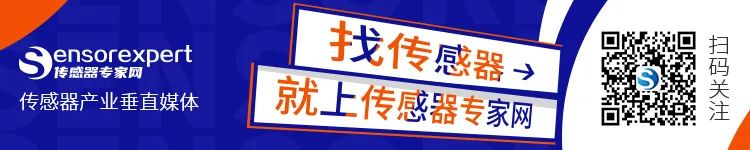
Have you ever wondered how many individual components are in an iPhone?
The accelerometer and gyroscope can detect the motion of the phone; light sensors, temperature sensors, pressure sensors, and humidity sensors can measure the environment of the phone; there are also sensors for connectivity like RFID, Bluetooth, and WiFi; as well as microphones and speakers for sound.
Most of these components are Micro-Electro-Mechanical Systems (MEMS).MEMS technology drives sensors to become smaller, while smaller sensors extend the reach of the Internet of Things.
What is MEMS Technology?
Micro-Electro-Mechanical Systems (MEMS) technology uses semiconductor manufacturing processes to produce miniaturized mechanical and electromechanical components ranging in size from less than one micron to several millimeters.MEMS devices can range from relatively simple structures without moving parts to complex electromechanical systems with multiple moving components.
MEMS are used not only for sensors but also across various fields. In addition to sensing, they are used in communication modules, actuators, and data processing devices. They are all miniature machines, with component sizes ranging from micrometers (one millionth of a meter) to millimeters.
MEMS devices cover a wide range, from simple machines with no moving parts to complex electromechanical systems with multiple moving components. These systems come in many different types: magnetic, electrical, thermal, chemical, optical, and mechanical systems.
Manufacturing MEMS devices requires many of the same techniques used to manufacture other semiconductor circuits: oxidation, diffusion, ion implantation, low-pressure chemical vapor deposition (LPCVD), sputtering, etc. In addition, MEMS use specialized processes such as micromachining.
Compared to earlier methods that achieve the same functions, MEMS devices are smaller, cheaper, and consume less power. They are also very sensitive and highly accurate.MEMS devices also have excellent repeatability, benefiting from the inherent tight tolerances of semiconductor process technology.
The downside is that while the production cost of parts is very low, the investments associated with designing, qualifying, and manufacturing MEMS products are substantial. As a result, manufacturers are less likely to develop parts for small-volume applications.
Types of MEMS Devices and MEMS Applications
Typical MEMS sensors employ mechanical structures that respond to mechanical or electrical stimuli (pressure, motion, acceleration, magnetic fields, etc.) and move in a controlled manner. A typical technology uses movement to change the distance between the plates of a variable capacitor.
Gyroscopes require multiple MEMS structures to measure angular motion.
Outputs can take various forms: analog voltage; output voltage; standard serial buses such as SPI or I2C; or proprietary protocols popular in automotive airbag applications (e.g., DSI or PSI5); wireless connection options include Bluetooth Low Energy (BLE).
MEMS devices can serve as single-function sensors.
MEMS Gyroscopes measure angular rotation by utilizing Coriolis acceleration, which generates forces on the MEMS structure as mass moves towards and away from the center of rotation. Gyroscopes come in single-axis, dual-axis, and tri-axis versions for different applications: for example, dual-axis gyroscopes are used for gaming and optical image stabilization, while tri-axis gyroscopes meet the needs of automotive telematics and navigation.
Accelerometers also use mass within the frame to measure static acceleration (i.e., gravity) and dynamic acceleration (e.g., vibrations, motion, tilt, impacts, etc.). Devices classified as accelerometers include inclinometers, vibration sensors, concussion sensors, tilt sensors, and motion sensors. Accelerometers also come with different axis combinations: single-axis devices are found in automotive collision sensors, while three-dimensional units appear in robotics, vibration monitoring, and anti-tampering applications.
Pressure Sensors measure pressure through the deflection caused in their MEMS structure. Some versions can measure pressure relative to atmospheric pressure and also measure absolute pressure relative to a vacuum-sealed chamber. MEMS pressure sensors can also indirectly measure other quantities, such as fluid flow, altitude, and water level.
Magnetometers measure mechanical effects caused by magnetic fields using various physical phenomena, such as the Hall effect.
Inertial Measurement Units (IMUs) measure linear and angular acceleration by combining tri-axis accelerometers and gyroscopes into a single unit; IMUs can also include magnetometers and pressure sensors to provide information about the device’s three-dimensional orientation and motion: acceleration on the x, y, and z axes; pitch, roll, yaw, altitude, etc. Applications include unmanned aerial vehicles (UAVs), robotics, factory automation, avionics, smartphones and tablets, virtual reality, and gaming.
MEMS Microphones operate by measuring changes in capacitance when sound waves strike a variable capacitor made of a movable diaphragm and a fixed backplate. They are widely used in consumer applications with space constraints, such as smartphones and tablets.
MEMS Biosensors measure detectable motions resulting from interactions between biomolecules. For example, in tuberculosis (TB) detection, a MEMS cantilever coated with TB antibodies deflects when an infected blood sample is placed on it.
MEMS Gas Sensors detect the presence of gases by measuring changes in resistance induced on the surface of the coated sensor. The sensor can detect low concentrations of target gases, with typical response times of less than one second. Humidity sensors are optimized to detect water vapor.
