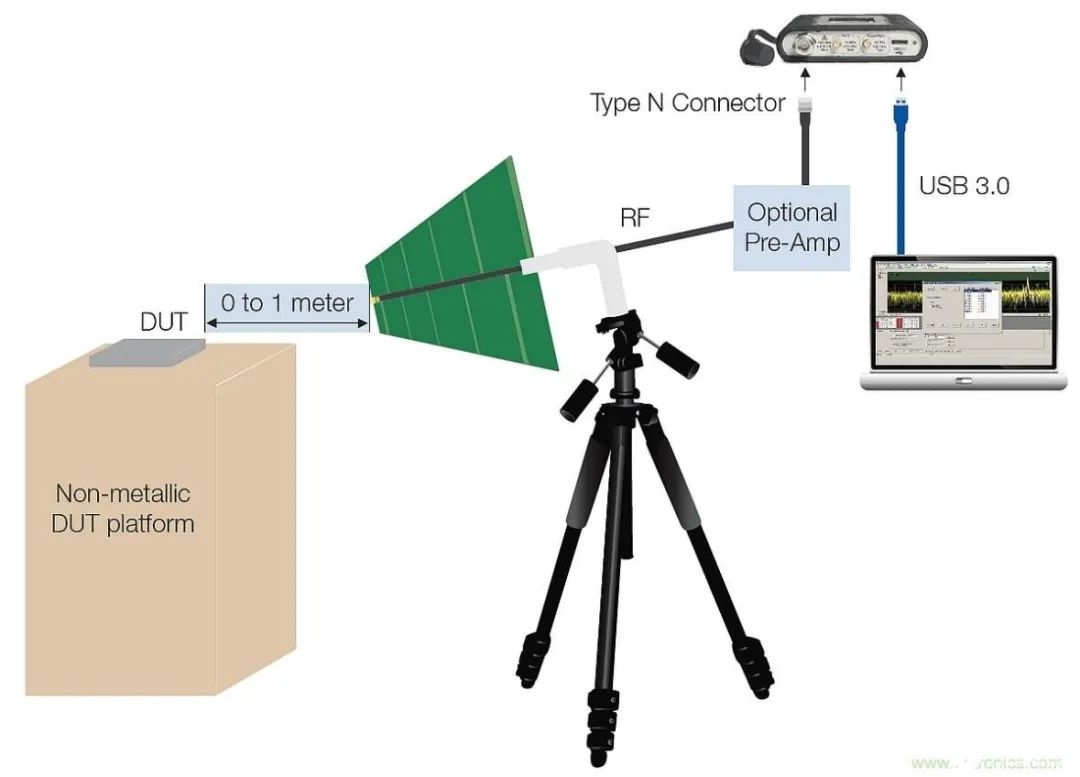
-
Nearly 60% of companies have resumed work, and 70% of companies are under financial strain – a deep scan of the impact of the COVID-19 pandemic on the electronics supply chain
-
Temperature measuring helmets are rising in popularity, accelerating deployment under the pandemic
-
Disassembling the Samsung foldable phone Galaxy Z Flip, dust resistance is a hard injury, and future technology exploration is still needed!
-
South Korea’s confirmed cases exceed 3000, the pandemic impacts the global industrial chain!
-
A decree! Is the fingerprint attendance market about to change?