
Source: Sensor Technology
Author: Faraday
Proximity sensors are widely used in various automated production lines, mechatronic equipment, and industries such as petroleum, chemicals, military, and scientific research. So, what is a proximity sensor?
A proximity sensor refers to a type of sensor that detects objects without contact, replacing limit switches and other contact detection methods. It can convert the movement information and presence information of the detected object into an electrical signal.
In the methods of converting to electrical signals, it includes methods that utilize electromagnetic induction to generate eddy currents in metallic objects, changes in capacitance due to the approach of the detection object, and methods using stones and guide switches. This includes inductive, capacitive, ultrasonic, photoelectric, and magnetic types.
Proximity sensors utilize a vibrating element that generates an alternating magnetic field. When a metal target approaches this magnetic field and reaches the sensing distance, eddy currents occur in the metal target, leading to vibration attenuation until the vibrating element of the proximity sensor stops vibrating. The changes in the vibration of the proximity sensor’s vibrating element are processed by an amplification circuit and converted into a switch signal, triggering control devices, thus achieving the purpose of non-contact detection by the proximity sensor. This is the operating principle of proximity sensors.
1. Since it can detect without contact, it does not wear out or damage the detected object.
2. Due to the use of contactless output methods, the lifespan is extended (except for magnetic types) and semiconductor outputs do not affect the lifespan of contact points.
3. Unlike optical detection methods, it is suitable for use in environments with water and oil, and is almost unaffected by stains, oil, and water on the detected object. Additionally, it includes products with Teflon casings and good chemical resistance.
4. Compared to contact switches, it can achieve high-speed response.
5. It can accommodate a wide temperature range.
6. It is not affected by the color of the detected object: it detects changes in the physical properties of the detected object, so it is almost unaffected by surface color.
7. Unlike contact types, it can be affected by surrounding temperature, surrounding objects, and similar sensors, including inductive and capacitive types, which can interfere with each other. Therefore, when setting up sensors, mutual interference must be considered. Additionally, in the inductive type, the influence of surrounding metals must be considered, while in the capacitive type, the influence of surrounding objects must be taken into account.
When a metal detection object approaches the sensing area of the proximity sensor, it can issue electrical commands without contact, pressure, or sparks, quickly reflecting the position and stroke of the moving mechanism. Even for general stroke control, its positioning accuracy, operational frequency, lifespan, ease of installation and adjustment, and adaptability to harsh environments are unmatched by ordinary mechanical stroke switches.
Classification of Proximity Sensors
Proximity sensors can be classified by working principle:
High-frequency oscillation type, capacitive type, inductive bridge type, permanent magnet type, and Hall effect type.
By operating principle, they can be divided into three categories:
High-frequency oscillation type utilizing electromagnetic induction, magnetic types using magnets, and capacitive types utilizing capacitance changes.
General type: mainly detects ferrous metals (iron).
All-metal type: detects any metal within the same detection distance.
Non-ferrous metal type: mainly detects non-ferrous metals like aluminum.
1. Two-wire proximity sensors:
Two-wire proximity sensors are easy to install and wire; they are widely used but have the disadvantage of high residual voltage and leakage current.
DC three-wire proximity sensors have two output types, NPN and PNP. Most products from Japan in the 1970s were NPN output, while both NPN and PNP output types are available in Western European countries. PNP output proximity sensors are generally used in PLC or computer control commands, while NPN output proximity sensors are more commonly used to control DC relays. In practical applications, the output form should be selected based on the characteristics of the control circuit.
Working Principles of Different Types of Proximity Sensors
Working principle of capacitive proximity sensors: Capacitive proximity sensors consist of high-frequency oscillators and amplifiers, forming a capacitor between the sensor’s detection surface and the ground, participating in the oscillation circuit. Initially, it is in an oscillating state. When an object approaches the sensor’s detection surface, the capacitance of the circuit changes, causing the high-frequency oscillator to oscillate. The oscillation and stop of these two states are converted into electrical signals and amplified into binary switch signals.
Working principle of inductive proximity sensors: Inductive proximity sensors consist of high-frequency oscillation, detection, amplification, triggering, and output circuits. The oscillator generates an alternating electromagnetic field at the sensor’s detection surface. When a metallic object approaches the sensor’s detection surface, the eddy currents generated in the metal absorb the energy of the oscillator, causing the oscillation to weaken until it stops. The oscillation and stop of the oscillator are converted into electrical signals, shaped and amplified into binary switch signals, and output after power amplification.
Working principle of high-frequency oscillation type proximity sensors: It consists of an LC high-frequency oscillator and amplification processing circuit. When a metallic object approaches the oscillation sensing head, eddy currents are generated, causing the oscillation ability of the proximity sensor to weaken, changing the parameters of the internal circuit, thereby recognizing the presence of a metallic object and controlling the switch.
Working principle of all-metal type sensors: All-metal type sensors are basically high-frequency oscillation types. Like the ordinary type, it also has an oscillation circuit. The energy loss caused by the induced current flowing in the target object affects the oscillation frequency. When the target object approaches the sensor, regardless of the type of metal, the oscillation frequency increases. The sensor detects this change and outputs a detection signal.
