Click the blue text to follow us
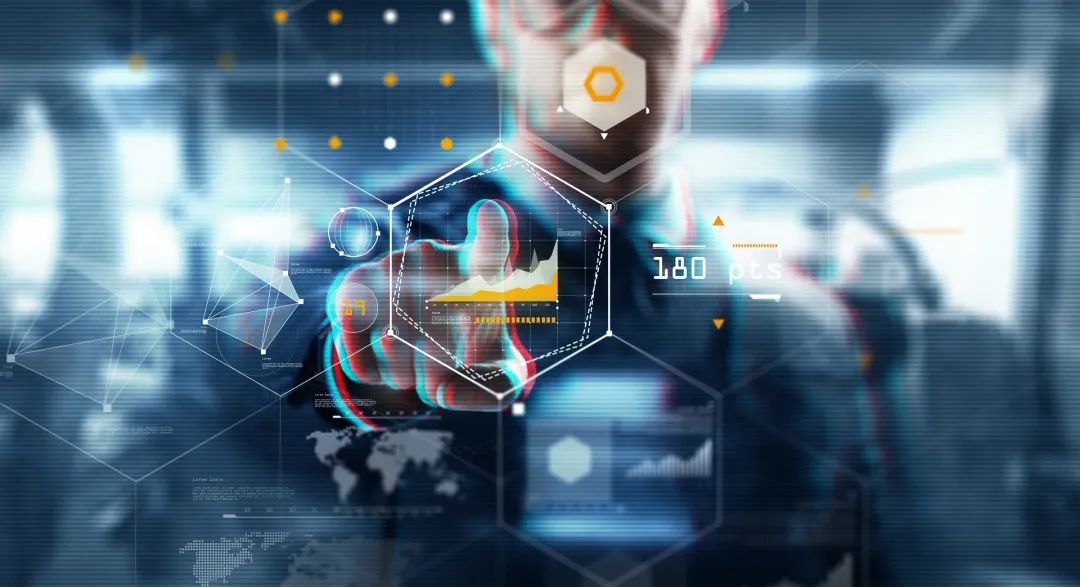
In recent years, tobacco production enterprises across the country have continuously improved the degree of modernization and automation of equipment through automation transformation and remote control upgrades.
Combining with industry characteristics, cigarette factories have begun to transition to “intelligent” production, which means achieving data interconnection among various systems through new technology networks, forming big data for factory operation and maintenance; integrating various businesses collaboratively to form a unified “Internet +” new platform; utilizing a large information system platform to achieve online services for all personnel and processes; using big data analysis to provide decision-making support for equipment operation and maintenance management, initially forming intelligent equipment operation and maintenance; making scientific decisions to achieve intelligent equipment operation and maintenance, promoting lean equipment management through intelligent equipment, and supporting high-quality development in the industry.
Business Framework, Requirements, and Overall Blueprint
Nanchang Cigarette Factory has systematically established an operational mechanism for equipment management in accordance with the requirements of closed-loop management throughout the entire life cycle, breaking down specific tasks to enhance comprehensive equipment efficiency, cultivate management and technical talents, and create a sustainable equipment management mechanism. Based on the information platform for equipment life cycle management (iTnPM@EAM) construction, fully integrating the factory’s long-term “six precision” management activities, it constructs an overall management goal of “establishing a system – achieving results – refining talents” for the equipment life cycle, as shown in Figure 1.
