For those working in the electronics industry, they are constantly “surrounded by PCB”, seeing it everywhere. PCB is fundamental, and precisely because it is fundamental, it is often overlooked. This article will discuss PCB and some commonly used terms in the PCB field.
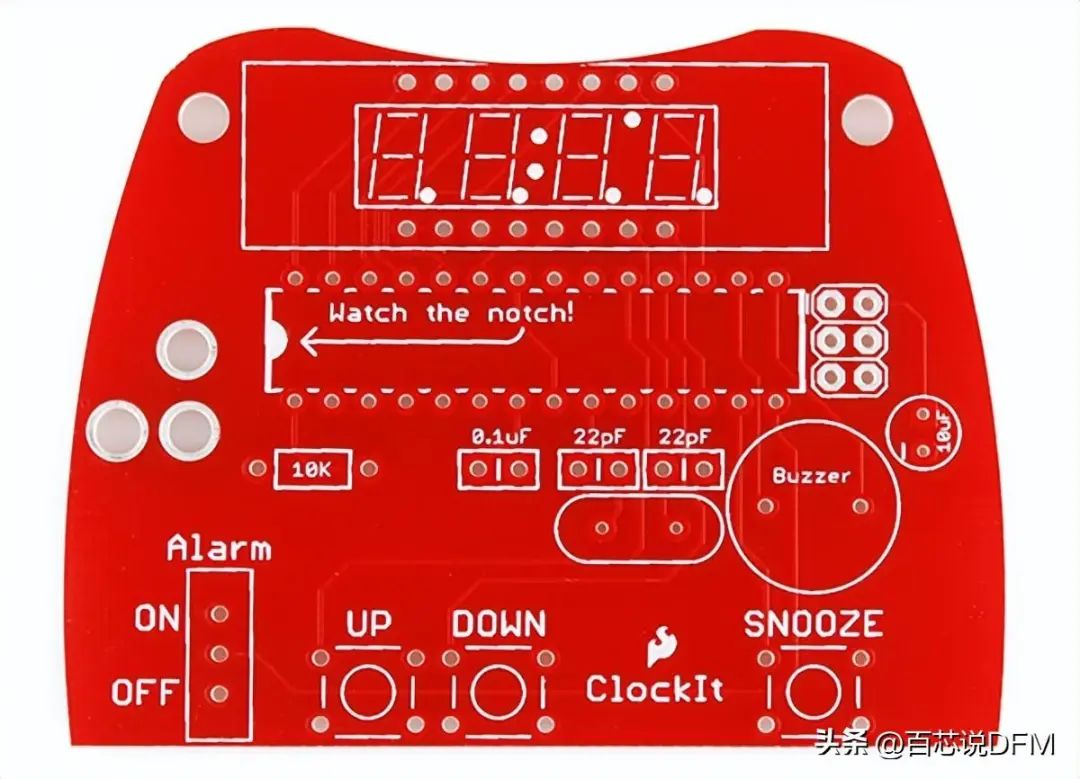
Image of PCB
1. What is a Printed Circuit Board?
The most common name is Printed Circuit Board. Before PCBs appeared, circuits were constructed through a laborious point-to-point wiring process. When the insulation layer of the wires began to age and crack, it often led to failures and short circuits at the wire connections.
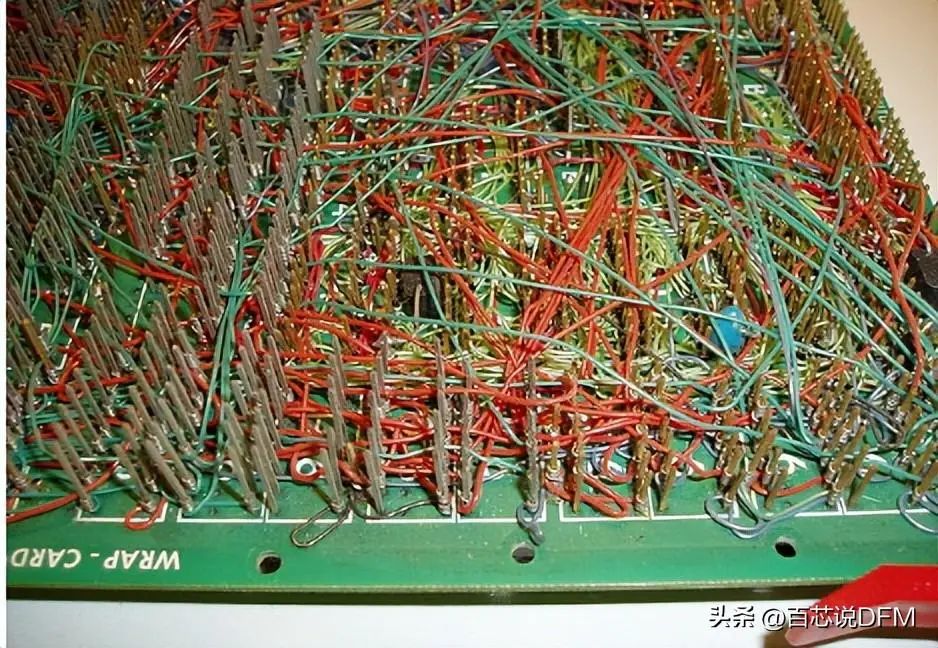
Circuit
As electronic products transitioned from vacuum tubes and relays to silicon and integrated circuits, the size and cost of electronic components began to decrease. Electronic products became increasingly common in consumption, and the pressure to reduce the size and manufacturing costs of electronic products prompted manufacturers to seek better solutions, leading to the birth of PCBs.
