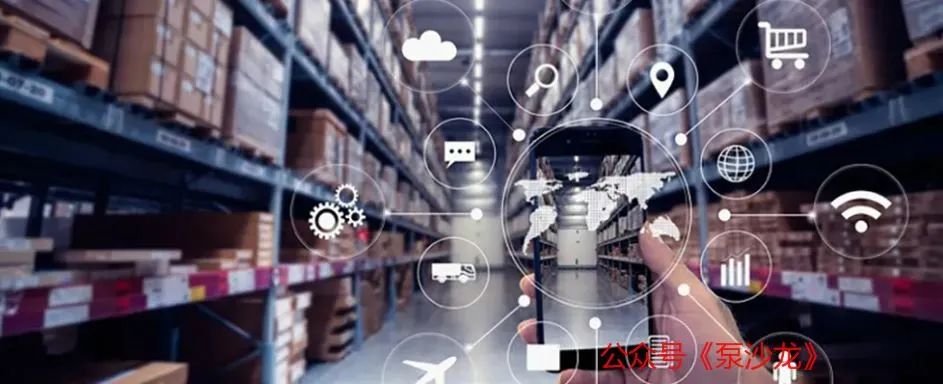
Using these tools can help companies maintain a competitive edge.
Michael Mills
Fluke Reliability
In recent years, economic pressures have increased across almost every industry, leading to a greater emphasis on work efficiency. To remain competitive, organizations/teams need to produce high-quality products quickly and reliably while operating under tighter budgets and reduced workforces.
Economic uncertainty has heightened the focus on maintaining machines rather than replacing them. This has led to the widespread adoption of interconnected tools such as Industrial Internet of Things (IIoT) sensors and artificial intelligence (AI) analytics. Monitoring asset health ensures that factories can maintain and repair assets before they fail, reducing costs and consistently meeting productivity targets. It also enables factories to operate efficiently even in the face of labor shortages.
A recent report[1] indicates that AI will be a top priority for 93% of companies within the next 12 months. 90% of senior decision-makers and over 80% of maintenance managers agree with this. Currently, only 8% of respondents are using predictive maintenance strategies, but 77% plan to shift to predictive/proactive maintenance, viewing AI as a key tool for this transition.
Predictive Maintenance and Work Efficiency
Predictive maintenance is a proactive strategy that addresses machine failures in advance and sets maintenance priorities. The strategy and core are simple: maintenance personnel monitor critical assets around the clock instead of waiting for machines to fail before repairing them. By tracking and analyzing information such as asset vibration levels, temperature, and sound, technicians can capture the first warning signs of new defects in assets. Predictive maintenance allows staff to detect machine failures early and make corrections while the failure is still minor. It significantly reduces downtime and enables managers to schedule repairs at the most convenient times.
However, predictive maintenance is not possible without today’s advanced digital tools, such as IIoT sensors and analytics software. Leveraging the power of interconnected sensors and AI-driven analytics elevates predictive maintenance to a new level.
It not only enables organizations to track the health of more assets, but advanced algorithms reduce the risk of misdiagnosing failures, avoiding delays in troubleshooting, and allowing maintenance teams to make the right decisions at the right time.
The Power of AI
AI excels in two key areas: automation and precision. This is also part of the reason why AI is so well-suited for predictive maintenance.
AI and Automation
Typical modern factories are nearly overwhelmed with vast amounts of data. In fact, most managers report that they lack the time or dedicated personnel to sift through all the asset health data they are collecting.
AI software can read large volumes of data at incredible speeds. The best AI software can accurately diagnose hundreds of different machine failures using condition monitoring data—all without human assistance. This allows technicians to focus on more complex tasks that AI cannot handle.
For teams with limited workforces, this is a game-changer. Using AI to sift through condition monitoring data means that teams won’t miss any critical information, and technicians won’t get bogged down in tedious tasks. Automating processes with AI can prevent human error, save money, and make scaling maintenance approaches possible.
However, it is important to remember that AI is not just about automating processes. The best AI tools can also perform complex diagnostics and help set maintenance priorities.
AI and Precision
A good AI diagnostic engine is detailed and precise. It sifts through condition monitoring data and can capture even the slightest deviation from machine baselines. Any deviation in vibration levels or temperature could indicate new or developing faults in the machine. If there is a change, AI will notice it.
However, next-generation AI tools do more than just flag high vibration levels and issue alerts. Today’s AI can carefully examine condition monitoring data in the environment and compare it with work order history, the age and utilization of specific assets, and even environmental factors to arrive at a highly accurate and reliable diagnosis.
Prescriptive Maintenance
Predictive maintenance can save teams time and resources, but the next step is even more exciting: a strategy known as prescriptive maintenance.
Prescriptive maintenance uses software and sensors to diagnose the root causes of machine defects and provides detailed recommendations for maintenance personnel. Prescriptive maintenance not only predicts machine failures but also seeks to find ways to keep equipment running at optimal performance by suggesting steps to resolve predicted issues and extending the time between events.
This is a win-win for work efficiency. Using AI alleviates the burden on technicians, allowing them to focus on more complex tasks and problem-solving. When AI helps set maintenance priorities, it can ensure that maintenance personnel make the most of their time and resources.
Where to Start Implementation?
AI and interconnected IIoT tools are here to stay. Integrating them into maintenance practices helps improve work efficiency and maintain a competitive edge by:
1) Implementing predictive maintenance so teams can address machine failures and unplanned downtime in advance.
2) Reducing maintenance costs by addressing asset failures early.
3) Scheduling necessary maintenance tasks at appropriate times instead of interrupting production.
4) Alleviating the burden on technicians.
Of course, implementing a new approach can feel overwhelming. Starting with pilot projects rather than rolling out new tools across the entire factory at once can be a beneficial approach. Start small, track progress, and you’ll have something to accurately measure what works and what needs adjustment.
Finally, a reminder: not all AI tools are alike or user-friendly. Be sure to look for an AI-driven diagnostic engine that has undergone comprehensive and thorough data training to recognize the subtle differences between healthy and deteriorating assets. The best AI engines have been trained on at least a trillion different data points. This ensures their accuracy in fault diagnosis. When used properly, AI and IIoT tools can significantly improve work efficiency, extend asset life, and reduce maintenance costs—making it a huge win across the board.
References
[1] info.fluke.com/frs-0624-download-value-of-ai-lp-1-a
Author Bio: Michael Mills is the Technical Manager at Fluke Reliability, dedicated to integrating sustainability into maintenance, reliability, and operational strategies. Mills has over a decade of experience in enterprise asset management and reliability-centered maintenance—based on condition and integrated condition monitoring.
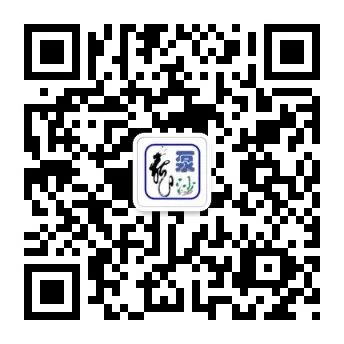