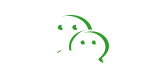
Editor’s Note
The WeChat public account of the Expert Committee of the China Plastics Association has launched a special issue of high-quality industry papers, totaling more than 30 issues, with two issues released per week. The papers in this special issue are all derived from the excellent submissions of the “2018 Conference on New Materials, New Technologies, and New Achievements in Plastics” and the Annual Meeting of the Expert Committee of the China Plastics Association. Please pay attention! It is gratifying that readers have successfully achieved the connection of technology supply and demand through this special issue.
Abstract:The control technology of injection molding machines is an essential part of the operating system of injection molding machines. With the advancement of science and technology, it has promoted the progress of control technology for injection molding machines. The arrival of Industry 4.0 has driven the development of intelligent control technology for injection molding machines. This paper reviews the control technology of injection molding machines, focusing on intelligent control technology, including hardware, software, and cloud technology, and elaborates on the advantages of intelligent control technology for injection molding, which actively guides injection operations, reduces human resources, and improves product quality. At the same time, the author presents certain ideas and prospects for the development of intelligent injection technology, providing a good development space for the advancement of intelligent injection technology for peers to reference.
Keywords:Injection Molding Machine, Control Technology, Intelligent Control, Development, Prospects
The plastic injection molding machine (referred to as the injection molding machine) is the largest variety of plastic machinery in terms of production and application in China. Since the first injection molding machine was born in China in 1958, after more than 50 years of development, it can now produce most types of machines. With the development of industrial technology, the control technology of injection molding machines has improved significantly. The control technology of injection molding machines has gone through the development process of relay and contactor control, electronic circuit sequential control, programmable logic controller (PLC) control, and computer technology control.Currently, the concept of “Industry 4.0” is sweeping the globe, and China is focusing on industrial automation, intelligence, and digitization, vigorously promoting “Made in China 2025” to complete industrial upgrades, which will also drive the transformation and development of injection molding machines in China. In the future, the control technology of injection molding machines will combine computer technology, cloud technology, and automation technology to implement closed-loop control, mainly driven by intelligent control technology, leading to intelligent equipment, intelligent production, and intelligent services in plastic product manufacturing factories.
I.Review of Control Technology for Injection Molding Machines
1.1.Relay and Contactor Control of Injection Molding Machines
Initially, injection molding machines generally used simple relay and contactor control, with control methods mostly being open-loop control, where action sequence switching was controlled by a combination of stroke switches and blocks. This could only be used for a specific fixed process; if the process changed, it needed to be readjusted or set again. The DC part was controlled by relays, while the AC part was controlled by contactors. This method of relay and contactor control has a simple structure, poor reliability, and low control precision.
1.1.1.Electronic Circuit Sequential Control
Electronic circuit sequential control uses discrete components or partially integrated circuits, initially replacing relays with gate circuits (logic circuits), using DC solenoids instead of AC solenoids, and using non-contact stroke switches and blocks to achieve action program switching, which has advantages such as fast sensing, small size, and low cost.
1.1.2Programmable Logic Controller Control
The programmable logic controller (PLC), developed in the late 1960s, consists of a central processing unit (CPU), input/output (I/O), memory, and programming device. It controls various types of mechanical equipment as the core of the automatic control device through digital or analog input/output. The PLC controls the actions and processes of injection molding machines, replacing time relays and intermediate relays with digital timers. A 24V DC voltage is supplied to DC solenoids. Displacement sensors are used to achieve action or process switching, and proportional pressure and flow control are also employed. The use of PLC for controlling the injection process and action sequences began in the late 1980s, laying a foundation for the automation of injection molding machines. However, due to various technical reasons at that time, the PLC control method also had its shortcomings, such as insufficient anti-interference ability, reliability, and temperature control precision at times. The process program could not be solidified or saved; every time the mold was changed (or the product variety changed), the process parameters had to be input and debugged, and operators needed a certain level of cultural knowledge and professional expertise, resulting in a low penetration rate and short usage time.