RF MEMS Switches combine electrostatically driven cantilevers with separate driver ICs to replace unreliable bulky electromechanical relays in RF switch applications. Various switch configurations can be used: for example, ADI’s ADGM1304 employs an SP4T configuration and can handle signals from DC to 14 GHz.
MEMS Optical Actuators, such as Texas Instruments’ Digital Micromirror Device (DMD), use MEMS technology to form a large number of independently controlled mirrors. Each mirror can tilt under electronic control to switch between “on” and “off” states. When enabled, pixels reflect light from the projector’s lamp into the lens, making them appear bright. In the off state, the light is directed elsewhere, making the pixel appear dark.
MEMS Oscillators contain a resonator that vibrates under electrostatic excitation from an analog driver chip. MEMS oscillators can produce frequencies from 1 Hz to several hundred MHz, with excellent stability, low power consumption, and high electromagnetic interference (EMI) immunity.
MEMS in the Internet of Things
The Internet of Things has a huge demand for miniature, low-cost sensors that monitor all aspects of production. These sensors must communicate information to other nodes in the factory network and must reliably operate in harsh electrical and mechanical environments. MEMS devices are tailor-made for this purpose: they are small, robust, and can incorporate additional circuit blocks for wired or wireless connectivity within the same package.
MEMS devices can effectively meet the requirements of many IoT applications:
1: Low Power Consumption
IoT sensors and gateways often require wireless and battery power. Because unit costs are lower, replacing the entire unit is often cheaper than reinstalling a new battery. Therefore, any reduction in power consumption extends the device’s lifespan. Some MEMS face the same power requirements as larger MEMS. Others leverage different forces in electromagnetics or fluid dynamics to reduce power consumption without sacrificing functionality (for example, consider the surface tension situation when delivering water through small pipes).
2: Miniaturization
Users typically want IoT devices to be small and unobtrusive in office and home environments. By definition, MEMS are unobtrusive. However, beyond user demands, in some IoT applications, it may be necessary to add the device to existing machinery (e.g., cars) that have limited hardware space. In other cases, such as wearable devices and biomedical applications, small size is a key requirement that must be met. Due to their smaller nature, MEMS meet and exceed these requirements.
3: Cost-Effectiveness
When deploying IoT solutions, scale is often a major concern. For example, when deploying sensors to monitor weather and humidity in agricultural fields, many devices will need to be seeded per acre. Or consider an asset tracking solution where a very large (and variable) number of assets may need to be tracked. In other applications such as transportation, devices may simply be disposable. MEMS are made using a process called photolithography, which makes mass production easy and cost-effective.
As more devices and applications are added to the Internet of Things, MEMS will become an increasingly viable solution.
For example, numerous applications of MEMS sensors in the industrial Internet of Things:
Industrial robots use MEMS-based 3-D gyroscopes and accelerometers to continuously measure changes in angular velocity and direction, replacing expensive rotary sensors and encoders. They can also detect excessive vibrations in joints and actuators, which may be a sign of premature failure.
MEMS accelerometers can detect harmful vibrations in other industrial machines or sense harmful shocks; MEMS pressure sensors measure water flow and air pressure; MEMS gas sensors check for toxic gas emissions; MEMS temperature sensors are critical components of many industrial processes.
In the IoT network infrastructure, MEMS oscillators are popular in programmable logic controllers (PLCs) that supervise the operation of robots and other units. Optical devices are suitable for human-machine interface (HMI) displays.
Factories themselves use MEMS in various ways. Pressure, temperature, and humidity sensors help control HVAC systems. Anti-tampering sensors are installed in smart meters; if an earthquake occurs, MEMS vibration sensors can help shut off gas supply.
Calibrated and temperature-compensated MEMS sensors can measure gas pressure in LPG and CNC-driven vehicles that transport products to loading and unloading platforms. After products leave the factory, asset tracking systems use MEMS to monitor the impact and vibration of goods.
Future Areas of MEMS Sensor Applications to Watch
Autonomous vehicles require dozens of sensors to interact with their surroundings. These sensors must also be as small as possible to avoid taking up space needed for other devices (manned and battery). Therefore, the automotive industry is one of the fields where MEMS sensor production and use are expected to grow the most.
MEMS-based accelerometers have high sensitivity and fault-safe performance in extremely critical applications, such as airbag activation and vehicle stability within the automotive end user.
Another area being explored for MEMS technology use is microphones. MEMS microphones can, for example, reduce the size of hands-free devices for phones and create smaller, more discreet assistive devices for people with hearing impairments.
The most spectacular and interesting use cases may be in biotechnology and medical technology. Procedures such as gastrointestinal examinations can be performed using cameras and tubes, with small guiding robots to execute them.
-
New Product Release | Aosong Electronics Launches Miniature Temperature and Humidity Measurement Module -
Packaging and Testing Giant – Changdian Technology’s Past and Present -
The Future 6 Fields with the Greatest Demand for Sensor Technology!
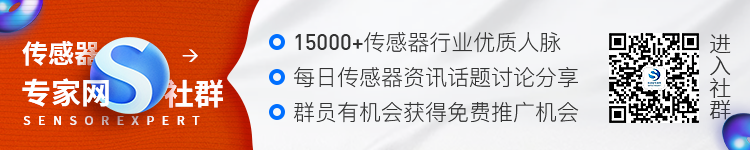