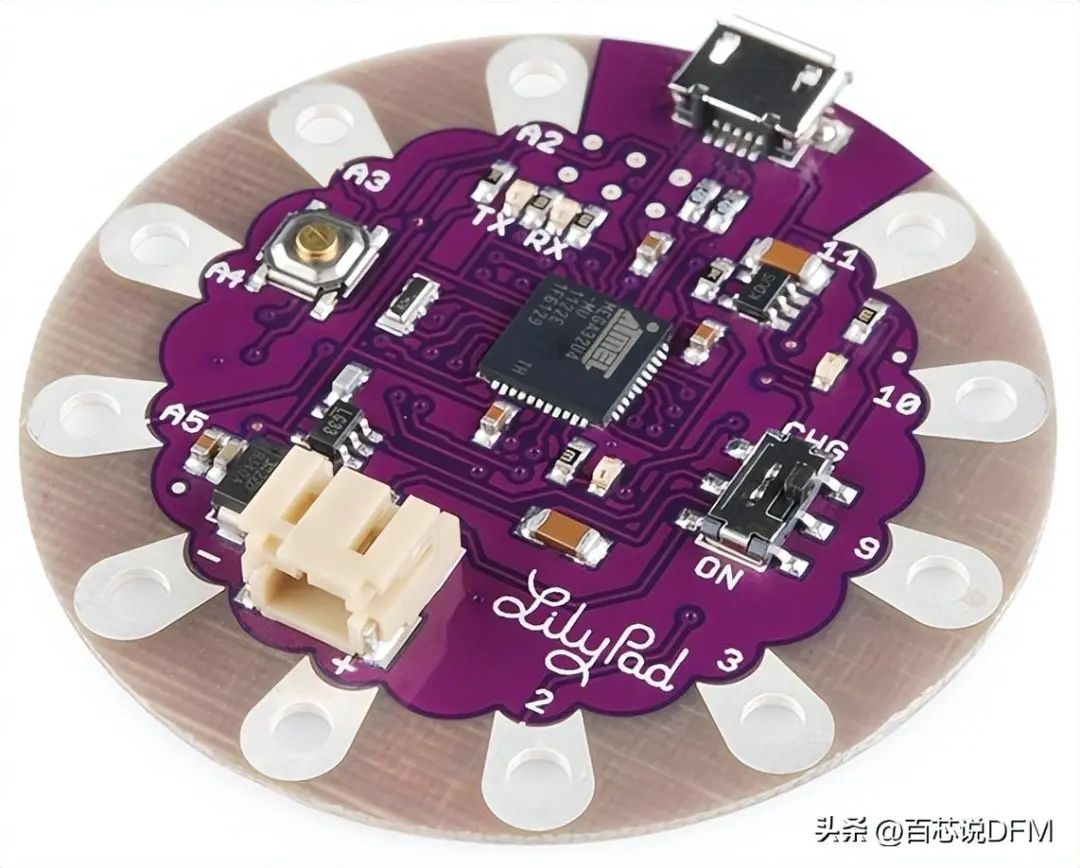
PCB
PCB stands for Printed Circuit Board, which is a board with wires and pads that connect various points together. In the above image, there are traces that electrically connect various connectors and components. PCBs allow routing of signals and power between physical devices. Solder is the metal that establishes electrical connections between the PCB surface and electronic components. As a metal, solder can also serve as a strong mechanical adhesive.
2. Structure of PCB
PCB is somewhat like a layer cake, as it has alternating layers of different materials, which are laminated together through heating and adhesive to form a single object.

Structure of PCB
1. FR4
The substrate is usually made of fiberglass. Generally speaking, the most common designation for fiberglass is “FR4”. This solid core provides the PCB with rigidity and thickness, along with flexible PCBs based on high-temperature plastics (Kapton or equivalent materials).
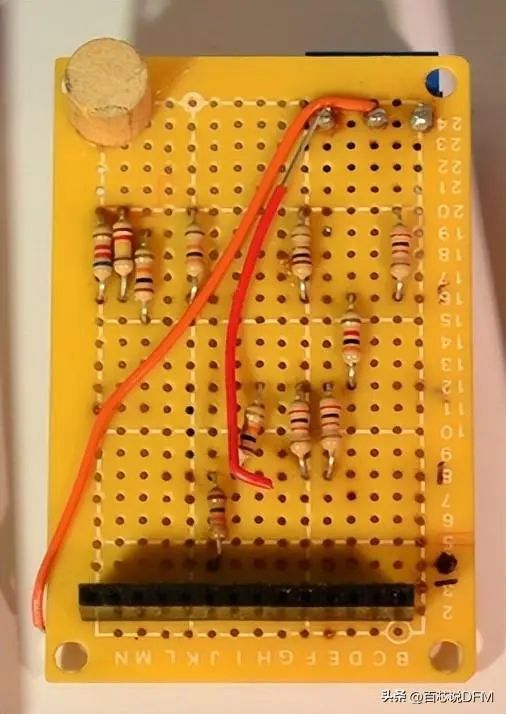
Perforated Board
Cheaper PCBs and perforated boards (as shown above) are made from other materials, such as epoxy resin or phenolic plastic, which lack the durability of FR4 but are much cheaper. When you solder, you often smell a very distinctive odor; these types of substrates are often used in low-end consumer electronics.