1.1.3PC Control
Using liquid crystal display (LCD) to display set parameters, process parameters, and process curves, graphical menus make the molding process essentially achieve a visual state, with large information capacity and intuitive operation. The use of LCD also provides computing power, fault alarms, and storage of process parameters, enabling open-loop and closed-loop monitoring during the molding process, significantly improving the performance of injection molding machines. In particular, high-performance embedded system control has gradually evolved from open-loop control to closed-loop control with proportional servo systems. Operators can use the input keyboard and LCD screen to set and adjust parameters such as pressure, speed, temperature, time, and displacement, making it regarded as a basic PC by many operators. The use of computer control has been prevalent since the late 1990s.
II.Overview and Development of Intelligent Control for Injection Molding
2.1.Introduction to Intelligent Control Technology for Injection Molding
Intelligent control technology for injection molding is a significant achievement in realizing Industry 4.0. The embedded real-time operating system used in intelligent control technology is Linux (analogous to the Windows operating system on computers). The Linux operating system on the controller is real-time; the so-called real-time nature ensures that a certain task must be completed within a specific time. It completes tasks within milliseconds. The real-time operating system Linux integrates hardware, software, algorithms, and other command forms (including cloud-based operations) to meet the required operational requirements.
There are two types of controllable variables for injection molding machines: analog input, including barrel system temperature, injection system pressure, clamping system pressure, and cavity system pressure; and digital input, including screw forward and backward position, injection table forward and backward position, etc. The hardware of the control system serves as the carrier for advanced control methods, consisting of three main parts: signal acquisition module, embedded computer control module, and human-machine interface devices such as keyboards and displays. Figure 1 shows the structural block diagram of the hardware part of the plastic machine control system.
Figure 1. Structural block diagram of the hardware part of the injection control system.
In Figure 1, the controller consists of three major modules: signal acquisition, central control, and user interface, with different modules including different units. The signal acquisition module contains both digital input/output units and analog input/output units; the central control module includes control units, storage units, and communication units; the user interface includes display units and user input units. Thus, the hardware system of the injection molding controller is a relatively complex integrated embedded computer detection and control system. Users input the required signals through the input unit (keyboard), which are transmitted to the injection molding machine through the central control module and signal acquisition module, while the actual situation of the injection molding machine is fed back to the display unit (LED screen) through the signal acquisition module and central control module, forming a human-machine dialogue interface. The hardware part can be scaled according to the required capacity.
The software part of the injection molding machine control system includes a customized real-time software support platform, advanced control methods for key process variables of injection molding machines, a modular control software system, and functions such as communication and storage. The specific structure of the software part is shown in Figure 2.
Figure 2. Structural diagram of the software part of the plastic machine control system.
The injection process has characteristics of rapidity and significant variability in each stage compared to traditional process industries. The software system must be built on a customized fast-switching real-time operating system platform. As seen in Figure 2, the software part of the control system adopts a modular design, with each module working independently to complete fixed functions, and modules synchronize through information transmission, with a large amount of data quickly synchronized through shared memory. The modular part also includes FMS (Flexible Manufacturing System) and other software existing in the software structure, increasing shared memory to extend the bus, increase bandwidth, and enhance frequency, ensuring centralized control of multiple machines.
Intelligent manufacturing control of injection molding is achieved through a terminal platform, utilizing a cloud manufacturing platform to realize data integration, process management, fault monitoring, and process optimization for the intelligent control of injection molding machines. The intelligent controller installed on the injection molding machine integrates the injection molding machine and surrounding auxiliary equipment and controls them via the controller, which feeds back to the terminal platform (including computers, PCs, and smartphones) through the cloud platform, achieving intelligent, automated, and digital injection molding. Currently, intelligent manufacturing control of injection molding is primarily composed of computer technology, cloud platforms (networks), management software, and hardware, forming a management system that promotes information interconnection, data sharing, transparent production, remote monitoring, improved quality, and reduced costs in intelligent, digital, and automated production. The basic block diagram is shown in Figure 3:
Figure 3. Block diagram of the relationship between mobile platform, cloud manufacturing, and controller.