Working principle of non-ferrous metal type sensors: Non-ferrous metal sensors are basically high-frequency oscillation types. They have an oscillation circuit, and the energy loss caused by the induced current flowing in the target object affects the change in oscillation frequency. When non-ferrous metal targets like aluminum or copper approach the sensor, the oscillation frequency increases; when ferrous metals like iron approach the sensor, the oscillation frequency decreases. If the oscillation frequency is higher than the reference frequency, the sensor outputs a signal.
Working principle of general proximity sensors: The coil L in the oscillation circuit generates a high-frequency magnetic field. When the target object approaches the magnetic field, an induced current (eddy current) is generated in the target object due to electromagnetic induction. As the target object approaches the sensor, the induced current increases, causing the load in the oscillation circuit to increase. Then, the oscillation weakens until it stops. The sensor uses an amplitude detection circuit to detect the change in oscillation state and outputs a detection signal.
Selection and Testing of Proximity Sensors
Selection of Proximity Sensors:
For different materials of detection objects and different detection distances, different types of proximity sensors should be selected to ensure high performance-to-price ratio in the system. The following principles should be followed in the selection:
1. When the detection object is made of metal: High-frequency oscillation type proximity sensors should be selected, as this type is most sensitive to detection of ferrous metals like iron and nickel. The sensitivity for aluminum, brass, and stainless steel is lower.
2. When the detection object is made of non-metal: Capacitive proximity sensors should be selected, such as for wood, paper, plastic, glass, and water.
3. When detecting and controlling both metal and non-metal at a long distance: Optical or ultrasonic proximity sensors should be selected.
4. When the detection object is metal but sensitivity requirements are not high: Low-cost magnetic proximity sensors or Hall effect proximity sensors can be selected.
Factors in Selecting Proximity Sensors:
① Detection type: Built-in amplifier, separate amplifier; ② Appearance: Round, square, groove type; ③ Detection distance: Measured in mm; ④ Detected objects: Iron, steel, copper, aluminum, plastic, water, paper, etc.; ⑤ Operating power supply: DC, AC, universal AC/DC; ⑥ Output form: Normally open (NO), normally closed (NC); ⑦ Output method: Two-wire, three-wire (NPN, PNP); ⑧ Shielded, unshielded; ⑨ Lead-out type, plug type, plug relay type; ⑩ Response frequency: How many objects can be detected in one second.
Testing of Proximity Sensors:
Determining release distance: When the actuating piece leaves the sensing surface of the proximity sensor from the front, measure the maximum distance the actuating piece leaves the sensing surface when the switch changes from action to release.
Measuring hysteresis H: The absolute value of the difference between the maximum action distance and the release distance.
Measuring action frequency: Use a variable speed motor to drive a rubber disk, fixing several steel pieces on the disk, adjusting the distance between the switch sensing surface and the actuating piece to about 80% of the switch’s action distance, rotating the disk, allowing the actuating piece to approach the proximity sensor in sequence. A speed measuring device is installed on the main shaft of the disk, and the switch output signal is shaped and connected to a digital frequency meter. At this point, start the motor and gradually increase the speed. Under the condition that the product of speed and the actuating piece equals the frequency counted, the action frequency of the switch can be read directly from the frequency meter.
Measuring repeatability accuracy: Fix the actuating piece on a measuring tool, and from outside the switch’s action distance by 120%, approach the action area of the switch from the front. The speed of motion is controlled at 0.1mm/s. When the switch is activated, read the value on the measuring tool, then exit the action area to turn off the switch. Repeat this 10 times, and finally calculate the maximum and minimum values of the 10 measurements and the difference from the average of the 10 measurements, where the larger difference is the repeatability accuracy error.
Troubleshooting Common Issues with Proximity Sensors
1. Provide stable power supply to the proximity sensor separately;
2. Ensure response frequency is within rated range;
3. Objects may shake during detection, causing them to exceed the detection area;
4. Multiple probes installed closely may interfere with each other;
5. There may be other objects in the detection area around the sensor probe;
6. Large power equipment nearby may cause electrical interference.
Proximity sensors are widely used in machine tools, metallurgy, chemicals, textiles, and printing industries. In automated control systems, they can serve as limit, counting, positioning control, and automatic protection components. Proximity sensors feature long lifespan, reliable operation, high repeat positioning accuracy, no mechanical wear, no sparks, no noise, and strong vibration resistance. Currently, the application range of proximity sensors is increasingly broad, and their development and innovation speed is also extremely rapid.
The reproduced content only represents the author’s views
It does not represent the position of the Institute of Semiconductors, Chinese Academy of Sciences
Editor: Chunxue
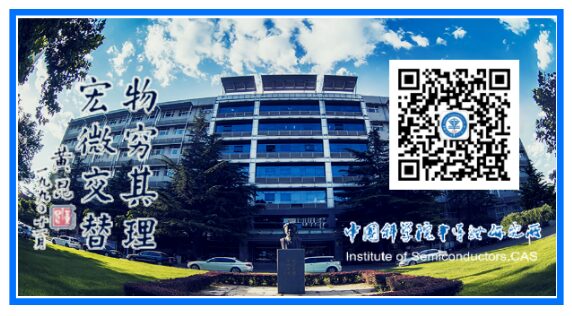