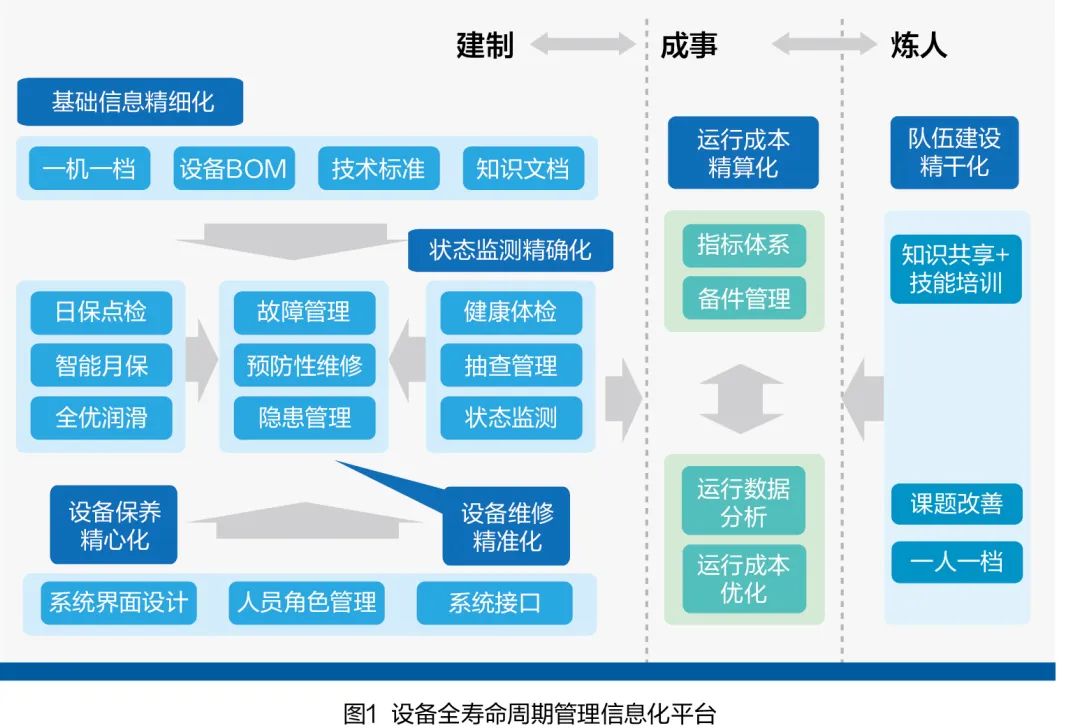
Data-driven, simply put, means making decisions and taking actions based on data as the core basis. Nanchang Cigarette Factory has made concrete plans to support the “six precision” management of equipment based on data-driven principles.
Foundation Precision. By utilizing information systems as tools, it achieves the refinement of equipment basic information data control. Just as employees have files, the enterprise also establishes files for equipment, forming a one-machine-one-file record to track the “history” of the equipment and provide foundational data support for subsequent equipment status prediction, precise repairs, and skilled teams.
Status Precision. Using advanced technology to track and monitor equipment status, combined with daily maintenance records, it achieves precise status prediction. Real-time detection and early warning are conducted, integrating production data, quality data, and minor downtimes to comprehensively evaluate and predict equipment status, thereby analyzing the precise condition of the equipment.
Maintenance Care. Focusing on preventive maintenance, it ensures meticulous maintenance of equipment, reducing the occurrence of faults from the source and ensuring stable operation of the equipment. Establishing mechanisms for daily maintenance by operators, inspections, lubrication by maintenance personnel, and evaluating work effectiveness through random checks and field inspections to form a closed loop.
Repair Precision. Based on data accumulation and analysis of daily fault repairs, it forms a fault dictionary and charts, and combines analysis of fault occurrences in key equipment areas for quick and precise repairs, optimizing repair strategies and improving repair efficiency while standardizing repair standards and establishing a preventive maintenance management system.
Cost Calculation. Minimizing costs associated with equipment operation control and maintenance, maximizing value with minimal investment, breaking down cost control indicators, and distributing them to various departments, forming performance contracts and analyzing spare parts consumption, as well as statistics on equipment maintenance costs to support cost control in equipment operation and maintenance.
Team Efficiency. Improving the training system, establishing effective training mechanisms, and building a platform for sharing equipment operation and repair knowledge, with each person having a file. Promoting employee learning enthusiasm through daily repairs and rational improvements, improving performance ranking and incentive mechanisms to motivate employees and enhance team skill levels.
The equipment life cycle management platform system built by Nanchang Cigarette Factory based on data-driven principles integrates core performance indicators, system documents, business processes, business forms, technical standards, and assessment mechanisms during the construction process. It synchronizes with the manufacturing execution system (MES) of Jiangxi Zhongyan Company, optimizing the equipment life cycle management system and the core business processes of the “six precision” management, promoting standardization, systematization, and intelligence in the company’s equipment management mechanisms. Its overall business blueprint is shown in Figure 2.