2.2.Advantages and Functions of Intelligent Control Technology for Injection Molding
The intelligent control system for injection molding is an entirely new system, essential for both new and upgraded old equipment. It has functions such as data acquisition, analysis, management, communication, display, and interface, integrating computer technology and internet cloud technology into an intelligent, digital control method. Compared to traditional control systems, its main advantages include: precise control of key process parameters at various stages of injection production, including speed, pressure, temperature, and positioning, and achieving full closed-loop control design for integrated liquid, machine, and electrical drive systems, thus ensuring the stability of the entire process and the quality of injection products.
2.2.1 Low-Cost Intelligent Upgrade of Plastic Machines
Using the intelligent control system for injection molding can significantly improve the processing accuracy and stability of the original machine, reduce the scrap rate of original injection processing, and minimize fluctuations in product weight and dimensions. The system is highly reliable, capable of shielding the impact of user operational errors on the system, and preventing abnormal system exits. The system is user-friendly; for commonly used functions, users can operate without reading the manual. The software interface style remains consistent, with all interface elements reasonably distributed and providing sufficient and necessary prompts, with clear instructions on related input constraints (the control interface is shown in Figure 4); at the same time, this intelligent control system can be used on all models of injection molding machines, as long as it is connected according to the original machine’s wiring diagram.
2.2.2 Intelligent Integration of Surrounding Equipment
Surrounding equipment for injection molding machines includes: drying equipment, hot runner controllers, extraction machines, robotic arms, conveyors, mold temperature controllers, chillers, as well as visual inspection equipment, in-mold sensor control, and in-mold cutting devices. Each of these surrounding devices has its own operating interface, and setting and checking need to be controlled on their respective equipment, which is inconvenient and time-consuming. The intelligent control system can integrate the injection molding machine and surrounding equipment into a unified control system for intelligent management, allowing for control, setting, checking, and recording on a single system operation interface.
2.2.3Intelligent Management of Process Records
There are many recording files on the production site, such as drying process records, injection molding process inspection records, production quantity records, non-conforming product classification statistics, equipment inspection records, mold inspection records, and product inspection records, which significantly increase the workload of operators. The intelligent control system for injection molding features real-time automatic recording and storage of processes, facilitating inquiries and achieving intelligent management of process records. Employees no longer need to make numerous records; various records of the shift can be saved in the system, including production completion status, good product rates, and completion rates; the system’s non-conforming product classification defect statistics include 25 types of defective product statistics, and each product’s defects can be selected from several easily occurring defects for classification statistics, such as silver streaks, weld lines, material shortage, breakage, and deformation; process records encompass all conventional process parameters. With such intelligent and automatic recording settings, the workload of operators is reduced, allowing them to focus more on product quality.
2.2.4 Intelligent Tracking of Process Parameters
The intelligent control system for injection molding provides intelligent tracking management of process parameters. It implements intelligent recording for settings and records of injection molding process parameters. The control system tracks process curves, precision tracking, time tracking, and process data tracking, etc. The process curves include injection curves, clamping curves, temperature control curves, etc.; precision tracking provides precise records of each mold’s modulus, cycle time, various pressures, switching and opening positions, injection and other speeds; time tracking records the time for injection, melting, holding pressure, opening mold, ejecting, and even the idle time during the injection process; precision tracking and time tracking each contain specific data for each mold, with error retention to two decimal places, and ultimately show maximum, minimum, and fluctuation values, with position errors of 0.6mm, time errors of 0.5s, and temperature errors of 0.3°C, demonstrating the system’s precision, which greatly aids in optimizing processes.
2.2.5 Intelligent Monitoring of Process
The intelligent control system for injection molding performs intelligent monitoring of the process during injection. The process conditions during injection can vary widely; in addition to manual monitoring, reliance on the system’s intelligent monitoring is essential. The process tracking within the system includes over 20 items, such as temperature conditions, maximum injection pressure, minimum injection position, switching position, switching time, and other commonly used states in injection molding for intelligent data tracking. Each product has its own characteristics, and based on equipment conditions, 4-6 projects that significantly impact the product can be selected for monitoring. The process tracking data includes the setting of upper and lower deviations and error values; when fluctuations occur during equipment operation, the system automatically adjusts and saves records. If fluctuations exceed the error values, the system will issue alarms or shut down, prompting operators. The intelligent monitoring system (IMS) also displays various fault indications, aiding in the analysis of various accident causes and rectification plans, as shown in Figure 5.
a) Query temperature anomaly nodes b) Automatically identify glue leakage causes
Figure 5. Fault query and display interface.
