Click the blue text above to follow “Playing is Production”
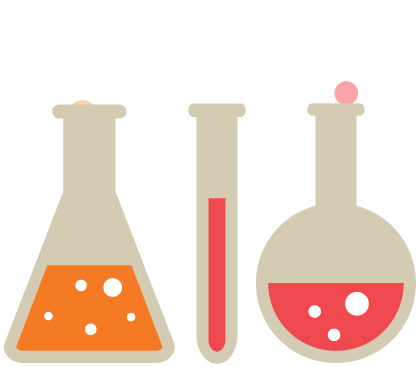
After playing with FDM 3D printing for over a year, I feel that the colors of plastic are too pure and monotonous. Although I could modify the printer for multi-material feeding with one nozzle extrusion.
This multi-color printer image is from https://www.3ders.org/articles/20160929-josef-prusas-mk2-set-to-enter-the-multi-color-3d-printer-race-with-a-clever-twist.html
But the printed results still feel flashy.
Moreover, regular FDM 3D printing has a problem: printing large flat surfaces takes a long time and is inefficient, and it is easy for the material to not adhere firmly to the platform, causing warping.
Compared to PLA plastic, I have no resistance to some beautiful and interesting wooden products.
For example, these wooden toys below:
TV Flat Stand
This one should have been polished and waxed after processing, so it looks very smooth.
Super Cute Toilet Paper Roll
This one, well, this one can also be considered a wooden product…
Although I have previously tried to make a tree person with wood-colored material, it still looked a bit like a plastic person. To make it easier for me to create structural frames or small wooden toys, I plan to build a small CNC milling machine to occasionally cut wood and acrylic and engrave circuit boards.
CNC stands for Computer Numerical Control machine, which pre-programs the cutting tool’s movement path, and the computer reads the tool path to shape the material parts. It is a traditional manufacturing method, belonging to subtractive manufacturing, in contrast to 3D printing’s additive manufacturing.
During my undergraduate studies, I was very annoyed by manufacturing processes and CNC courses, from designing processing technology, designing fixtures, generating tool paths, to tool alignment, it was time-consuming and labor-intensive. I remember during my metalworking internship, it took a whole day just to grind a hammer. Nowadays, I could easily do it with an angle grinder. The worst part was the working environment, with debris and oil making everything dirty. I didn’t expect that I would voluntarily jump back into the CNC pit…
As an individual player with limited funds, I will first make a three-axis CNC, which can move in the XYZ three directions, theoretically similar to a 3D printer. However, my 3D printer uses a CoreXY structure, and the XY is driven by belt pulleys, which may not work if converted to CNC.
This CNC is driven by three 42 stepper motors + T8 lead screws, with 12mm linear shafts for the rails, a 300W spindle motor, and the control part uses a GRBL control board; CNC shield is also fine, Arduino 2560 + RAMPS should also work, but the firmware needs some modification. The frame uses 2020 aluminum profiles, and the connectors use PVC plastic parts. It should be able to cut wood and acrylic without pressure; whether it can engrave aluminum remains to be tested.
All parts are as follows:
Assembly is a physical job. This time, I completed it with my friend, the sword-wielding Peiqi. The pictures are not very good; I tried time-lapse photography, but it turned out a bit rough. The video time is about 1:90 of the actual assembly time.
First machining test video, the noise is quite loud, please lower the volume.
First machining finished product.
During the first machining, I wasn’t very familiar with it; the feed rate was too high, and the feed speed was too fast. I wanted to engrave text but ended up cutting through. The wood used was plywood, and the cut edges were very rough. The fixture was too thick, and the clamping effect was poor. The wood chips were not cleaned up in time. These issues will be addressed in future updates.
Many of my undergraduate classmates have gone on to study CNC or work in related fields after graduation. I hope they won’t dislike my low-end toy machine too much.
– THE END –
Follow me to play together~
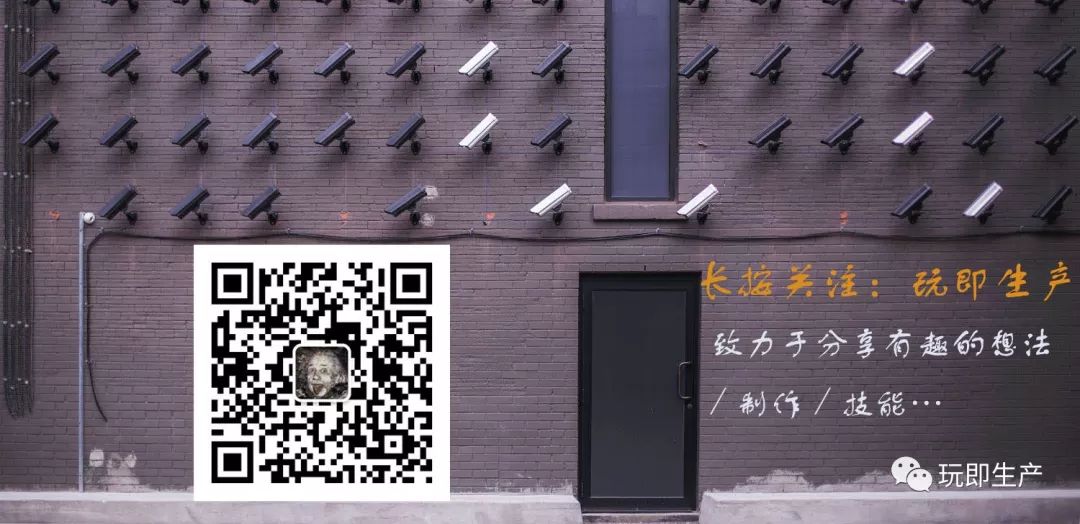