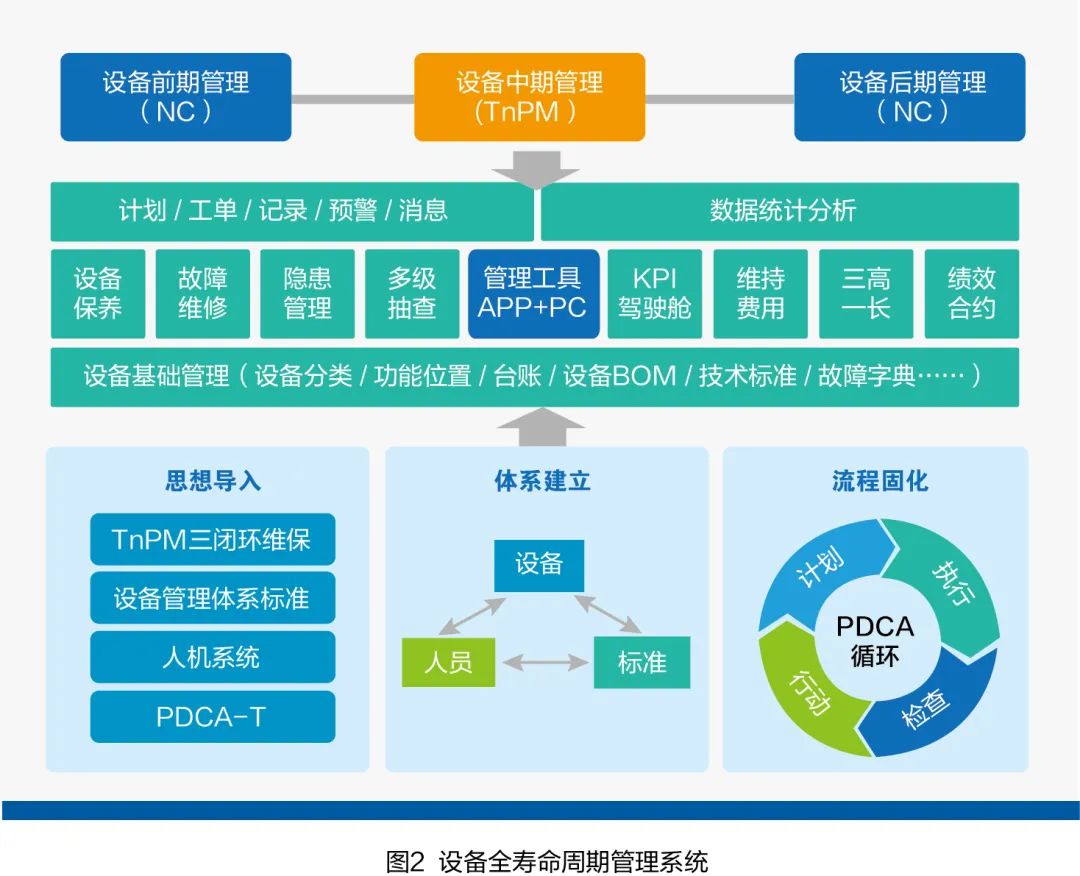
Specific Practices of Deep Integration
After more than three years of continuous iteration and upgrades, the data-driven equipment life cycle management system platform at Nanchang Cigarette Factory has been deeply integrated into the entire process of the “six precision” management of equipment, featuring the following characteristics.
Importing Management Philosophy. The system construction is based on advanced ideas such as TnPM and equipment management systems, providing methodologies for equipment construction.
Optimizing the institutional system: Using a cyclical model of human-machine-standard interaction to plan business models that support equipment operation and maintenance systems.
Leveraging management tools: Utilizing information tools to scientifically track and analyze data-driven equipment fundamentals, operation and maintenance, repairs, and decision-making.
Solidifying management processes: Through systems, tools, PDCA, etc., to control the entire equipment management process in a closed loop, solidifying processes and implementing management execution.
Figure 3 shows the main functional modules of the “six precision” management that have been interconnected and operationalized.