The thermal decomposition temperature of phenolic resin is lower, and when the soldering iron is left on the circuit board for too long, it can cause them to delaminate, smoke, and burn.
2. Copper Layer
The next layer is a thin copper foil, which is laminated to the circuit board through heating and adhesive. In a typical double-sided PCB, copper is coated on both sides of the substrate. In cheaper electronic products, the PCB may only have copper on one side. When we refer to double-sided or 2-layer boards, we mean the number of copper layers (2) in the baked noodles. This can range from as few as 1 layer to as many as 16 layers or more.
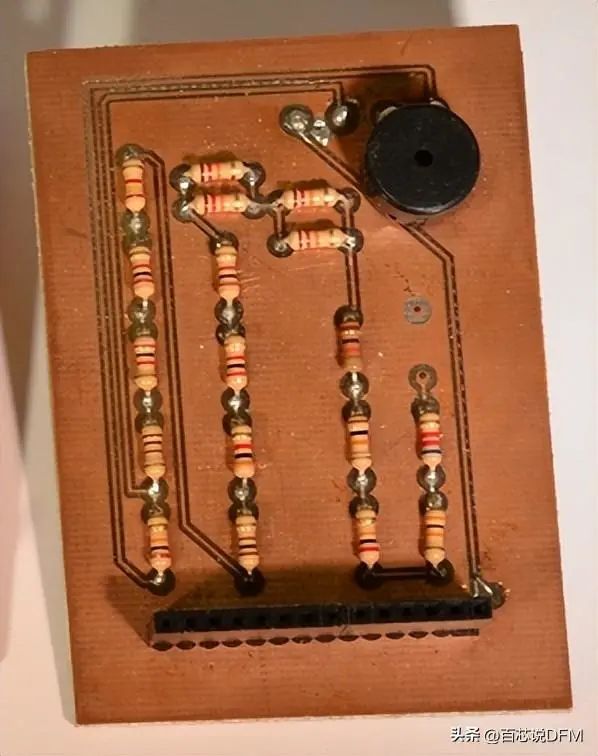
PCB Exposed Copper, No Solder Mask or Silkscreen
The thickness of copper can vary and is specified by weight in ounces/square foot. The vast majority of PCBs contain 1 ounce of copper per square foot, but some PCBs that handle very high power may use 2 or 3 ounces of copper. Each square ounce is equivalent to about 35 microns or 0.0014 inches of copper thickness.
3. Solder Mask Layer
The layer on top of the copper foil is called the solder mask layer. It usually gives the PCB a green color (but there are other colors as well). The solder mask layer covers the copper layer to prevent the copper traces from accidentally contacting other metals, solder, or conductive pads. This layer helps users solder in the correct position and prevents soldering bridges.
In the example below, the green solder mask layer is applied to most of the PCB, covering fine traces while leaving silver rings and SMD pads exposed for soldering.
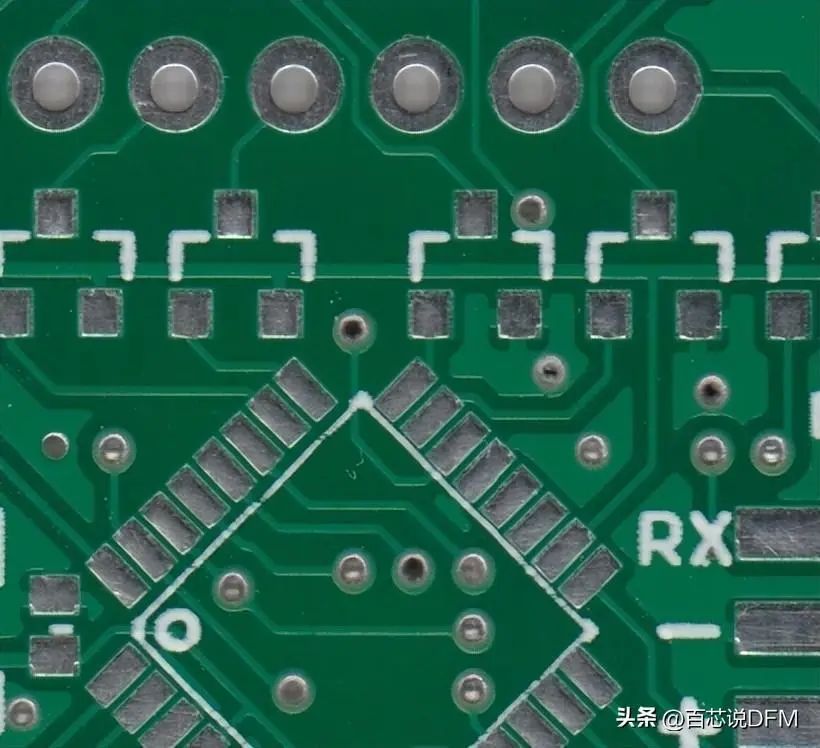
PCB Solder Mask Layer
The most common color for solder mask is green, but there are many other colors as well. For example: blue, red, white.