2.2.6 Intelligent Connection of Systems and Display Devices
The system can be used not only on the injection molding machine PC but also on various display devices. TV screens can be hung on-site, computers can be used in the office, and smartphones can download apps for control. Major projects include mold material information, production statistics, waste statistics, molding processes, remote monitoring, etc., as well as production performance statistics, process data analysis, weight data analysis, and more, with the capability to manage multiple machines, detailing what each device is producing and real-time information on production transfer. The use of smartphones enables management personnel to understand on-site production conditions even when outside and even adjust process parameters.
2.2.7 Intelligent Management of Production and Services
By utilizing intelligent control technology for injection molding, integrating FMS systems, and employing high-tech management methods such as eliminating intermediate links and sharing information at high and middle levels, only by closely coordinating “planning” and “production” can products be traceable, intelligently scheduled, and managed throughout the process, allowing enterprise and workshop managers to grasp changes in the production site in the shortest time, make accurate judgments, and respond quickly, ensuring that production plans are reasonably and swiftly corrected. The company management cloud platform can also share with upstream and downstream customers in the supply chain, directly linking customer needs and management services.
2.3.Development Requirements for Intelligent Control Technology for Injection Molding
Currently, intelligent control technology for injection molding has made a good start and has developed a certain usage atmosphere, but there is still some room for future development.
2.3.1 Visual Inspection of Products
Surface defects in plastic products during molding processing affect subsequent processing and the appearance, usability, and integrity of the products. In traditional processing, manual visual inspection methods lead to missed detections due to worker responsibility and physiological fatigue, and the workload significantly impacts workers’ physical and mental health. To improve the efficiency and accuracy of product inspections, the intelligent control system for injection molding should utilize machine vision technology to perform intelligent detection of surface defects in plastic products. The machine vision system includes light sources, imaging systems, image capture systems, image collection and digitization modules, and image processing modules. On-site, mainly CCD (Charge Coupled Device) cameras are installed on the injection molding machine to align with the products being ejected from the mold, using optical imaging systems to project the measured object’s image onto the CCD sensor surface, where the image illuminance signal is converted into video signals, with machine vision technology (expert system evaluation) determining the defects of plastic parts. Additionally, scanning guns, similar to those used in supermarkets, can be used to scan both sides of plastic parts, with the system providing a pass or fail judgment on the plastic parts.
2.3.2 Mobile Operating System
Currently, the intelligent control system for injection molding can be used on smartphones, demonstrating the superiority of mobile operation and future development trends. With the development and application of 5G technology in smartphones, various functions of smartphones are becoming more complete, and the response speed of smartphones is increasing, making the operation interface on smartphones more flexible and convenient for more people to master and operate. When the PC board on the injection molding machine occasionally malfunctions, mobile operation will highlight its advantages. The scanning function on smartphones is not yet replaceable by other devices.
2.3.3 Modularization of Process Parameters
Modularization of process parameters refers to creating certain modules based on material categories for process parameters. Common materials such as ABS have their process modules, including ideal states for molding injection process temperature, speed, pressure, time, and mold temperature. When operators use these modules, they can select parameters based on the size of the plastic part, conduct trial molds, and then adjust other process parameters based on the trial mold results. This concept is similar to the operation of a point-and-shoot camera, making it easier for general technical staff to adjust injection molding processes.
2.3.4 Visualization of Process Settings
Visualization of process settings is closely related to the modularization of process parameters. A visualization module can be added after modularization, allowing for observation of material flow and filling conditions during the trial mold adjustment process on the PC screen (or smartphone), providing control and monitoring over in-mold conditions, and enabling identification of defects in plastic parts, leading to adjustments and revisions in the molding process. Currently, there are two methods: one is the development of a visual design platform for injection molding machines, and the other is the in-mold visual design of injection products. Whichever method is adopted, it needs to be reflected on the PC screen (or smartphone) to facilitate visualization of process settings.