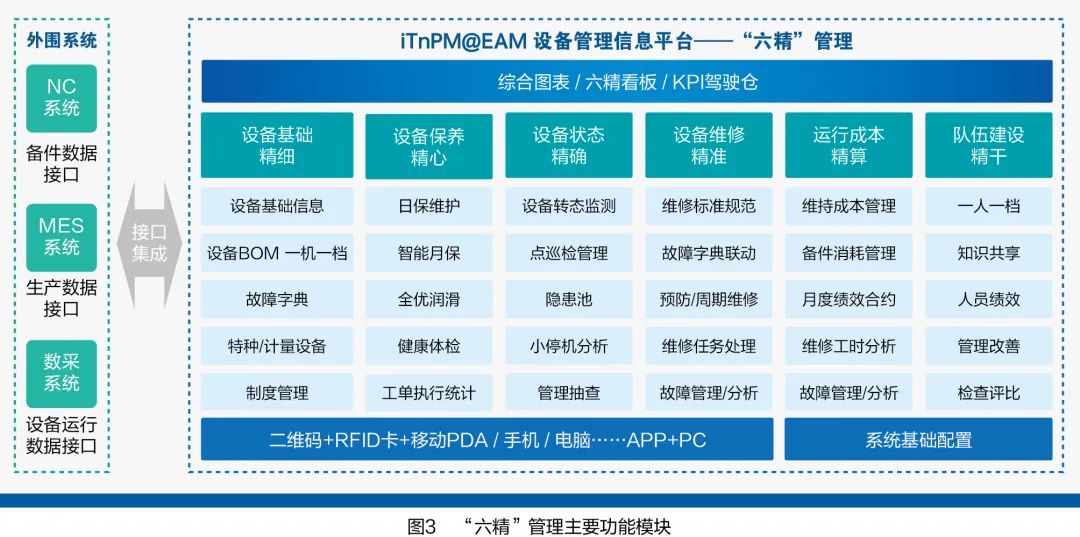
Refined Management of Basic Equipment Information. Optimized the “one-machine-one-file” management of basic equipment information, achieving static and dynamic information sharing on PC and mobile ends, establishing electronic equipment history cards, conducting data completeness analysis and optimization reminders, and featuring the ability to penetrate and analyze dynamic information; associating and synchronizing the equipment tree with spare parts information and images; managing special equipment inspection certificates and automatic warning management for measuring equipment; and batch modification of basic information for same model equipment.
Meticulous Equipment Maintenance. Constructed a health status evaluation model for equipment, allowing for monthly maintenance work based on equipment health status; one-click health checks for monthly maintenance contents related to quality hazards; automatically optimizing daily and monthly maintenance cycles, forming effective multi-level check and verification functions; continuously optimizing lubrication standards and tracking oil consumption, automatically generating lubrication lists and statistical reports.
Precise Equipment Status Prediction. Through effective multi-level check functions, conducting spot checks on inspection work effects; analyzing trends in status monitoring values and providing alerts for abnormal states; implementing special point inspection functions for equipment, statistically analyzing inspection data, and automatically generating inspection trend charts and reports.
Precision in Equipment Repairs. Standardized repair management, binding repair implementation with repair standards; automatically forming fault dictionaries, recording historical faults, and sorting and alerting based on the number of faults in key equipment areas; forming a closed loop for fault/hazard reporting, handling, and acceptance, associating repair processes with spare parts consumption information; reinforcing preventive maintenance for equipment, achieving planned maintenance management; implementing small downtime management for equipment; generating repair calls, automatically creating maintenance calendars and boards, and displaying them on-site for real-time monitoring of repair execution status.
Streamlined Cost Accounting. Connecting outsourced repairs and spare parts NC systems, promptly recording equipment repair work orders and spare parts consumption, recording repair hours, and achieving outsourced repair functionality, managing reports and statistical analysis for outsourced repair costs and spare parts consumption; monthly equipment performance assessment supported by information technology.
Efficient Team Building. Established a platform for sharing equipment operation and repair knowledge and technical exchanges; supported the implementation of performance contracts in workshops, automatically forming individual, team, and workshop equipment management performance evaluations and ranking mechanisms.
Management Effectiveness and Features
The data-driven equipment life cycle management platform at Nanchang Cigarette Factory effectively supports the implementation of the “six precision” management work.
Firstly, by building a multidimensional data visualization analysis platform, it achieves autonomous configuration of performance indicators and can connect or extract data in real-time according to needs, realizing multi-dimensional data penetration functionality.
Secondly, the key equipment operation indicators are displayed on large screens, providing the required data analysis reports for management personnel at all levels.
Thirdly, it can customize different pages for various levels and visitors, displaying pending items, critical equipment operation information, and other contents in real-time.
Fourthly, it has improved the display of “six precision” management for building intelligent factories, providing a strong foundational support.
Fifthly, it realizes visualization of equipment status, presenting real-time results of equipment operation and automatically triggering alerts for anomalies, with execution effects automatically analyzed and summarized.
Sixthly, applying big data thinking and new technologies for information/data collection, it has preliminarily achieved predictions of degradation patterns in key equipment areas.■
Author Unit: Jiangxi Zhongyan Nanchang Cigarette Factory