4. Silkscreen
The white silkscreen layer is applied on top of the solder mask layer. Silkscreen printing adds letters, numbers, and symbols to the PCB for easier assembly and indication, helping people better understand the circuit board. We often use silkscreen labels to indicate the function of each pin or LED.
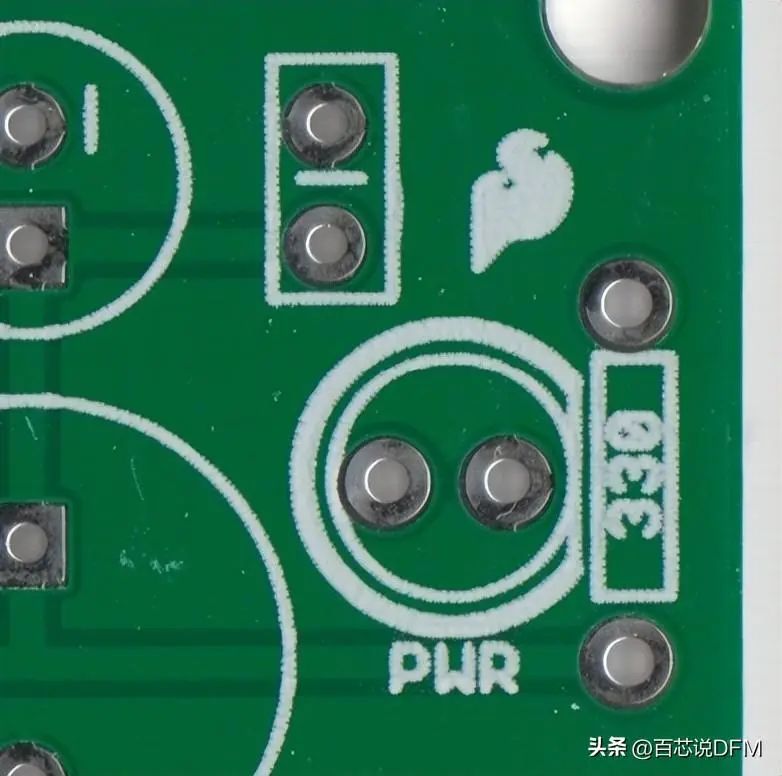
Silkscreen is most commonly white, but any color of ink can be used. Black, gray, red, and even yellow silkscreen colors are widely used, but generally, it is less common for a PCB to have multiple colors.
3. PCB Terminologies
1. Annular Ring
The copper ring around the plated through hole in the PCB.
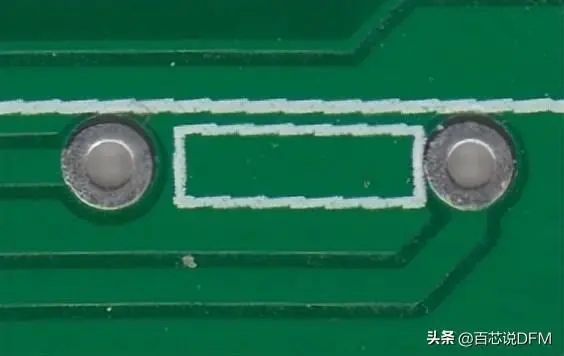
Annular Ring
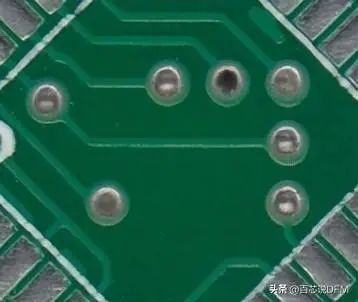
Annular Ring
2. DRC
Design Rule Check. A software check on the design to ensure that it does not contain errors, such as improper trace contact, traces that are too thin, or holes that are too small.
3. Drill Hit
The intended location for drilling holes in the design, or where they actually drill holes on the circuit board. Drill hits caused by dull drill bits are a common manufacturing issue.
4. Gold Finger
Metal pads exposed along the edge of the circuit board for establishing connections between two circuit boards.
Common examples include computer expansion boards or memory boards, as well as the edges of older cassette-based video games.