2.3.5 Collaborative Cloud Technology
Utilizing cloud services allows enterprises to avoid substantial fixed asset investments in purchasing software and hardware and does not require additional information management personnel. By leveraging the services provided by cloud service providers, enterprises can quickly obtain services in a short time. This will significantly assist enterprises that are under time constraints. Starting from virtualization technology, a cloud computing platform is being established, with three clouds currently established: infrastructure cloud, desktop cloud, and collaborative research cloud. These three clouds essentially form the ecological system of the entire information center.
Currently, intelligent control has basically realized the first two clouds, enhancing the system’s technical content. The key is to establish the collaborative research cloud; currently, the collaborative cloud can be rented, such as Huawei Cloud, Inspur Cloud, etc., providing great convenience for users and promoting technological collaborative management. This facilitates remote collaborative adjustments of processes by technicians, and particularly during technical breakthroughs, external experts can be invited to solve on-site process issues, and collaborative learning of processes provides new opportunities for technical staff. This allows all process work to be conducted in a collaborative environment, assisting technicians in auxiliary tasks, enabling them to focus solely on production issues. This can improve overall efficiency, primarily enhancing the benefits of process settings and reducing scrap rates.
2.3.6 Customization of System Development
Promoting intelligent control systems represents an increase in costs for enterprises. If all functions are equipped on the system, the price can be quite high, putting pressure on small enterprises to promote intelligent control systems. Therefore, the promotion of intelligent control systems should be tailored to the requirements of enterprises, the conditions of equipment, and the needs of products, achieving targeted customization of system manufacturing to reduce system costs and allow more small and medium-sized enterprises to utilize intelligent control systems for injection molding. Of course, consideration should also be given to enterprises that, after recovering their initial investment, may wish to add required functions to the original system, meeting the needs for low-cost upgrades or expansions.
2.3.7 Localization of Mold Searching
Molds are crucial production materials and the foundation of all injection molding production. Generally, enterprises have mold racks to help organize mold placements. Even with mold racks, large and medium-sized enterprises often have a vast quantity of molds, requiring about 10 minutes or more to locate a mold on the rack. Some molds are too large to be placed on racks and are randomly piled on the floor; some workers do not adhere to management standards for placement, leading to a lack of clear information on mold locations over time, resulting in wasted valuable time searching for molds. A mold positioning system can help achieve instant mold localization with a single press of a button, a beep, and a flash, easily locating the mold, and the positioning system can seamlessly integrate with the intelligent controller or intelligent production management system or mold production management system, simplifying management operations.
2.3.8 Deepening System Development
The deepening development of intelligent control systems will address current issues such as the difficulty of achieving high precision in products, the challenge of controlling high-performance products, and ensuring high precision of equipment. Four solutions are proposed for deep development: static and dynamic composite compensation technology for forming precision; online perception and precise control technology for orientation structures; precision assurance technology for equipment under high-speed and high-pressure conditions; and integrated equipment and automated production line technology. If these series of intelligent control solutions for injection molding can be resolved or applied, it will deepen the application of intelligent control systems in injection molding, significantly improving product quality and production efficiency in the injection molding industry.
III.Conclusion
In the nearly 60 years of development of injection molding machines in China, with the advancement of computer technology and cloud technology, the control technology of injection molding machines has rapidly developed and improved. Traditional injection control technology primarily relied on hydraulic pumps, hydraulic valves, oil quality boards, oil pipelines, and mechanical parameters as control means. Now, intelligent control technology for injection molding combines product processes, mechanical parameters of injection molding machines, and overall process parameters (injection speed, holding pressure, melting speed, back pressure, position, etc.) to form a closed-loop control of the injection process, fundamentally ensuring product quality (weight, dimensions, surface appearance), enhancing overall product quality, reducing production costs, and increasing economic benefits. Intelligent control technology for injection molding is part of “Made in China 2025” and has even greater development potential in the future. Through the introduction of machine vision, mold protectors, online quality perception systems for molds, and intelligent integrated systems, an open and user-friendly production efficiency optimization and monitoring platform has been established, promoting the development of intelligent control technology for injection molding.