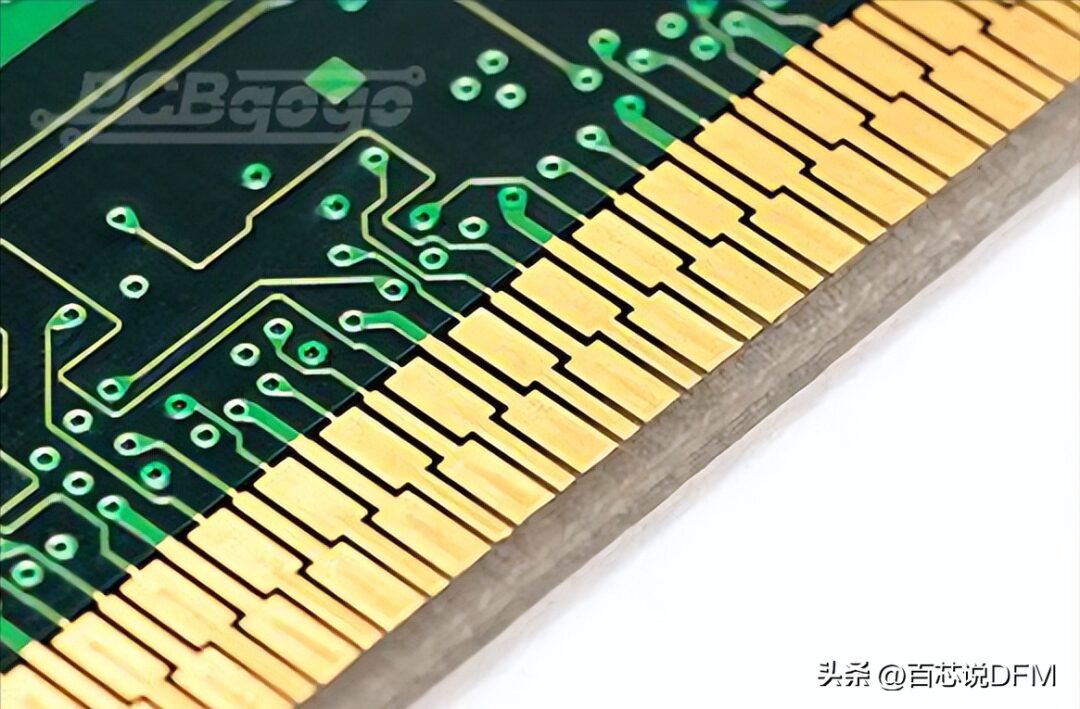
PCB Gold Finger
5. Stamping Hole
Stamping holes are an alternative method to separate the board from the panel using v-score. Many holes are concentrated together to form a weak point, making it easy to break the board afterwards.
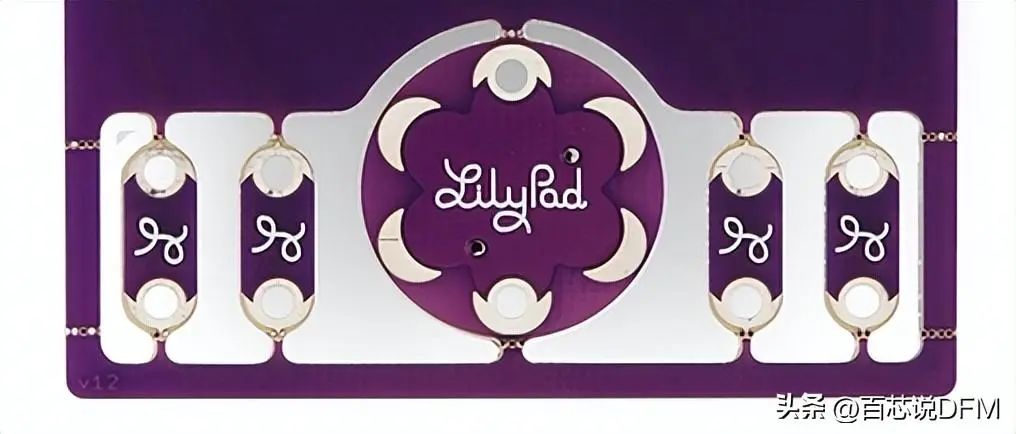
Stamping Hole
6. Pad
The exposed metal part on the surface of the circuit board, used for soldering components.
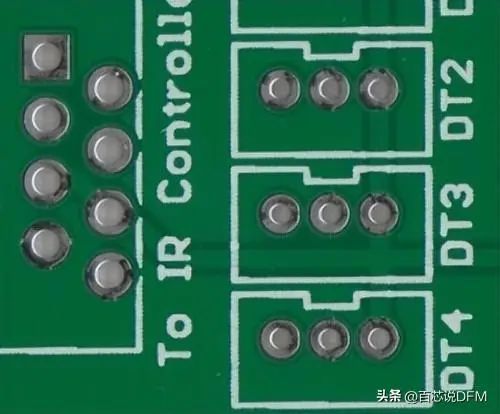
PTH (Plated Through Hole) Pad

SMD (Surface Mount Device) Pad
7. Panel
A larger circuit board made up of many smaller circuit boards that will be separated before use.
Automated circuit board handling equipment often encounters problems when processing smaller circuit boards, and by grouping multiple circuit boards together, processing speed can be significantly increased.
8. Stencil
A thin metal (sometimes plastic) template located on the circuit board, allowing solder paste to be deposited in specific areas during assembly.
9. Pick and Place
The machine or process that places components on the circuit board.
10. Plane
Continuous copper blocks on the circuit board, defined by boundaries rather than traces, often referred to as “pours”.
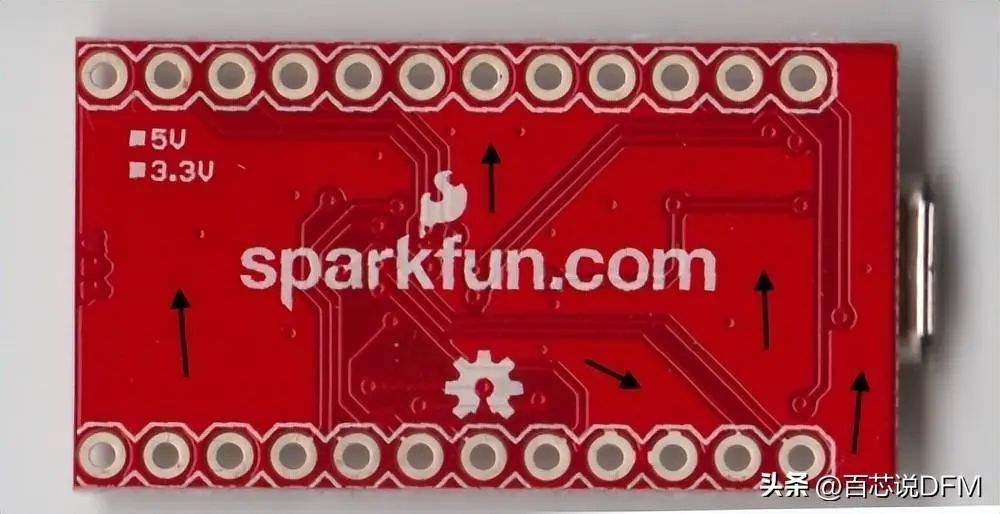
Parts of the PCB without traces but grounded
11. Plated Through Hole
A hole on the circuit board that has an annular ring and is plated through the circuit board. It may be a connection point for through-hole components, vias for signal transmission, or mounting holes.
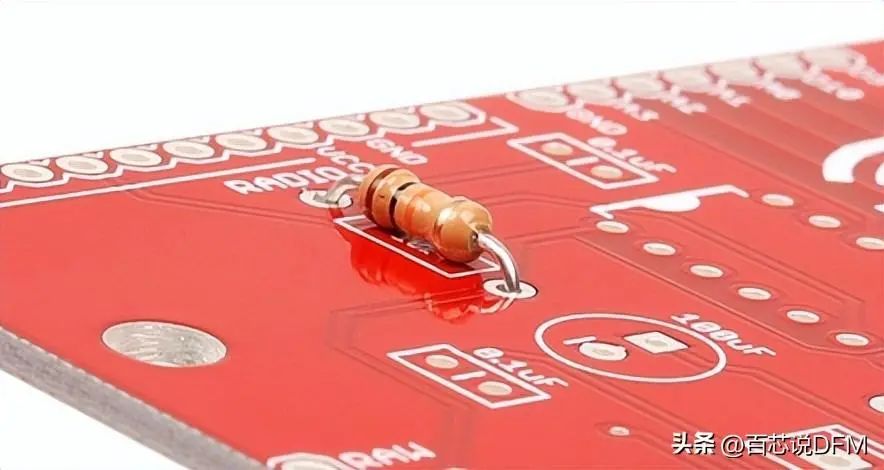
Insert PTH resistor into PCB, ready for soldering
Insert PTH resistor into PCB, ready for soldering. The legs of the resistor pass through the holes. The plated holes may have traces connected to them on both the front and back of the PCB.
12. Spring Contact
Spring contacts, used for temporary connections for testing or programming purposes.
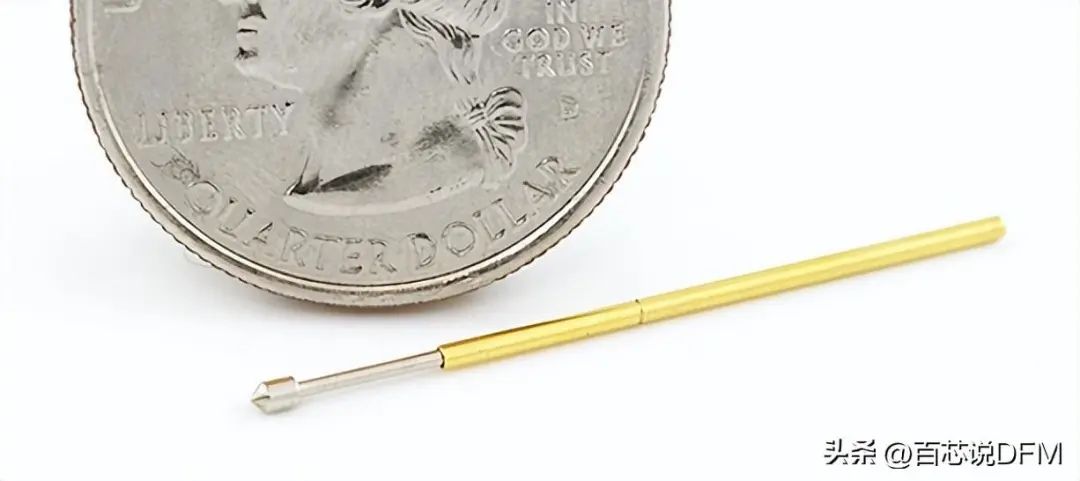
Popular pointed spring contact
13. Reflow Soldering
Melting solder to form joints between pads and component leads.
14. Silkscreen
Letters, numbers, symbols, and images on the circuit board. Usually available in only one color, and the resolution is typically low.
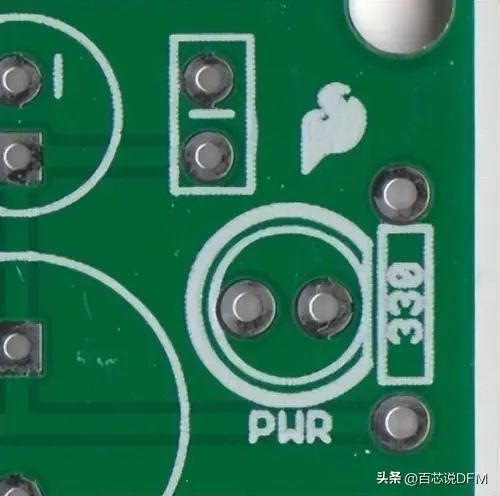
Silkscreen marks this LED as power LED
15. Slot
Any non-circular hole on the board, slots may or may not be plated. Slots can sometimes increase the cost of the circuit board, as they require additional cutting time.