References
[1]Analysis of the Development Trends of China’s Plastic Machinery Industry[EB/OL].[2016-05-19]. http://www.sohu.com/a/76204992_240598
[2] Current Technical Level and Future Development Trends of China’s Injection Molding Machine Industry[EB/OL]. [2016-01-2]].
[3] Zhang Qimiao.Design of Computer Control System for Large Injection Molding Machines[D]. University of Science and Technology of China, 2005.04.01. 1-83
[4] Li Jinban, Lu Yixin, Ma Zhenghua et al.Collection and Processing of Hydraulic Steering Gear Test Data Using a Single Board Machine[J]. Journal of Jiangsu University: Natural Science Edition,1998(7)3; 97-107
[5] Liu Ziheng.Control Technology and Development Trends of Injection Molding Machines in China[J]. China Packaging Industry, 2011.3; 46+48
[6] Li Huajun. Design of Intelligent Controller for Injection Molding Machine[D]. Zhejiang University, 2002.03.01. 1-77
[7] Liu Yiwei, Xia Wei, Zhou Fengsong et al. Intelligent Monitoring System for Injection Molding Machines Based on Component Technology[J]. Engineering Plastics Applications;2006(34)11; 69-72
[8] Chen Kejian, Wu Yubin. Design of Intelligent Control Systems for Injection Molding Machines[J]. Journal of Shenzhen University (Science and Engineering Edition), 1998(15)4; 19-23
[9] Wang Jing, Li Huajun, Wei Wei. Design of Human-Machine Interface System for Intelligent Control of Injection Molding Machines[J]. Automation Instrumentation;2001(22)11;6-9
[10]Patent Abstract. A Smartphone-Based Control System for Injection Molding Machines[J]. Rubber and Plastic Technology and Equipment (Plastic);2017(43)8;70-71
[11] Interview.A Bright Future of Shared Intelligent Manufacturing and the Industrial Internet of Things[J]. JufengPlastic; 2017,10;40-41
[12] Liu Bin, Wu Shengjin, Zou Shifang. Automatic Detection Technology for Surface Defects of Plastic Products Based on Machine Vision[J]. Plastic Industry;2009(37)12;5-9+15
[13] Patent Abstract. A Smartphone-Based Control System for Injection Molding Machines[J]. Rubber and Plastic Technology and Equipment (Plastic);2017(43)8;70-71
[14]360 Encyclopedia. Cloud Services[EB/OL].[2017-10-24]. https://baike.so.com/doc/787725-833430.html
[15] Technical Plan. Oil Exploration Goes to the Cloud, Collaborative Research Improves Efficiency. [EB/OL].[ 2016-07-06].
[16] Mold RFID Intelligent Positioning System[EB/OL]. http://www.zhiyin-tech.com/Meetings/info/id/13.html
[17] Advanced Polymer Intelligent Manufacturing. “Innovation and Development of Green Manufacturing Technology in the Polymer Industry” [EB/OL].[2018-7-20]. https://mp.weixin.qq.com/s/abQ5OCY1txnT_LYOCG-DJg
[18] Tao Yongliang. Promotion of Intelligent Process Control for Injection Molding[J]. Rubber and Plastic Technology and Equipment (Plastic); 2018(44)8; 32-35
Company Introduction:
Chongqing Chuanyi Engineering Plastic Co., Ltd. (formerly Sichuan Instrument Factory No. 13) is located in the picturesque and historically rich cultural city of Beibei, Chongqing. The company was restructured into a state-owned limited company with shareholding in 2004 and has legal person status. The company has more than 20 injection molding machines, over 60 employees, and more than 10 various senior and intermediate professional technical management personnel. The company mainly produces engineering plastic products, also engaging in extrusion and vacuum aluminum plating, and designs and develops molds according to user needs. It primarily serves the automotive, instrumentation, communication, and chemical industries, with its leading products being automotive lamp plastic parts processing, achieving a certain scale. The company has passed the ISO9001 quality management system certification.
Statement: The content of this article only represents the author’s personal views. Please read and comment civilly.