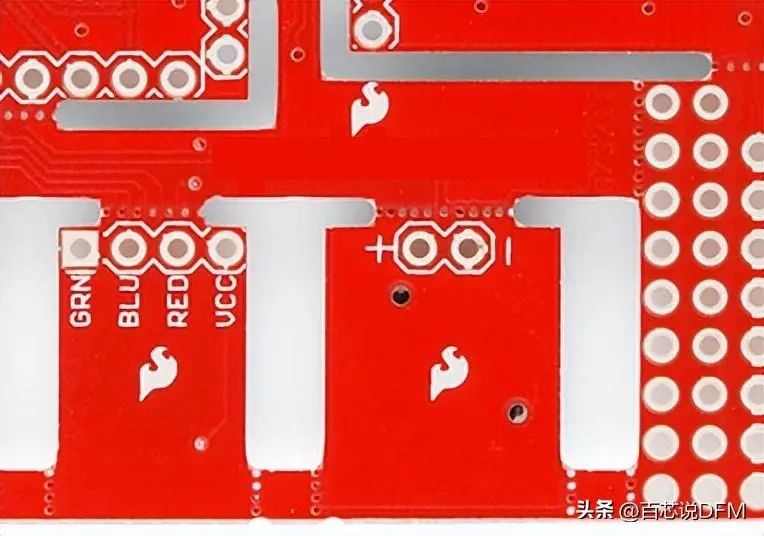
Complex slot showing multiple stamping holes
Note: The corners of slots cannot be made completely square, as they are cut with round end mills.
16. Solder Paste
Small solder balls suspended in a gel medium, applied to the surface mount pads on the PCB with the help of the solder paste stencil before placing components.
During reflow soldering, the solder in the solder paste melts, forming electrical and mechanical joints between the pads and components.
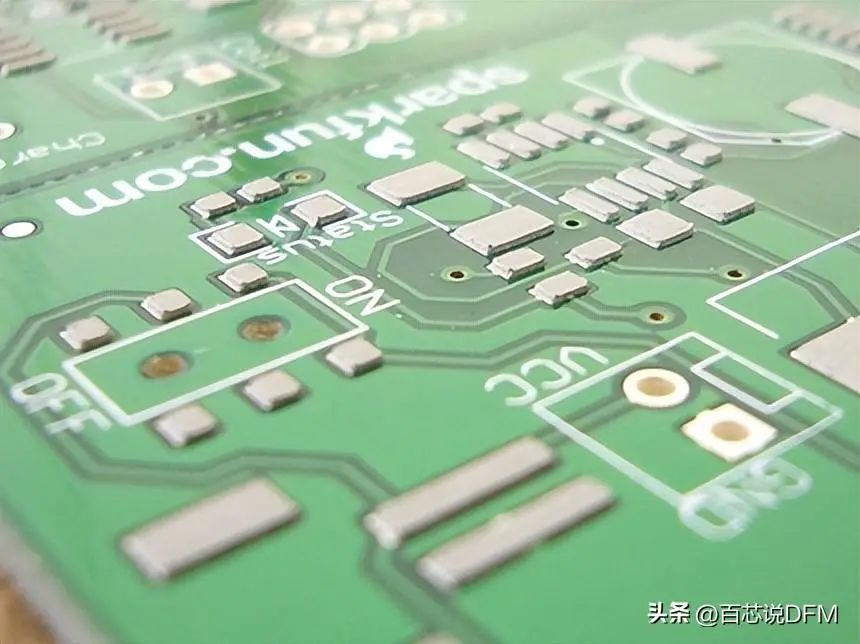
Solder paste on PCB shortly before placing components
17. Solder Paste
Paste used for quickly hand-soldering circuit boards with through-hole components. Usually contains a small amount of melted solder, quickly dipping the circuit board into it, leaving solder points on all exposed pads.
18. Solder Mask Layer
A protective layer covering the metal to prevent short circuits, corrosion, and other issues. Usually green, but other colors (SparkFun red, Arduino blue, or Apple black) are also possible. Sometimes referred to as “resist”.
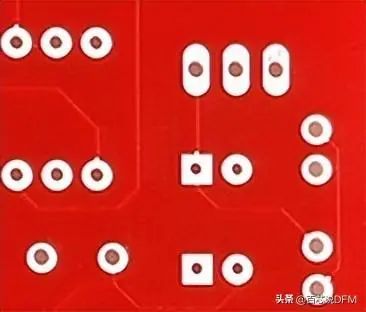
Solder mask covers signal traces but leaves pads to be soldered
19. Solder Bridge
A small amount of solder connecting two adjacent pins on components on the circuit board, according to the design, solder bridges can be used to connect two pads or pins together, and they may also lead to unintended short circuits.
20. Surface Mount
A construction method that allows components to be simply mounted on the board without leads passing through holes on the board. This is the primary assembly method used today, allowing for fast and easy assembly of circuit boards.
21. Thermal Via
Small traces connecting pads to planes; if pads do not dissipate heat, it becomes difficult to reach a sufficiently high temperature to form good solder joints. Poorly dissipating pads feel “sticky” when you try to solder, and reflow takes an unusually long time.
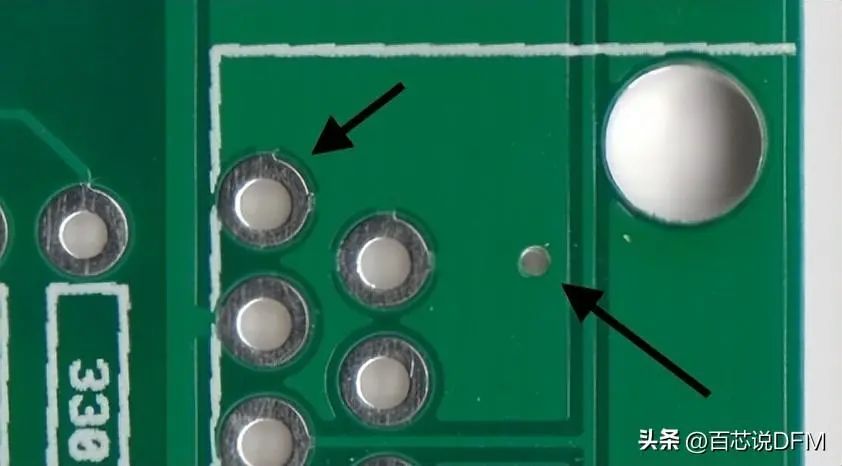
Pad with two small traces (thermal vias) connects pins to ground layer. On the right, a via without heat will connect it completely to the ground plane.
22. Thieving
Shadow lines, grid lines, or copper dots left in areas of the circuit board without planes or traces. Reduces etching difficulty because less time is needed to remove unwanted copper in the slots.
23. Trace
A continuous path of copper on the circuit board.
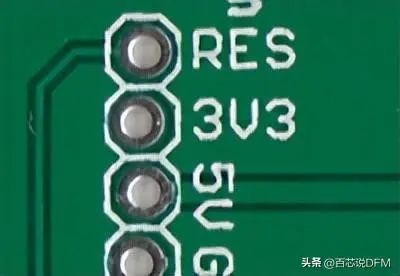
Small trace connecting the reset pad to another part of the board. Larger, thicker traces connect to the 5V power pin.
24. V-score
Partial cuts through the board that allow it to be easily broken along a line.
25. Via
A hole on the circuit board used to pass signals from one layer to another. Tent vias are covered with solder mask to prevent them from being soldered. Vias that connect connectors and components are usually uncovered (uncovered) for easy soldering.
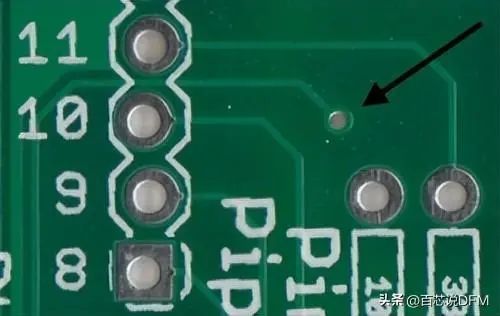
Front and back of the same PCB showing a tented via
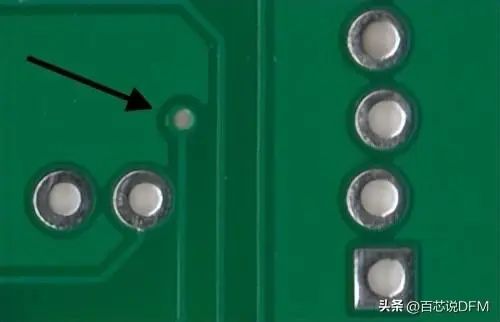
Via
Front and back of the same PCB showing a tented via. This via passes signals from the front of the PCB through the middle of the board to the back.
26. Wave Soldering
Method of soldering circuit boards with through-hole components, where the circuit board is passed through a wave of molten solder, adhering to exposed pads and component leads.
4. How to Design a PCB?
PCB design involves a lot and cannot be explained clearly in one go; here are some suggestions.
1. Look for CAD software packages
There are many low-cost or free options for PCB design on the market. Pay attention to the following points when choosing:
-
Is therea large user base for the software package? The more users there are, the more likely you are to find ready-made libraries containing the components you need.
-
Is it easy to use? If it is difficult to use, you won’t want to use it.
-
Is it feature-rich? Some may have limitations on design, such as layer count, component count, board size, etc.; most will allow paid upgrades for features.
-
Convertibility? Some free programs do not allow exporting or converting designs.
2. Learn from others’ layouts
This is the most straightforward; learn from others’ layouts and study how others do it. Especially now, there are many open-source materials online to learn from, where you can gain a lot of knowledge.
3. Practice, practice, and practice
4. Lower your expectations
Your first circuit board design will definitely have many issues; even by the 20th board design, there may still be problems. At this point, you need to adjust your mindset; having issues is normal.
5. Schematic Diagram
Designing a circuit board without a good schematic diagram usually has some issues, so the schematic is very important.
That’s all about PCB knowledge, and I hope everyone supports it.
Original link: https://learn.sparkfun.com/tutorials/pcb-basics/all
Disclaimer: This article is sourced from Baixin EMA DFM, and copyright belongs to the original author. If there are any copyright issues regarding the work, please contact us in a timely manner, thank you!